Virtual Design and Construction (VDC) stands at the forefront of construction’s digital revolution, transforming how we plan, execute, and deliver complex building projects. By integrating 3D modeling, real-time collaboration tools, and data-driven decision-making processes, VDC empowers construction teams to identify conflicts before breaking ground, reduce costly rework, and accelerate project delivery timelines by up to 30%.
In today’s competitive construction landscape, where margins are tight and schedules demanding, VDC emerges as the critical differentiator between project success and failure. Leading construction firms leveraging VDC report an average of 15-20% reduction in project costs, 25% improvement in labor productivity, and significant enhancement in stakeholder communication and coordination.
The convergence of Building Information Modeling (BIM), artificial intelligence, and cloud computing has elevated VDC from a mere visualization tool to an comprehensive project management framework. This technological ecosystem enables construction professionals to simulate construction sequences, optimize resource allocation, and ensure precise execution of complex designs while maintaining strict quality standards.
For construction executives and project managers seeking to maintain competitive advantage in an increasingly digital industry, understanding and implementing VDC isn’t just an option—it’s an imperative. The methodology’s ability to integrate design, construction, and operational data creates a single source of truth that drives informed decision-making throughout the project lifecycle.
The Core Components of Virtual Design & Construction
Building Information Modeling (BIM) Integration
Building Information Modeling serves as the cornerstone of successful Virtual Design and Construction implementation, providing a comprehensive digital framework that integrates all aspects of construction projects. At its core, 3D BIM modeling creates detailed, data-rich representations of building components, enabling teams to visualize, analyze, and optimize designs before physical construction begins.
The integration of BIM within VDC processes facilitates enhanced collaboration among stakeholders through a centralized information platform. This unified approach allows architects, engineers, contractors, and owners to access real-time project data, coordinate activities, and identify potential conflicts early in the development phase. The model serves as a single source of truth, containing vital information about building components, specifications, and performance requirements.
BIM’s capability to generate accurate quantity takeoffs, cost estimates, and construction schedules directly supports VDC’s objective of improving project predictability and efficiency. Through parametric modeling and automated clash detection, teams can resolve design conflicts virtually, significantly reducing costly on-site modifications and delays.
Furthermore, BIM integration enables sophisticated analysis of building performance, sustainability factors, and lifecycle costs. This comprehensive approach to project planning and execution aligns perfectly with VDC’s goals of optimizing construction processes and delivering superior project outcomes.
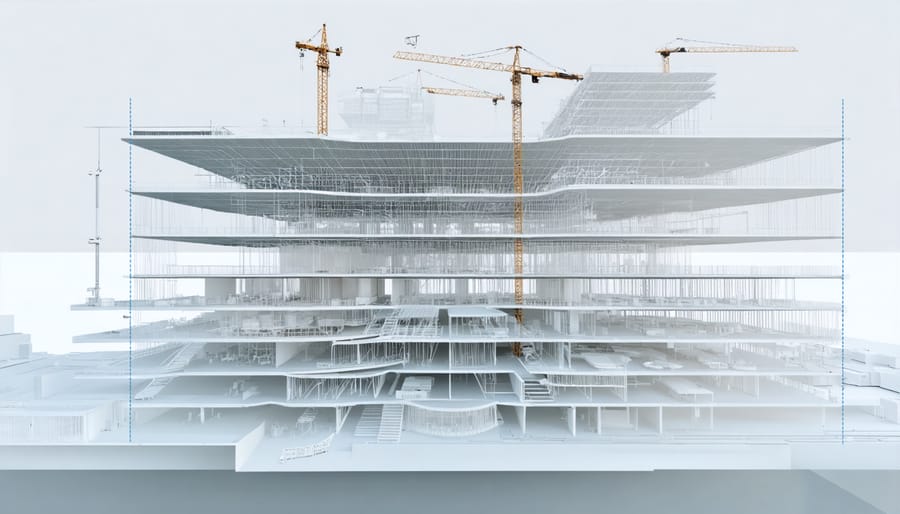
Digital Collaboration Tools and Platforms
In modern VDC implementation, digital collaboration tools serve as the backbone of successful project delivery. Cloud-based platforms like Autodesk BIM 360, Procore, and PlanGrid enable real-time coordination among project stakeholders, regardless of their physical location. These platforms integrate essential features such as document management, version control, and clash detection capabilities.
Common Building Information Modeling (BIM) software solutions, including Revit, Navisworks, and Tekla, facilitate seamless information exchange between different disciplines. Project teams utilize these tools alongside specialized communication platforms like Microsoft Teams and Slack for daily coordination and decision-making processes.
Virtual meeting spaces and augmented reality interfaces are increasingly becoming standard in VDC workflows, allowing teams to conduct virtual site walks and design reviews. These technologies, combined with mobile applications and cloud storage solutions, create a comprehensive ecosystem that supports efficient project delivery while maintaining data security and accessibility throughout the construction lifecycle.
Data Analytics and Project Intelligence
In modern construction projects, data-driven decision making has become fundamental to successful VDC implementation. Advanced analytics tools process vast amounts of project data, providing actionable insights for optimization and risk management. These systems aggregate information from multiple sources, including BIM models, IoT sensors, and project management platforms, to create comprehensive performance dashboards.
Real-time analytics enable project teams to monitor construction progress, resource utilization, and cost metrics with unprecedented accuracy. By analyzing historical data alongside current project metrics, teams can better predict potential challenges and develop proactive solutions. This predictive capability helps minimize delays, reduce waste, and optimize resource allocation across project phases.
Project intelligence platforms integrate with VDC workflows to provide detailed performance analytics, scheduling optimization, and cost tracking. These platforms utilize machine learning algorithms to identify patterns and anomalies, helping teams make informed decisions about construction sequencing, material procurement, and workforce deployment. The resulting insights drive improved project outcomes, enhanced collaboration, and more efficient construction processes.
Real-World Implementation Strategies
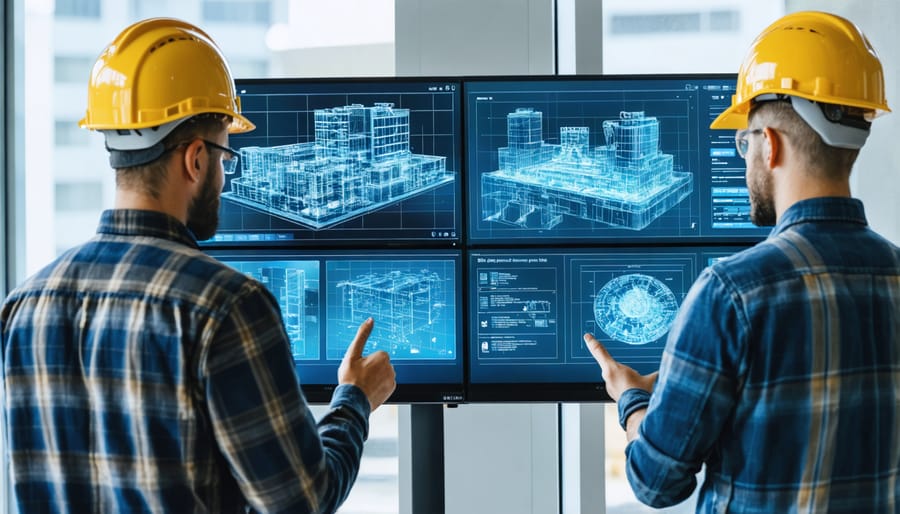
Team Integration and Training
Successful implementation of Virtual Design & Construction requires a strategic approach to team integration and training. Organizations must develop a comprehensive framework that addresses both technical skills and collaborative workflows. This begins with identifying key stakeholders across departments and establishing clear roles and responsibilities within the VDC ecosystem.
Training programs should follow a tiered approach, starting with foundational concepts and progressing to advanced applications. Core team members require intensive training in VDC software platforms, while project managers and executives need focused sessions on strategic implementation and ROI analysis. Regular workshops and hands-on sessions help reinforce learning and encourage adoption across the organization.
Cross-functional collaboration is essential for VDC success. Organizations should create dedicated spaces for team interaction and establish regular coordination meetings. Building Information Modeling (BIM) coordinators play a crucial role in facilitating communication between design teams, construction managers, and trade contractors.
Change management strategies are vital for overcoming resistance to new technologies and workflows. This includes developing clear protocols for data sharing, establishing standardized processes, and creating feedback mechanisms to continuously improve VDC implementation.
Organizations should also consider partnering with educational institutions and industry experts to maintain current knowledge of emerging technologies and best practices. Measuring team performance through key performance indicators helps track progress and identify areas for improvement in VDC capabilities.
Workflow Optimization
Virtual Design & Construction significantly enhances workflow optimization by streamlining processes across the entire construction lifecycle. Through integrated digital workflows, project teams can eliminate redundancies, reduce errors, and improve collaboration efficiency. The implementation of standardized processes and automated tasks allows for better resource allocation and time management.
Key optimization strategies include establishing centralized data repositories, implementing automated clash detection, and creating standardized digital templates for recurring tasks. These approaches minimize manual intervention and ensure consistency across project phases. By leveraging cloud-based platforms, teams can access real-time information and make informed decisions quickly, reducing delays and improving project outcomes.
Communication protocols within VDC frameworks enable seamless information exchange between stakeholders. Regular virtual coordination meetings, supported by 3D models and integrated project dashboards, facilitate faster problem-solving and decision-making. This collaborative environment reduces the need for rework and accelerates project delivery timelines.
Advanced scheduling tools within VDC systems allow for precise resource planning and allocation. By analyzing historical data and current project metrics, teams can optimize workforce distribution and equipment utilization. This data-driven approach leads to more accurate project timelines and cost estimates.
The implementation of automated quality control processes and progress tracking mechanisms ensures consistent adherence to project standards. Regular performance analytics help identify bottlenecks and areas for improvement, enabling continuous workflow refinement throughout the project lifecycle.
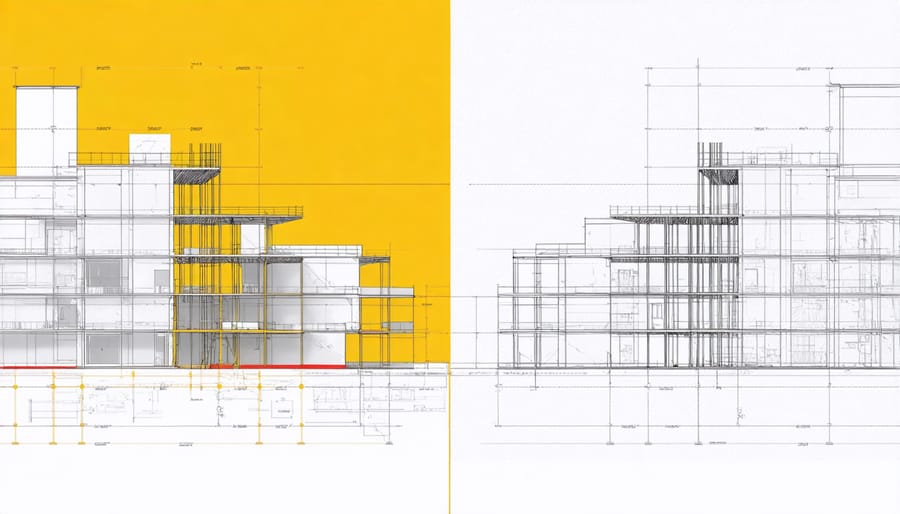
Quality Control and Risk Management
Virtual Design and Construction significantly enhances quality control processes and risk management through its comprehensive digital modeling and simulation capabilities. By creating detailed virtual representations before physical construction begins, project teams can identify potential conflicts, safety hazards, and quality issues early in the development phase.
The model-based quality control process enables teams to perform thorough clash detection, ensuring that building systems and components integrate seamlessly. This proactive approach drastically reduces rework costs and schedule delays that typically arise from unforeseen conflicts discovered during construction.
Risk management is substantially improved through VDC’s ability to simulate construction sequences and analyze potential failure points. Project teams can virtually test different scenarios and construction methodologies, identifying optimal approaches while minimizing exposure to safety risks and technical challenges. This capability is particularly valuable in complex projects where traditional risk assessment methods might miss critical interdependencies.
Quality metrics can be embedded directly within the virtual model, allowing for automated checking against design standards and regulatory requirements. Real-time monitoring and reporting capabilities enable project managers to track quality indicators throughout the construction process, ensuring compliance with project specifications and maintaining high standards of workmanship.
The integration of VDC with quality management systems creates a documented trail of decision-making and quality control measures, providing valuable data for continuous improvement and risk mitigation strategies in future projects.
Case Study: VDC Success in Action
The Shanghai Tower project stands as a compelling example of VDC implementation at its finest. This 632-meter skyscraper, completed in 2015, showcased how Virtual Design and Construction can transform a complex construction project’s execution and outcomes.
The project team, led by Gensler architects and the Shanghai Construction Group, implemented a comprehensive VDC strategy from the earliest planning stages. They utilized an integrated BIM platform that connected over 30 different disciplines, including structural engineering, MEP systems, and façade design. This integration enabled real-time collaboration among team members spread across multiple continents.
One of the most significant challenges was the tower’s unique twisted form and double-skin façade system. The VDC team created detailed 3D models that simulated wind loads and structural responses, leading to design optimizations that reduced material usage by 32% compared to initial estimates. Virtual mock-ups allowed stakeholders to evaluate design alternatives without physical construction, saving approximately $58 million in potential rework costs.
The construction sequence was meticulously planned using 4D modeling, which linked the 3D model with the project schedule. This approach helped identify and resolve over 600 potential conflicts before they materialized on site. The team also utilized cloud-based collaboration tools, enabling instantaneous updates and decision-making across the project team.
Key success metrics from the project included:
– 16% reduction in overall construction time
– 25% decrease in material waste
– 35% improvement in labor productivity
– Zero major safety incidents during construction
– $91 million in total cost savings
The project’s clash detection processes alone prevented an estimated 98% of potential field conflicts, demonstrating the power of virtual coordination. The team’s use of mobile devices on-site connected to the VDC platform enabled real-time access to current model information, ensuring construction accuracy and reducing errors.
Perhaps most importantly, the project established new benchmarks for sustainable construction practices. The VDC implementation enabled precise material quantity calculations and optimization of building systems, contributing to the building’s LEED Platinum certification.
This case study demonstrates how strategic VDC implementation can deliver substantial benefits in complex construction projects, from cost savings and schedule compression to enhanced safety and sustainability outcomes. The Shanghai Tower’s success has influenced VDC adoption in subsequent mega-projects worldwide.
Future Trends and Innovations
AI and Machine Learning Integration
The integration of AI in construction has revolutionized Virtual Design and Construction practices, introducing unprecedented levels of automation and analytical capabilities. Machine learning algorithms now enhance clash detection, optimize building designs, and predict potential construction challenges before they materialize on-site.
Advanced AI systems analyze vast quantities of project data to identify patterns and correlations that human observers might miss. This capability enables more accurate cost estimations, schedule optimization, and resource allocation. For instance, AI-powered platforms can process thousands of historical project records to predict potential delays and suggest mitigation strategies.
In the realm of design optimization, machine learning algorithms evaluate multiple design iterations simultaneously, considering factors such as energy efficiency, material usage, and construction feasibility. These systems can generate alternative design solutions that meet specified criteria while maintaining project constraints.
Real-time monitoring and analysis have been transformed through AI integration. Smart sensors and IoT devices feed data into AI systems that continuously assess construction progress, safety conditions, and quality control metrics. This enables project managers to make data-driven decisions and implement corrective measures proactively.
Looking ahead, emerging AI applications in VDC include generative design capabilities, automated code compliance checking, and predictive maintenance modeling. These advancements are setting new standards for project efficiency and risk management in the construction industry.
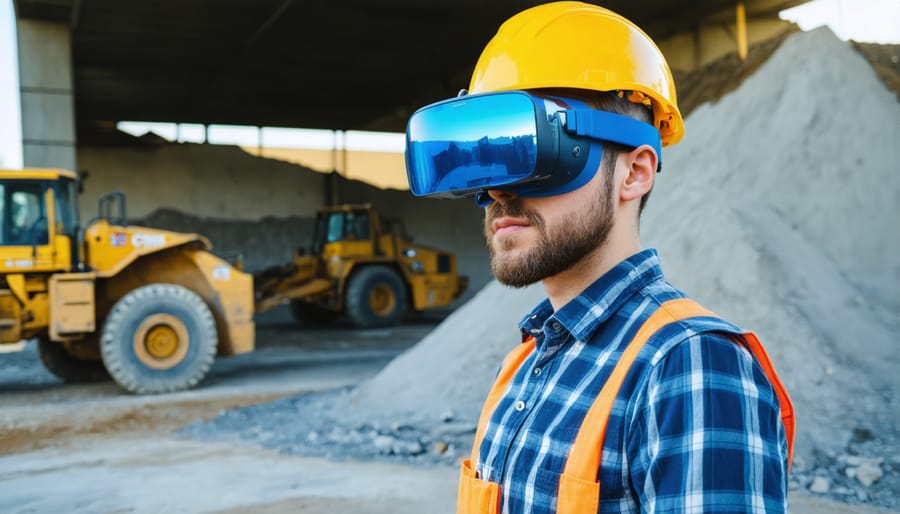
Mixed Reality and Advanced Visualization
Mixed Reality (MR) and advanced visualization tools are revolutionizing how construction professionals interact with virtual designs and project data. By combining elements of virtual and augmented reality with digital twins technology, these solutions enable teams to visualize, analyze, and modify designs in unprecedented ways.
Modern MR platforms allow stakeholders to walk through virtual buildings before construction begins, identifying potential conflicts and optimizing spatial arrangements. Using devices like Microsoft HoloLens or similar headsets, project teams can overlay digital models onto physical construction sites, ensuring precise alignment between virtual designs and actual construction progress.
These visualization tools have demonstrated significant benefits in complex projects, including a 25% reduction in design review time and a 40% decrease in coordination-related errors. For instance, the recent expansion of Singapore’s Changi Airport utilized MR technology to coordinate mechanical systems installation, resulting in zero major clashes during construction.
Advanced visualization also enhances collaboration between remote teams, allowing real-time design modifications and immediate feedback from stakeholders worldwide. Project managers can conduct virtual site walks with clients, while engineers can inspect building systems through x-ray-like views of structures, all without physical presence on site.
As these technologies continue to mature, they’re becoming increasingly integrated with BIM workflows, artificial intelligence, and real-time data analytics, creating a more comprehensive and intuitive project visualization ecosystem.
Virtual Design & Construction has proven to be a transformative force in the construction industry, delivering substantial benefits across project lifecycles. The implementation of VDC practices consistently demonstrates improved project outcomes through enhanced collaboration, reduced errors, optimized schedules, and significant cost savings. Organizations that have successfully adopted VDC report up to 25% reduction in project delivery time and up to 20% decrease in construction costs.
To successfully implement VDC in your organization, consider the following actionable steps: First, assess your current technological capabilities and identify gaps that need addressing. Begin with a pilot project to test and refine your VDC processes, ensuring your team gains confidence and expertise gradually. Invest in comprehensive training programs for staff at all levels, as successful VDC implementation relies heavily on team competency and buy-in.
Establish clear protocols for data management and communication channels, ensuring seamless information flow between stakeholders. Standardize your VDC processes across projects while maintaining flexibility to accommodate project-specific requirements. Partner with experienced VDC consultants or hire specialized professionals to guide your implementation journey and accelerate the learning curve.
Remember that successful VDC adoption is an iterative process that requires ongoing commitment and refinement. Regular assessment of outcomes, gathering feedback from team members, and staying current with technological advancements will help optimize your VDC implementation strategy. Focus on measuring and documenting ROI to justify continued investment and expansion of VDC capabilities.
The future of construction clearly lies in digital transformation, with VDC at its core. Organizations that embrace this change now will be better positioned to compete in an increasingly technology-driven industry. By following these implementation guidelines and maintaining a long-term perspective, construction firms can successfully navigate the transition to VDC-enabled operations and realize its full potential for delivering superior project outcomes.