Manufacturing’s carbon footprint represents one of the most pressing challenges in modern industry, with the sector accounting for nearly 30% of global carbon emissions. Implementing effective zero carbon manufacturing strategies has become imperative for survival in an increasingly regulated and environmentally conscious market.
Leading manufacturers are already demonstrating that substantial emissions reductions of 40-60% are achievable through strategic interventions in production processes, energy systems, and supply chain operations. From automotive giants retrofitting facilities with renewable energy systems to chemical producers implementing breakthrough carbon capture technologies, the pathway to lower emissions is clear and commercially viable.
This article examines proven methodologies for reducing manufacturing carbon footprints, backed by real-world case studies and quantifiable results. We’ll explore practical solutions across energy optimization, process efficiency, material innovation, and sustainable supply chain management – providing actionable insights for manufacturing leaders committed to meeting ambitious carbon reduction targets while maintaining operational excellence and profitability.
Our analysis draws from extensive research and interviews with industry pioneers who have successfully transformed their operations, offering a blueprint for manufacturers at any stage of their sustainability journey. The focus remains on implementable solutions that deliver measurable impact within realistic timeframes and resource constraints.
Energy-Efficient Manufacturing Processes
Smart Energy Management Systems
Smart energy management systems represent a critical advancement in reducing manufacturing’s carbon footprint through intelligent monitoring and control. By implementing AI-driven energy optimization solutions, manufacturers can achieve significant reductions in energy consumption while maintaining production efficiency.
These systems utilize IoT sensors strategically placed throughout manufacturing facilities to collect real-time data on energy usage patterns, equipment performance, and environmental conditions. Advanced analytics platforms process this data to identify energy waste, predict maintenance needs, and automatically adjust system parameters for optimal performance.
Key components typically include:
– Real-time energy consumption monitoring
– Predictive maintenance algorithms
– Automated load balancing
– Dynamic peak demand management
– Machine learning-based optimization routines
Industry data shows that smart energy management systems can reduce energy consumption by 15-30% in manufacturing facilities. For example, a leading automotive manufacturer implemented IoT-based energy monitoring across their production lines, resulting in a 25% reduction in energy costs and associated carbon emissions within the first year.
The system’s ability to identify and respond to inefficiencies in real-time ensures continuous optimization of energy usage. This proactive approach not only reduces carbon emissions but also improves operational efficiency and reduces maintenance costs, making it a compelling investment for forward-thinking manufacturers.
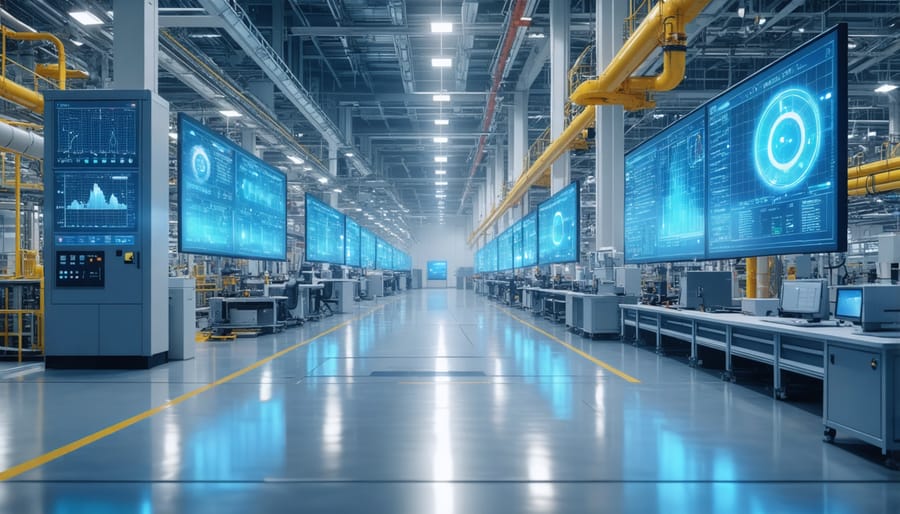
Waste Heat Recovery Solutions
Waste heat recovery represents a significant opportunity for manufacturers to reduce their carbon footprint while improving operational efficiency. Manufacturing processes typically generate substantial amounts of excess heat that often dissipates into the atmosphere. By implementing strategic heat recovery systems, facilities can capture and repurpose this energy for various applications.
Common waste heat recovery methods include the installation of heat exchangers, which transfer thermal energy from exhaust gases to incoming air or process fluids. These systems can pre-heat materials, generate steam for power production, or support facility heating requirements. Advanced technologies like Organic Rankine Cycle (ORC) systems can convert low-grade waste heat into electricity, providing an additional power source for manufacturing operations.
According to industry studies, implementing waste heat recovery solutions can reduce energy consumption by 20-30% in energy-intensive manufacturing processes. For instance, a leading cement manufacturer achieved annual energy savings of 15,000 MWh by installing a waste heat recovery system in their kiln operations, resulting in a significant reduction in carbon emissions.
Key considerations for implementing waste heat recovery systems include:
– Heat source temperature and quality
– Distance between heat source and potential use points
– Economic feasibility and return on investment
– System maintenance requirements
– Integration with existing processes
Regular monitoring and optimization of these systems ensure maximum efficiency and carbon reduction benefits, making waste heat recovery an essential component of sustainable manufacturing practices.
Sustainable Material Innovation
Low-Carbon Materials
The adoption of low-carbon materials represents a critical strategy in reducing manufacturing’s carbon footprint. Alternative cementitious materials, such as ground granulated blast furnace slag (GGBS) and fly ash, can reduce CO2 emissions by up to 80% compared to traditional Portland cement. These supplementary materials not only decrease environmental impact but often enhance concrete durability and performance.
Cross-laminated timber (CLT) has emerged as a sustainable alternative to steel and concrete, offering significant carbon storage benefits while maintaining structural integrity. Recent studies indicate that CLT construction can reduce carbon emissions by 40-50% compared to conventional building materials.
Recycled steel and aluminum are increasingly prevalent in manufacturing, requiring only about 25% of the energy needed to produce virgin materials. Advanced sorting technologies and quality control measures ensure these recycled materials meet industry standards while substantially reducing environmental impact.
Bio-based materials, including hemp-based products and mycelium composites, are gaining traction in manufacturing applications. These renewable resources offer excellent thermal and acoustic properties while sequestering carbon during growth. Industry leaders are also exploring carbon-negative materials, such as CO2-cured concrete, which actively absorbs carbon dioxide during the curing process.
When selecting low-carbon materials, manufacturers should consider full lifecycle assessments, including extraction, processing, transportation, and end-of-life disposal. Environmental Product Declarations (EPDs) provide standardized metrics for comparing material carbon footprints and making informed decisions.
Circular Economy Practices
Implementing circular economy practices in manufacturing represents a significant opportunity for carbon footprint reduction. By adopting circular economy materials and closed-loop production systems, manufacturers can significantly decrease waste while conserving resources.
Key strategies include implementing reverse logistics systems that enable the recovery and reprocessing of used materials. For instance, leading construction material manufacturers have established take-back programs for unused or demolition materials, achieving recycling rates of up to 95% in some facilities.
Waste reduction initiatives should focus on both production processes and packaging. Advanced manufacturing techniques, such as precision cutting and additive manufacturing, can minimize material waste during production. Companies implementing these strategies report material savings of 20-30% compared to traditional manufacturing methods.
Resource recovery systems, including water recycling and heat recovery, further enhance circular economy practices. Case studies from industry leaders demonstrate that implementing closed-loop water systems can reduce water consumption by up to 80%, while heat recovery systems can recapture up to 60% of process heat for reuse.
To maximize effectiveness, manufacturers should establish monitoring systems to track material flows and identify opportunities for waste reduction. This data-driven approach enables continuous improvement in resource efficiency while supporting sustainability reporting requirements.
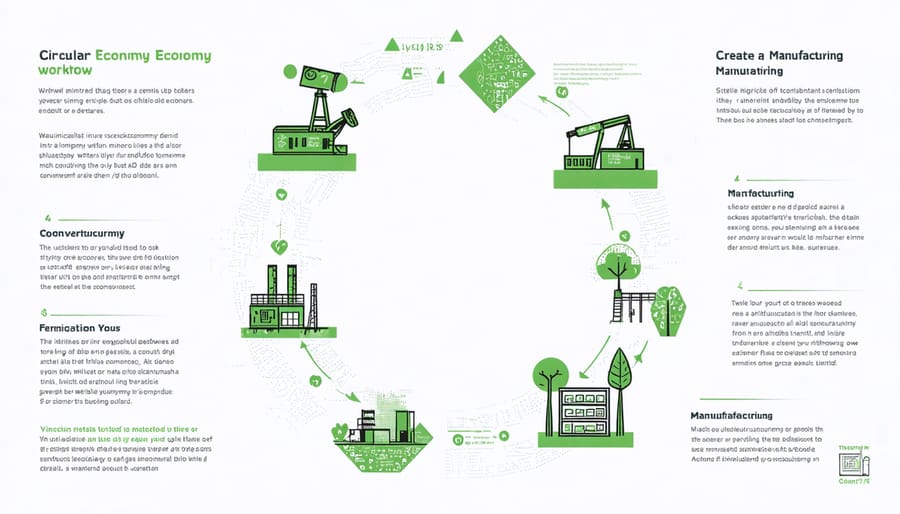
Supply Chain Optimization
Local Sourcing Benefits
Local sourcing of materials and components plays a crucial role in reducing manufacturing’s carbon footprint by significantly decreasing transportation-related emissions. Studies show that sourcing materials within a 100-mile radius can reduce transportation emissions by up to 30% compared to international shipping.
Beyond transportation benefits, local sourcing strengthens regional supply chains and enables better quality control. Manufacturers can conduct regular supplier audits, ensuring materials meet sustainability standards while maintaining closer relationships with suppliers to implement joint carbon reduction initiatives.
According to industry research, local sourcing can reduce overall product carbon footprint by 15-25% when considering both direct and indirect emissions. This includes reduced inventory storage requirements, decreased packaging needs, and more efficient logistics planning.
Companies implementing local sourcing strategies report additional benefits such as improved supply chain resilience, faster response times to market demands, and reduced risk of supply chain disruptions. For instance, a leading construction materials manufacturer reduced its annual carbon emissions by 2,000 metric tons by transitioning 60% of its raw material sourcing to local suppliers.
To maximize these benefits, manufacturers should develop comprehensive supplier evaluation criteria that include carbon footprint metrics, establish local supplier development programs, and invest in regional manufacturing capabilities.
Transportation Efficiency
Transportation efficiency plays a crucial role in reducing manufacturing’s carbon footprint, with logistics accounting for up to 25% of a facility’s total emissions. Implementing strategic route optimization through advanced GPS and AI-powered logistics software can reduce fuel consumption by 15-20%. Companies should prioritize consolidating shipments and adopting just-in-time delivery practices to minimize unnecessary trips.
Electric and hybrid vehicles for short-haul transportation have shown promising results, with early adopters reporting emission reductions of up to 60% in their local distribution networks. For long-haul requirements, considering intermodal transportation options, such as rail-truck combinations, can decrease carbon emissions by 30% compared to traditional trucking alone.
Warehouse location optimization is equally important. Establishing distribution centers closer to major transportation hubs and end-users can significantly reduce travel distances. Leading manufacturers have implemented load optimization techniques, ensuring trucks operate at maximum capacity while maintaining proper weight distribution.
Regular fleet maintenance, driver training in fuel-efficient practices, and the use of aerodynamic modifications on vehicles can further reduce fuel consumption by 5-10%. Companies should also consider partnering with carriers who have demonstrated commitment to sustainability through certified green fleet programs and alternative fuel adoption.
Case Study: Carbon-Neutral Manufacturing Facility
The Schneider Electric manufacturing facility in Lexington, Kentucky, stands as a premier example of successful carbon footprint reduction in the manufacturing sector. Completed in 2021, this 185,000-square-foot facility achieved carbon neutrality through a comprehensive approach combining advanced technology, renewable energy integration, and innovative process optimization.
The facility implemented several key strategies to achieve its carbon-neutral status. First, they installed a 2.4MW solar array on the facility’s roof, which generates approximately 60% of their annual energy needs. The remaining power requirements are met through power purchase agreements (PPAs) with local wind farms, ensuring 100% renewable energy usage.
Energy efficiency improvements played a crucial role in their success. The facility upgraded to smart LED lighting systems with occupancy sensors, reducing lighting energy consumption by 75%. Advanced building automation systems optimize HVAC operations, resulting in a 30% reduction in heating and cooling energy usage. The installation of energy-efficient manufacturing equipment and real-time energy monitoring systems further reduced their overall energy consumption by 40% compared to their previous facility.
Waste reduction initiatives were equally important in their carbon-neutral journey. The facility implemented a closed-loop manufacturing process that recycles 98% of industrial waste. Water consumption was reduced by 35% through the installation of rainwater harvesting systems and water-efficient processing equipment.
The results have been remarkable: annual carbon emissions were reduced by 5,000 metric tons, equivalent to removing 1,000 cars from the road. The facility’s operational costs decreased by 45%, with an ROI achieved within four years. This success has inspired Schneider Electric to implement similar strategies across their global manufacturing network.
The project demonstrates that achieving carbon neutrality in manufacturing is not only environmentally responsible but also economically viable. The facility serves as a blueprint for other manufacturers looking to reduce their carbon footprint while maintaining operational efficiency and profitability.
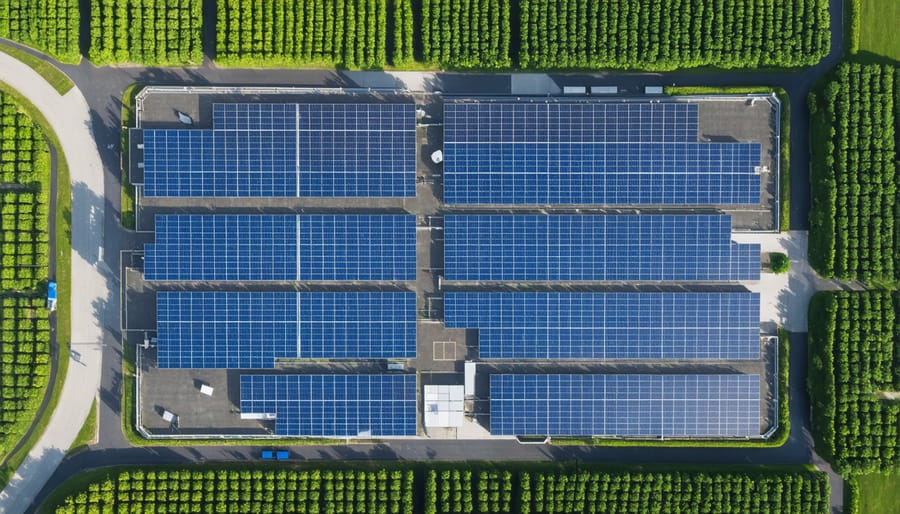
Technology Integration
Digital Twin Technology
Digital twin technology represents a significant breakthrough in reducing manufacturing carbon footprint through virtual simulation and real-time optimization. By creating detailed digital replicas of manufacturing processes, companies can analyze, test, and optimize operations without consuming additional resources or generating unnecessary emissions.
These virtual models, integrated with IoT-enabled monitoring systems, provide real-time insights into energy consumption patterns, material usage, and production efficiency. Manufacturers can simulate various scenarios to identify optimal operating conditions that minimize carbon emissions while maintaining productivity.
Case studies have shown that implementing digital twins can reduce energy consumption by 10-30% through precise process optimization. For instance, a leading cement manufacturer achieved a 15% reduction in carbon emissions by using digital twin technology to optimize kiln operations and thermal efficiency.
Key benefits include:
– Predictive maintenance scheduling to prevent energy-wasteful equipment failures
– Real-time adjustment of production parameters for optimal efficiency
– Virtual testing of sustainability initiatives before physical implementation
– Continuous monitoring and optimization of resource consumption
Digital twins also enable manufacturers to identify and eliminate hidden inefficiencies that contribute to unnecessary emissions, such as excess heat generation, compressed air leaks, or suboptimal material flow patterns. This technology proves particularly valuable in complex manufacturing environments where multiple variables affect overall carbon output.
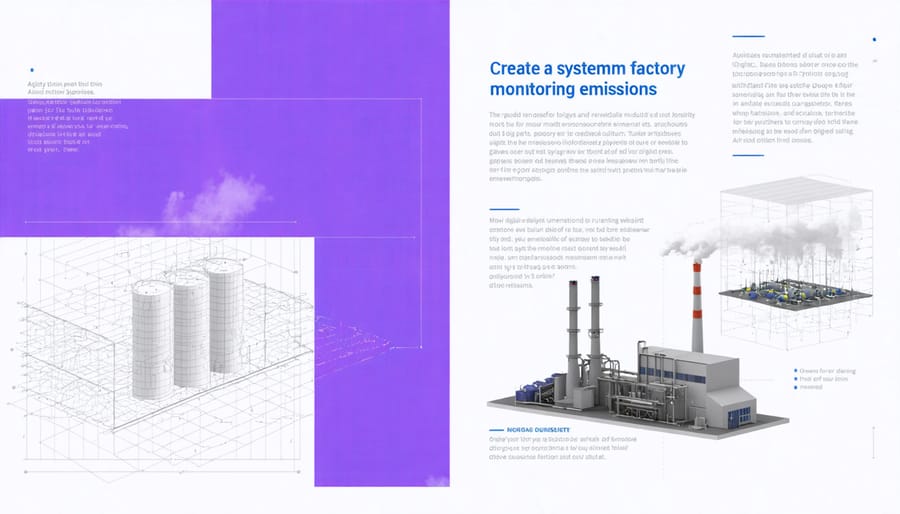
Automated Environmental Monitoring
Modern manufacturing facilities are increasingly adopting automated environmental monitoring systems to track and reduce their carbon footprint in real-time. These sophisticated systems integrate IoT sensors, data analytics, and artificial intelligence to provide continuous monitoring of emissions, energy consumption, and other crucial sustainability metrics.
Key components typically include networked emission sensors installed at critical points throughout the facility, smart energy meters, and centralized monitoring platforms. These systems can detect anomalies instantly, allowing facility managers to respond promptly to any deviations from optimal performance levels. For example, if a production line shows unexpected increases in energy consumption or emissions, the system alerts operators immediately, enabling swift corrective action.
Advanced monitoring solutions also facilitate automated reporting and compliance documentation, streamlining regulatory requirements while providing valuable data for continuous improvement initiatives. Many systems now incorporate predictive analytics capabilities, helping manufacturers anticipate potential issues before they impact environmental performance.
Implementation costs are often offset by improved operational efficiency and reduced environmental compliance risks. Case studies from leading manufacturers show that automated monitoring systems typically achieve 15-20% reductions in carbon emissions within the first year of deployment, primarily through early detection and prevention of inefficiencies in production processes.
The manufacturing industry stands at a crucial turning point in its journey toward sustainability. By implementing the strategies discussed throughout this article, manufacturers can significantly reduce their carbon footprint while maintaining operational efficiency and competitiveness. The combination of energy-efficient technologies, renewable energy adoption, waste reduction protocols, and sustainable supply chain practices creates a comprehensive approach to emissions reduction.
Looking ahead, the industry’s commitment to carbon reduction will likely strengthen as technological innovations continue to emerge. Smart manufacturing systems, artificial intelligence, and advanced materials processing techniques promise even greater opportunities for sustainability. The integration of circular economy principles and the increasing adoption of carbon capture technologies will further accelerate progress toward carbon neutrality.
Success in reducing industrial carbon emissions requires a coordinated effort across all organizational levels, from shop floor operations to executive decision-making. Companies that embrace these changes now will not only contribute to global climate goals but also position themselves advantageously in an increasingly environmentally conscious market.
As regulations tighten and stakeholder expectations evolve, the imperative for manufacturers to reduce their carbon footprint will only grow stronger. The tools, technologies, and strategies outlined here provide a robust foundation for immediate action and long-term planning. By prioritizing sustainability initiatives and maintaining a commitment to continuous improvement, manufacturers can lead the way in building a more sustainable industrial future.