Deploy IoT device management systems strategically across construction sites by establishing centralized control hubs that monitor equipment location, maintenance schedules, and real-time performance metrics. Integrate asset tracking sensors with existing project management platforms to create a seamless workflow that drives digital transformation in construction. Implement automated maintenance alerts and predictive analytics to prevent equipment downtime, reduce operational costs, and extend asset lifecycles.
Construction firms managing extensive IoT networks must prioritize cybersecurity protocols, ensuring encrypted data transmission and regular security audits protect sensitive project information. Real-time monitoring capabilities enable project managers to optimize resource allocation, track equipment utilization rates, and maintain compliance with safety regulations across multiple job sites simultaneously.
The integration of IoT devices into construction operations delivers quantifiable benefits: 30% reduction in equipment downtime, 25% improvement in resource utilization, and 40% faster response times to maintenance issues. These technological advances transform traditional asset management into a data-driven, predictive system that enhances project efficiency and bottom-line results.
Current Challenges in Construction Inventory Management
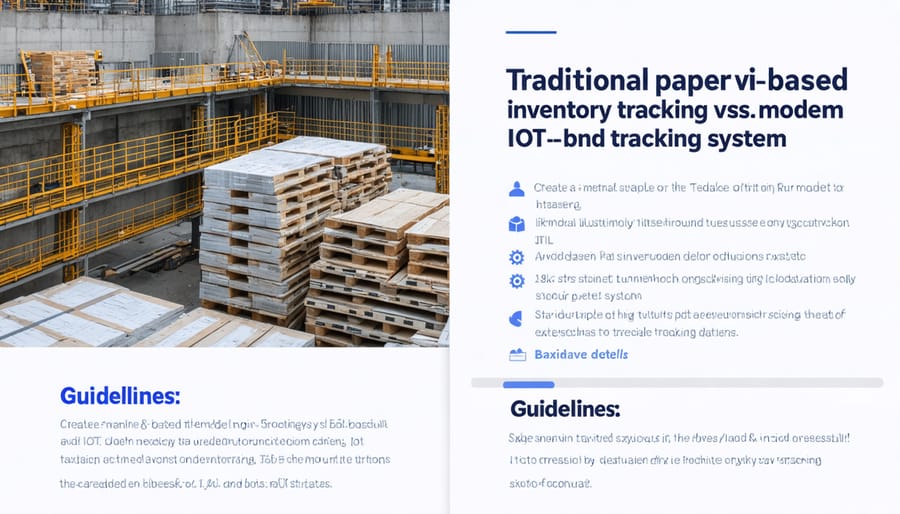
Common Pain Points
Construction companies face significant challenges when managing IoT devices across multiple job sites. Device interoperability remains a persistent issue, with various manufacturers using different protocols and communication standards, making seamless integration difficult. Data security poses another critical concern, as connected devices create potential vulnerabilities in the construction network infrastructure.
Real-time tracking of numerous IoT sensors and equipment can overwhelm existing IT systems, particularly when dealing with large-scale projects. Battery life management and device maintenance across remote locations present logistical hurdles, often requiring specialized technical expertise not readily available on-site.
Connectivity issues in remote construction areas or underground work zones frequently disrupt data transmission, affecting project monitoring and decision-making. Additionally, the cost of implementing and maintaining IoT infrastructure, including sensor replacement and software updates, can strain project budgets. Environmental factors such as extreme temperatures, dust, and vibration also impact device reliability and longevity, necessitating robust protection measures and regular maintenance protocols.
Cost Implications
Poor IoT device inventory management can significantly impact a construction company’s bottom line. Studies indicate that inefficient tracking of IoT devices leads to an average cost increase of 23% in equipment maintenance and replacement. Lost or misplaced devices not only require immediate replacement but also result in project delays and reduced operational efficiency.
The financial implications extend beyond direct replacement costs. Untracked devices may continue incurring subscription fees long after becoming inactive, while unauthorized devices can create security vulnerabilities leading to costly breaches. Industry data shows that construction firms lose an estimated $15,000 to $50,000 annually due to improper IoT asset management.
Furthermore, inadequate device tracking affects warranty claims and maintenance schedules. Without proper documentation, companies often miss warranty periods and pay for repairs that should be covered. Regular calibration and certification requirements may also lapse, potentially resulting in regulatory non-compliance fines and project setbacks.
Essential IoT Devices for Construction Inventory
RFID and NFC Systems
RFID (Radio Frequency Identification) and NFC (Near Field Communication) systems serve as cornerstone technologies in modern construction inventory management, offering unprecedented control and visibility over IoT devices. These wireless tracking solutions integrate seamlessly with existing digital procurement tools, enabling real-time asset monitoring and automated data collection.
Construction firms implementing RFID systems report significant improvements in inventory accuracy, with error rates dropping by up to 95% compared to manual tracking methods. The technology allows for simultaneous scanning of multiple tagged items without line-of-sight requirements, drastically reducing the time spent on inventory counts and asset verification.
NFC technology, operating at shorter ranges, provides enhanced security for sensitive equipment access and maintenance logging. Project managers can instantly retrieve equipment histories, maintenance schedules, and certification status by simply scanning tagged assets with NFC-enabled devices.
Key benefits include:
– Automated equipment tracking and location services
– Enhanced theft prevention and recovery
– Streamlined maintenance scheduling
– Improved regulatory compliance documentation
– Real-time utilization monitoring
Implementation costs have decreased significantly in recent years, making these systems increasingly accessible for construction firms of all sizes. The return on investment typically manifests within 12-18 months through reduced equipment loss, improved operational efficiency, and better resource allocation.
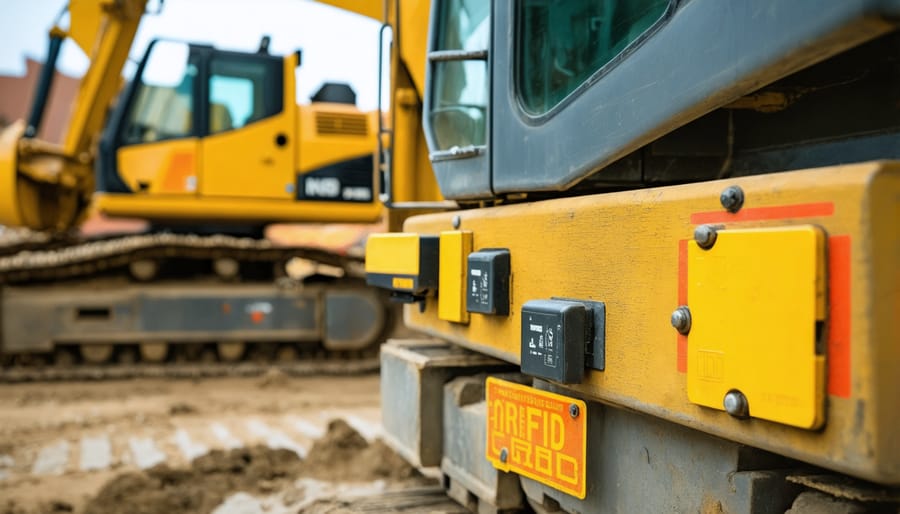
Smart Sensors and Monitors
Smart sensors and environmental monitors form the backbone of modern IoT-enabled construction sites, providing real-time data crucial for project efficiency and safety compliance. These sophisticated devices track various parameters including temperature, humidity, air quality, noise levels, and precise asset locations through GPS and proximity sensing.
Environmental sensors play a vital role in maintaining optimal working conditions and protecting sensitive materials. For instance, concrete curing processes can be closely monitored through temperature and humidity sensors, ensuring proper hardening conditions are maintained. Similarly, air quality sensors help protect worker health by detecting harmful particulates and gases, automatically triggering ventilation systems when necessary.
Location tracking sensors offer unprecedented visibility into equipment movement and utilization. GPS-enabled devices monitor heavy machinery locations, helping prevent theft and optimize deployment across large construction sites. Proximity sensors assist in collision avoidance and restricted area access control, significantly improving site safety.
The implementation of these sensors requires strategic placement and regular calibration to ensure accuracy. Leading construction firms report up to 30% improvement in resource utilization and a 25% reduction in safety incidents after deploying comprehensive sensor networks. Integration with central management platforms enables automated alerts and data-driven decision making, transforming raw sensor data into actionable insights for project managers.
For maximum effectiveness, sensors should be configured to site-specific requirements and environmental conditions, with redundancy built into critical monitoring areas. Regular maintenance and battery replacement schedules ensure continuous operation throughout the project lifecycle.
Best Practices for IoT Device Management
Device Configuration and Setup
Successful IoT device deployment in construction projects begins with systematic configuration and setup procedures. The initial phase involves network infrastructure assessment, ensuring adequate coverage and bandwidth capacity across the construction site. Site managers should establish a dedicated server or cloud platform to manage device data and implement appropriate security protocols before device installation.
Each IoT device requires proper calibration according to manufacturer specifications and project requirements. This includes setting measurement parameters, establishing communication protocols, and configuring reporting intervals. Device registration within the central management system must include unique identifiers, location data, and specific function assignments.
Integration testing is crucial before full deployment. This involves verifying connectivity, data transmission accuracy, and system response times. Construction teams should document baseline readings and establish performance benchmarks for future reference. Emergency protocols and failsafe mechanisms need configuration to ensure continuous operation during network disruptions.
The final setup phase includes user access configuration, establishing role-based permissions, and training key personnel on device operation and basic troubleshooting procedures. Regular system checks during the first week of deployment help identify and resolve any configuration issues promptly.
Maintenance Protocols
Regular maintenance of IoT devices in construction environments requires a systematic approach to ensure optimal performance and longevity. Establish a preventive maintenance schedule that includes monthly firmware updates, quarterly hardware inspections, and bi-annual system audits. Document all maintenance activities in a centralized digital log for compliance and tracking purposes.
Implement automated monitoring systems to detect potential issues before they escalate. Set up alert thresholds for battery levels, connectivity strength, and sensor accuracy. When troubleshooting, follow a hierarchical approach: first verify power supply and connectivity, then check sensor calibration, and finally assess data transmission integrity.
Create standard operating procedures (SOPs) for common issues, including step-by-step resolution guides. Train site personnel on basic troubleshooting procedures and establish clear escalation protocols for complex technical issues. Maintain an inventory of essential spare parts and backup devices to minimize downtime.
Regular maintenance should also include security updates, network vulnerability assessments, and verification of data backup systems. Document any pattern of failures or recurring issues to inform future device selection and deployment strategies. Consider environmental factors such as dust, vibration, and temperature fluctuations when adjusting maintenance frequencies.
Security Measures
Implementing robust security measures is critical when managing IoT devices in construction environments. Begin by establishing a comprehensive device authentication protocol, requiring unique credentials for each connected device and implementing multi-factor authentication for administrative access. Regular firmware updates and security patches should be automatically deployed across all devices to protect against emerging vulnerabilities.
Network segmentation is essential, isolating IoT devices from critical business systems through dedicated VLANs. Implement end-to-end encryption for all data transmission, particularly for sensitive information such as equipment locations and operational parameters. Consider adopting blockchain-enabled security solutions for enhanced data integrity and transparent device management.
Conduct regular security audits and vulnerability assessments to identify potential weaknesses in your IoT infrastructure. Maintain detailed logs of device activities and access attempts, enabling quick detection and response to security incidents. Establish clear security policies for device deployment, including guidelines for decommissioning and proper disposal of outdated equipment to prevent unauthorized access to historical data.
Integration with Existing Systems
Data Collection and Analysis
IoT devices generate vast amounts of real-time data that can transform construction inventory management when properly analyzed. Through strategic sensor placement and data collection points, organizations can track material movement, monitor equipment usage patterns, and predict maintenance needs with unprecedented accuracy.
Key metrics typically collected include asset location coordinates, utilization rates, environmental conditions, and operational status. Advanced analytics platforms process this data to identify trends, optimize stock levels, and generate actionable insights. For example, concrete sensors can monitor curing conditions while providing real-time updates on material availability and quality.
Machine learning algorithms analyze historical data patterns to predict future inventory requirements, reducing overstock situations and preventing material shortages. This predictive capability enables just-in-time delivery systems and helps maintain optimal inventory levels across multiple project sites.
By implementing automated data collection and analysis systems, construction firms can reduce manual tracking errors by up to 90% while improving inventory turnover rates. The resulting insights enable better decision-making regarding procurement timing, storage optimization, and resource allocation, ultimately leading to significant cost savings and improved project efficiency.
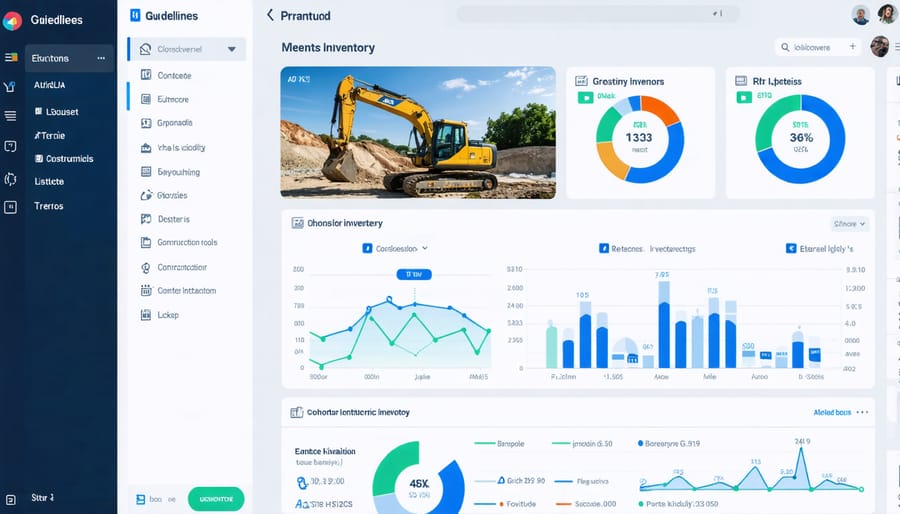
Workflow Automation
Workflow automation represents a significant advancement in IoT device management, enabling construction firms to streamline their operations and reduce manual intervention. By implementing automated procurement workflows and smart scheduling systems, companies can optimize resource allocation and maintenance schedules with unprecedented efficiency.
Integration of IoT sensors with project management platforms allows for real-time monitoring and automated responses to predefined triggers. For instance, when equipment usage reaches certain thresholds, the system can automatically schedule maintenance, order replacement parts, or adjust operational parameters. This proactive approach minimizes downtime and extends asset lifespan.
Construction firms implementing workflow automation report up to 30% reduction in administrative tasks and a 25% improvement in resource utilization. The key to successful automation lies in creating clear protocols and establishing reliable data pipelines between IoT devices and management systems. By configuring smart alerts and automated reporting mechanisms, teams can focus on strategic decisions while routine tasks are handled systematically.
Case Study: Success in Action
Turner Construction’s implementation of IoT technology at their $500 million commercial development project in Seattle demonstrates the transformative power of smart device management in construction inventory control. In 2021, the company deployed a comprehensive IoT ecosystem to track and manage over 3,000 assets across their 15-acre construction site.
The system utilized RFID tags, GPS trackers, and environmental sensors connected to a centralized cloud platform. Each piece of equipment, from power tools to heavy machinery, was equipped with appropriate tracking devices. Strategic placement of IoT gateways throughout the site ensured continuous connectivity and real-time data transmission.
Within six months of implementation, Turner reported remarkable improvements:
– 32% reduction in equipment loss and theft
– 47% decrease in time spent locating tools and materials
– 28% improvement in equipment utilization rates
– 18% reduction in unnecessary rental costs
– 85% faster inventory audits
The project team implemented a three-tier monitoring system: basic RFID tracking for small tools, GPS tracking for mobile equipment, and advanced sensors for critical machinery that monitored usage patterns and maintenance needs. The system automatically generated alerts when equipment needed servicing or when items moved outside designated zones.
Project Manager Sarah Chen noted, “The real-time visibility transformed our operations. We could instantly locate any piece of equipment, predict maintenance needs, and optimize resource allocation. The system paid for itself within the first year.”
Key to success was the thorough training program developed for site personnel and the establishment of clear protocols for device management. The team created standardized procedures for tagging new equipment, maintaining sensors, and responding to system alerts.
This implementation serves as a blueprint for large-scale IoT adoption in construction inventory management, demonstrating how proper planning and execution can deliver measurable operational improvements and significant cost savings.
As the construction industry continues to embrace IoT technology, effective device management remains crucial for successful digital transformation. The key to maximizing ROI lies in implementing robust security protocols, establishing clear maintenance schedules, and ensuring seamless integration with existing systems. Industry leaders who have adopted comprehensive IoT management strategies report significant improvements in operational efficiency, cost reduction, and project delivery times.
Looking ahead, the construction sector can expect to see more sophisticated IoT solutions emerge, with AI-driven analytics and predictive maintenance becoming standard features. The focus will increasingly shift toward scalable, cloud-based management platforms that can handle thousands of connected devices across multiple project sites. Success in this evolving landscape will depend on maintaining a balance between technological advancement and practical implementation, always keeping security and reliability at the forefront of IoT device management strategies.