Revolutionizing modern construction, offsite manufacturing represents a fundamental shift in how we design, build, and deliver construction projects. In controlled factory environments, building components are precision-engineered and assembled with unprecedented accuracy, reducing on-site construction time by up to 50% while maintaining superior quality standards. This manufacturing-led approach combines advanced automation, digital technology, and lean production methods to address the construction industry’s most pressing challenges: labor shortages, project delays, and rising costs.
Leading construction firms worldwide are rapidly adopting offsite manufacturing techniques, from modular buildings to prefabricated mechanical systems, driving a projected market growth from $130 billion in 2022 to over $200 billion by 2027. The integration of Building Information Modeling (BIM) with offsite manufacturing processes enables seamless collaboration between designers, manufacturers, and contractors, ensuring precise component fitting and minimal waste.
With sustainability demands intensifying and skilled labor becoming increasingly scarce, offsite manufacturing emerges as not just an alternative construction method, but a critical solution for the industry’s future. This transformative approach delivers consistent quality, reduced environmental impact, and enhanced worker safety while meeting the growing demand for faster, more efficient construction delivery.
The Evolution of Offsite Manufacturing in Construction
From Prefab to Advanced Manufacturing
The evolution of offsite manufacturing in construction has transformed dramatically from basic prefabricated components to sophisticated, technology-driven production systems. Early prefab methods focused primarily on simple modular units and standardized building elements, but today’s advanced manufacturing facilities leverage automation, robotics, and digital technologies to achieve unprecedented precision and efficiency.
Modern offsite facilities now integrate Building Information Modeling (BIM), artificial intelligence, and Internet of Things (IoT) sensors throughout the manufacturing process. These technologies enable real-time quality control, automated assembly processes, and seamless coordination between design teams and production floors. Computer-controlled machinery ensures consistent production quality while reducing material waste and labor costs.
The introduction of mass customization capabilities has been particularly revolutionary, allowing manufacturers to produce bespoke components at scale without sacrificing efficiency. Advanced materials like cross-laminated timber (CLT) and engineered composites have expanded the possibilities for prefabricated elements, while 3D printing technology is beginning to make its mark in component production.
This technological progression has elevated offsite manufacturing from a simple alternative to traditional construction to a sophisticated, data-driven approach that’s reshaping the industry’s future.
Digital Integration and Industry 4.0
Digital transformation is revolutionizing offsite manufacturing through the integration of innovative construction technologies and Industry 4.0 principles. Building Information Modeling (BIM) serves as the cornerstone of this evolution, enabling seamless collaboration between design teams and manufacturing facilities while ensuring precise component production and assembly.
Advanced robotics and automation systems are increasingly prevalent in offsite facilities, performing tasks such as cutting, welding, and assembly with unprecedented accuracy. These systems integrate with real-time monitoring and quality control processes, significantly reducing errors and improving production efficiency.
Internet of Things (IoT) sensors embedded throughout the manufacturing process provide valuable data on production metrics, environmental conditions, and material performance. This data-driven approach enables predictive maintenance, optimizes resource allocation, and ensures consistent quality standards across all manufactured components.
Cloud-based project management platforms facilitate real-time communication between stakeholders, allowing for immediate adjustments to design specifications and production schedules. This digital integration has dramatically improved supply chain visibility and coordination, reducing delays and ensuring just-in-time delivery of components to construction sites.
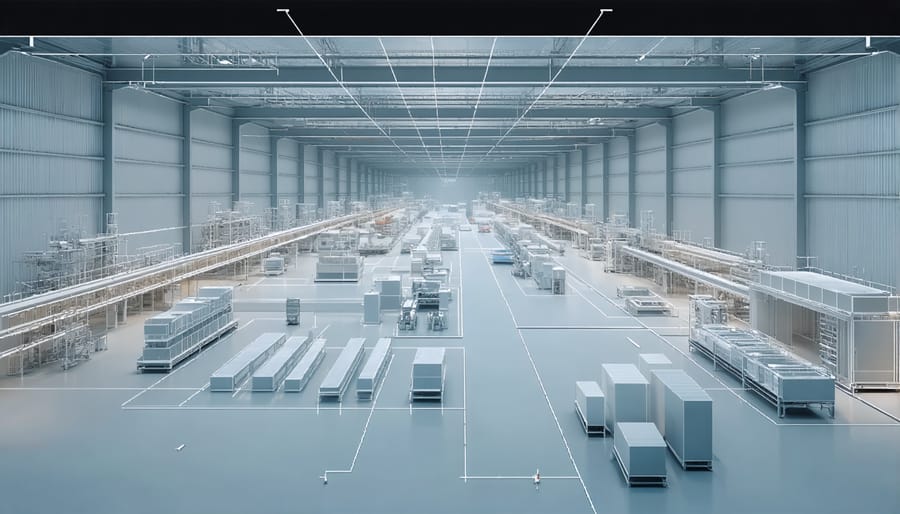
Key Components of Modern Offsite Manufacturing
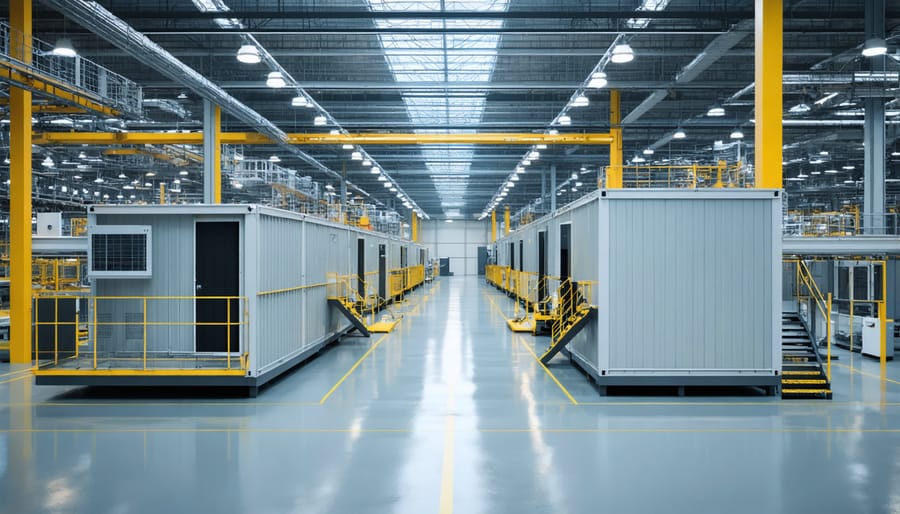
Modular Construction Systems
Modern modular construction systems represent a significant evolution in offsite manufacturing, encompassing various approaches that cater to different project requirements. Understanding the distinctions between modular vs prefab construction methods is crucial for implementing the most suitable solution for specific projects.
Volumetric modular systems, which involve the production of complete three-dimensional units in factory settings, offer the highest level of completion before site delivery. These units typically include finished interior components, mechanical systems, and exterior cladding. In contrast, panelized systems focus on manufacturing flat components like walls, floors, and roof sections, providing greater flexibility in transportation and final assembly.
Hybrid modular systems combine both approaches, utilizing volumetric units for high-specification areas like bathrooms and kitchens while employing panelized construction for other building sections. This flexibility allows contractors to optimize efficiency while maintaining quality control throughout the construction process.
Pod systems, specialized for specific room types, have gained popularity in hospitality and healthcare projects, where standardized, high-quality spaces are essential. These self-contained units are fully fitted in the factory, significantly reducing on-site installation time and ensuring consistent quality standards.
Panelized Building Components
Panelized building components represent a significant advancement in offsite manufacturing, offering a balanced approach between modular construction and traditional building methods. These engineered components typically include wall panels, roof trusses, and floor systems that are precision-manufactured in controlled factory environments.
The panels are designed using advanced CAD systems and manufactured with automated equipment, ensuring dimensional accuracy and consistent quality. Common types include structural insulated panels (SIPs), precast concrete panels, and light gauge steel frame panels, each offering specific advantages for different project requirements.
A key benefit of panelized construction is its flexibility in design and transportation. Unlike full modular units, panels can be efficiently packed and shipped to construction sites, reducing logistics costs. Once on-site, these components can be rapidly assembled, typically reducing construction time by 30-50% compared to traditional methods.
Quality control in panel manufacturing facilities includes rigorous testing protocols and inspection procedures. Environmental conditions are carefully controlled, eliminating weather-related delays and ensuring optimal material performance. This controlled environment also allows for precise integration of electrical, plumbing, and HVAC components within the panels.
Recent innovations in panel systems include advanced thermal performance features, improved fire resistance ratings, and enhanced acoustic properties, making them increasingly popular in both residential and commercial construction projects.
Quality Control and Standardization
Quality control in offsite manufacturing environments follows rigorous protocols and standardized processes that often exceed traditional on-site construction standards. Factory settings enable consistent environmental conditions, precise measurements, and automated quality checks throughout the production process. Each component undergoes multiple inspection points, from raw material verification to final assembly testing.
Modern offsite facilities employ advanced quality management systems that integrate digital technology, including 3D scanning, BIM compliance checks, and automated testing equipment. These systems ensure dimensional accuracy, structural integrity, and adherence to specifications while maintaining detailed documentation for quality assurance purposes.
Standardization plays a crucial role through implementation of ISO 9001 requirements and industry-specific certifications. Manufacturing facilities typically maintain dedicated quality control teams who conduct regular audits, perform materials testing, and verify compliance with building codes and regulations. This systematic approach results in significantly lower defect rates compared to traditional construction methods.
The controlled environment also allows for continuous improvement through data collection and analysis, enabling manufacturers to refine processes and implement preventive measures based on historical performance metrics.
Real-World Implementation and Case Studies
Commercial Project Success Stories
Several high-profile commercial modular construction projects have demonstrated the significant advantages of offsite manufacturing in recent years. The B1M4 Office Complex in London achieved a 30% reduction in construction time and a 20% cost saving through the implementation of prefabricated components. The project’s success hinged on precise factory-controlled manufacturing of structural elements and MEP systems.
In Singapore, the Crowne Plaza Changi Airport Hotel extension showcased the potential of Prefabricated Prefinished Volumetric Construction (PPVC). The 243-room addition was completed in just 17 months, less than half the time required for traditional construction methods. Each room module was fully finished offsite, complete with interior fixtures and furnishings, achieving exceptional quality control standards.
The McDonald’s Restaurant Standardization Program in Australia demonstrates how offsite manufacturing can optimize franchise development. Using prefabricated modules, new restaurants are assembled in just 48 hours on-site, reducing local disruption and ensuring consistent brand standards across locations.
These projects highlight key benefits of offsite manufacturing: accelerated project delivery, improved quality control, reduced site disruption, and enhanced sustainability through waste reduction. The success of these implementations has led to increased adoption across the commercial construction sector, particularly in urban areas where minimizing construction impact is crucial.
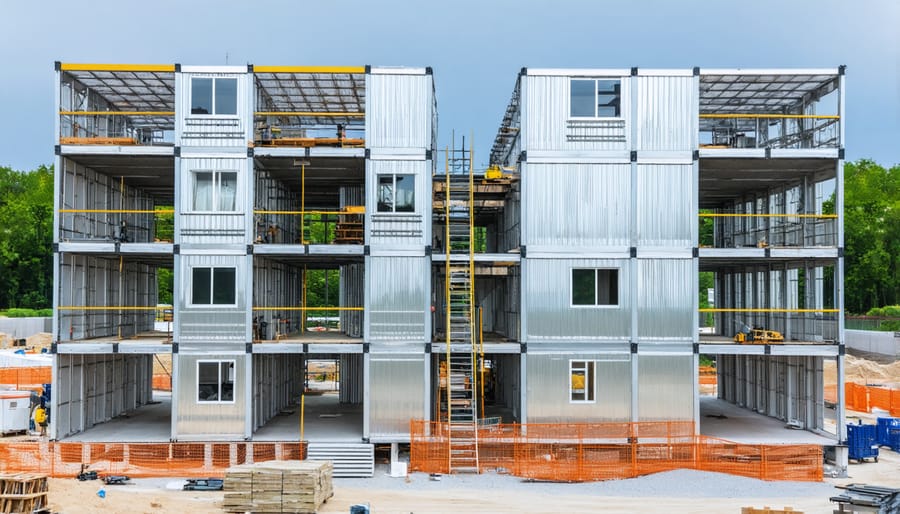
Residential Development Applications
Several notable residential development projects have successfully implemented offsite manufacturing, demonstrating its effectiveness in housing construction. The Apex Housing Development in Manchester, UK, completed in 2022, utilized modular construction for 120 apartments, reducing the construction timeline by 40% compared to traditional methods. The project achieved a 30% cost reduction while maintaining high-quality standards through factory-controlled production.
In Australia, the Nightingale Village project in Melbourne showcased the integration of prefabricated elements across seven buildings. The development incorporated pre-assembled bathroom pods, structural panels, and MEP systems, resulting in minimal on-site waste and a 25% faster completion time. The quality control measures in the factory environment led to superior thermal performance and reduced defects.
The Urban Village Project in Sweden represents another successful implementation, where 85% of the construction process occurred offsite. This development of 200 residential units featured standardized components that could be easily maintained and replaced, promoting long-term sustainability. The project achieved a remarkable 45% reduction in carbon emissions compared to conventional construction methods.
These case studies demonstrate how offsite manufacturing can address housing demands efficiently while maintaining high standards of quality and sustainability. The success of these projects has influenced other developers to adopt similar approaches, particularly in urban areas where construction speed and minimal disruption are crucial factors.
Cost and Time Savings Analysis
Studies consistently demonstrate that offsite manufacturing delivers significant cost and time savings compared to traditional construction methods. Analysis of recent industry data reveals that projects utilizing offsite manufacturing typically achieve 20-30% reduction in overall construction time and 15-25% decrease in total project costs.
These efficiency gains stem from several key factors. The controlled factory environment eliminates weather-related delays and enables simultaneous site preparation and component manufacturing. Labor costs decrease substantially due to streamlined processes, reduced material waste, and improved worker productivity in the factory setting.
Research from leading construction firms indicates that offsite manufacturing can reduce material waste by up to 90% compared to on-site construction. This not only reduces direct material costs but also minimizes disposal expenses and environmental impact. Quality control measures in the factory environment result in fewer defects and rework, further contributing to cost savings.
Time savings are particularly notable in large-scale projects. Case studies of commercial buildings show that offsite manufacturing can reduce construction schedules by up to 50%. This acceleration translates to earlier occupancy, faster return on investment, and reduced financing costs.
Additional cost benefits include lower site supervision requirements, reduced equipment rental periods, and decreased insurance premiums due to lower on-site risks. When factoring in lifecycle costs, offsite manufactured buildings often demonstrate superior long-term value through improved energy efficiency and reduced maintenance needs.
Future Outlook and Industry Impact
Emerging Technologies and Innovation
The future of offsite manufacturing is being shaped by groundbreaking technological innovations that promise to revolutionize construction processes. Advanced robotics and automation systems are increasingly being integrated into manufacturing facilities, enabling precise assembly of building components with minimal human intervention. Artificial Intelligence (AI) and machine learning algorithms are optimizing production schedules and enhancing quality control processes, while contributing to construction supply chain optimization.
Digital twin technology is emerging as a game-changer, allowing manufacturers to create virtual replicas of building components and simulate their performance before production begins. This capability significantly reduces errors and enables real-time modifications to meet specific project requirements. 3D printing technology is also advancing rapidly, with manufacturers now able to produce complex architectural elements and structural components at scale.
The integration of Internet of Things (IoT) sensors and smart materials is enabling enhanced monitoring of prefabricated components during manufacturing, transportation, and installation. These technologies provide valuable data for quality assurance and help predict maintenance needs throughout the building’s lifecycle, marking a significant step forward in construction efficiency and sustainability.
Market Growth Projections
The offsite manufacturing market is experiencing robust growth, with industry analysts projecting a compound annual growth rate (CAGR) of 6.8% from 2023 to 2028. This trajectory is driven by increasing demand for sustainable construction methods, labor shortage solutions, and improved project efficiency. Recent market research indicates that the global offsite construction market, valued at $157.2 billion in 2022, is expected to reach $235.4 billion by 2028.
Key growth drivers include urbanization in developing economies, government initiatives promoting prefabrication, and technological advancements in manufacturing processes. The residential sector shows particularly strong potential, with modular housing solutions gaining traction across major markets. Commercial construction follows closely, with healthcare and education facilities leading adoption rates.
Regional analysis suggests Asia-Pacific will maintain the highest growth rate, followed by North America and Europe. This growth is supported by increasing investments in smart manufacturing facilities and the integration of Industry 4.0 technologies. Industry experts anticipate that by 2025, approximately 30% of new construction projects in developed markets will incorporate significant offsite components, marking a transformative shift in traditional construction methodologies.
Offsite manufacturing represents a transformative approach that is reshaping the construction industry’s future. The benefits of improved quality control, reduced waste, faster project completion, and enhanced worker safety make it an increasingly attractive option for construction firms worldwide. As technology continues to advance, particularly in areas of automation and digital design integration, the potential for offsite manufacturing will only grow. Industry leaders are already seeing significant returns on investment through reduced labor costs, improved sustainability metrics, and heightened project predictability. Looking ahead, the sector is poised for substantial growth, driven by increasing urbanization, housing demands, and the need for more sustainable construction methods. While challenges remain in areas such as initial investment costs and supply chain optimization, the trajectory of offsite manufacturing suggests it will become an integral part of modern construction practices, fundamentally changing how we approach building projects.