In today’s high-performance building landscape, R-value materials stand as the cornerstone of energy efficiency optimization. These thermal resistance champions determine a structure’s ability to maintain consistent indoor temperatures while minimizing energy consumption. Recent advances in material science have revolutionized insulation technology, offering construction professionals unprecedented control over thermal performance. From aerogel-enhanced panels boasting R-values of 10.3 per inch to vacuum-insulated panels delivering R-values up to 50 per inch, modern building materials are redefining what’s possible in thermal resistance. As construction costs and energy regulations continue to evolve, understanding the scientific principles, application methods, and cost-benefit analyses of high-R-value materials has become essential for industry leaders committed to delivering superior building performance. This comprehensive examination explores cutting-edge insulation technologies, their practical implementations, and the economic implications that shape modern construction decisions.
Understanding R-Value: Beyond the Numbers
What R-Value Really Measures
R-value quantifies a material’s capacity to resist heat flow, measured in units of (ft²·°F·h/BTU) in imperial units or (m²·K/W) in metric. This thermal resistance measurement indicates how effectively a material impedes the transfer of heat through conduction, with higher values signifying better insulating properties.
The measurement is determined by calculating the difference in temperature across the material’s thickness, divided by the heat flux through it. This relationship is expressed through Fourier’s Law of Heat Conduction, where R-value is inversely proportional to the material’s thermal conductivity and directly proportional to its thickness.
In practical applications, R-value becomes particularly significant when evaluating building envelope performance. A material with an R-value of 19 resists heat flow nearly twice as effectively as one with an R-value of 10. However, it’s crucial to understand that R-value benefits don’t scale linearly – doubling the thickness of insulation doesn’t necessarily double its effective thermal resistance.
Construction professionals should note that R-values are typically measured under ideal laboratory conditions at 75°F (24°C), and actual performance may vary with temperature fluctuations, moisture content, and installation quality.
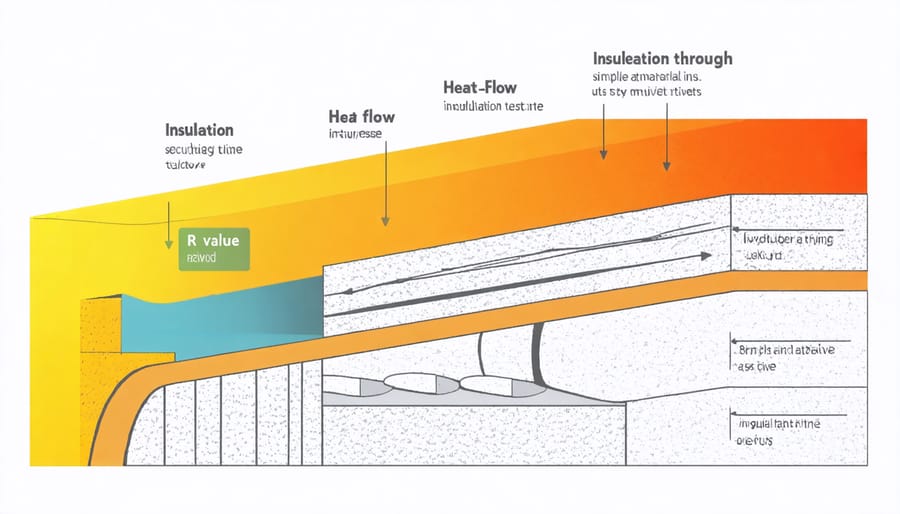
Why R-Value Matters in Modern Construction
In today’s construction landscape, R-value has become a critical metric that directly impacts building performance and operational costs. As energy costs continue to rise and sustainability regulations become more stringent, the importance of proper insulation cannot be overstated. Recent studies show that buildings with optimized R-values can reduce heating and cooling costs by up to 40%, making them essential for energy-efficient commercial construction projects.
Building codes across North America and Europe now mandate minimum R-value requirements, reflecting growing awareness of their role in environmental protection and energy conservation. These regulations have pushed the industry toward innovative insulation solutions and advanced building envelope designs. The impact extends beyond mere compliance; higher R-values contribute to improved occupant comfort, reduced HVAC system wear, and enhanced building durability.
From a financial perspective, investing in materials with appropriate R-values typically yields positive returns within 3-5 years through reduced energy costs. This ROI becomes even more compelling when considering government incentives and green building certifications, which often reward superior thermal performance with tax benefits and increased property values.
High-Performance Insulation Materials
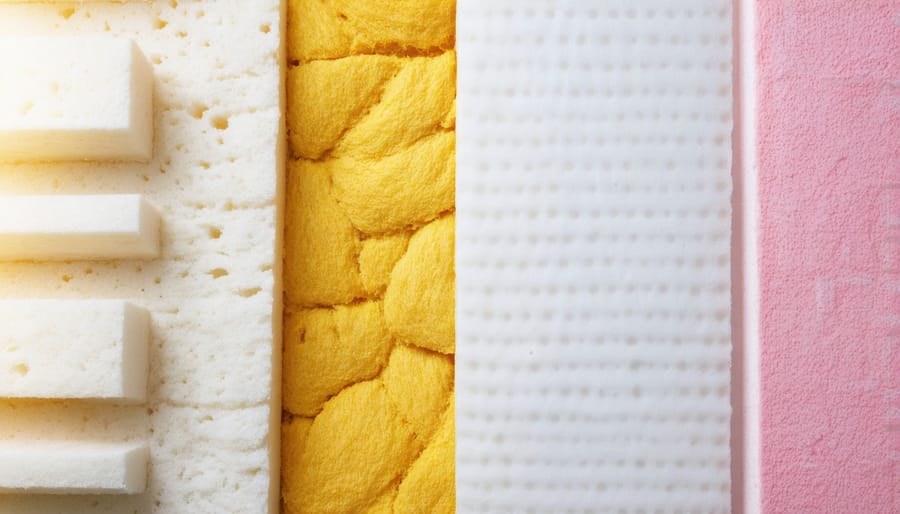
Traditional Insulation Solutions
Traditional insulation materials remain the cornerstone of building envelope design, offering proven performance and established R-value ratings. Fiberglass, the most widely used insulation material, consists of fine glass fibers and typically achieves R-values between 2.2 and 3.8 per inch. Available in both batts and loose-fill forms, fiberglass excels in both wall cavity and attic applications, providing consistent thermal resistance when properly installed.
Cellulose insulation, made from recycled paper products treated with fire retardants, delivers R-values of 3.2 to 3.8 per inch. Its density and ability to fill irregular spaces make it particularly effective for retrofit projects and areas with complex framing. The material’s capacity to reduce air infiltration often results in better real-world performance compared to laboratory R-value ratings.
Mineral wool, also known as rock wool or slag wool, offers R-values between 3.0 and 3.3 per inch while providing superior fire resistance and sound attenuation. Its water-resistant properties and dimensional stability make it ideal for demanding applications in commercial construction. The material maintains its R-value even in extreme temperature conditions, offering consistent performance throughout its service life.
Each of these traditional solutions presents specific advantages in terms of cost-effectiveness, installation requirements, and long-term performance. Their established track record and well-documented thermal properties continue to make them reliable choices for meeting building code requirements and energy efficiency goals.
Advanced Synthetic Materials
In the realm of advanced building materials, synthetic insulation technologies have revolutionized thermal efficiency in construction. Polyurethane foam leads the industry with R-values ranging from R-5.5 to R-6.5 per inch, significantly outperforming traditional materials. Available in both closed-cell and open-cell variants, polyurethane offers exceptional air-sealing properties and moisture resistance when properly installed.
Expanded polystyrene (EPS) and extruded polystyrene (XPS) continue to evolve, with newer formulations achieving R-values of R-4 to R-5 per inch. These materials maintain their thermal performance over time and offer excellent dimensional stability. Recent developments in graphene-enhanced polystyrene have shown promising results, potentially increasing R-values by up to 20% while reducing material thickness.
Emerging technologies include vacuum insulated panels (VIPs), which achieve remarkable R-values of R-25 to R-30 per inch. Though currently expensive for widespread application, VIPs represent the future of high-performance building envelopes. Phase-change materials (PCMs) integrated into synthetic insulation systems are also gaining traction, offering dynamic thermal regulation capabilities that complement traditional R-value measurements.
These advanced materials often incorporate recycled content and low-GWP blowing agents, addressing both performance and sustainability requirements in modern construction projects.
Breakthrough Insulation Technologies
Recent advancements in insulation technology have revolutionized the construction industry’s approach to thermal efficiency. Aerogels, originally developed for aerospace applications, now represent one of the most promising breakthrough materials. With an R-value of R-10 per inch, silica aerogels offer nearly twice the insulating performance of traditional materials while being incredibly lightweight and fire-resistant.
Vacuum Insulated Panels (VIPs) have emerged as another groundbreaking solution, delivering R-values of R-25 to R-30 per inch. These panels consist of a microporous core material enclosed in an airtight envelope under vacuum conditions. While their initial cost remains higher than conventional materials, VIPs are particularly valuable in projects where space constraints necessitate maximum thermal performance in minimal thickness.
Looking toward future innovations, researchers are developing phase-change materials (PCMs) that actively manage heat transfer by absorbing and releasing thermal energy. Smart insulation systems incorporating graphene and carbon nanotubes show promise in creating responsive building envelopes that adapt to environmental conditions.
Advanced manufacturing techniques, including 3D printing of insulation materials, are enabling the creation of optimized cellular structures that maximize thermal resistance while minimizing material usage. These developments, combined with ongoing research into bio-based composites and hybrid materials, suggest a future where building insulation becomes increasingly efficient, sustainable, and adaptable to specific project requirements.
Optimizing R-Value in Building Design
Strategic Material Selection
The strategic selection of building materials based on their R-values requires careful consideration of multiple factors, including climate zone, building type, and specific application requirements. In regions with extreme temperatures, whether hot or cold, materials with higher R-values become crucial for maintaining optimal thermal performance. This approach aligns with modern construction systems that prioritize energy efficiency.
For cold climates, materials like closed-cell spray foam insulation (R-6.5 per inch) and polyisocyanurate rigid foam boards (R-6.0 to R-6.5 per inch) offer superior thermal resistance. In contrast, hot climates may benefit from reflective insulation systems combined with traditional materials to manage heat gain effectively.
Building professionals should consider the placement and exposure of materials within the structure. Roof assemblies typically require higher R-values than walls due to direct solar exposure and heat loss patterns. Below-grade applications demand moisture-resistant materials with consistent R-values under varying conditions.
The material’s long-term performance characteristics are equally important. Some materials may experience R-value degradation over time, while others maintain their thermal properties throughout their service life. Factors such as moisture susceptibility, compression resistance, and dimensional stability should influence material selection.
Cost-effectiveness analysis should encompass not just initial material expenses but also installation complexity, durability, and potential energy savings. High-performance materials with superior R-values may command premium prices but often justify their cost through reduced energy consumption and enhanced building comfort over time.
Installation Best Practices
Proper installation is critical for maximizing the effectiveness of R-value building materials. Start by ensuring all surfaces are clean, dry, and free from debris before installation. When installing insulation, maintain consistent compression across the entire surface area, as over-compression can reduce R-value effectiveness by up to 50%.
Create continuous thermal barriers by avoiding gaps between insulation pieces. Use proper cutting tools to achieve precise fits around electrical boxes, plumbing, and other penetrations. For fibrous insulation, install pieces snugly between framing members without forcing or stretching the material.
Vapor barriers require careful attention during installation. Position them on the warm side of the wall assembly in most climate zones to prevent moisture accumulation. Overlap seams by at least 6 inches and seal them with appropriate tape or mastic. Pay special attention to corners and joints where air infiltration commonly occurs.
For rigid foam insulation, use compatible adhesives or mechanical fasteners as recommended by the manufacturer. Install boards in a staggered pattern to minimize thermal bridging through seams. When using multiple layers, offset the joints between layers to create a more effective thermal barrier.
Quality control during installation is essential. Regular inspections should verify proper material density, thickness, and coverage. Document environmental conditions during installation, as temperature and humidity can affect material performance. Address any gaps, compression issues, or moisture problems immediately to maintain the designed R-value performance.
Protect installed materials from weather exposure and mechanical damage during construction. Schedule insulation installation to minimize the time between placement and covering with finishing materials. This careful attention to installation details ensures the specified R-values are achieved and maintained throughout the building’s lifecycle.
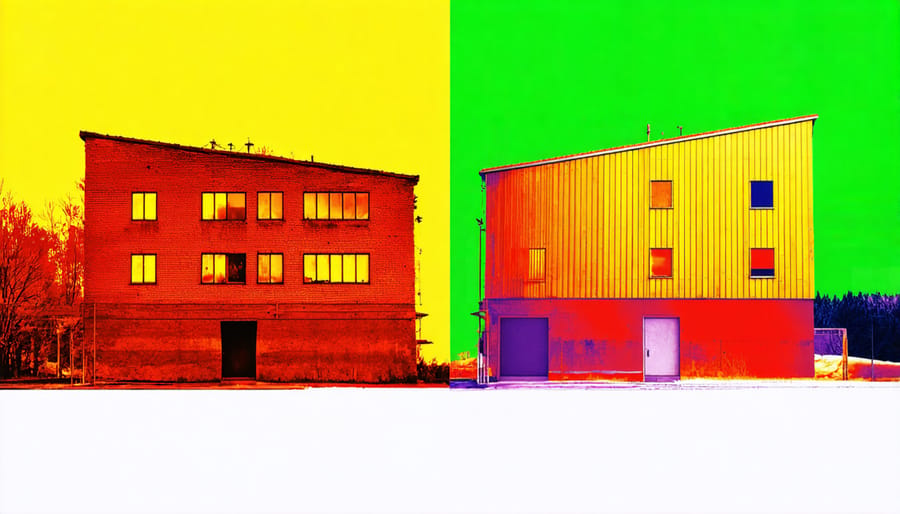
Cost-Benefit Analysis of High R-Value Materials
When evaluating high R-value materials for construction projects, the initial investment must be weighed against long-term energy savings and operational costs. Premium insulation materials like closed-cell spray foam, which offers R-values of 6.0-7.0 per inch, typically cost 2-3 times more than traditional fiberglass batts. However, analysis shows that these materials often pay for themselves within 5-7 years through reduced energy consumption.
A recent industry study examining commercial buildings in varied climate zones demonstrated that buildings utilizing high R-value materials achieved 30-40% reduction in annual heating and cooling costs compared to those meeting minimum code requirements. This translates to approximately $0.75-1.25 per square foot in annual energy savings, depending on local utility rates and climate conditions.
The cost-benefit equation also factors in installation expenses and material longevity. While materials like polyisocyanurate panels have higher upfront costs ($1.00-1.50 per square foot), their superior durability and resistance to settling can reduce maintenance and replacement needs over the building’s lifetime. Structural Insulated Panels (SIPs), though initially more expensive, reduce labor costs by combining structural elements with insulation.
Installation costs vary significantly between materials. Traditional fiberglass might cost $0.50-1.00 per square foot to install, while spray foam applications can range from $2.00-3.50 per square foot. However, higher R-value materials often require less thickness to achieve desired thermal performance, potentially reducing overall wall cavity requirements and preserving valuable floor space.
Environmental conditions and local energy codes significantly impact ROI calculations. In extreme climate zones, premium insulation materials typically achieve ROI 30-40% faster than in moderate regions. Additionally, many jurisdictions offer incentives and tax rebates for exceeding minimum energy efficiency requirements, further improving the financial equation for high-performance materials.
When conducting cost-benefit analyses, professionals should consider the building’s intended lifespan, local energy costs, climate zone requirements, and potential future energy price increases to make informed decisions about insulation investments.
The evolution of R-value building materials continues to shape the future of sustainable construction. As energy efficiency requirements become more stringent, manufacturers are developing innovative solutions that combine higher thermal resistance with improved sustainability profiles. The emergence of nano-engineered materials and advanced composites promises even greater thermal performance while reducing material thickness and weight. Economic considerations remain crucial, but declining costs of high-performance insulation materials are making them increasingly viable for mainstream construction projects. Looking ahead, the industry can expect continued advancement in smart insulation systems, bio-based materials, and hybrid solutions that optimize both thermal performance and environmental impact. Success in future construction projects will depend on balancing these technological innovations with practical implementation and cost-effectiveness while meeting ever-evolving energy efficiency standards.