Environmental innovations are radically transforming the construction industry, driving unprecedented advances in building efficiency, sustainability, and performance. As global climate challenges intensify, pioneering sustainable design practices and breakthrough technologies are revolutionizing how we conceive, construct, and operate modern buildings.
From carbon-negative concrete alternatives to AI-powered energy management systems, these innovations aren’t just incremental improvements—they’re fundamental shifts in construction methodology. Industry leaders implementing these solutions are reporting up to 40% reductions in energy consumption, 30% decreases in construction waste, and significant improvements in building lifecycle costs.
The convergence of environmental imperatives with technological capabilities has created unprecedented opportunities for construction professionals. Advanced materials, smart systems, and regenerative design principles are now essential components of future-forward building projects, offering both environmental benefits and compelling returns on investment.
This comprehensive analysis examines the most impactful environmental innovations reshaping our industry, providing practical insights for implementation across diverse construction projects and scales.
Smart Materials Revolutionizing Sustainable Construction
Self-Healing Materials and Bio-Concrete
Self-healing materials and bio-concrete represent groundbreaking advances in construction technology, offering solutions that significantly reduce maintenance requirements while extending building lifespans. These innovative materials incorporate living organisms or specialized compounds that actively repair damage without human intervention.
Bio-concrete, developed through extensive research in biomineralization, contains bacterial spores that activate when cracks appear. When exposed to water and oxygen, these bacteria produce limestone, effectively sealing cracks up to 0.8mm wide. Field tests have demonstrated a 20-30% reduction in maintenance costs over traditional concrete structures.
Recent developments include engineered polymers with microcapsules containing healing agents. When material damage occurs, these capsules rupture, releasing compounds that chemically bond to repair the breach. This technology has shown particular promise in structural elements exposed to high stress and environmental factors.
In commercial applications, self-healing materials have demonstrated remarkable durability in infrastructure projects. The Rotterdam Bridge pilot project, implementing self-healing concrete in specific sections, reported an 85% reduction in surface cracks after 12 months of exposure to heavy traffic and weather conditions.
For construction professionals, these materials offer compelling long-term cost benefits despite higher initial investment. Analysis shows that buildings incorporating self-healing materials can achieve a 40% reduction in lifecycle maintenance costs compared to conventional materials. This innovation aligns with sustainable construction practices while meeting stringent durability requirements for modern infrastructure projects.
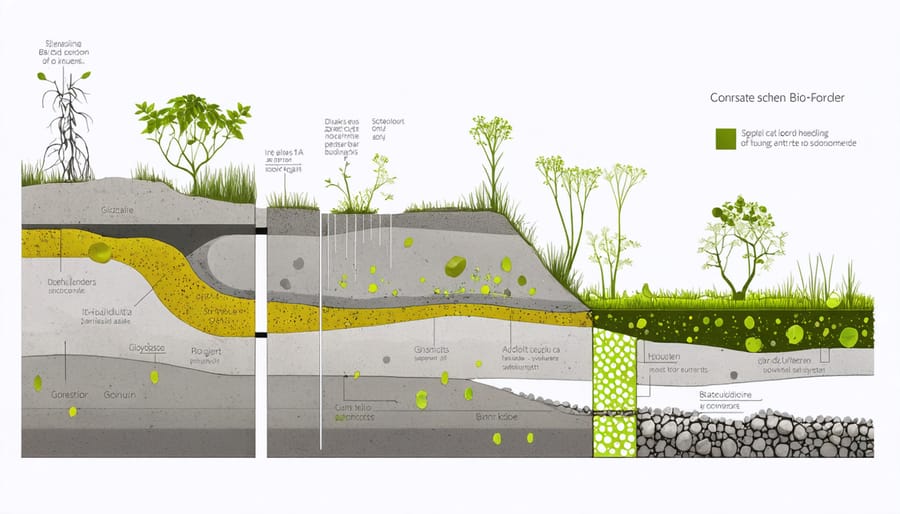
Carbon-Negative Building Components
Carbon-negative building components represent a revolutionary advancement in sustainable construction, offering materials that actively remove CO2 from the atmosphere during their lifecycle. These innovative materials achieve this through advanced carbon sequestration processes and innovative manufacturing techniques.
Biochar-enhanced concrete leads this category, incorporating specially processed organic waste that locks carbon within the material structure while improving strength characteristics. Recent studies indicate that each cubic meter of biochar-concrete can sequester up to 25kg of CO2 equivalent, surpassing traditional concrete’s carbon footprint by a significant margin.
Cross-laminated timber (CLT) treated with carbon-absorbing compounds has emerged as another groundbreaking solution. When sourced from sustainably managed forests and treated with specialized carbon-capturing finishes, these elements can store approximately 1 ton of CO2 per cubic meter while providing excellent structural properties.
Algae-based facade panels represent the latest development in this field. These bio-reactive components not only absorb CO2 through photosynthesis but also generate biomass that can be harvested for energy production. Field tests demonstrate that a 200-square-meter installation can capture the equivalent CO2 of 25 trees annually.
Implementation costs for carbon-negative components have decreased by 30% over the past two years, making them increasingly viable for commercial projects. Leading construction firms report enhanced project sustainability ratings and improved client satisfaction when incorporating these materials into their builds.
Energy Generation and Storage Breakthroughs
Building-Integrated Photovoltaics (BIPV)
Building-Integrated Photovoltaics represents a significant advancement in sustainable architecture, seamlessly merging solar power generation with traditional building elements. Unlike conventional solar panels mounted on existing structures, BIPV systems serve dual purposes: they function as both building materials and power generators, effectively reducing overall construction costs while maximizing energy efficiency.
Modern BIPV solutions include solar glass windows, photovoltaic roof tiles, and solar facade elements that maintain architectural aesthetics while generating clean energy. According to recent industry data, BIPV installations can offset up to 60% of a building’s electricity consumption while providing thermal insulation benefits.
A notable example is the Copenhagen International School, featuring 12,000 solar panels integrated into its facade. The installation generates 300 MWh annually while serving as an architectural statement piece, demonstrating how BIPV can enhance both function and form.
For construction professionals, BIPV implementation requires careful consideration of factors including:
– Solar orientation and shading analysis
– Building code compliance
– Integration with existing electrical systems
– Maintenance accessibility
– Weather resistance and durability
The ROI potential of BIPV systems has improved significantly, with payback periods typically ranging from 7-10 years, depending on location and energy costs. As manufacturing processes advance and efficiency increases, these systems are becoming increasingly cost-competitive with traditional building materials.
The future of BIPV lies in emerging technologies like perovskite solar cells and transparent solar materials, which promise even greater integration possibilities while maintaining high energy conversion rates.
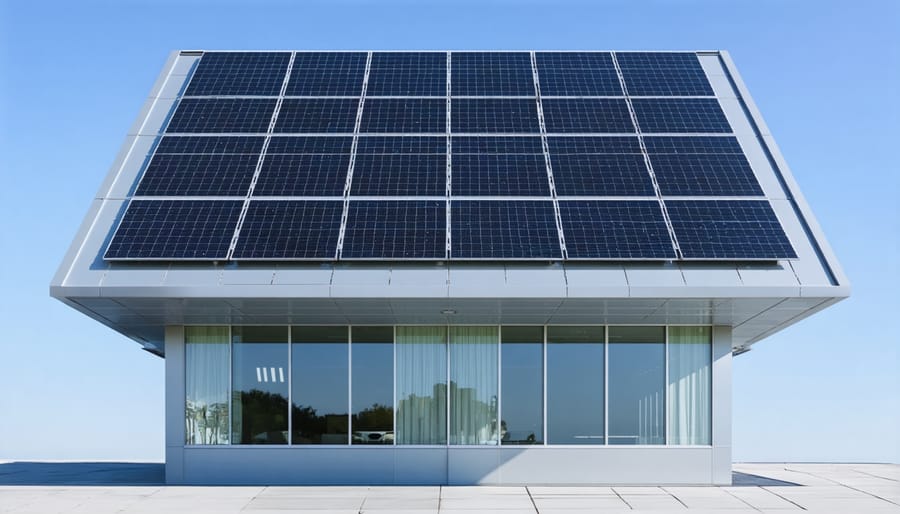
Advanced Energy Storage Solutions
The construction industry is witnessing a remarkable transformation in energy storage capabilities, with innovative energy solutions reshaping how buildings manage and utilize power. Advanced lithium-ion battery systems, specifically designed for commercial construction applications, now offer unprecedented storage capacity and operational efficiency. These next-generation systems can effectively store excess energy during off-peak hours and redistribute it during high-demand periods, significantly reducing operational costs and grid dependency.
Recent developments in solid-state battery technology promise even greater energy density and improved safety profiles, making them particularly suitable for urban construction projects. These systems integrate seamlessly with building management software, enabling real-time monitoring and optimization of energy consumption patterns.
Thermal energy storage solutions, utilizing phase-change materials (PCMs), are gaining traction in commercial construction. These systems can store and release thermal energy during phase transitions, providing a sustainable approach to temperature regulation and reducing HVAC system loads by up to 30%.
Flow battery technology represents another breakthrough, offering scalable storage solutions ideal for large-scale commercial developments. Unlike traditional batteries, flow batteries can be easily sized to meet specific project requirements and maintain consistent performance over extended lifecycles.
Integration of artificial intelligence and machine learning algorithms with these storage systems enables predictive energy management, automatically adjusting storage and distribution patterns based on historical usage data and real-time demand forecasting. This smart approach to energy management can result in energy cost reductions of 15-25% while ensuring optimal building performance.
Waste Reduction Technologies
3D Printing and Precision Construction
3D printing technology is revolutionizing construction practices by dramatically reducing material waste while enhancing precision and design flexibility. Advanced manufacturing systems, particularly large-scale concrete printers, can now produce complex structural elements with up to 40% less material compared to traditional construction methods.
Recent case studies demonstrate that 3D-printed structures require minimal post-processing and generate significantly less on-site waste. For instance, the Amsterdam Canal House project achieved a 95% reduction in construction waste through precise material deposition and digital design optimization.
The technology’s layer-by-layer approach enables contractors to use exactly the amount of material needed, eliminating excess cutting and formatting waste common in traditional construction. Advanced software algorithms optimize material distribution, ensuring structural integrity while minimizing volume requirements.
Beyond waste reduction, 3D printing facilitates the creation of complex geometries that would be impractical or impossible with conventional methods. This capability allows architects and engineers to design structures that are both materially efficient and environmentally responsive.
Quality control in 3D-printed construction is enhanced through continuous monitoring systems and automated processes, resulting in fewer errors and reduced material wastage due to corrections or replacements. The technology also supports the use of recycled materials and alternative sustainable composites, further reducing environmental impact.
As the technology matures, industry experts predict that 3D printing will become standard practice for specific construction applications, particularly in prefabrication and custom architectural elements, where precision and material efficiency are paramount.
Circular Economy Solutions
The construction industry is witnessing a paradigm shift toward circular economy solutions, revolutionizing how materials are sourced, used, and repurposed. Leading contractors are implementing sustainable construction practices that prioritize material recovery and waste reduction through innovative recycling technologies.
Advanced material passport systems are gaining traction, enabling precise tracking of building components throughout their lifecycle. These digital tools catalog material compositions, structural properties, and potential reuse applications, facilitating efficient recovery during renovation or demolition phases.
Innovative recycling technologies are transforming construction waste into valuable resources. Concrete crushing and separation systems now achieve 95% material recovery rates, while new chemical processes can break down composite materials into their original components. Companies are developing specialized equipment that can separate and process mixed construction waste on-site, reducing transportation costs and environmental impact.
Material banks and resource marketplaces are emerging as crucial infrastructure for the circular economy. These platforms connect suppliers of recovered materials with potential buyers, creating efficient secondary markets for construction materials. Some leading contractors have established dedicated material recovery facilities that process and certify reclaimed materials for immediate reuse in new projects.
The integration of Building Information Modeling (BIM) with material tracking systems is enabling contractors to plan for future material recovery during the design phase, maximizing the potential for circular material flows in construction projects.
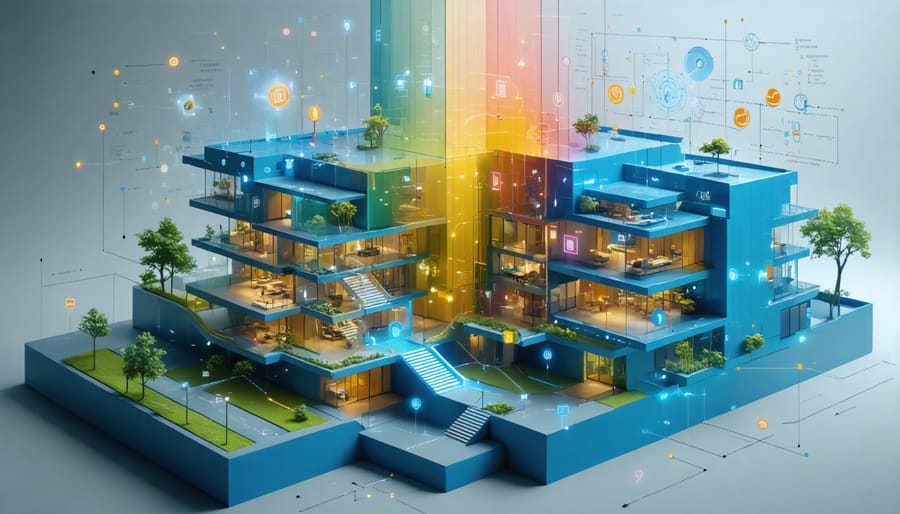
AI and IoT in Green Building Management
Predictive Maintenance Systems
Predictive maintenance systems powered by artificial intelligence are revolutionizing how construction companies manage their environmental impact and operational efficiency. These advanced systems utilize real-time data collection through IoT sensors to monitor equipment performance, energy consumption, and potential maintenance issues before they escalate into costly problems.
By analyzing patterns in equipment usage, energy consumption, and wear indicators, AI algorithms can predict maintenance needs with remarkable accuracy. This proactive approach reduces unexpected downtime, extends equipment lifespan, and optimizes energy usage across construction sites and completed buildings.
Case studies from leading construction firms demonstrate that predictive maintenance systems can reduce energy waste by up to 25% and maintenance costs by 30%. For example, a recent implementation at a commercial high-rise in Singapore resulted in a 20% reduction in HVAC-related energy consumption through early detection of system inefficiencies.
These systems also contribute to environmental sustainability by minimizing unnecessary part replacements and reducing the carbon footprint associated with emergency repairs. The integration of predictive maintenance with building management systems enables construction companies to maintain optimal performance while adhering to strict environmental standards and regulations.
Companies implementing these solutions report significant improvements in operational efficiency and environmental compliance, making predictive maintenance a crucial component of sustainable construction practices.
Smart Energy Management
Smart energy management systems powered by IoT technology are revolutionizing how construction projects monitor and optimize energy consumption. These sophisticated solutions integrate sensors, real-time data analytics, and automated controls to achieve unprecedented levels of energy efficiency.
Recent implementations demonstrate energy savings of 25-40% in commercial buildings through IoT-enabled systems. These platforms utilize machine learning algorithms to analyze occupancy patterns, environmental conditions, and equipment performance, automatically adjusting HVAC, lighting, and other building systems for optimal efficiency.
Key components include smart meters, occupancy sensors, and intelligent thermostats that communicate through a central management platform. The system continuously monitors energy usage patterns, identifying inefficiencies and suggesting improvements. For instance, a major office complex in Singapore reduced its energy consumption by 35% by implementing IoT-based controls that automatically adjusted cooling systems based on real-time occupancy and weather data.
Construction professionals can now access detailed energy analytics through mobile applications, enabling remote monitoring and immediate response to anomalies. Advanced features include predictive maintenance alerts, load balancing capabilities, and integration with renewable energy sources. This technological convergence creates buildings that not only consume less energy but actively participate in grid optimization and demand response programs.
The construction industry stands at a pivotal moment in its evolution, with environmental innovations reshaping how we conceive, build, and operate structures. These advancements are not merely trends but fundamental shifts that are transforming the sector’s environmental impact. From self-healing materials to AI-powered energy management systems, these innovations demonstrate the industry’s commitment to sustainability and efficiency.
The economic benefits of these innovations are becoming increasingly clear, with many companies reporting significant cost savings through reduced energy consumption, decreased waste, and lower maintenance requirements. Early adopters of these technologies are establishing competitive advantages while setting new industry standards for environmental responsibility.
Looking ahead, the integration of these innovations is expected to accelerate, driven by stricter environmental regulations, increasing client demand for sustainable buildings, and advancing technology. Industry experts predict that the next decade will see even more revolutionary developments, particularly in areas such as carbon-negative materials, advanced recycling technologies, and intelligent building systems that can adapt to environmental conditions in real-time.
The success of these environmental innovations ultimately depends on industry-wide adoption and continued investment in research and development. As construction professionals embrace these solutions, they not only contribute to environmental preservation but also position themselves at the forefront of a more sustainable and profitable future for the industry.