Measure, track, and optimize your building’s environmental impact through robust sustainability metrics in construction that drive real-world results. Global construction leaders have revolutionized project performance by implementing precise sustainability indicators across three critical domains: resource efficiency, environmental impact, and social responsibility.
Industry benchmarks reveal that organizations leveraging comprehensive sustainability metrics achieve 40% greater resource optimization and 35% reduced carbon emissions compared to traditional construction approaches. Leading firms now integrate real-time monitoring systems that track energy consumption, waste reduction, and water usage through IoT sensors and advanced analytics platforms.
This data-driven transformation demands structured implementation of key performance indicators (KPIs) that align with international standards like LEED, BREEAM, and WELL Building certification requirements. Construction professionals must prioritize measurable metrics including embodied carbon calculations, operational energy intensity, construction waste diversion rates, and occupant well-being indicators to demonstrate tangible sustainability achievements and secure competitive advantages in today’s environmentally conscious market.
Energy Performance Metrics
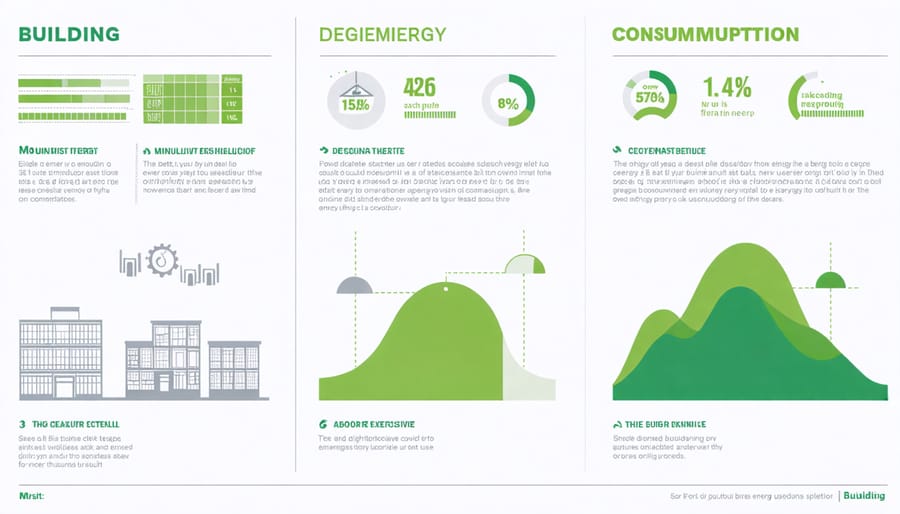
Operational Energy Consumption
Operational energy consumption metrics are crucial indicators for evaluating a building’s ongoing environmental impact and implementing effective energy efficiency strategies. The primary metrics include Energy Use Intensity (EUI), measured in kWh/m²/year, which enables standardized comparisons across different building sizes and types. Building managers should track both total energy consumption and peak demand values, typically monitored through smart meters and building management systems (BMS).
Key performance indicators include the Building Energy Rating (BER), HVAC system efficiency ratios, and lighting power density (LPD). Real-time energy monitoring systems can break down consumption patterns by end-use, helping identify optimization opportunities. The Energy Cost Index (ECI) combines consumption data with utility rates to assess financial performance.
Industry benchmarks suggest that high-performing commercial buildings should maintain an EUI below 150 kWh/m²/year, while exceptional performers can achieve below 100 kWh/m²/year. Monthly energy performance tracking should include baseline comparisons, weather normalization, and occupancy adjustments to ensure meaningful analysis.
For comprehensive assessment, organizations should monitor both absolute energy consumption and intensity metrics, setting reduction targets aligned with science-based climate goals. Regular energy audits and continuous commissioning processes help maintain optimal performance and identify emerging efficiency opportunities.
Embodied Energy Assessment
Embodied energy assessment quantifies the total energy consumed throughout a building material’s lifecycle, from raw material extraction to manufacturing, transportation, and installation. This comprehensive evaluation helps construction professionals make informed decisions about material selection and optimize their project’s environmental impact.
The assessment process typically involves three key components: initial embodied energy (manufacturing and transportation), recurring embodied energy (maintenance and replacement), and end-of-life energy (demolition and disposal). Industry professionals utilize established databases like the Inventory of Carbon and Energy (ICE) to access standardized energy values for common construction materials.
To calculate embodied energy, practitioners multiply material quantities by their respective energy coefficients, typically measured in megajoules per kilogram (MJ/kg). For example, concrete has an embodied energy value of approximately 0.75-1.1 MJ/kg, while structural steel ranges from 20-25 MJ/kg. This analysis enables teams to compare alternative materials and construction methods effectively.
Leading construction firms are increasingly incorporating Building Information Modeling (BIM) tools to automate embodied energy calculations. These platforms can integrate material quantities with energy databases, providing real-time assessments during the design phase. This approach allows for early intervention and optimization of material choices, supporting more sustainable construction practices while maintaining project efficiency and performance requirements.
Resource Efficiency Metrics
Material Circularity Indicators
Material Circularity Indicators (MCIs) provide crucial metrics for evaluating how effectively construction materials move through the circular economy. These indicators focus on two primary aspects: the percentage of recycled content in new materials and the potential for materials to be recycled or reused at the end of their lifecycle.
Key metrics include the Input Circularity Rate (ICR), which measures the proportion of recycled or reused materials in new construction products. For instance, leading construction firms typically aim for an ICR of at least 25% in structural materials and 40% in finishing materials. The Output Circularity Rate (OCR) assesses the percentage of materials that can be effectively recycled or reused after demolition.
Design for Disassembly (DfD) scores evaluate how easily building components can be separated and recovered at end-of-life. This metric typically considers factors such as connection types, material compatibility, and component accessibility. Projects achieving high DfD scores often demonstrate 80% or greater potential material recovery rates.
Material waste factors are also essential indicators, measuring the ratio of waste generated during construction to total material input. Industry leaders target waste factors below 5% for primary materials. Additionally, the Material Recoverability Index (MRI) provides a composite score combining recyclability potential, contamination risks, and local recycling infrastructure availability.
These indicators help construction professionals make informed decisions about material selection and assembly methods while supporting circular economy objectives and reducing environmental impact.
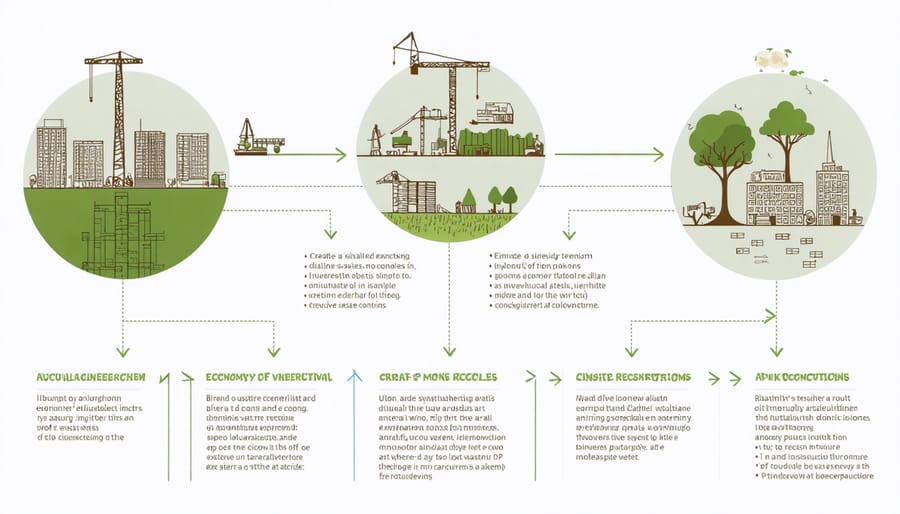
Water Usage Efficiency
Water usage efficiency in construction encompasses both the construction phase and operational lifecycle of buildings, requiring careful monitoring and management through specific metrics. Construction professionals typically measure water consumption using gallons per square foot (GPF) during construction activities and gallons per occupant during building operation.
Key performance indicators include the Water Use Intensity (WUI), which measures the total water consumed annually divided by the gross floor area. For construction sites, tracking metrics include daily water consumption for activities like concrete mixing, dust suppression, and equipment cleaning. Many leading projects achieve efficiency rates of 20-30% below baseline through implementation of water-efficient practices.
Operational water efficiency metrics focus on fixture performance (measured in gallons per flush or gallons per minute), irrigation system efficiency (typically targeting 30% reduction from conventional systems), and process water consumption. Advanced buildings incorporate real-time monitoring systems that track water usage patterns and detect leaks, providing data for continuous optimization.
Case studies from LEED-certified projects demonstrate that comprehensive water management strategies can reduce consumption by up to 40% compared to conventional buildings. This includes implementing low-flow fixtures, rainwater harvesting systems, and water-efficient landscaping. Regular benchmarking against industry standards helps teams identify opportunities for improvement and validate conservation efforts.
For effective implementation, teams should establish clear baseline measurements, set specific reduction targets, and maintain detailed consumption logs throughout the project lifecycle.
Carbon Footprint Metrics
Operational Carbon Metrics
Operational carbon metrics measure the ongoing greenhouse gas emissions produced during a building’s functional lifetime, forming a crucial component of sustainable construction management practices. These metrics typically focus on three primary areas: energy consumption, HVAC systems performance, and occupant-related emissions.
The most widely adopted operational carbon metric is the Energy Use Intensity (EUI), measured in kWh/m²/year, which quantifies a building’s total energy consumption relative to its floor area. This is complemented by the Carbon Intensity Index (CII), which converts energy usage into CO₂ equivalent emissions, providing a standardized measurement for environmental impact assessment.
Real-time monitoring systems play a vital role in tracking these metrics, utilizing smart meters and building management systems (BMS) to collect and analyze data. Key performance indicators include:
– Annual energy consumption patterns
– Peak load demands
– System efficiency ratios
– Occupancy-adjusted emission rates
– Carbon offset achievements
Industry best practices recommend establishing baseline measurements during the first year of operation, followed by quarterly assessments against reduction targets. This approach enables facilities managers to identify optimization opportunities and implement corrective measures promptly. Leading construction firms are increasingly adopting automated monitoring solutions that provide dashboard visualization of these metrics, enabling more responsive and data-driven sustainability management.
Embodied Carbon Assessment
Embodied carbon assessment involves calculating the total carbon emissions associated with construction materials throughout their lifecycle, from extraction and manufacturing to transportation and installation. This comprehensive analysis typically employs standardized methodologies such as EN 15978 and PAS 2050 to ensure accurate and comparable results across projects.
Key calculation components include material quantity takeoffs, emission factors from verified databases (like ICE Database or EPD), and transportation distances. Modern assessment tools like One Click LCA and Tally integrate with BIM software to streamline this process, enabling real-time carbon calculations during design phases.
Material-specific considerations are crucial, with concrete, steel, and aluminum typically contributing the highest carbon footprints. For instance, replacing traditional Portland cement with supplementary cementitious materials can reduce embodied carbon by 30-50%. Similarly, specifying recycled steel can lower emissions by up to 90% compared to virgin material.
Process emissions from construction activities are calculated using equipment fuel consumption data, site energy usage, and waste management metrics. Leading construction firms now maintain detailed carbon inventories, tracking emissions from heavy machinery, temporary works, and on-site operations.
Best practice includes establishing project-specific carbon budgets early in design, conducting regular assessments throughout construction, and implementing reduction strategies based on findings. Documentation of assessment results should align with recognized reporting frameworks like LEED v4 or BREEAM to facilitate third-party verification and certification.
Implementation and Monitoring
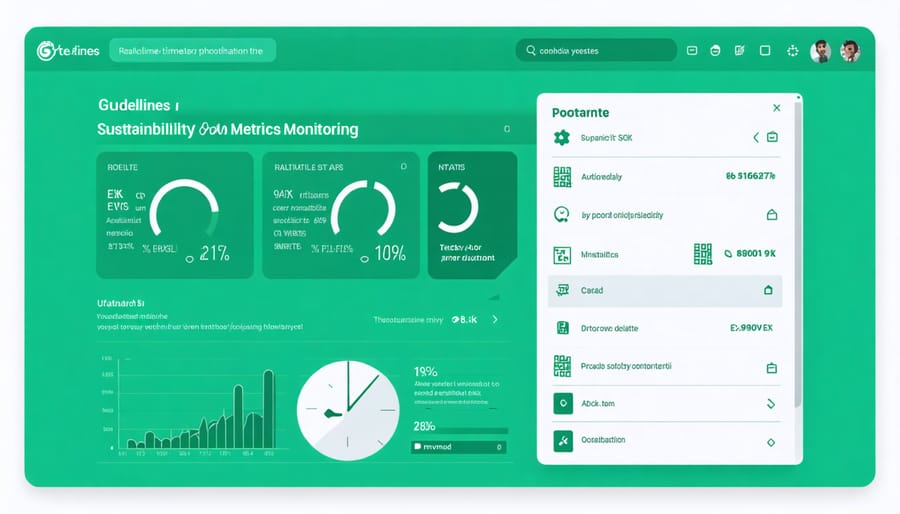
Digital Tools and Technologies
Modern sustainability tracking demands sophisticated digital construction tools that enable real-time monitoring and precise data analysis. Leading platforms like BuildingGreen Analytics and EcoTracker Pro offer comprehensive dashboard solutions that integrate multiple sustainability metrics into a single interface. These systems typically feature automated data collection through IoT sensors, performance visualization tools, and predictive analytics capabilities.
Cloud-based sustainability management systems (SMS) have emerged as essential tools for tracking environmental impact metrics. These platforms excel at monitoring energy consumption, water usage, waste management, and carbon emissions through integrated building management systems. Notable features include automated reporting functions that align with certification requirements for LEED, BREEAM, and other sustainability standards.
Building Information Modeling (BIM) software has evolved to incorporate sustainability analysis modules, enabling teams to simulate and optimize environmental performance during the design phase. These tools can calculate embodied carbon, predict operational energy consumption, and assess material lifecycle impacts before construction begins.
Mobile applications and web-based platforms now facilitate real-time data collection from construction sites, enabling immediate tracking of waste diversion rates, material recycling percentages, and transportation-related emissions. Advanced analytics capabilities help identify trends, forecast potential issues, and generate compliance reports for regulatory requirements and stakeholder communications.
Reporting and Certification Standards
Leading sustainability reporting frameworks include the Global Reporting Initiative (GRI) Standards, which provide comprehensive guidelines for environmental, social, and governance reporting in construction. These standards require detailed documentation of energy consumption, waste management, and carbon emissions, with specific performance indicators that must be regularly monitored and verified.
LEED certification remains the gold standard for sustainable building practices, requiring adherence to strict metrics across multiple categories. Projects must demonstrate compliance through documented evidence of energy efficiency, water conservation, and sustainable material usage. The certification process involves third-party verification and ongoing performance monitoring.
The International Organization for Standardization (ISO) 14001 framework provides another crucial standard for environmental management systems. Construction companies must establish measurable objectives, implement monitoring systems, and undergo regular audits to maintain certification.
Emerging standards like the Task Force on Climate-related Financial Disclosures (TCFD) are gaining prominence, requiring organizations to report on climate-related risks and opportunities. These frameworks demand sophisticated data collection systems and transparent reporting mechanisms.
To ensure compliance, construction firms typically employ specialized sustainability managers or consultants who oversee data collection, verification, and reporting processes. Regular internal audits, combined with external verification, help maintain certification status and ensure continuous improvement in sustainability performance. Documentation must be detailed, accurate, and readily available for stakeholder review and certification renewal processes.
Implementing sustainability metrics in construction projects is a critical step toward achieving measurable environmental, social, and economic improvements. Throughout this discussion, we’ve explored various key metrics that can drive sustainable outcomes, from energy efficiency and water conservation to waste management and social impact measurements. The success of these metrics lies not just in their selection but in their proper implementation and continuous monitoring.
To begin implementing these sustainability metrics in your projects, start by establishing clear baseline measurements and setting realistic, achievable targets. Prioritize metrics that align with your organization’s specific goals and regulatory requirements. Consider developing a phased approach, beginning with essential metrics like energy consumption and waste reduction before expanding to more complex measurements.
Create a robust data collection and monitoring system, ensuring all stakeholders understand their roles in tracking and reporting. Regular reviews and adjustments will help optimize your sustainability strategy over time. Invest in training your team members to properly understand and utilize these metrics, as their engagement is crucial for success.
Remember that sustainability metrics should be living measurements that evolve with your projects and organization. Stay informed about industry best practices, emerging standards, and new measurement technologies. By maintaining flexibility while ensuring consistency in measurement approaches, you can build a sustainable framework that delivers tangible results and contributes to the broader goals of environmental stewardship and social responsibility in construction.