Revolutionizing the construction industry demands urgent attention as innovative, eco-friendly building materials emerge to address climate change and resource scarcity. Today’s sustainable construction practices are being transformed by breakthrough materials that combine performance with environmental responsibility.
From carbon-negative concrete alternatives to bio-based composites derived from agricultural waste, these next-generation materials are redefining industry standards while dramatically reducing environmental impact. Recent advances in material science have produced options that not only match traditional materials in durability and strength but often surpass them—all while cutting embodied carbon by up to 70%.
For construction professionals and project stakeholders, this evolution represents both an opportunity and imperative. As global building codes increasingly mandate sustainable materials and clients demand greener solutions, staying ahead of these innovations has become crucial for competitive advantage. This comprehensive exploration examines the most promising sustainable materials emerging in 2024, their practical applications, and the critical considerations for successful implementation in modern construction projects.
Bio-Based Construction Materials Leading the Green Revolution
Engineered Wood Products and Mass Timber
Engineered wood products (EWPs) and mass timber represent a significant advancement in sustainable building materials, offering remarkable strength-to-weight ratios and environmental benefits. Cross-laminated timber (CLT) leads this innovation, enabling the construction of tall wooden buildings that were previously impossible. These engineered products demonstrate superior dimensional stability and fire resistance compared to traditional lumber, while significantly reducing carbon footprint.
Mass timber systems, including glue-laminated timber (glulam) and laminated veneer lumber (LVL), provide structural solutions that rival steel and concrete in performance. Recent developments in manufacturing processes have enhanced their durability and structural capabilities, making them suitable for large-scale commercial projects. The University of British Columbia’s 18-story Brock Commons Tallwood House exemplifies the potential of mass timber construction, completing assembly 70% faster than conventional methods while sequestering 1,753 metric tons of carbon dioxide.
Manufacturing innovations have also addressed historical concerns about moisture and pest resistance through advanced treatment processes and strategic design considerations. The integration of digital fabrication technologies with mass timber production enables precise customization and minimal waste, further enhancing sustainability credentials. These advancements have positioned engineered wood products at the forefront of sustainable construction, offering a viable alternative to traditional building materials while supporting carbon reduction goals.
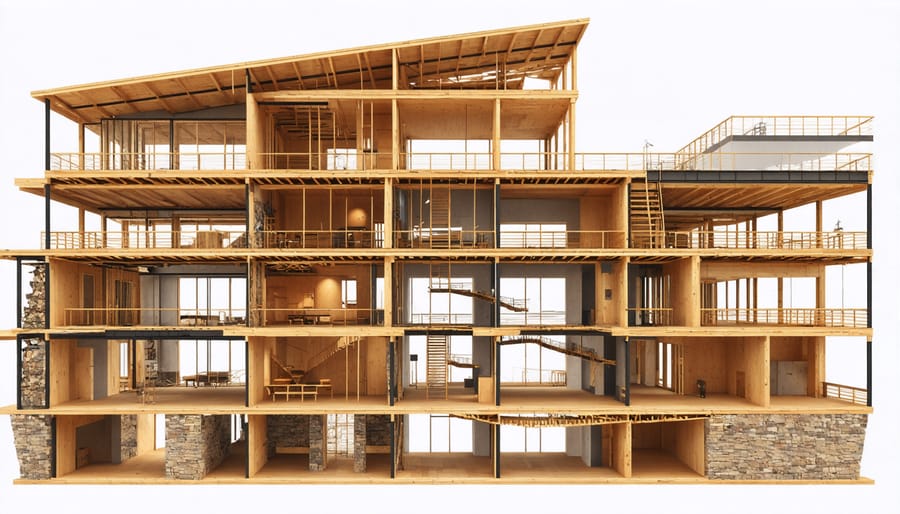
Mycelium-Based Materials
Mycelium-based materials represent a groundbreaking advancement in sustainable construction, utilizing the root structure of mushrooms to create robust, lightweight building components. These bio-engineered materials are produced by combining agricultural waste with mycelium spores, which grow to form a dense network of natural fibers over several days.
The resulting material exhibits remarkable properties, including fire resistance, excellent thermal insulation, and acoustic absorption capabilities. Recent testing has demonstrated compressive strengths comparable to traditional insulation materials, with density values ranging from 65 to 300 kg/m³ depending on the substrate used.
Dell Technologies’ packaging initiative and The Living’s Hy-Fi tower in New York have demonstrated successful commercial applications of mycelium-based materials. The tower, constructed entirely from mycelium bricks, proved the material’s structural viability and biodegradability in architectural applications.
Key advantages include minimal energy requirements during production, zero waste at end-of-life, and natural carbon sequestration. Current research focuses on improving water resistance and standardizing production methods for widespread commercial adoption.
However, challenges remain in scaling production and achieving consistent material properties. Industry experts predict that with ongoing research and development, mycelium-based materials could replace traditional insulation and non-load-bearing components within the next decade, particularly in low-rise construction and interior applications.
Smart and Self-Healing Materials
Self-Repairing Concrete Technologies
Self-repairing concrete technologies represent a significant breakthrough in sustainable construction, offering solutions to one of the industry’s most persistent challenges: concrete deterioration. These innovative materials incorporate either bacterial spores or chemical agents that activate when cracks appear, effectively healing the damage without human intervention.
The bacterial approach utilizes specially selected bacteria strains, typically Bacillus species, which remain dormant within the concrete matrix until exposed to water through cracking. Once activated, these microorganisms produce calcium carbonate through their metabolic processes, filling cracks up to 0.8mm wide. This biological healing process not only repairs structural damage but also enhances the concrete’s durability and water resistance.
Chemical self-healing systems employ encapsulated healing agents that release when cracks form. These capsules contain various compounds, such as sodium silicate or polyurethane precursors, which react upon exposure to air or moisture to form solid compounds that seal the cracks. Recent field trials have shown that chemical systems can effectively heal cracks within 24-48 hours under optimal conditions.
Industry testing has demonstrated that self-repairing concrete can reduce maintenance costs by up to 50% over a structure’s lifetime while significantly extending its service life. The technology has proven particularly valuable in infrastructure projects exposed to harsh environmental conditions, such as marine structures and underground facilities.
Despite higher initial costs—typically 20-30% more than conventional concrete—the long-term benefits include reduced maintenance requirements, improved structural integrity, and lower lifecycle carbon emissions. As production scales up and technology advances, experts predict costs will decrease, making self-repairing concrete increasingly viable for mainstream construction applications.
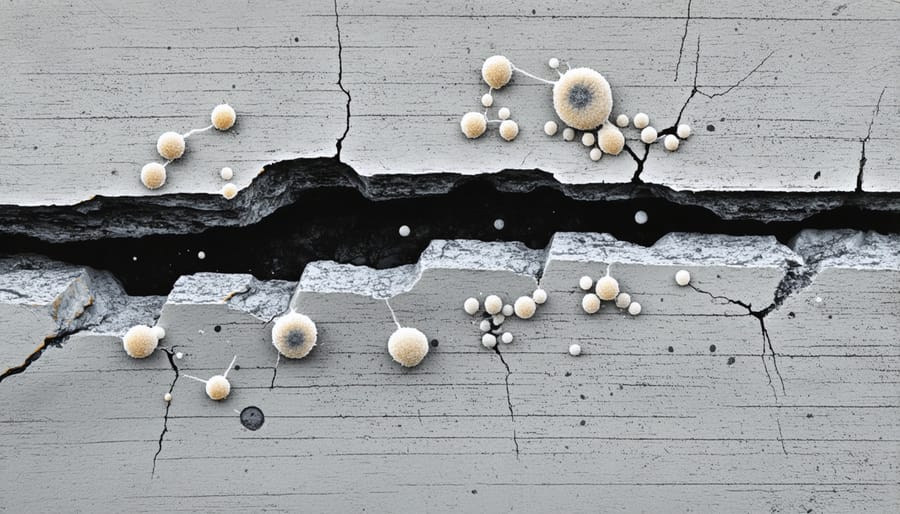
Phase-Change Materials
Phase-change materials (PCMs) represent a groundbreaking advancement in sustainable temperature regulation for buildings. These innovative materials can absorb, store, and release large amounts of thermal energy during phase transitions, effectively maintaining consistent indoor temperatures while reducing HVAC energy consumption by 20-30% in typical commercial applications.
PCMs work by changing their physical state – typically from solid to liquid and back – at specific temperature thresholds. When integrated into building materials like wallboards, concrete, or insulation systems, they absorb excess heat during warm periods and release it when temperatures drop, creating a natural temperature-regulation cycle.
Recent developments have introduced microencapsulated PCMs, which consist of microscopic polymer shells containing phase-change compounds. This technology allows for seamless integration into traditional construction materials without compromising structural integrity. Leading manufacturers now offer PCM-enhanced gypsum boards that can store up to 330 kJ/m² of thermal energy.
Implementation case studies have shown remarkable results. The Edge building in Amsterdam, incorporating PCM-enhanced concrete, achieved a 40% reduction in cooling costs during its first year of operation. Similarly, a commercial complex in Dubai utilizing PCM-integrated facade panels demonstrated peak load reductions of 25% during extreme summer conditions.
The most commonly used PCMs in construction include organic compounds like paraffins and fatty acids, and inorganic materials such as salt hydrates. Selection criteria depend on the desired phase-change temperature, typically ranging from 19°C to 25°C for building applications, and the specific climate conditions of the project location.
While initial material costs remain higher than traditional alternatives, the long-term energy savings and reduced carbon footprint make PCMs an increasingly attractive option for sustainable construction projects.
Recycled and Upcycled Building Components
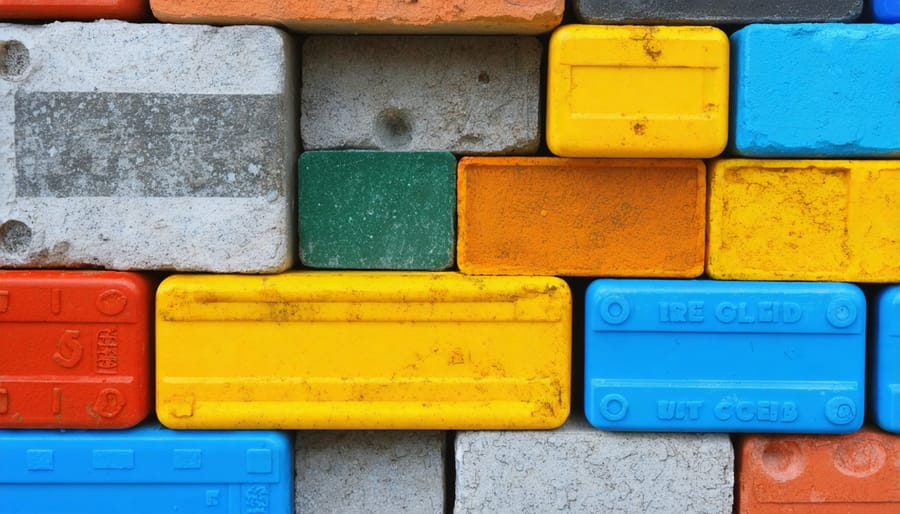
Plastic-Based Construction Materials
The construction industry is witnessing a remarkable transformation with the integration of recycled plastic materials, offering innovative solutions to both waste management and sustainable building practices. Recent developments have led to the creation of high-performance plastic lumber, composite decking, and structural elements that match or exceed traditional materials in durability and strength.
Leading manufacturers are now producing construction blocks made from processed plastic waste, which demonstrate excellent thermal insulation properties while being up to 60% lighter than conventional concrete blocks. These materials show particular promise in non-load-bearing applications and insulative wall systems, with thermal resistance values typically 20% higher than traditional alternatives.
Field testing has demonstrated that plastic-based construction materials exhibit superior resistance to moisture, rot, and insect infestation. Moreover, these materials require minimal maintenance and boast lifespans exceeding 50 years. Recent implementations in commercial projects have shown cost savings of up to 30% in long-term maintenance expenses.
Environmental impact assessments indicate that incorporating recycled plastic materials in construction can divert significant amounts of waste from landfills – with each typical residential project utilizing approximately 2-3 tons of recycled plastic. This approach not only addresses waste management challenges but also reduces carbon emissions associated with traditional material production.
However, industry professionals should note that proper material selection and installation techniques are crucial, as thermal expansion characteristics differ from conventional materials. Successful implementation requires adherence to manufacturer specifications and understanding of material behavior under various environmental conditions.
Industrial By-Product Integration
Industrial by-products are revolutionizing sustainable construction through innovative material development and waste reduction strategies. Steel slag, a by-product of steel manufacturing, is being successfully incorporated into high-performance concrete mixtures, offering enhanced durability and reduced carbon footprint compared to traditional Portland cement. Research indicates that slag-based concrete can achieve up to 40% reduction in CO2 emissions while maintaining structural integrity.
Fly ash, generated from coal-burning power plants, has emerged as a crucial supplementary cementitious material. When properly processed and integrated, it improves concrete workability and reduces water demand by up to 15%. Major construction projects worldwide have demonstrated its effectiveness, with several skyscrapers utilizing fly ash concrete in their foundations and structural elements.
Glass powder derived from recycled containers is gaining traction as a partial cement replacement, offering improved mechanical properties and reducing landfill waste. Recent studies show that fine glass powder can replace up to 30% of cement content without compromising structural performance.
Agricultural waste products, such as rice husk ash and sugarcane bagasse ash, are being transformed into valuable construction materials. These materials exhibit excellent pozzolanic properties and can enhance concrete durability while providing a sustainable solution for agricultural waste management.
The integration of these industrial by-products not only addresses waste management challenges but also creates more resilient and environmentally responsible building materials. Construction firms implementing these solutions report significant cost savings and improved environmental performance metrics.
Implementation Challenges and Industry Adoption
Despite the promising potential of sustainable construction materials, several significant challenges impede their widespread adoption in the industry. Cost remains a primary concern, with many innovative materials carrying higher upfront expenses compared to traditional options. While lifecycle cost analyses often demonstrate long-term savings, the initial investment can deter budget-conscious developers and contractors.
Technical barriers also present challenges, particularly regarding compliance with existing building codes and standards. Many sustainable materials require new testing protocols and certification processes, leading to delays in market introduction and regulatory approval. Additionally, construction professionals need specialized training to properly handle and install these materials, creating a skills gap that must be addressed through comprehensive education programs.
Supply chain constraints pose another significant hurdle. The integration of circular economy principles into material production often requires establishing new procurement networks and manufacturing processes. This transformation demands substantial investment in infrastructure and logistics systems.
However, industry leaders are actively working to overcome these challenges. Organizations are developing innovative financing models to offset initial costs, while manufacturers are scaling up production to achieve economies of scale. Professional associations and educational institutions are creating specialized training programs to build workforce capacity.
Market acceptance is gradually improving as successful project implementations demonstrate the viability of sustainable materials. Government incentives, green building certifications, and increasing environmental regulations are driving adoption. Additionally, growing consumer awareness and demand for sustainable construction are compelling industry stakeholders to embrace these innovations.
To accelerate adoption, the construction industry must focus on standardization, quality assurance, and performance validation. Collaborative efforts between manufacturers, researchers, and regulatory bodies are essential to establish clear guidelines and specifications. This coordinated approach will help build confidence in sustainable materials and facilitate their integration into mainstream construction practices.
The construction industry stands at a pivotal moment in its evolution toward sustainability. The emergence of innovative materials like carbon-negative concrete, mycelium-based composites, and transparent wood demonstrates a clear shift toward environmentally conscious building solutions. These developments are not merely trends but represent fundamental changes in how we approach construction.
Industry adoption rates for sustainable materials continue to rise, driven by stringent environmental regulations, growing consumer demand, and improved cost-effectiveness. Market projections indicate that the sustainable construction materials sector will experience double-digit growth over the next decade, with particular emphasis on bio-based materials and recycled composites.
Looking ahead, several key trends will shape the future of sustainable construction materials. Advanced material science and nanotechnology will enable the development of even more efficient and environmentally friendly options. The integration of smart technologies with sustainable materials will create buildings that are not only eco-friendly but also responsive to environmental conditions.
The challenge moving forward lies in scaling production, reducing costs, and standardizing testing protocols for new materials. However, with continued investment in research and development, along with supportive policy frameworks, these obstacles are likely to be overcome. The construction industry’s commitment to sustainability, coupled with technological advancement, suggests a future where sustainable materials become the norm rather than the exception in construction projects worldwide.