Single-story modular homes revolutionize residential construction by delivering up to 50% faster build times and 20% lower costs compared to traditional site-built homes. Modern modular vs prefab construction methods have evolved to meet stringent quality standards while offering unprecedented design flexibility and structural integrity. Industry data demonstrates that precision-engineered modules, constructed in controlled factory environments, consistently outperform conventional building methods in terms of material waste reduction, energy efficiency, and quality control metrics. For construction professionals and project stakeholders, single-story modular construction represents a compelling solution to address rising labor costs, compressed project timelines, and increasingly complex building regulations while maintaining superior quality standards and architectural versatility.
The Engineering Behind Single-Story Modular Construction
Design and Manufacturing Process
The design and manufacturing process of single-story modular homes employs innovative construction techniques within climate-controlled factory environments. Computer-aided design (CAD) software enables precise architectural planning and engineering calculations, ensuring structural integrity and optimal space utilization. Each module undergoes a systematic production sequence on assembly lines, where specialized teams focus on specific components.
The process begins with the steel chassis fabrication, followed by floor system assembly and structural wall erection. Electrical, plumbing, and HVAC systems are installed with remarkable precision, as the controlled environment eliminates weather-related variables. Quality control inspectors verify each phase of construction against stringent building codes and manufacturer specifications.
Interior finishes, including drywall, cabinetry, and flooring, are installed while modules remain protected from environmental elements. This controlled setting allows for superior material storage conditions and consistent application of finishes. Simultaneously, exterior components such as roofing, siding, and insulation are applied using standardized procedures that ensure uniform quality.
The manufacturing process typically requires 6-12 weeks from initial design to completion, significantly faster than traditional construction methods. Each module undergoes final quality assurance testing before transportation to the building site, where crane-assisted assembly and utility connections complete the home installation process.
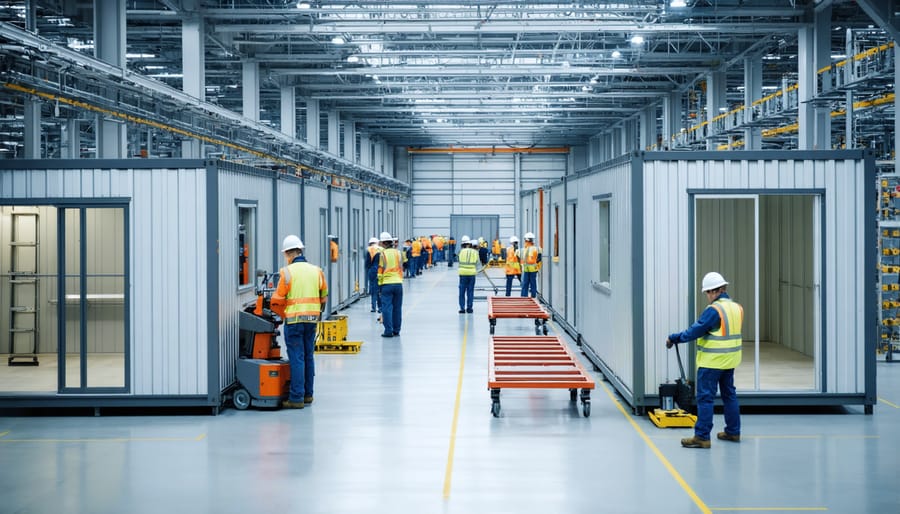
Quality Control and Building Standards
Quality control in single-story modular construction adheres to rigorous standards that often exceed those of traditional site-built homes. Each module undergoes systematic inspection at multiple stages during the factory-based manufacturing process, ensuring consistent quality and compliance with local, state, and federal building codes.
The manufacturing environment enables precise quality control through standardized procedures and automated processes. Third-party inspectors regularly assess structural components, electrical systems, plumbing installations, and insulation during assembly. These inspections are documented through detailed reports and photographic evidence, providing comprehensive verification of compliance with building standards.
Modular homes must meet or exceed the International Building Code (IBC) requirements, along with specific state and local regulations. The production process includes multiple checkpoints where qualified professionals verify structural integrity, material quality, and proper installation of all components. Factory conditions allow for precise moisture control during construction, significantly reducing the risk of mold and material warping common in traditional construction.
Quality assurance extends beyond the factory floor through transportation and installation phases. Specialized packaging and handling procedures protect modules during transit, while certified installers follow manufacturer specifications for foundation preparation and module assembly. Post-installation inspections ensure proper connection of utilities and structural elements, completing a comprehensive quality control cycle that maintains the integrity of the modular home from production to occupancy.
Cost Analysis and Time Efficiency
Construction Timeline Advantages
Single-story modular construction offers significant timeline advantages over traditional site-built homes, with projects typically completing 30-50% faster. While conventional construction methods require 6-9 months for completion, modular homes can be ready for occupancy in just 3-4 months, depending on site conditions and local regulations.
This accelerated timeline is achieved through parallel construction processes. While site work and foundations are being prepared on-location, the home’s modules are simultaneously being manufactured in a climate-controlled facility. This concurrent production eliminates weather-related delays and reduces the impact of labor shortages that often plague traditional construction sites.
Industry data shows that modular construction can reduce overall project duration by up to 50% through standardized processes and assembly-line efficiency. A typical single-story modular home’s timeline breaks down as follows:
– Factory Production: 4-6 weeks
– Site Preparation: 2-3 weeks
– Module Transportation: 1-2 days
– On-site Assembly: 1-2 weeks
– Final Finishing: 2-3 weeks
Recent case studies demonstrate even greater efficiency gains. The Riverside Development Project in Colorado completed 12 single-story modular homes in the time traditionally required for four site-built homes, representing a 66% reduction in construction duration. This acceleration directly translates to reduced carrying costs, earlier occupancy, and faster return on investment for developers and property owners.
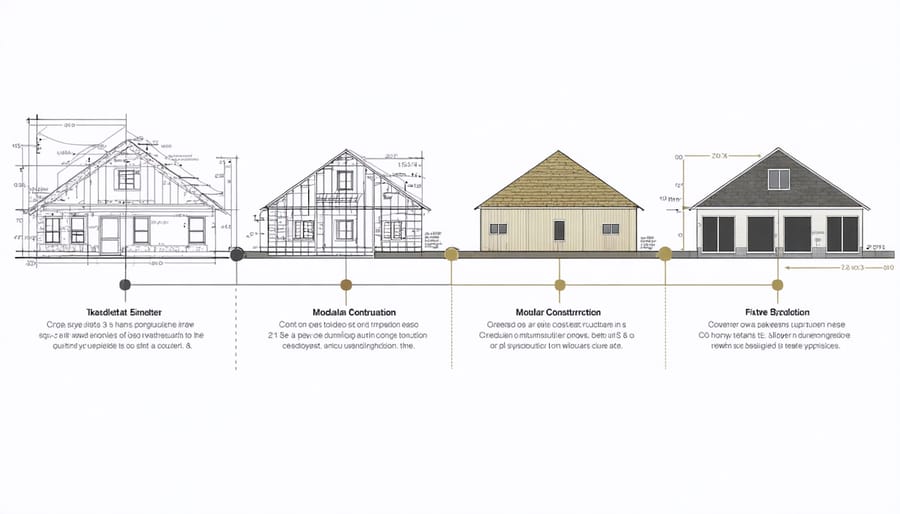
Cost-Benefit Analysis
A comprehensive cost-benefit analysis of single-story modular homes reveals significant financial advantages when compared to traditional construction methods. Initial construction costs typically range from $80 to $160 per square foot, representing a 10-20% reduction in overall project expenses. These savings primarily stem from reduced labor costs, shortened construction timelines, and minimized material waste.
Project timelines for modular construction average 30-50% shorter than conventional builds, directly impacting carrying costs and enabling faster return on investment. Construction financing requirements are generally lower due to abbreviated build schedules, while the controlled factory environment minimizes weather-related delays and associated cost overruns.
Long-term value considerations demonstrate favorable outcomes in several key areas. Energy efficiency ratings in modular homes typically exceed those of site-built counterparts by 15-20%, resulting in reduced operational costs throughout the building’s lifecycle. Insurance premiums often prove more competitive due to superior quality control and structural integrity inherent in factory-built components.
Recent industry data indicates that modular homes maintain comparable appreciation rates to traditional construction, with some markets showing superior value retention. Maintenance costs generally trend lower due to precise factory assembly and rigorous quality control measures. Additionally, the standardized construction process facilitates more accurate cost forecasting and budgeting.
However, potential cost implications include transportation expenses, which typically account for 3-5% of total project costs, and site preparation requirements, which remain comparable to traditional construction. Crane rental and setting costs must also be factored into the initial budget, though these expenses are often offset by reduced labor requirements and accelerated project completion.
Sustainable Features and Energy Efficiency
Environmental Impact
Single-story modular construction demonstrates significant environmental advantages over traditional building methods, primarily through waste reduction and sustainable material utilization. Industry studies indicate that modular construction typically generates 30-40% less waste compared to site-built homes, as materials are precisely cut and assembled in controlled factory environments.
The controlled manufacturing process enables efficient material recycling programs, with many facilities achieving recycling rates above 90% for materials like steel, wood, and drywall. Advanced inventory management systems ensure optimal material usage, while standardized dimensions reduce off-cuts and excess material ordering.
Sustainable material selection in modular construction frequently includes recycled steel frames, FSC-certified lumber, low-VOC finishes, and energy-efficient insulation materials. Many manufacturers are now incorporating innovative eco-friendly materials such as bamboo flooring, recycled composite decking, and sustainably sourced structural components.
Factory construction also minimizes site disturbance and reduces carbon emissions associated with construction vehicle traffic. A recent industry analysis revealed that modular projects typically require 40% fewer vehicle movements compared to traditional construction methods. Additionally, the controlled environment allows for better implementation of moisture management protocols, reducing the risk of material damage and subsequent waste during the construction process.
Energy Performance
Single-story modular homes excel in energy-efficient modular construction due to their controlled factory assembly environment and advanced materials integration. Contemporary modular units typically achieve energy performance ratings 20-30% superior to traditional site-built homes, primarily through precision-engineered building envelopes and systematic quality control during manufacturing.
Key energy performance features include factory-installed continuous insulation, triple-pane windows with low-E coatings, and advanced air sealing techniques that minimize thermal bridging. The controlled environment allows for precise installation of mechanical systems and ensures consistent optimizing building energy efficiency across all components.
Recent industry data indicates that single-story modular homes routinely achieve HERS Index scores between 45-60, significantly outperforming the reference home score of 100. This translates to substantial operational cost savings, with many owners reporting 40-50% reductions in annual energy consumption compared to conventional construction.
Smart home technology integration during factory assembly further enhances energy performance through automated climate control systems and real-time energy monitoring capabilities, enabling precise management of resource consumption while maintaining optimal comfort levels.
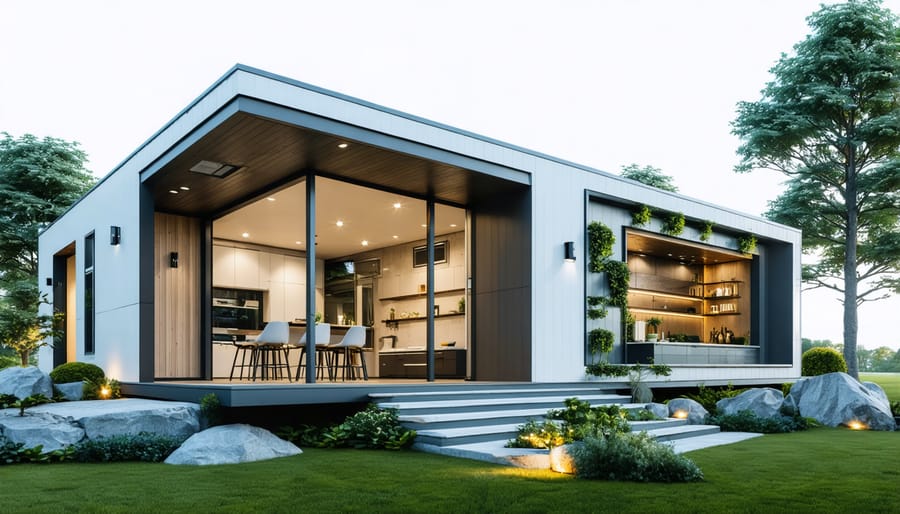
Case Study: Recent Single-Story Modular Project
The Oakridge Development in Colorado Springs, completed in 2023, serves as an exemplary demonstration of modern single-story modular construction excellence. This 2,400-square-foot residential project, executed by Summit Modular Construction in partnership with Green Valley Architects, showcases the efficiency and innovation possible in contemporary modular building.
The project consisted of four modules, each precisely manufactured in Summit’s climate-controlled facility over eight weeks. The design incorporated advanced energy-efficient features, including triple-pane windows, spray foam insulation, and a smart HVAC system, resulting in a HERS rating of 42 – significantly better than traditional site-built homes.
Key project metrics demonstrate the advantages of modular construction:
– Total construction time: 14 weeks (8 weeks in-factory, 6 weeks on-site)
– Cost savings: 15% compared to traditional construction methods
– Weather-related delays: Zero
– Change orders: Only two minor adjustments
– Waste reduction: 87% less construction waste than comparable site-built projects
The foundation work commenced while modules were being manufactured, utilizing a modified pier-and-beam system specifically designed for modular applications. This parallel processing contributed significantly to the accelerated project timeline.
Quality control measures included thorough factory inspections at five key stages, with third-party verification ensuring compliance with both local building codes and ICC-approved modular construction standards. The modules underwent extensive testing for structural integrity, including specialized transportation stress analysis.
Project challenges included coordinating precise delivery timing with crane availability and managing site access on a relatively compact lot. The construction team overcame these obstacles through detailed logistics planning and the use of a specialized transport system with hydraulic leveling capabilities.
The finished home features:
– 3 bedrooms, 2.5 bathrooms
– Open-concept living area
– 9-foot ceiling height throughout
– Custom-designed kitchen with prefabricated cabinetry
– Integrated smart home technology
– Zero-threshold entries for accessibility
– Energy-efficient appliances and LED lighting
Post-completion analysis revealed that the modular approach reduced the project’s carbon footprint by approximately 43% compared to traditional construction methods, primarily due to reduced transportation requirements and minimal on-site construction activity. The project has since become a benchmark for sustainable, efficient modular construction in the region.
Single-story modular homes represent a significant advancement in construction technology, offering compelling advantages that position them as a formidable solution for modern building needs. The evidence from numerous successful implementations demonstrates their superior cost-efficiency, with projects consistently reporting 10-20% savings compared to traditional construction methods. The reduced construction timeline, typically 30-50% faster than conventional building approaches, delivers substantial financial benefits while maintaining exceptional quality standards.
Industry trends indicate a growing adoption of single-story modular construction, driven by increasing labor costs and skilled worker shortages in traditional construction. The controlled factory environment ensures consistent quality, while advanced manufacturing processes and technologies continue to expand design possibilities and customization options.
Looking ahead, the sector is poised for significant growth, with projections suggesting a 5.8% annual increase in modular construction adoption over the next five years. Technological innovations in materials and manufacturing processes are expected to further enhance the benefits of modular construction, particularly in energy efficiency and sustainability metrics.
For construction professionals and project stakeholders, single-story modular homes offer a practical, efficient, and future-ready solution that addresses current industry challenges while meeting evolving market demands. As environmental regulations tighten and labor markets remain competitive, the advantages of modular construction will likely become even more pronounced, cementing its position as a preferred method for residential construction projects.