Harnessing the power of cutting-edge industrial energy systems is crucial for construction professionals striving to optimize efficiency, reduce costs, and meet sustainability goals. From advanced cogeneration technologies to intelligent energy management platforms, innovative solutions are transforming how industrial facilities generate, distribute, and consume energy. By leveraging real-time data analytics, predictive maintenance, and AI-driven optimization, these systems enable unprecedented levels of control, flexibility, and responsiveness. Case studies demonstrate the tangible benefits, with leading companies achieving significant reductions in energy consumption, emissions, and operational expenses. As the industry evolves, staying at the forefront of these advancements is essential for construction professionals seeking to deliver future-proof, high-performance industrial projects that excel in an increasingly competitive and environmentally conscious landscape.
Cogeneration & CHP
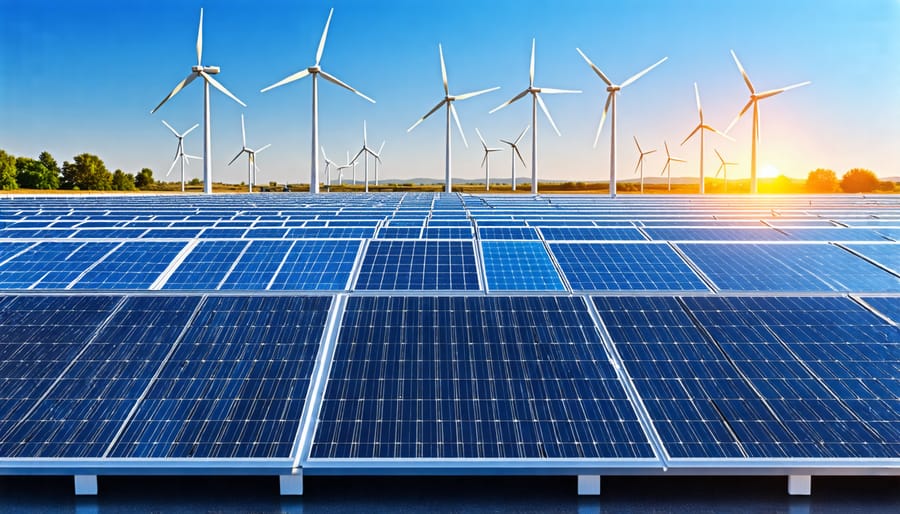
How CHP Systems Work
Combined Heat and Power (CHP) systems, also known as cogeneration, simultaneously generate electricity and useful thermal energy from a single fuel source. By capturing and utilizing heat that would otherwise be wasted in conventional power generation, CHP systems can achieve total system efficiencies of up to 80% or higher. This is a significant improvement over the average efficiency of about 45% for traditional electricity generation. In a typical CHP system, a prime mover such as a gas turbine or reciprocating engine burns fuel to generate electricity. The waste heat from this process is then recovered and used for various applications, including space heating, cooling, and industrial processes. By integrating power and heat generation, CHP systems reduce energy costs, improve energy security, and lower greenhouse gas emissions. These benefits make CHP an attractive option for many industrial facilities seeking to optimize their energy systems.
Real-World CHP Success Stories
Several manufacturers have achieved impressive results by implementing combined heat and power (CHP) systems in their facilities. For example, a leading food processing company installed a 4.4 MW CHP system, reducing energy costs by over $1 million annually while increasing reliability and reducing emissions. In another case, a large chemical plant adopted a 25 MW CHP system, achieving an overall efficiency of 85% and cutting carbon emissions by 200,000 tons per year. Additionally, a major automotive manufacturer implemented a 14 MW CHP system, saving $5 million in annual energy costs and providing enhanced power resilience for critical operations. These real-world success stories demonstrate the significant benefits that industrial facilities can realize by embracing CHP technology, including improved efficiency, reduced costs, lower emissions, and increased energy security.
Microgrids
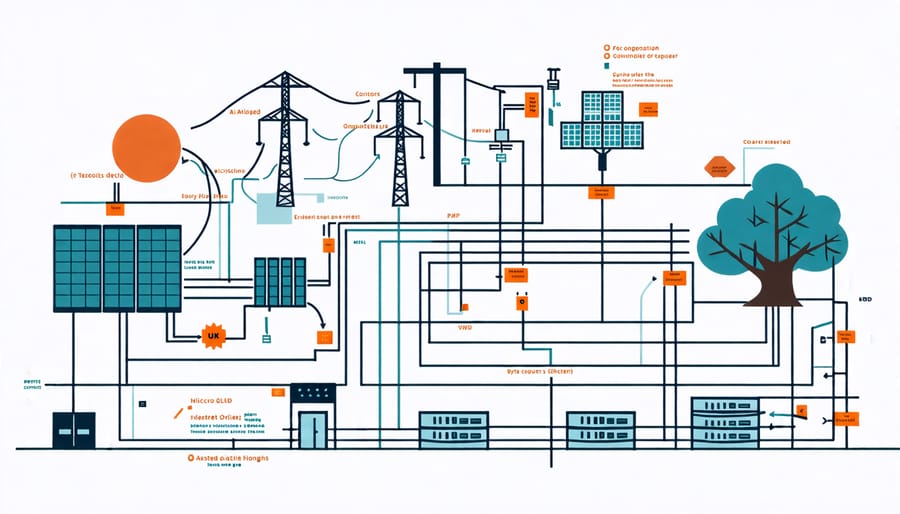
Microgrid Controllers: The Brains of the Operation
Microgrid controllers are the central nervous system of industrial energy systems, orchestrating the complex interactions between distributed energy resources, loads, and the utility grid. Recent advancements in controller technology have unlocked new capabilities, enabling more intelligent, adaptive, and resilient microgrids. Cutting-edge controllers leverage artificial intelligence, machine learning, and advanced optimization algorithms to continuously monitor and adjust microgrid operations in real-time. They can anticipate demand, forecast renewable energy production, and make split-second decisions to maintain stability, efficiency, and reliability. These smart controllers also facilitate seamless transitions between grid-connected and islanded modes, ensuring uninterrupted power supply even during grid outages. With enhanced cybersecurity features and remote monitoring capabilities, modern microgrid controllers provide a secure, flexible, and future-proof foundation for industrial energy management. As the brains behind the operation, these advanced controllers are driving the adoption of microgrids and transforming the way industries generate, distribute, and consume energy.
Solar PV & Battery Storage
Evaluating If Solar Is Right For Your Facility
When evaluating if solar is right for your industrial facility, several key factors should be considered. First, assess your facility’s energy consumption patterns and electricity costs to determine the potential financial benefits of going solar. Next, evaluate your facility’s physical characteristics, such as available roof space, roof type, and shading from nearby structures, to ensure suitability for solar panel installation. It’s also important to consider your location’s climate and average sunlight exposure, as this will impact the system’s energy production.
Once you’ve determined that your facility is a good candidate for solar, the next step is to select the optimal system size. This involves calculating your facility’s energy needs and matching them with the appropriate solar panel array size. Factors to consider include your current and projected energy consumption, available space for panels, and budget. Working with experienced solar professionals can help you determine the most cost-effective and efficient system size for your specific needs.
By carefully evaluating your facility’s suitability for solar and selecting the right system size, you can maximize the benefits of this clean energy technology while minimizing upfront costs and potential challenges. Investing the time to make informed decisions at this stage will help ensure a successful solar installation that delivers long-term energy savings and environmental benefits for your industrial facility.
Waste Heat to Power
Waste heat to power (WHP) systems are an innovative technology that capture waste heat from industrial processes and convert it into usable electricity. By harnessing this otherwise wasted thermal energy, WHP systems improve energy efficiency, reduce greenhouse gas emissions, and provide cost savings for industrial facilities.
The primary technologies used in WHP systems include organic Rankine cycle (ORC) engines, Kalina cycle systems, and thermoelectric generators. ORC engines utilize an organic fluid with a lower boiling point than water to generate power from low-temperature heat sources. Kalina cycle systems employ a mixture of ammonia and water as the working fluid, allowing for efficient power generation across a wide range of temperatures. Thermoelectric generators use solid-state devices to convert temperature differences directly into electrical energy.
The benefits of implementing WHP systems in industrial settings are substantial. By generating electricity from waste heat, facilities can reduce their reliance on grid power and lower energy costs. WHP systems also contribute to environmental sustainability by reducing the carbon footprint associated with electricity generation. Additionally, WHP can improve the overall efficiency of industrial processes and help facilities meet increasingly stringent energy regulations.
WHP systems find applications across various industries, including cement production, steel manufacturing, oil and gas refineries, and chemical processing plants. For example, a cement plant can capture waste heat from its kiln exhaust gases to generate electricity, offsetting a portion of its energy consumption. Similarly, oil refineries can harness waste heat from process streams to power on-site equipment, reducing the need for external energy sources.
As the demand for energy efficiency and sustainability grows, waste heat to power systems are becoming an increasingly attractive option for industrial facilities looking to optimize their energy use and minimize environmental impact.
AI-Optimized Energy Management
The advent of artificial intelligence (AI) and machine learning technologies is revolutionizing industrial energy management, enabling unprecedented levels of efficiency and optimization. AI-powered energy management systems leverage advanced algorithms to continuously analyze vast amounts of data from sensors, meters, and other connected devices. By identifying patterns, predicting demand, and making real-time adjustments, these intelligent systems can significantly reduce energy consumption and costs.
One of the key benefits of AI in energy management is its ability to optimize efficiency across multiple systems and processes. Machine learning algorithms can analyze historical data, weather patterns, occupancy levels, and other variables to determine the most energy-efficient settings for HVAC, lighting, and other building systems. This dynamic optimization ensures that energy is used only when and where it’s needed, minimizing waste and maximizing savings.
Moreover, AI-based energy management systems can predict maintenance needs and prevent equipment failures. By continuously monitoring the performance of critical assets, such as boilers, chillers, and pumps, these systems can detect anomalies and potential issues before they lead to costly downtime. Predictive maintenance not only extends the lifespan of equipment but also helps avoid unexpected disruptions to operations.
Another significant advantage of AI in industrial energy management is its ability to seamlessly integrate disparate systems and data sources. By breaking down silos and facilitating communication between various components, AI enables a holistic approach to energy optimization. This integration allows for more accurate forecasting, better decision-making, and improved overall performance.
As the construction industry embraces the power of AI and machine learning, the potential for energy savings and operational improvements is immense. By implementing AI-optimized energy management systems, industrial facilities can not only reduce their environmental impact but also gain a competitive edge through increased efficiency and reduced operating costs.
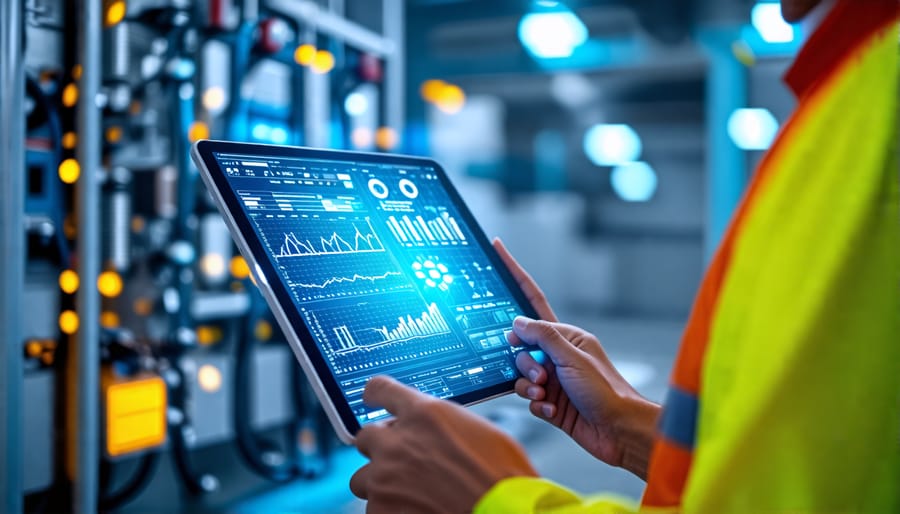
Conclusion
In conclusion, these five innovative industrial energy systems offer significant benefits for manufacturing facilities looking to improve efficiency, reduce costs, and enhance sustainability. From advanced cogeneration and waste heat recovery to cutting-edge energy storage solutions, these technologies harness untapped potential to energy efficiency and optimize resource utilization. By integrating renewable energy sources, implementing smart grid technologies, and leveraging AI-driven optimization, manufacturers can not only reduce their environmental footprint but also gain a competitive edge in an increasingly eco-conscious market. The adoption of these groundbreaking systems has the power to revolutionize manufacturing, setting new standards for performance, reliability, and sustainability. As the industry continues to evolve, it is crucial for decision-makers to explore and invest in these transformative solutions. By staying at the forefront of technological advancements, manufacturers can position themselves for long-term success while contributing to a greener, more sustainable future. We encourage readers to delve deeper into these cutting-edge industrial energy systems and consider how they can be implemented in their own facilities to unlock the full potential of advanced energy management.