Transform your supply chain operations through robust compliance risk management protocols that safeguard project integrity and streamline regulatory adherence. Modern construction supply chains face unprecedented complexity, with global material sourcing, stringent environmental regulations, and intricate supplier networks demanding sophisticated oversight mechanisms.
Digital compliance tracking platforms, real-time supplier documentation verification, and automated compliance alerts now represent the cornerstone of effective supply chain governance. Leading construction firms leverage these tools to maintain continuous regulatory alignment while reducing administrative burden and minimizing project delays.
Industry leaders acknowledge that supply chain compliance extends beyond mere regulatory checkbox exercises. It encompasses sustainable sourcing practices, ethical labor standards, quality control protocols, and comprehensive risk mitigation strategies. By implementing systematic compliance frameworks, construction organizations can protect their operations, enhance stakeholder trust, and secure competitive advantages in an increasingly scrutinized marketplace.
This strategic approach to supply chain compliance delivers measurable improvements in project outcomes, supplier relationship management, and operational efficiency. Forward-thinking construction professionals recognize that robust compliance programs serve as foundational elements for sustainable growth and operational excellence.
The Evolution of Supply Chain Compliance in Construction
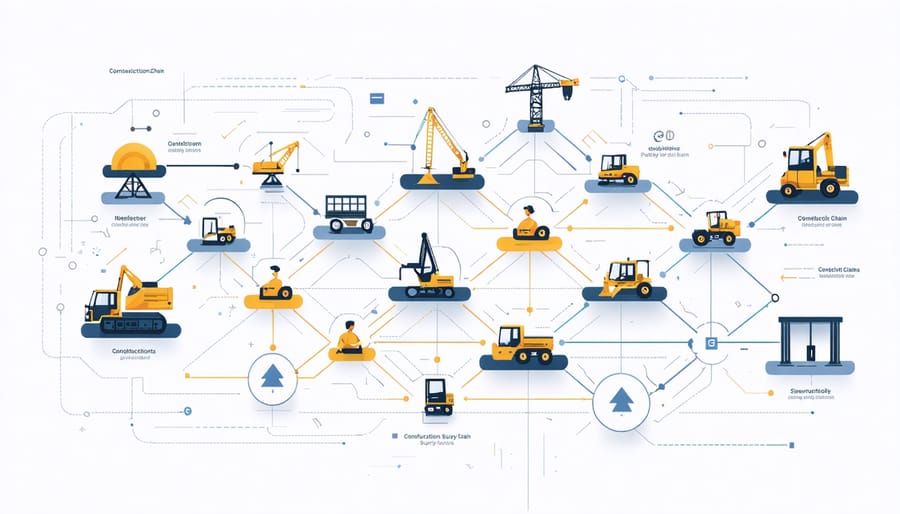
Key Regulatory Requirements
Construction supply chain compliance is governed by multiple regulatory frameworks that demand strict adherence. At the forefront are essential OSHA regulations that establish baseline safety requirements for materials handling and storage. The International Building Code (IBC) and local building codes set specific standards for material quality and sourcing, while environmental regulations like the EPA’s guidelines govern sustainable procurement practices.
Companies must also comply with the Buy American Act for federal projects, which requires the use of domestically produced materials unless specifically exempted. The Foreign Corrupt Practices Act (FCPA) impacts international supply chains, ensuring transparency in overseas material sourcing and vendor relationships.
Material traceability requirements have become increasingly stringent, with many jurisdictions now requiring detailed documentation of material origins and specifications. Supply chain participants must maintain comprehensive records of compliance certifications, testing reports, and chain of custody documentation. Additionally, emerging regulations around carbon footprint reporting and sustainable sourcing are reshaping compliance requirements for construction supply chains.
Modern Compliance Challenges
Construction companies today face unprecedented challenges in maintaining compliant supply chains, driven by increasingly complex regulatory requirements and global market dynamics. Material traceability has become particularly demanding, with firms needing to verify the origin and quality of components across multiple tiers of suppliers. This complexity is further amplified by evolving environmental regulations and sustainability requirements that demand detailed documentation of carbon footprints and material compositions.
Digital transformation presents both opportunities and obstacles, as companies struggle to integrate new tracking systems while maintaining compatibility with legacy processes. The COVID-19 pandemic has highlighted vulnerabilities in traditional supply chain models, forcing organizations to reassess their risk management strategies and supplier diversification approaches.
Labor compliance has emerged as another critical concern, with increased scrutiny on working conditions and fair labor practices throughout the supply network. Construction firms must now monitor not only their direct suppliers but also sub-suppliers for adherence to labor standards and safety regulations.
Additionally, geopolitical tensions and trade restrictions have created uncertainty in material sourcing, while rapid price fluctuations and material shortages require more sophisticated procurement strategies and alternative supplier arrangements.
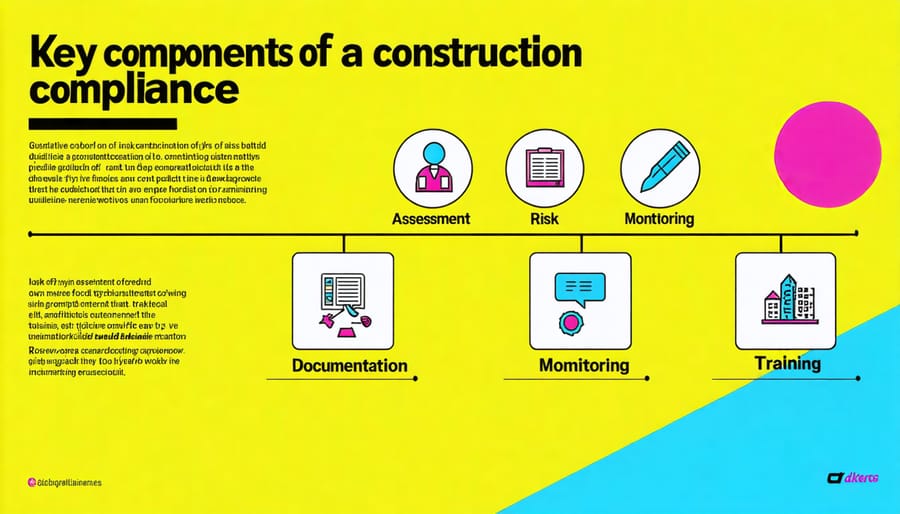
Building a Robust Compliance Framework
Risk Assessment and Due Diligence
Effective risk assessment and due diligence form the cornerstone of robust supply chain compliance in construction. The process begins with a systematic evaluation of potential suppliers using a multi-tiered approach that considers financial stability, operational capacity, safety records, and regulatory compliance history.
Construction firms should implement a standardized supplier assessment framework that includes both quantitative and qualitative metrics. Key evaluation criteria should encompass financial health indicators, past project performance, quality management systems, and environmental compliance records. This assessment should be supported by thorough background checks, including verification of licenses, certifications, and insurance coverage.
Due diligence investigations should extend beyond surface-level checks to include site visits, reference checks, and detailed analysis of supplier operations. Modern construction companies are increasingly utilizing digital tools and databases to streamline this process, enabling real-time monitoring of supplier performance and compliance status.
Risk matrices should be developed to categorize suppliers based on criticality and potential impact on project delivery. High-risk suppliers warrant enhanced scrutiny and more frequent audits, while lower-risk vendors may require less intensive monitoring. Regular reassessment is crucial, as supplier risk profiles can change over time due to market conditions, regulatory changes, or organizational restructuring.
Documentation of all assessment findings and due diligence activities is essential for maintaining transparency and demonstrating compliance with regulatory requirements. This documentation should be regularly reviewed and updated to reflect changing risk landscapes and emerging compliance requirements.
Documentation and Reporting Systems
Effective documentation and reporting systems form the backbone of supply chain compliance in construction projects. These systems must capture and track material specifications, certifications, supplier qualifications, and delivery schedules while maintaining clear audit trails. Digital documentation platforms have become industry standard, enabling real-time tracking and automated compliance verification.
Key documentation requirements typically include material safety data sheets (MSDS), certificates of conformance, quality control reports, and supplier performance metrics. Organizations should implement standardized templates and workflows to ensure consistency across all documentation processes. Regular reporting intervals should be established, with clear escalation protocols for non-compliance issues.
Modern construction firms increasingly utilize integrated project management software that incorporates supply chain documentation features. These systems enable automated alerts for expiring certifications, upcoming compliance deadlines, and potential risks. Cloud-based solutions facilitate secure information sharing among stakeholders while maintaining version control and access permissions.
To ensure documentation effectiveness, organizations should conduct periodic audits of their reporting systems, update procedures based on regulatory changes, and provide regular training to staff responsible for documentation management. This systematic approach helps maintain compliance while reducing administrative burden and potential errors.
Supplier Qualification and Monitoring
Effective supplier qualification and monitoring requires a systematic approach that combines rigorous initial assessment with ongoing performance evaluation. The process begins with comprehensive pre-qualification screenings, including financial stability checks, safety record reviews, and verification of necessary certifications. Construction companies must establish clear quality control standards and compliance metrics against which potential suppliers are evaluated.
Regular audits and performance assessments form the cornerstone of ongoing monitoring efforts. These should include scheduled site visits, documentation reviews, and real-time tracking of key performance indicators (KPIs). Implementation of digital monitoring systems can streamline this process, providing instant alerts for compliance issues and maintaining detailed supplier scorecards.
Risk-based monitoring frameworks help organizations allocate resources effectively by focusing more attention on critical suppliers and high-risk materials. This approach should incorporate both quantitative metrics, such as delivery performance and defect rates, and qualitative factors like responsiveness to corrective actions and commitment to continuous improvement. Regular review meetings with key suppliers ensure alignment with compliance requirements and facilitate proactive problem-solving.
Technology and Compliance Management
Digital Solutions for Compliance Tracking
In today’s complex construction environment, digital solutions have become essential tools for effective compliance tracking across supply chains. Modern software platforms offer comprehensive features that enable real-time monitoring, automated reporting, and proactive risk management.
Cloud-based compliance management systems provide centralized platforms where stakeholders can access, update, and verify compliance documentation. These systems typically include features such as supplier qualification databases, certification tracking, and automated alert systems for expiring certifications or permits.
Leading solutions incorporate artificial intelligence and machine learning capabilities to analyze patterns, predict potential compliance issues, and suggest corrective actions before problems escalate. Integration with procurement systems ensures that only approved suppliers meeting compliance requirements can be selected for projects.
Mobile applications extend these capabilities to the field, allowing site managers to verify compliance status, conduct inspections, and document issues in real-time. Digital documentation systems maintain secure audit trails and streamline regulatory reporting processes.
Enterprise resource planning (ERP) systems with dedicated compliance modules offer seamless integration between supply chain management, quality control, and compliance tracking. These systems can monitor multiple compliance parameters simultaneously, from material certifications to worker qualifications and safety requirements.
Advanced analytics dashboards provide executives with comprehensive visibility into compliance metrics, helping identify trends, bottlenecks, and areas requiring attention. This data-driven approach enables organizations to make informed decisions and continuously improve their compliance programs while maintaining efficient operations.
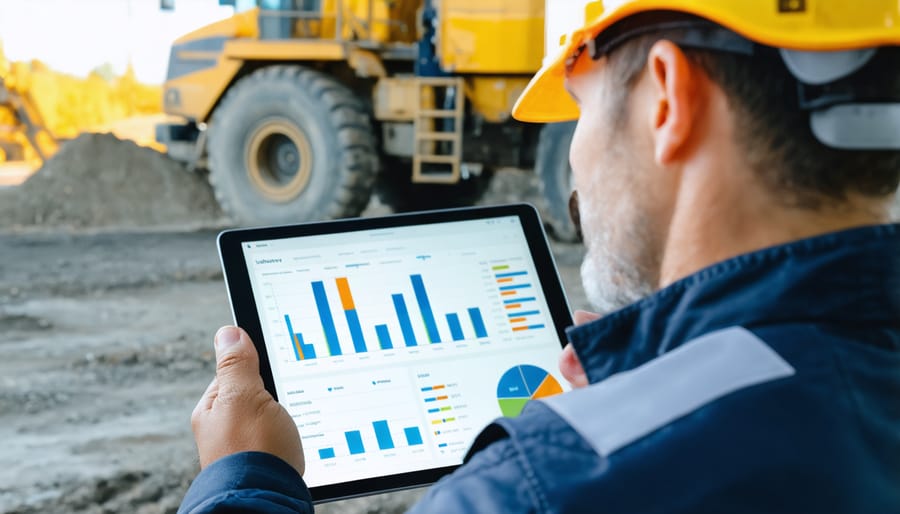
Data Analytics and Reporting
In today’s digital-driven construction environment, data analytics plays a pivotal role in maintaining and improving supply chain compliance. Advanced analytics platforms enable companies to monitor supplier performance, track material origins, and ensure adherence to data privacy compliance requirements in real-time.
Construction firms are increasingly implementing automated reporting systems that provide comprehensive visibility across the supply chain. These systems collect and analyze data from multiple touchpoints, including supplier assessments, delivery performance metrics, quality control reports, and regulatory compliance documentation. By leveraging predictive analytics, organizations can identify potential compliance risks before they materialize and take proactive measures to address them.
Key performance indicators (KPIs) such as supplier compliance rates, documentation accuracy, and certification status are continuously monitored through customized dashboards. This enables project managers and compliance officers to make data-driven decisions and implement corrective actions promptly. Modern analytics tools also facilitate the generation of detailed compliance reports for stakeholders, auditors, and regulatory bodies.
The integration of artificial intelligence and machine learning algorithms has enhanced the capability to detect patterns and anomalies in supply chain data. This technological advancement helps identify non-compliant practices, unauthorized suppliers, or suspicious transaction patterns that might compromise project integrity or regulatory compliance.
Best Practices and Implementation Strategies
Training and Communication
Effective training and communication form the cornerstone of successful supply chain compliance in construction projects. Organizations must develop comprehensive training programs that address both initial onboarding and ongoing education for all stakeholders involved in the supply chain process.
Key personnel should receive specialized training on compliance protocols, regulatory requirements, and risk management strategies. This includes detailed instruction on documentation procedures, supplier verification processes, and material tracking systems. Regular workshops and refresher courses ensure that team members stay current with evolving compliance standards and industry best practices.
Communication strategies should establish clear channels between suppliers, contractors, project managers, and compliance officers. Implementation of standardized reporting templates and regular compliance review meetings helps maintain transparency and accountability throughout the supply chain network.
Digital platforms and management systems play a crucial role in facilitating effective communication. These tools enable real-time updates, automated notifications for compliance deadlines, and centralized document sharing. Regular supplier audits and performance reviews should be communicated through formal channels, with clear documentation of findings and required corrective actions.
Organizations should also develop crisis communication protocols to address potential compliance breaches or supply chain disruptions. This includes establishing a clear chain of command for decision-making and communication during critical situations, ensuring swift and appropriate responses to compliance-related challenges.
Remember to measure the effectiveness of training programs through regular assessments and feedback mechanisms, adjusting content and delivery methods as needed to maximize understanding and retention among all stakeholders.
Continuous Improvement Processes
A robust continuous improvement process is essential for maintaining effective supply chain compliance in construction projects. Regular audits and performance assessments help identify gaps and opportunities for enhancement while ensuring adherence to evolving industry standards and regulations.
To implement an effective continuous improvement framework, organizations should establish quarterly review cycles that evaluate key performance indicators (KPIs) across supplier relationships, material quality, and documentation compliance. These reviews should involve cross-functional teams, including procurement specialists, quality control managers, and project leads.
Data collection and analysis play crucial roles in driving improvements. Modern construction firms utilize digital platforms to track supplier performance metrics, delivery times, and compliance violations. This data-driven approach enables organizations to identify patterns and implement targeted corrective actions.
Best practices for continuous improvement include:
– Regular supplier evaluations and feedback sessions
– Updated risk assessments based on market conditions
– Integration of new compliance requirements into existing processes
– Documentation of lessons learned from previous projects
– Implementation of corrective action plans
– Training programs to address identified knowledge gaps
Construction companies should also establish a formal change management process to ensure smooth implementation of improvements while maintaining operational continuity. This includes clear communication channels, stakeholder engagement strategies, and measurable success metrics.
Annual compliance program reviews should assess the effectiveness of existing protocols and incorporate industry best practices and technological advancements to enhance supply chain management efficiency.
Supply chain compliance in construction continues to evolve as the industry faces new challenges and opportunities. The increasing complexity of global supply networks, coupled with stricter regulatory requirements and sustainability mandates, necessitates a more sophisticated approach to compliance management.
Looking ahead, digital transformation will play a pivotal role in reshaping supply chain compliance. Advanced technologies such as blockchain, IoT sensors, and AI-powered analytics are becoming essential tools for maintaining transparency and traceability throughout the supply chain. These innovations enable real-time monitoring, automated documentation, and predictive risk assessment capabilities that were previously unattainable.
The future of construction supply chain compliance will likely see greater emphasis on environmental sustainability and social responsibility. Companies that proactively address these aspects while maintaining traditional quality and safety standards will gain competitive advantages in an increasingly conscious market.
Key success factors for effective supply chain compliance programs include:
– Comprehensive risk assessment and management strategies
– Integration of digital solutions for monitoring and reporting
– Regular training and development of compliance personnel
– Strong supplier relationships and clear communication channels
– Continuous improvement of compliance processes
As the construction industry continues to globalize, organizations must remain vigilant in adapting their compliance programs to meet emerging challenges. Those who invest in robust compliance frameworks today will be better positioned to navigate future regulatory landscapes and maintain sustainable, resilient supply chains.