Energy-efficient technologies have revolutionized modern construction, delivering unprecedented reductions in operational costs while meeting increasingly stringent environmental regulations. Through smart building energy management systems and advanced materials, today’s buildings can achieve up to 40% greater energy efficiency compared to conventional structures. Industry leaders are rapidly adopting integrated solutions that combine IoT sensors, automated controls, and high-performance building envelopes to optimize energy consumption in real-time.
The convergence of artificial intelligence, machine learning, and building automation has created a new paradigm in construction technology, where predictive analytics and dynamic response systems continuously adjust building operations to maximize efficiency. These innovations not only reduce environmental impact but also provide significant returns on investment, with many projects reporting complete system cost recovery within 3-5 years of implementation.
For construction professionals and decision-makers, understanding and implementing these technologies has become crucial for maintaining competitive advantage and meeting evolving client demands for sustainable, high-performance buildings. The following analysis examines the most effective energy-efficient technologies currently available and their practical applications in modern construction projects.
Advanced Building Envelope Technologies
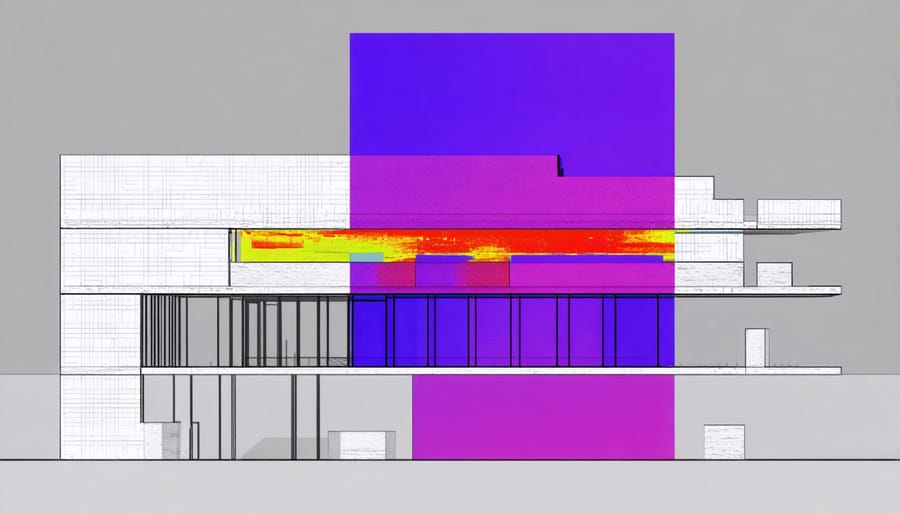
Smart Insulation Materials
Smart insulation materials represent a significant advancement in energy efficient building technologies, with phase-change materials (PCMs) and aerogel insulation leading the innovation curve. PCMs are engineered to absorb, store, and release thermal energy during phase transitions, effectively maintaining consistent indoor temperatures while reducing HVAC loads. These materials can be integrated into building elements such as walls and ceiling panels, providing thermal regulation without additional mechanical systems.
Aerogel insulation, often called “frozen smoke,” represents another breakthrough in thermal management. With a thermal conductivity as low as 0.015 W/mK, aerogels offer superior insulation performance while being remarkably lightweight. Their nano-porous structure, comprising 95-99% air, creates an extremely effective barrier against heat transfer. Recent developments have made aerogel blankets and panels more commercially viable for construction applications.
Implementation studies have shown that buildings utilizing PCMs can reduce heating and cooling energy consumption by 20-30%, while aerogel insulation can achieve thermal resistance values up to R-20 per inch, significantly outperforming traditional materials. These advanced materials are particularly valuable in retrofit projects where space constraints limit conventional insulation options, and in new construction where maximum energy efficiency is paramount.
High-Performance Windows and Glazing
Recent advancements in window technology have revolutionized building envelope performance, with electrochromic glass and vacuum-insulated glazing leading the innovation frontier. Electrochromic glass systems utilize an electrical current to alter the window’s tint level, automatically responding to external conditions and occupant preferences. This dynamic glazing can reduce solar heat gain by up to 77% during peak hours while maintaining optimal natural light levels and views.
Vacuum-insulated glazing (VIG) represents another breakthrough in thermal performance. By creating a vacuum between two glass panes, VIG achieves R-values three to four times higher than conventional double-glazing systems. These units typically measure only 8.3mm in thickness, making them ideal for both new construction and retrofit applications.
The implementation of these technologies has shown remarkable results in commercial applications. The Edge building in Amsterdam, featuring electrochromic glazing throughout its facade, reports a 42% reduction in energy costs related to heating, cooling, and lighting. Similarly, a recent retrofit project in Singapore using VIG demonstrated an annual energy savings of 31% compared to conventional glazing systems.
While initial costs remain higher than traditional windows, the ROI typically materializes within 3-5 years through reduced HVAC loads and lighting requirements. Integration with building management systems further optimizes performance, allowing for automated control based on occupancy patterns, weather conditions, and energy pricing.
Intelligent HVAC Systems
AI-Powered Climate Control
Machine learning algorithms are revolutionizing climate control systems, offering unprecedented efficiency in building energy management. Modern AI-powered building systems can reduce HVAC energy consumption by 20-30% through predictive analytics and real-time optimization.
These intelligent systems utilize multiple data points, including occupancy patterns, weather forecasts, thermal loads, and historical performance metrics to make dynamic adjustments. Advanced sensors deployed throughout the building create a comprehensive network that feeds real-time information to the central AI controller, enabling precise temperature and humidity control in different zones.
Recent implementations in commercial buildings have demonstrated remarkable results. For instance, a 50-story office building in Singapore achieved a 25% reduction in cooling costs after implementing AI-driven climate control. The system learned occupancy patterns over three months and optimized air handling units accordingly, maintaining comfort levels while minimizing energy waste.
Key features of modern AI climate control systems include:
– Predictive maintenance scheduling based on equipment performance analysis
– Dynamic load balancing across multiple HVAC units
– Automated adjustment of ventilation rates based on CO2 levels and occupancy
– Integration with weather forecasting systems for proactive temperature management
The technology’s self-learning capabilities enable continuous improvement in efficiency. As these systems gather more operational data, their algorithms become increasingly accurate at predicting and responding to building climate needs, resulting in enhanced energy savings and occupant comfort levels.
For optimal implementation, construction professionals should focus on proper sensor placement, system integration capabilities, and scalable architecture that can accommodate future technological advances.
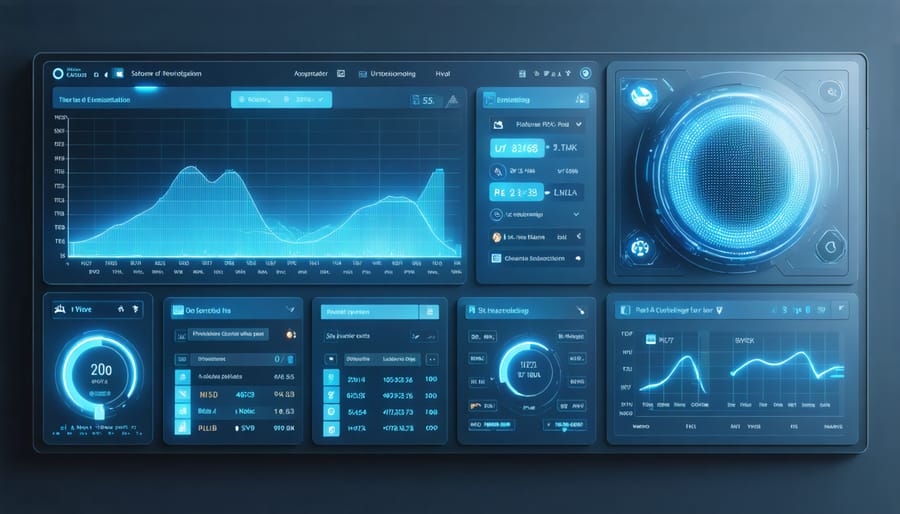
Heat Recovery Systems
Heat recovery systems represent a significant advancement in building energy efficiency, capturing and repurposing thermal energy that would otherwise be lost to the environment. Energy Recovery Ventilation (ERV) systems are particularly effective, transferring both heat and moisture between incoming and outgoing air streams, maintaining optimal indoor conditions while reducing HVAC energy consumption by 40-80%.
Modern heat recovery solutions extend beyond ventilation to include waste heat utilization from various building processes. Industrial facilities can recover heat from manufacturing operations, while commercial buildings often capture thermal energy from refrigeration systems and IT equipment. These recovered energy streams can be redirected to pre-heat water, support space heating, or facilitate other thermal processes.
Advanced heat exchangers, including plate, rotary, and run-around systems, form the core of these recovery solutions. Plate heat exchangers offer high efficiency with no moving parts, while rotary systems excel in moisture transfer capabilities. Run-around systems provide flexibility by allowing heat transfer between non-adjacent spaces.
Implementation costs typically range from $5-15 per square foot, with ROI periods of 2-5 years depending on climate conditions and energy prices. Building operators report average energy savings of 20-40% on heating and cooling costs after installing comprehensive heat recovery systems. These systems are particularly valuable in extreme climates where temperature differentials create significant recovery potential.
Smart Lighting Solutions
Advanced LED Technologies
Recent advancements in LED technology have revolutionized energy-efficient lighting solutions in construction. The latest generation of smart LEDs incorporates advanced control systems, enabling dynamic adjustment of light output based on occupancy patterns and ambient light conditions. These systems can achieve energy savings of up to 80% compared to traditional lighting solutions.
Quantum dot LED technology represents a significant breakthrough, offering enhanced color accuracy and luminous efficacy exceeding 200 lumens per watt. This innovation particularly benefits spaces requiring precise color rendering, such as retail environments and architectural displays.
Tunable white LED systems are gaining prominence in commercial and healthcare facilities, supporting circadian rhythm management through automated color temperature adjustments throughout the day. These systems have demonstrated improved occupant well-being and productivity while maintaining optimal energy efficiency.
Mini and micro LED applications are emerging as game-changers for large-scale architectural lighting. These ultra-compact solutions provide superior brightness and control granularity while reducing power consumption by up to 40% compared to conventional LED arrays.
Integration with building management systems through IoT-enabled LED fixtures allows for predictive maintenance and real-time energy optimization. Advanced sensors and machine learning algorithms continuously adjust lighting parameters, ensuring optimal performance while minimizing energy waste.
Automated Lighting Controls
Automated lighting controls represent a significant advancement in energy efficiency, combining sophisticated sensor technology with intelligent management systems to optimize lighting usage. These systems utilize occupancy sensors, photocells, and programmable timers to ensure lights operate only when needed and at appropriate intensity levels.
Motion and occupancy sensors detect human presence and automatically adjust lighting accordingly, reducing energy waste in unoccupied spaces. Advanced systems incorporate passive infrared (PIR) and ultrasonic technologies, offering coverage ranges of up to 2,000 square feet per sensor with 98% accuracy in detection.
Daylight harvesting systems leverage natural light to decrease artificial lighting requirements. Photosensors continuously monitor ambient light levels and automatically dim or brighten artificial lighting to maintain consistent illumination while maximizing energy savings. Studies show that properly implemented daylight harvesting can reduce lighting energy consumption by 20-60%.
Modern automated lighting controls often integrate with building management systems (BMS) through protocols like DALI or BACnet, enabling centralized control and monitoring. These systems provide detailed usage analytics, helping facility managers identify additional energy-saving opportunities and optimize lighting schedules based on occupancy patterns.
Implementation costs typically see returns within 2-3 years through reduced energy consumption and extended lamp life, making automated lighting controls a cost-effective solution for both new construction and retrofits.
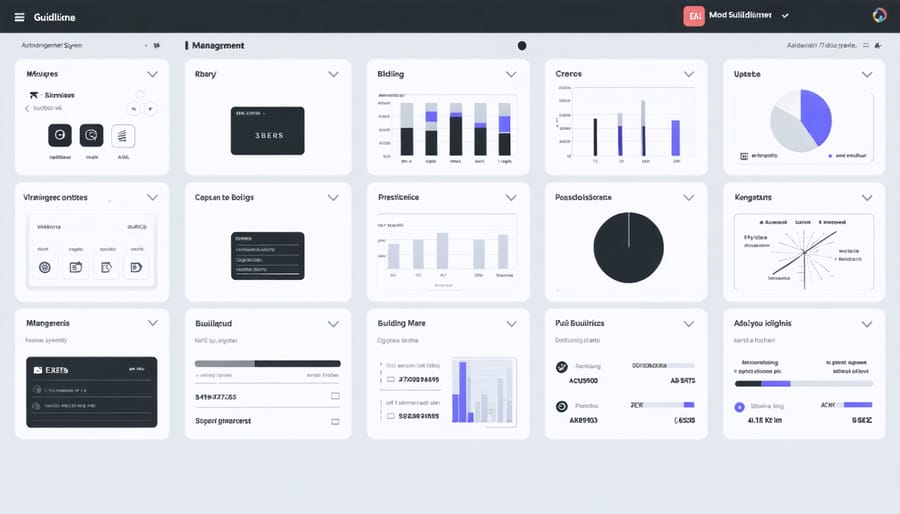
Building Energy Management Systems (BEMS)
Real-Time Energy Monitoring
Real-time energy monitoring systems have revolutionized how construction projects and buildings manage their energy consumption, forming a cornerstone of modern sustainable energy solutions. Smart metering infrastructure, coupled with advanced analytics platforms, provides unprecedented visibility into energy usage patterns and operational inefficiencies.
These systems utilize a network of IoT sensors and meters that continuously collect data on electricity consumption, HVAC performance, lighting systems, and other energy-consuming equipment. The collected data is processed through sophisticated analytics engines that provide actionable insights through user-friendly dashboards.
Key capabilities include load profiling, peak demand analysis, and anomaly detection. Building managers can identify energy waste in real-time, allowing for immediate corrective actions. For instance, the system can detect equipment operating outside optimal hours or HVAC systems running inefficiently, triggering automated alerts for maintenance teams.
Recent implementations have demonstrated significant results. A commercial office building in Singapore achieved a 23% reduction in energy consumption within six months of deployment, while a manufacturing facility in Germany optimized its production schedule based on energy usage patterns, resulting in 15% cost savings.
The integration of artificial intelligence and machine learning algorithms has further enhanced these systems’ capabilities, enabling predictive maintenance and automated optimization of building systems based on historical data and usage patterns.
Predictive Maintenance
Predictive maintenance powered by artificial intelligence represents a significant advancement in managing energy-efficient building systems. By analyzing real-time data from sensors and equipment, AI algorithms can detect potential failures before they occur, optimizing maintenance schedules and preventing energy waste from malfunctioning systems.
Studies show that AI-driven predictive maintenance can reduce energy consumption by 10-15% while extending equipment life by up to 20%. The technology utilizes machine learning to establish baseline performance metrics and identify patterns that indicate potential issues. For instance, when an HVAC system begins consuming more energy than its established baseline, the AI can flag this anomaly for investigation before it leads to significant efficiency losses.
Modern building management systems (BMS) integrate these predictive capabilities with smart sensors that monitor various parameters including temperature, humidity, vibration, and power consumption. The AI processes this data to create detailed maintenance forecasts, allowing facility managers to schedule interventions during off-peak hours and optimize resource allocation.
A notable case study from a commercial office complex in Singapore demonstrated that implementing predictive maintenance reduced unexpected equipment failures by 85% and decreased maintenance costs by 30% while maintaining optimal energy efficiency levels. The system paid for itself within 18 months through reduced operational costs and energy savings.
Integration with existing building automation systems is typically straightforward, making predictive maintenance a practical solution for both new construction and retrofitting projects.
The integration of energy-efficient technologies in construction continues to revolutionize how we approach building design and operation. As demonstrated throughout this analysis, these innovations offer substantial benefits, including average energy savings of 30-50% compared to conventional building methods, significant reductions in operational costs, and enhanced occupant comfort and productivity.
The future outlook for energy-efficient construction technologies is particularly promising. Industry experts project that the global market for smart building technologies will exceed $100 billion by 2025, driven by increasing environmental regulations, rising energy costs, and growing awareness of sustainability imperatives. Emerging technologies such as AI-powered building management systems, advanced thermal storage solutions, and next-generation photovoltaic materials are poised to further transform the industry.
Key success factors for implementation include comprehensive planning, proper integration of various systems, and ongoing monitoring and maintenance. Construction professionals must stay informed about evolving technologies and best practices while considering the specific requirements of each project. The return on investment for energy-efficient technologies continues to improve, with many solutions now offering payback periods of less than five years.
As we move forward, the adoption of energy-efficient technologies will become increasingly crucial for meeting sustainability goals and maintaining competitive advantage in the construction industry. Organizations that embrace these innovations early will be better positioned to meet future regulatory requirements and client demands while contributing to global environmental objectives.