Ensure strict compliance with OSHA standards, the baseline for construction safety in the U.S. Implement a comprehensive safety training program for all workers, covering site-specific hazards, PPE usage, and emergency protocols. Foster a strong safety culture through management commitment, worker engagement, and regular safety audits. Stay current on evolving industry best practices and technologies to mitigate risks on your jobsites.
Fall Protection Standards
Guardrail Systems
Guardrail systems are a critical component of fall protection in construction. OSHA standards require guardrails to be at least 42 inches high, with a midrail and toe board. Top rails must withstand a 200-pound force, while midrails must resist 150 pounds. Guardrails are required on any platform or walkway 4 feet or more above a lower level. They should be placed on all open sides and ends of platforms, as well as around holes and skylights. Proper installation is key, with posts no more than 8 feet apart and rails secured to withstand the required forces. Regular inspection and maintenance ensure ongoing effectiveness. Guardrail systems, when implemented correctly, provide a reliable and visible barrier to prevent falls and protect workers at height. Consult OSHA regulations and industry best practices for detailed specifications on materials, dimensions, and testing requirements to ensure compliance and maximize safety on your construction site.
Personal Fall Arrest Systems
Personal fall arrest systems (PFAS) are essential for ensuring worker safety at heights. The most common types of PFAS include full-body harnesses, lanyards, and anchors. Full-body harnesses distribute fall forces across the shoulders, thighs, and pelvis, providing superior protection compared to body belts. Lanyards connect the harness to an anchor point and are designed to limit free fall distance and arrest forces. Anchors must be capable of supporting at least 5,000 pounds per attached worker.
To wear a PFAS properly, adjust the harness straps snugly across the chest, shoulders, and legs. The D-ring should be positioned between the shoulder blades. Lanyards should be attached to the D-ring and an appropriate anchor point. Workers must ensure there is sufficient clearance below to avoid hitting lower levels in the event of a fall.
Regular inspection of PFAS components is critical. Before each use, check harnesses for frayed edges, broken stitches, and damaged buckles or D-rings. Lanyards should be free of cuts, burns, and excessive wear. Any equipment showing signs of deterioration must be removed from service immediately. Proper maintenance, including cleaning and storage away from heat, moisture, and direct sunlight, can extend the life of PFAS components. By selecting appropriate equipment, wearing it correctly, and conducting thorough inspections, construction professionals can significantly reduce the risk of fall-related injuries and fatalities on the job site.
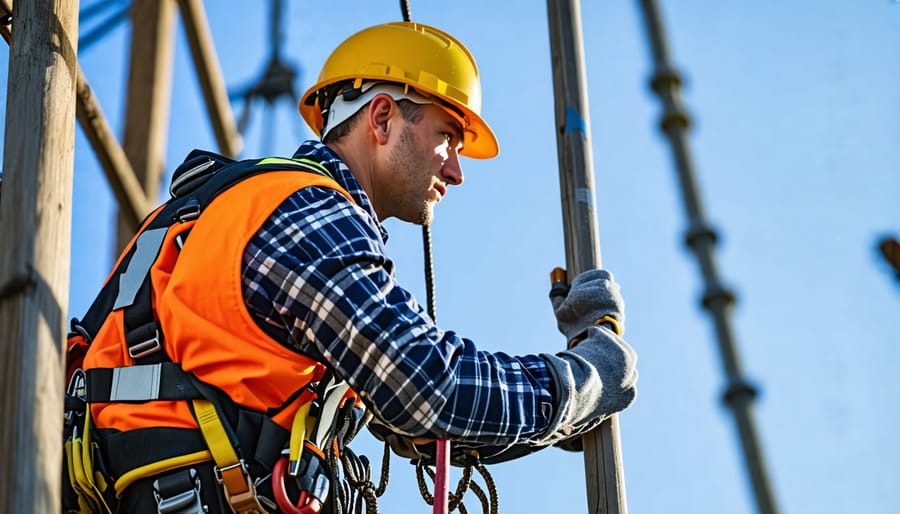
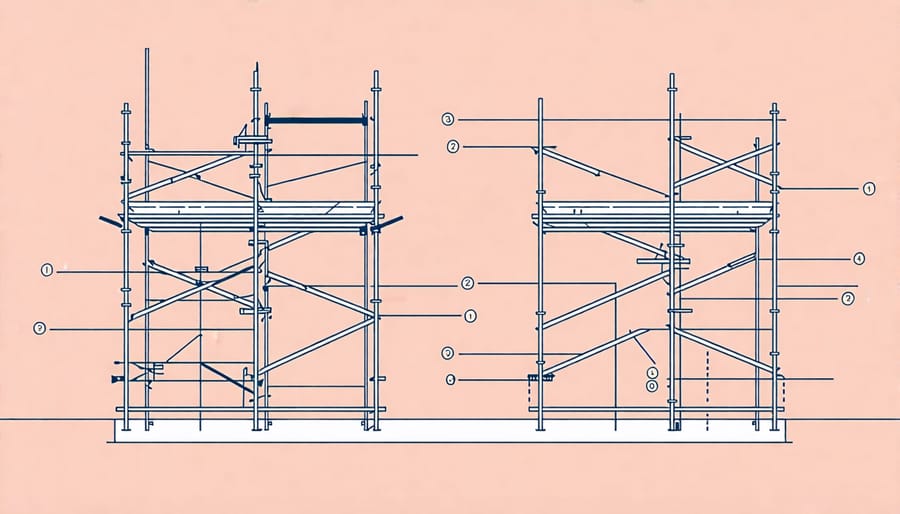
Scaffolding Safety
OSHA requires scaffolding to be designed and constructed to support its own weight and at least four times the maximum intended load. It must be erected on solid footing and be equipped with guardrails, midrails, and toeboards. Scaffolding must also undergo regular inspections by a competent person to ensure its structural integrity and identify any potential hazards.
Fall protection is a critical component of scaffolding safety. Workers on scaffolding more than 10 feet above a lower level must be protected from falling by guardrails or a personal fall arrest system. Crossbraces cannot be used as a substitute for guardrails. Scaffolding access must be provided by ladders, stairwells, ramps, or walkways, and must be free of slipping hazards.
Weight capacity is another key consideration. Each scaffold and scaffold component must support, without failure, its own weight and at least four times the maximum intended load applied or transmitted to it. Suspension ropes must be capable of supporting at least six times the maximum intended load. It’s crucial to adhere to the manufacturer’s weight capacity guidelines and not overload the scaffolding.
Proper training is essential for anyone involved in the erection, disassembly, moving, operating, repairing, maintaining, or inspecting of scaffolding. They must be trained by a competent person to recognize hazards associated with the work and understand the procedures to control or minimize those hazards. Refresher training may be needed to maintain proficiency and ensure a safe working environment.
Regular maintenance and prompt repairs are also vital. Any damaged or weakened scaffold components must be immediately repaired or replaced. Suspension ropes should be protected from heat-producing processes or corrosive substances. By adhering to OSHA’s scaffolding safety standards, the construction industry can significantly reduce the risk of accidents and injuries related to scaffolding use.
Excavation and Trenching Safety
Excavation and trenching work poses significant safety risks, necessitating strict adherence to OSHA standards. Soil classification is a critical first step, with soils categorized as stable rock, Type A, Type B, or Type C based on their composition and stability. Type C soils, including granular and saturated soils, require the most robust protective systems.
Sloping, shoring, and shielding are the primary methods for protecting workers in excavations. Sloping involves cutting back the trench wall at an angle inclined away from the excavation. The angle of the slope depends on soil type, with steeper slopes allowed in more stable soils. Shoring systems, such as hydraulic and pneumatic shores, provide temporary support to prevent cave-ins. Shielding, including trench boxes and sliding trench shields, protects workers by physically withstanding the forces of a cave-in.
Regular inspections by a competent person are essential for identifying and mitigating hazards. Inspections should occur daily before work begins, as well as after any event that could alter soil conditions, such as heavy rain or vibrations from nearby equipment. The competent person must have the authority to immediately eliminate hazards or stop work until issues are resolved.
Safe access and egress are crucial for excavations 4 feet deep or more. Ladders, stairways, or ramps must be located within 25 feet of all workers. For trenches 20 feet deep or greater, multiple means of access/egress are required.
Other key safety measures include:
– Keeping excavated materials and equipment at least 2 feet from the edge of excavations
– Providing warning systems for mobile equipment operating near excavation edges
– Conducting atmospheric testing in excavations deeper than 4 feet with potential hazardous atmospheres
– Developing site-specific emergency response plans
By prioritizing soil analysis, using appropriate protective systems, conducting thorough inspections, and ensuring safe access/egress, construction professionals can significantly reduce the risks associated with excavation and trenching operations.
Electrical Safety Standards
Electrical safety is paramount in the construction industry, with clear standards in place to prevent shocks, fires, and other hazards. Proper grounding of electrical systems and equipment is essential, ensuring that any fault current has a safe path to the ground. Ground Fault Circuit Interrupters (GFCIs) are required in wet or damp locations, protecting workers from electrocution by quickly cutting off power when an imbalance is detected.
Maintaining adequate clearance from overhead power lines is crucial, with specific distances mandated based on voltage. Lockout/tagout procedures must be followed when servicing or maintaining electrical equipment, ensuring that energy sources are completely isolated and preventing accidental startup.
Personal Protective Equipment (PPE) is a vital component of electrical safety. Workers must wear appropriate insulating gloves, face shields, and flame-resistant clothing when working on or near energized parts. Regular safety training is essential to ensure that all personnel understand and adhere to safe work practices.
Implementing an effective jobsite safety program that incorporates electrical safety standards, along with ongoing safety training, is key to protecting workers and maintaining a safe work environment. By prioritizing electrical safety and following established standards, the construction industry can significantly reduce the risk of accidents and injuries related to electrical hazards.
Implementing a Safety Program
Safety Training
Safety training is a cornerstone of maintaining a secure and compliant work environment in the construction industry. OSHA mandates that employers provide comprehensive safety training to all workers, covering topics such as fall protection, electrical safety, hazard communication, and proper use of personal protective equipment (PPE). Training should be conducted by qualified instructors and tailored to the specific hazards present on each job site.
Frequency of training varies based on the nature of the work and the associated risks. OSHA requires that workers receive initial training upon hiring and whenever their job duties or work environment changes significantly. Refresher training should be provided at regular intervals, typically annually, to reinforce key concepts and update workers on any new safety protocols or regulations.
In addition to general safety training, specialized instruction may be necessary for certain high-risk activities such as confined space entry, excavation, or working with hazardous materials. Employers should conduct thorough job hazard analyses to identify these situations and develop appropriate training programs. Documenting all safety training is crucial for maintaining compliance records and ensuring that workers have the knowledge and skills needed to perform their duties safely on construction sites.
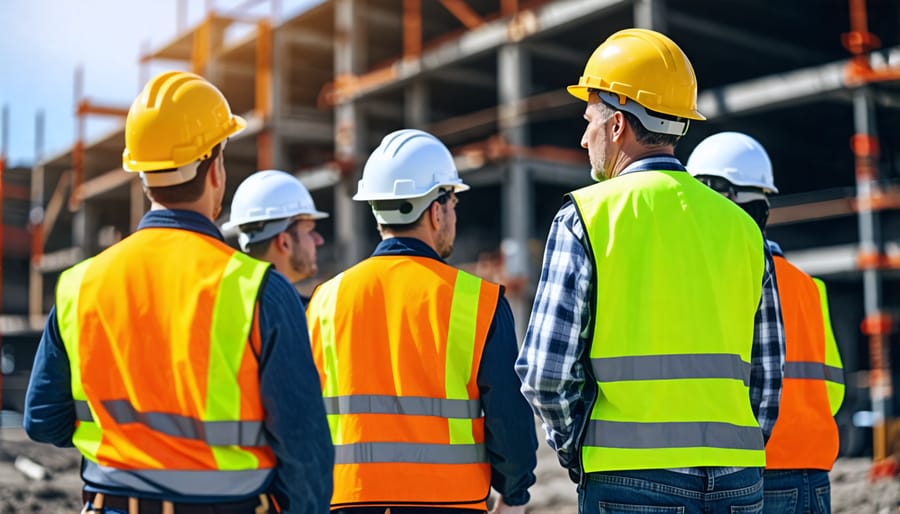
Incident Reporting & Investigation
Prompt incident reporting is crucial for maintaining a safe construction site. All accidents, near misses, and hazardous conditions should be reported immediately to supervisors or designated safety personnel. Establish clear reporting procedures and train employees on the proper channels for communicating safety concerns. Encourage a culture of transparency and emphasize that reporting incidents is essential for preventing future occurrences.
When an incident occurs, a thorough investigation must be conducted to identify the root causes and implement corrective actions. The investigation process should involve gathering evidence, interviewing witnesses, and analyzing the sequence of events leading up to the incident. It’s essential to approach investigations with an objective mindset, focusing on facts rather than assigning blame.
Investigations should result in actionable recommendations to prevent similar incidents from happening again. This may involve modifying work procedures, providing additional training, or implementing new safety measures. Document the investigation findings and communicate the lessons learned to all relevant parties, including employees, managers, and stakeholders.
Regular review and analysis of incident reports can reveal patterns or trends that may not be apparent from individual cases. Use this data to identify areas for improvement in your safety management system and prioritize corrective actions accordingly. By treating each incident as a learning opportunity, the construction industry can continuously enhance its safety standards and protect the well-being of its workforce.
Conclusion
Safety standards are the foundation of a thriving and responsible construction industry. By understanding and consistently applying these standards, construction professionals can protect workers, ensure quality projects, and contribute to the overall well-being of the industry. It is crucial for everyone involved in construction projects, from architects and engineers to project managers and on-site workers, to prioritize safety at every stage. Staying informed about the latest safety regulations, best practices, and technological advancements is an ongoing responsibility. For further information and resources on construction industry safety standards, consult organizations such as the Occupational Safety and Health Administration (OSHA), the American National Standards Institute (ANSI), and the Construction Industry Institute (CII). By working together and upholding the highest safety standards, the construction industry can continue to build a safer, more prosperous future for all stakeholders.