Robotics and automation are fundamentally reshaping the construction industry, delivering unprecedented gains in productivity, safety, and precision. From autonomous excavators navigating job sites to robotic arms performing complex welding operations, these technologies are addressing the sector’s most pressing challenges – labor shortages, project delays, and quality control issues. Industry leaders implementing robotics solutions report up to 30% reduction in project completion times and a 25% decrease in construction costs.
The convergence of artificial intelligence, sensors, and advanced robotics is enabling construction firms to automate traditionally manual tasks while gathering crucial real-time data for informed decision-making. Specialized robots now handle everything from bricklaying and concrete finishing to site surveying and structural monitoring, working alongside human workers to enhance capabilities rather than replace them.
As construction faces increasing demands for sustainability, efficiency, and worker safety, robotics technology offers a compelling solution. Early adopters are already demonstrating how automated systems can operate 24/7, maintain consistent quality standards, and significantly reduce workplace injuries. With the global construction robotics market projected to reach $7.9 billion by 2027, this technological revolution is rapidly becoming an essential consideration for forward-thinking construction firms seeking to maintain their competitive edge.
The Evolution of Construction Robotics
From Manual to Automated: Key Milestones
The evolution of construction automation has transformed the industry through several pivotal developments. In the 1960s, the introduction of basic programmable machines marked the first step toward automated construction processes. The 1980s saw the emergence of computer-aided design (CAD) systems, revolutionizing project planning and visualization.
A significant breakthrough came in the early 2000s with the development of autonomous equipment for earthwork and material handling. By 2010, 3D printing technology began making inroads into construction, enabling the creation of complex structural components with unprecedented precision. The integration of artificial intelligence and machine learning algorithms in 2015 enhanced robotic systems’ ability to adapt to varying site conditions and tasks.
Recent milestones include the deployment of collaborative robots (cobots) in 2018, designed to work alongside human workers safely, and the introduction of swarm robotics in 2020, allowing multiple robots to coordinate complex construction tasks. These developments have significantly improved project efficiency, worker safety, and construction quality while reducing costs and completion times.
IoT Integration and Smart Construction Sites
IoT integration has revolutionized how robotic systems operate on modern construction sites, creating interconnected networks that enhance efficiency and productivity. Through strategic placement of sensors and smart devices, construction robots can now communicate and coordinate their activities while sharing crucial real-time data across the project ecosystem.
These smart construction environments utilize advanced IoT platforms to monitor multiple parameters simultaneously, including equipment location, operational status, and environmental conditions. Construction managers can access this information through centralized dashboards, enabling immediate decision-making and resource optimization.
The integration of IoT with robotics has enabled automated workflow management, where machines can adjust their operations based on real-time feedback from other connected devices. For instance, autonomous vehicles can modify their routes based on site conditions reported by environmental sensors, while robotic arms can adjust their material handling patterns according to inventory management systems.
Data collected through IoT networks also supports predictive maintenance schedules for robotic equipment, reducing downtime and extending machinery lifespan. This seamless integration of IoT and robotics creates a more responsive, efficient, and safer construction environment, where all components work in harmony to achieve project objectives.
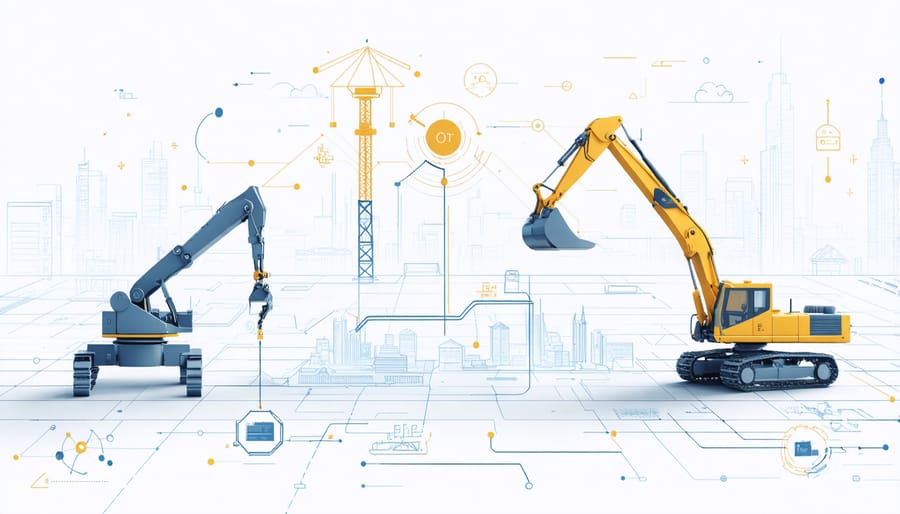
Current Applications of Robotics in Construction
Automated Material Handling and Transportation
Automated material handling systems are revolutionizing construction sites by streamlining logistics and reducing manual labor requirements. These robotic solutions include autonomous mobile robots (AMRs), automated guided vehicles (AGVs), and sophisticated crane systems that can precisely transport materials across construction sites with minimal human intervention.
Recent implementations demonstrate significant efficiency gains, with some projects reporting up to 30% reduction in material handling time. For instance, the deployment of robotic material handlers at a major commercial development in Singapore achieved a 25% increase in productivity while reducing workplace accidents by 40%.
These systems utilize advanced sensors and AI algorithms to navigate complex construction environments safely. Modern robotic handlers can automatically identify, sort, and transport various construction materials, from structural components to finishing materials. They excel at repetitive tasks like brick distribution, panel transportation, and inventory management.
Key benefits include:
– Enhanced worker safety by reducing heavy lifting requirements
– Improved inventory tracking through integrated RFID systems
– Consistent 24/7 operation capability
– Reduced material damage during transport
– Optimized site logistics through real-time tracking
However, successful implementation requires careful planning and integration with existing workflows. Construction managers must consider factors such as site layout, material flow patterns, and integration with Building Information Modeling (BIM) systems to maximize the effectiveness of automated handling solutions.
Looking ahead, the integration of 5G technology and advanced AI will further enhance these systems’ capabilities, enabling more sophisticated coordination between multiple robotic handlers and improved adaptation to dynamic construction environments.
Precision Assembly and 3D Printing
Precision assembly and additive manufacturing technologies are revolutionizing construction processes through automated systems that deliver unprecedented accuracy and efficiency. 3D printing robots are now capable of constructing complex structural elements with minimal human intervention, reducing labor costs while maintaining exceptional quality standards.
Recent implementations have demonstrated the ability to print entire building components, from wall sections to architectural features, with tolerances as precise as 1mm. These systems utilize advanced computer vision and sensor arrays to ensure proper material deposition and structural integrity throughout the construction process.
Robotic assembly systems are particularly effective in prefabrication facilities, where controlled environments enable precise manipulation of building components. These systems excel in tasks such as steel beam placement, panel installation, and complex joinery work that traditionally required extensive manual labor and time.
The integration of machine learning algorithms has enhanced these systems’ adaptive capabilities, allowing them to adjust to material variations and environmental conditions in real-time. This intelligence, combined with sophisticated end-effectors and multi-axis movement, enables robots to handle diverse construction materials and perform intricate assembly sequences with remarkable precision.
Industry leaders report up to 60% reduction in assembly time and a 45% decrease in material waste when implementing these automated systems, making them increasingly attractive for large-scale construction projects where efficiency and precision are paramount.
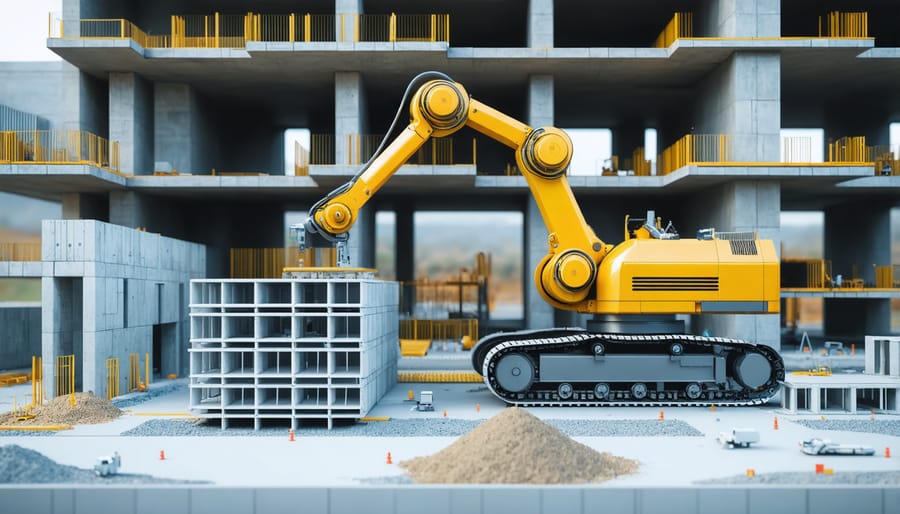
Quality Control and Site Monitoring
Robotic systems are revolutionizing quality control and monitoring processes in construction, offering unprecedented precision and reliability in site supervision. Advanced sensors and AI-powered robots are now capable of conducting comprehensive inspections that were traditionally performed by human inspectors, reducing errors and increasing efficiency.
These automated systems utilize computer vision and LiDAR technology to perform real-time quality assessments of structural elements, material placement, and dimensional accuracy. For instance, Boston Dynamics’ Spot robot, equipped with 360-degree cameras and specialized sensors, can autonomously navigate construction sites, documenting progress and identifying potential issues before they become costly problems.
Recent developments in site monitoring innovations have introduced drones and crawling robots that can access hard-to-reach areas, performing detailed structural inspections and thermal imaging analysis. These systems generate detailed reports and 3D visualizations, enabling project managers to make data-driven decisions quickly.
Quality control robots are particularly effective at detecting non-conformities in concrete work, welding, and building envelope installations. They can measure tolerances within millimeters and compare actual construction against BIM models in real-time. This level of precision ensures compliance with specifications and building codes while maintaining consistent documentation throughout the project lifecycle.
The integration of these robotic systems with cloud-based platforms allows for immediate data sharing and analysis, creating a transparent and efficient quality management process that enhances project outcomes and reduces rework costs.
Implementation Challenges and Solutions
Cost and ROI Considerations
Implementing robotics in construction requires careful financial analysis and strategic planning. Initial investment costs for construction robots typically range from $50,000 to $500,000 per unit, depending on complexity and capabilities. However, these figures should be considered alongside potential returns and long-term cost savings.
ROI calculations must factor in several key elements: reduced labor costs, increased productivity, improved safety metrics, and decreased material waste. Case studies from leading construction firms indicate that well-implemented robotics solutions can achieve ROI within 18-36 months. For instance, automated bricklaying systems have demonstrated up to 300% efficiency improvements compared to traditional methods.
Operating costs include maintenance, software updates, training, and energy consumption. However, these are often offset by reduced insurance premiums, lower worker compensation claims, and decreased project timeline overruns. Industry data suggests that construction robots can reduce overall project costs by 20-30% when properly integrated into existing workflows.
To maximize ROI, companies should consider scalable solutions that can be deployed across multiple projects. Leasing options and robotics-as-a-service models are emerging as alternatives to outright purchases, making advanced automation more accessible to mid-sized contractors. Additionally, government incentives and tax benefits for implementing innovative construction technologies can help offset initial investments.
For optimal financial outcomes, organizations should conduct thorough cost-benefit analyses, considering both immediate project requirements and long-term strategic goals before investing in construction robotics.
Integration with Existing Workflows
Successfully integrating robotics into existing construction workflows requires a strategic, phased approach that minimizes disruption while maximizing efficiency gains. The key lies in identifying specific processes where automation can provide immediate value without compromising established safety protocols or quality standards.
Start by conducting a comprehensive workflow analysis to determine which tasks are most suitable for robotic integration. Common entry points include material handling, repetitive tasks like bricklaying, and quality inspection processes. Implementation should begin with pilot programs in controlled environments, allowing teams to familiarize themselves with the new technology while maintaining productivity.
Training programs are essential for successful integration. Construction teams need dedicated instruction on operating robotic systems, understanding their limitations, and managing the human-robot interface. This includes establishing clear communication protocols and defining roles between automated systems and human workers.
Data integration platforms play a crucial role in connecting robotic systems with existing project management software, BIM models, and scheduling tools. These platforms ensure seamless information flow and real-time coordination between automated and manual processes.
Consider creating hybrid workflows where robots and human workers complement each other’s strengths. For example, robots can handle precise, repetitive tasks while skilled workers focus on complex decision-making and quality oversight. This approach helps maintain workforce engagement while improving overall project efficiency.
Regular assessment and adjustment of integration strategies ensure continuous improvement and optimal performance as teams become more comfortable with robotic systems.
Future Outlook and Industry Impact
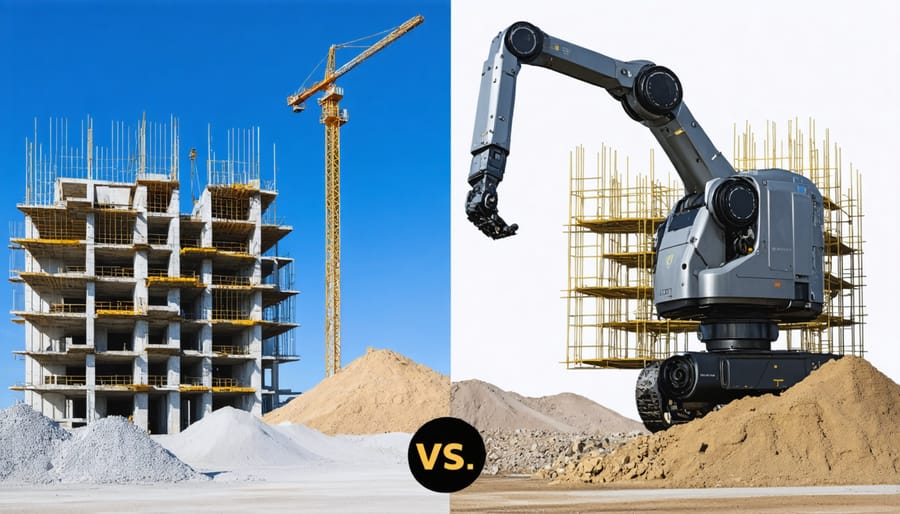
Emerging Technologies and Applications
The construction industry is witnessing a remarkable evolution in robotic technologies that promise to revolutionize building processes. Advanced autonomous systems equipped with computer vision and machine learning capabilities are being developed to handle complex tasks like brick laying, concrete finishing, and structural assembly. These innovations are complemented by AI predictive maintenance systems that ensure optimal performance and reduced downtime.
Exoskeletons are emerging as a game-changing technology, enhancing worker capabilities while reducing physical strain and injury risks. These wearable robotic systems are becoming more sophisticated, with newer models featuring enhanced ergonomics and longer battery life, making them increasingly practical for daily construction tasks.
3D printing robots are advancing beyond experimental phases, with several companies developing large-scale systems capable of printing entire building structures. These machines can work continuously, significantly reducing construction time while maintaining precise specifications.
Swarm robotics is another promising development, where multiple autonomous robots collaborate to complete complex tasks. These systems are being tested for applications like site surveying, material transportation, and assembly operations, offering unprecedented efficiency and coordination.
Drone technology is evolving to include advanced sensors and real-time mapping capabilities, enabling more accurate site monitoring and progress tracking. Integration with Building Information Modeling (BIM) systems is creating seamless workflows between design, construction, and quality control processes.
Workforce Implications and Skills Development
The integration of robotics in construction is reshaping workforce dynamics, creating both challenges and opportunities for industry professionals. While some traditional roles may be automated, new positions focusing on robot operation, maintenance, and programming are emerging. Construction workers increasingly need to develop hybrid skill sets that combine conventional construction knowledge with technological expertise.
Key areas of skills development include robotic system operation, data analysis, and digital workflow management. Project managers and site supervisors must understand both construction processes and robotic capabilities to effectively integrate automated systems into existing workflows. Technical training programs and certifications in construction robotics are becoming essential for career advancement.
Despite automation concerns, the construction industry is experiencing a shift rather than a reduction in labor demands. Skilled workers are needed to oversee robotic operations, maintain equipment, and handle complex tasks that require human judgment. Companies are investing in upskilling programs to help their workforce adapt to new technologies while retaining valuable industry experience.
Educational institutions and industry organizations are responding by developing specialized curricula that combine traditional construction skills with robotics training. This evolution in skills requirements is creating opportunities for workers to increase their value through technological proficiency while maintaining their core construction expertise. Success in this transformed landscape requires a commitment to continuous learning and adaptation to emerging technologies.
The integration of robotics in construction represents a fundamental shift in how we approach building projects. As demonstrated throughout this article, automated systems and robotic solutions are increasingly becoming essential tools for improving efficiency, safety, and quality in construction operations. Industry professionals should prioritize developing comprehensive robotics implementation strategies, focusing on worker training, technology assessment, and phased adoption approaches. The key to success lies in selecting solutions that address specific operational challenges while providing measurable returns on investment. Construction leaders must stay informed about emerging technologies, engage with technology providers, and foster a culture of innovation within their organizations. By embracing robotics while maintaining a balanced approach to implementation, construction firms can position themselves at the forefront of industry evolution, ensuring long-term competitiveness and operational excellence in an increasingly automated construction landscape.