Building material selection shapes the very foundation of construction excellence, determining not only structural integrity but also long-term project success. In today’s rapidly evolving construction landscape, quality materials represent the critical difference between structures that stand the test of time and those that require constant maintenance and premature replacement. Recent industry data reveals that investing in premium building materials reduces lifecycle costs by 23-35% while extending structural longevity by up to four decades.
The convergence of innovative manufacturing processes, sustainable practices, and advanced material science has revolutionized the building materials market. From high-performance concrete formulations to engineered wood products that rival steel in strength, modern construction professionals now have access to an unprecedented array of materials that combine durability with environmental responsibility. These advancements enable architects and builders to meet increasingly stringent building codes while delivering projects that exceed client expectations for performance, sustainability, and cost-effectiveness.
This comprehensive examination explores the latest developments in quality building materials, offering practical insights into selection criteria, performance metrics, and implementation strategies that drive successful construction outcomes. Whether managing large-scale commercial projects or specialized residential developments, understanding the nuanced relationship between material quality and project success remains fundamental to construction excellence.
Defining Quality in Modern Construction Materials
Performance Indicators
Performance indicators serve as crucial benchmarks for evaluating building material quality, enabling construction professionals to make informed decisions based on quantifiable data. Compressive strength, measured in megapascals (MPa) or pounds per square inch (psi), remains a fundamental metric for structural materials like concrete and steel. Tensile strength and flexural strength provide additional insights into material behavior under various load conditions.
Durability indicators include water absorption rate, freeze-thaw resistance, and chemical resistance properties. The moisture vapor transmission rate (MVTR) helps predict material performance in different environmental conditions, while thermal performance metrics such as R-value and U-value determine insulation effectiveness.
Fire resistance ratings, measured in hours, indicate a material’s ability to maintain structural integrity during fire exposure. Impact resistance, typically measured through standardized drop tests or impact energy absorption, helps assess material durability in high-traffic areas. Sound transmission class (STC) ratings evaluate acoustic properties, while volatile organic compound (VOC) emissions measurements ensure compliance with environmental and health standards.
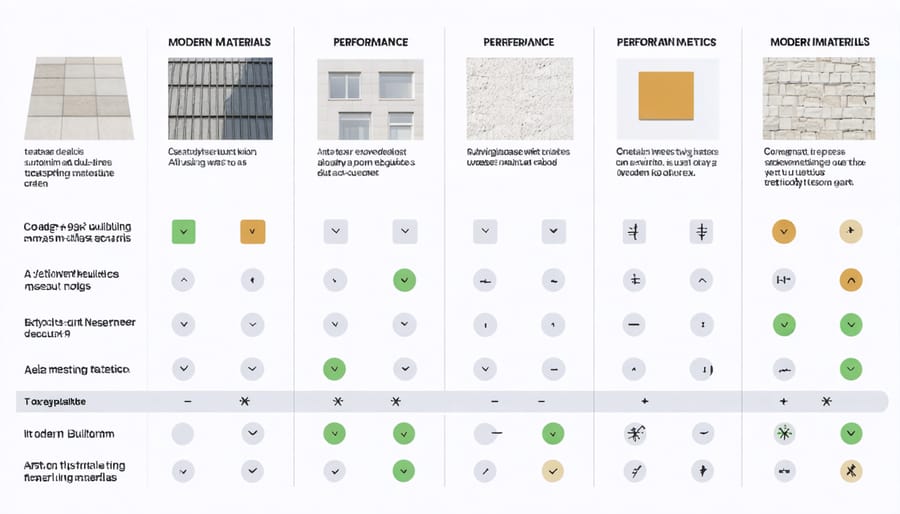
Certification Standards
Industry-standard certifications play a crucial role in validating the quality and performance of building materials. Key certification bodies like ASTM International, ISO, and ICC-ES establish rigorous testing protocols and performance criteria that materials must meet. These standards ensure consistency, durability, and safety across construction projects.
ASTM standards are particularly significant in North America, covering everything from concrete strength requirements to thermal insulation performance. Materials undergo extensive laboratory testing for properties such as compressive strength, fire resistance, and environmental impact. The ICC-ES evaluation process provides additional verification through independent assessment of building products and materials.
For sustainable construction, certifications like LEED, BREEAM, and Cradle to Cradle assess environmental impact and material health. These programs evaluate factors including recycled content, VOC emissions, and lifecycle assessment.
Quality control protocols typically involve both initial type testing and ongoing production monitoring. Manufacturers must maintain detailed documentation of testing procedures, results, and quality control measures. Third-party verification ensures compliance with established standards, providing architects and contractors with confidence in material performance and reliability.
Regular updates to certification standards reflect evolving building codes and technological advancements, ensuring continued relevance and effectiveness.
Revolutionary Materials Reshaping Construction
Advanced Composites
Modern construction has been revolutionized by the emergence of advanced composites, which represent a significant leap forward in building material technology. These advanced building components combine multiple materials to create products that outperform traditional options in nearly every metric.
Carbon fiber reinforced polymers (CFRP) lead the innovation wave, offering strength comparable to steel at just one-fifth the weight. These composites have found particular success in structural reinforcement and seismic retrofitting projects, where their high tensile strength and corrosion resistance provide crucial advantages.
Fiber-reinforced polymer (FRP) composites have emerged as game-changers for infrastructure projects. Their exceptional durability and resistance to environmental degradation make them ideal for bridges, marine structures, and high-stress architectural elements. Recent applications have demonstrated up to 30% reduction in installation time compared to conventional materials.
Glass fiber composites represent another breakthrough, particularly in facade systems and architectural panels. These materials offer superior thermal performance while maintaining structural integrity, with thermal conductivity rates 50% lower than traditional alternatives.
The integration of nano-materials into composite structures has yielded even more impressive results, with some hybrid composites showing up to 40% improvement in strength-to-weight ratios over first-generation composites. This advancement has opened new possibilities for sustainable, high-performance construction solutions that meet increasingly demanding building codes and environmental standards.
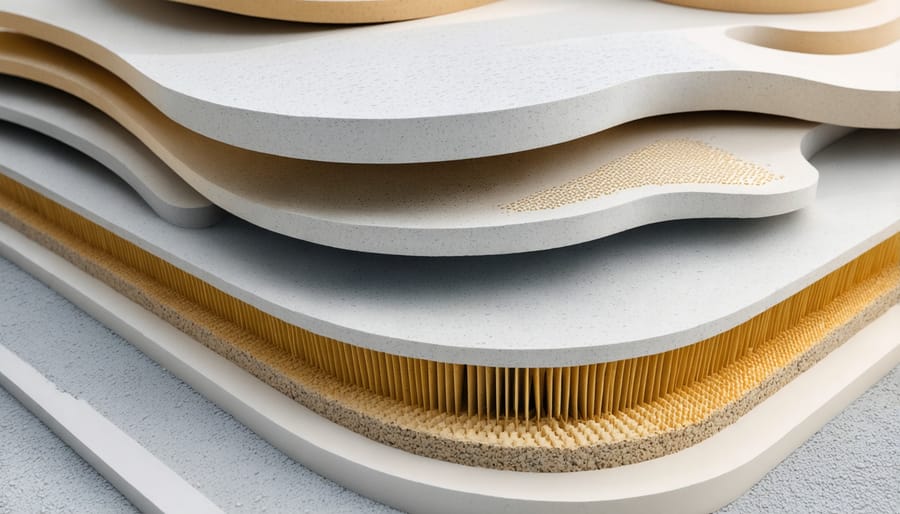
Smart Materials
Smart materials represent a revolutionary advancement in construction technology, offering adaptive properties that respond to environmental changes and integrated monitoring capabilities. These materials enhance building performance while providing real-time data about structural integrity and environmental conditions.
Phase-changing materials (PCMs) exemplify this innovation, automatically adjusting their physical state to regulate building temperature. When integrated into walls or ceiling panels, PCMs absorb excess heat during warm periods and release it when temperatures drop, significantly reducing energy consumption.
Self-healing concrete, incorporating specialized bacteria or polymers, can automatically repair minor cracks and fissures, extending structural longevity and reducing maintenance costs. This technology is particularly valuable in infrastructure projects exposed to harsh environmental conditions.
Piezoelectric materials convert mechanical stress into electrical signals, enabling continuous structural health monitoring. These materials can detect and report potential structural issues before they become critical, enhancing building safety and maintenance efficiency.
Smart glass technologies respond to changing light conditions, automatically adjusting their opacity to optimize natural lighting and thermal comfort. This reduces energy costs while improving occupant comfort.
Integrated sensor networks within smart materials provide real-time data about moisture levels, temperature variations, and structural loads. This information enables predictive maintenance strategies and optimal building performance management.
The implementation of smart materials requires careful consideration of cost-benefit ratios and specific project requirements. While initial costs may be higher than traditional materials, the long-term benefits in energy savings, maintenance reduction, and enhanced safety often justify the investment.
Sustainable Innovations
The construction industry is witnessing a remarkable shift toward sustainable innovations that combine environmental responsibility with superior performance. Advanced composite materials, such as carbon fiber-reinforced polymers and bio-based composites, are revolutionizing traditional building practices while maintaining exceptional structural integrity. These materials offer enhanced durability and reduced environmental impact compared to conventional options.
Cross-laminated timber (CLT) has emerged as a game-changing sustainable material, providing the strength of concrete while sequestering carbon and reducing construction time. When integrated with energy-efficient building solutions, CLT structures can achieve impressive sustainability metrics while meeting stringent building codes.
Recent developments in self-healing concrete incorporate beneficial bacteria that activate when cracks form, automatically repairing damage and extending the material’s lifespan. This innovation significantly reduces maintenance requirements and associated costs over time. Similarly, transparent wood, created through a novel chemical process, offers superior insulation properties while maintaining natural aesthetics and reducing reliance on artificial lighting.
Recycled materials are also being engineered to meet high-performance standards. Advanced processing techniques transform post-consumer plastics and glass into robust building components, while reclaimed steel undergoes rigorous testing to ensure structural integrity. These innovations demonstrate that sustainability and quality are not mutually exclusive but rather complementary aspects of modern construction materials.
Cost-Benefit Analysis
Initial vs. Lifecycle Costs
When evaluating building materials, the initial purchase price often overshadows the long-term financial implications. However, construction professionals must consider the total cost of ownership across a project’s lifespan. While premium materials typically demand higher upfront investments, they frequently yield substantial returns through reduced maintenance, extended durability, and enhanced performance.
Case studies consistently demonstrate that investing in quality materials can optimize construction costs over time. For instance, high-grade structural steel might cost 15-20% more initially but can extend a building’s service life by decades while minimizing maintenance expenses. Similarly, premium insulation materials may increase initial costs by 25% but typically deliver energy savings of 30-40% annually.
The lifecycle cost analysis should factor in installation efficiency, maintenance requirements, replacement intervals, and energy performance. Quality materials often facilitate faster installation, reducing labor costs and project timelines. They also tend to offer superior warranties, better resistance to environmental factors, and improved compliance with evolving building codes, ultimately providing better value for stakeholders despite higher initial investments.
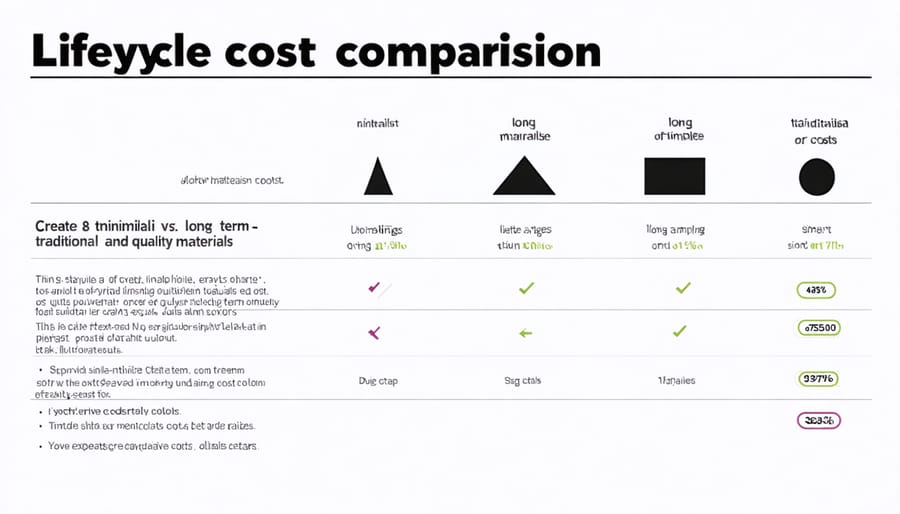
ROI Metrics
Measuring the ROI of quality building materials requires a systematic approach focused on several key performance indicators. Initial cost versus lifecycle value stands as a primary metric, typically calculated by comparing upfront material expenses against long-term maintenance savings and extended service life. Industry studies indicate that premium materials can reduce maintenance costs by 20-30% over a 10-year period.
Energy efficiency metrics play a crucial role, measured through thermal performance ratings, R-values, and annual energy consumption reduction. High-quality insulation materials, for instance, often demonstrate ROI within 3-5 years through reduced heating and cooling costs.
Durability metrics include weather resistance ratings, wear indices, and mean time between replacements. Construction professionals should track failure rates, warranty claims, and replacement frequency to quantify long-term cost benefits. Safety performance metrics, such as fire resistance ratings and structural integrity measures, contribute to insurance premium reductions and liability mitigation.
Project timeline efficiency serves as another vital indicator, with superior materials often reducing installation time and minimizing rework requirements. Documentation of labor cost savings, reduced callback rates, and accelerated project completion provides tangible evidence of material quality impact on overall project economics.
Implementation Strategies
Selection Criteria
When evaluating building materials, construction professionals must follow a systematic approach based on several critical factors. Performance requirements should be the primary consideration, including structural integrity, load-bearing capacity, and resistance to environmental factors. Materials must meet or exceed relevant building codes and industry standards while demonstrating proven durability in similar applications.
Cost analysis should encompass not just initial procurement expenses but also long-term maintenance requirements, lifecycle costs, and potential replacement intervals. This comprehensive financial assessment helps ensure optimal return on investment while maintaining quality standards.
Sustainability credentials have become increasingly important, requiring evaluation of environmental impact, recycled content, and energy efficiency. Look for materials with recognized certifications and documented performance data from independent testing laboratories.
Availability and supply chain reliability are crucial factors, as consistent material quality and timely delivery impact project schedules. Consider local sourcing options and manufacturer track records for meeting delivery commitments.
Technical compatibility with other building components must be verified through thorough documentation review and consultation with suppliers. This includes examining chemical compatibility, thermal expansion characteristics, and installation requirements.
Quality control measures should be assessed, including manufacturer testing protocols, batch consistency, and quality assurance programs. Request samples for testing and evaluate previous applications in similar environmental conditions.
Consider installation requirements, including specialized tools, skilled labor needs, and specific environmental conditions necessary for proper application. This evaluation helps prevent costly installation issues and ensures optimal material performance throughout the building’s lifecycle.
Integration Best Practices
Successful integration of quality building materials requires meticulous planning and execution throughout the construction process. Begin by establishing comprehensive material handling protocols, ensuring proper storage conditions to maintain material integrity. Temperature, humidity, and protection from environmental factors should be monitored consistently.
Implementation should follow manufacturer specifications precisely, with particular attention to installation sequences and compatibility between different materials. Create detailed quality control checkpoints at critical stages, documenting each phase with photographs and inspection reports.
Proper tool selection and calibration are essential for optimal installation results. Ensure all installation teams are thoroughly trained on material-specific techniques and safety requirements. Regular toolbox talks can help maintain awareness of best practices and address any emerging challenges.
Consider environmental conditions during installation. Many materials require specific temperature ranges and moisture levels for proper curing and bonding. Schedule installations accordingly and provide temporary climate control when necessary.
Maintain detailed records of batch numbers, installation dates, and environmental conditions for future reference and warranty purposes. Implement a systematic approach to testing and verification, including pull-out tests for anchors and adhesion tests for coatings.
Establish clear communication channels between suppliers, installers, and project managers to address technical questions promptly. Regular site inspections by manufacturer representatives can provide additional quality assurance and help identify potential issues before they become problems.
Finally, develop a comprehensive maintenance plan to ensure the longevity of installed materials, including cleaning protocols and scheduled inspections.
In today’s rapidly evolving construction landscape, the selection and implementation of quality building materials remain paramount to project success. Throughout this comprehensive examination, we’ve explored the critical factors that define superior construction materials, from durability and sustainability to cost-effectiveness and regulatory compliance.
The key takeaway for construction professionals is the necessity of a balanced approach to material selection. While initial costs matter, the long-term value proposition of high-quality materials often yields better returns through reduced maintenance, enhanced building performance, and improved occupant satisfaction. Industry leaders should prioritize materials that meet or exceed current building codes while anticipating future regulatory changes.
To implement these insights effectively, consider establishing a systematic approach to material evaluation that includes:
– Regular assessment of new market offerings and innovations
– Development of comprehensive testing protocols
– Creation of detailed material specifications
– Implementation of rigorous quality control measures
– Documentation of material performance over time
Success in modern construction projects demands careful attention to material selection, storage, and application. Stay informed about emerging technologies and sustainable alternatives, but always validate their practical applications before large-scale implementation. Remember that the most successful projects balance innovation with proven performance, ensuring that quality remains the cornerstone of every construction decision.
By maintaining these standards and continuously updating your knowledge base, you’ll be better positioned to deliver exceptional results that stand the test of time while meeting increasingly demanding project requirements.