Design an industrial building with purpose, efficiency, and safety at the forefront. Consider the specific operational needs and workflow of the facility to optimize layout and functionality. Incorporate sustainable features like energy-efficient systems, natural lighting, and eco-friendly materials to reduce environmental impact and operating costs. Prioritize employee well-being with ergonomic workspaces, proper ventilation, and amenities that promote a healthy, productive work environment. Ensure compliance with all relevant building codes, safety regulations, and industry standards to create a structurally sound, hazard-free facility.
1. Site Selection and Layout
Choosing the Right Location
When choosing the right location for an industrial building, several key factors must be carefully considered. The site should align with the facility’s operational needs, ensuring efficient workflows and optimal productivity. Zoning regulations and land use restrictions are critical, as the chosen location must permit the intended industrial activities. Access to essential utilities, such as power, water, and waste management, is paramount for smooth operations. The site should also offer convenient accessibility for employees, suppliers, and distribution networks, considering proximity to highways, ports, or rail lines. Moreover, the potential for future expansion should be evaluated, allowing room for business growth and adaptability to changing market demands. By thoroughly assessing these aspects, decision-makers can select a location that sets the foundation for a successful and sustainable industrial facility.
Optimizing Site Layout
When designing an industrial building, optimizing the site layout is critical for maximizing efficiency and functionality. Careful consideration should be given to the arrangement of structures, parking areas, loading docks, and traffic flow patterns. By strategically placing these elements, designers can streamline operations, minimize congestion, and enhance safety. Leveraging the natural features of the site, such as topography, drainage patterns, and existing vegetation, can also contribute to a more sustainable and cost-effective design. Conducting thorough site analysis and engaging in collaborative planning with stakeholders are essential steps in achieving an optimized site layout that meets the specific needs of the industrial facility.
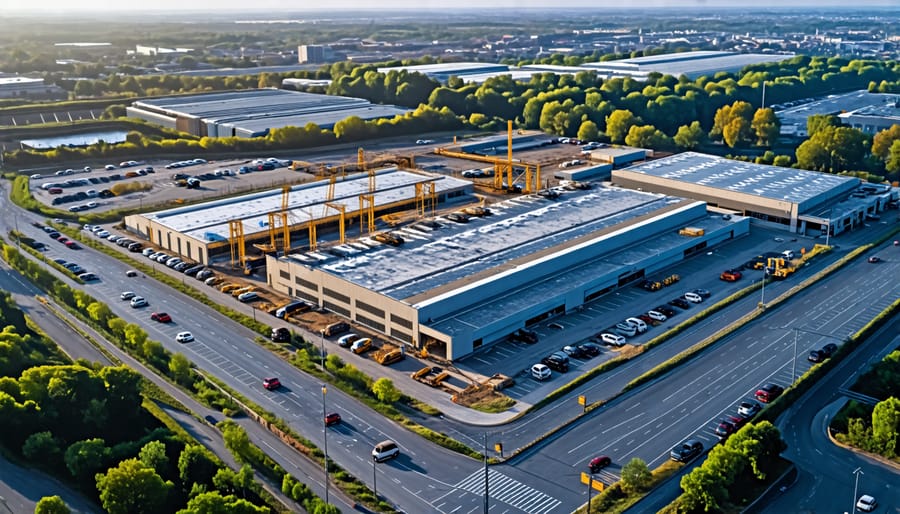
2. Structural Design and Materials
Determining the optimal structural design and materials is crucial for ensuring an industrial building’s long-term performance and functionality. The building’s framing system, whether steel, concrete, or a combination, must provide the necessary strength, stability, and support for the intended use. Factors such as load-bearing capacity, span distances, and resistance to environmental stressors should guide the selection process.
Roofing materials should be chosen based on durability, energy efficiency, and compatibility with the building’s design and climate. Options range from traditional built-up roofs to more modern single-ply membranes and metal roofing systems. Exterior cladding materials should balance aesthetic appeal with practical considerations like weatherproofing, insulation value, and ease of maintenance. Popular choices include precast concrete panels, metal siding, and insulated composite panels.
When selecting materials, prioritize those that offer the best combination of durability, cost-effectiveness, and sustainability. Life-cycle cost analysis can help identify options that provide the greatest long-term value. Additionally, consider materials with inherent fire resistance, low maintenance requirements, and minimal environmental impact. Engaging with experienced structural engineers and building envelope consultants can provide valuable insights and ensure the design meets all performance and code requirements while optimizing constructability and budget.
3. Workflow and Equipment Integration
Analyzing Workflows
Analyzing workflows is a critical first step in designing an efficient industrial building. Collaborating closely with end users, such as production managers and employees, provides invaluable insights into daily processes, equipment requirements, and storage needs. By thoroughly understanding these operational details, architects and engineers can optimize the layout and flow of the facility.
Through careful space planning, the design team can minimize wasted motion, streamline material handling, and create a logical progression of activities. Factors such as the size and placement of equipment, the width of aisles, and the location of storage areas all contribute to overall efficiency. By designing with workflow in mind, industrial buildings can maximize productivity, reduce bottlenecks, and create a safer, more ergonomic environment for workers. Ultimately, a well-designed facility not only enhances operational performance but also positively impacts the bottom line.
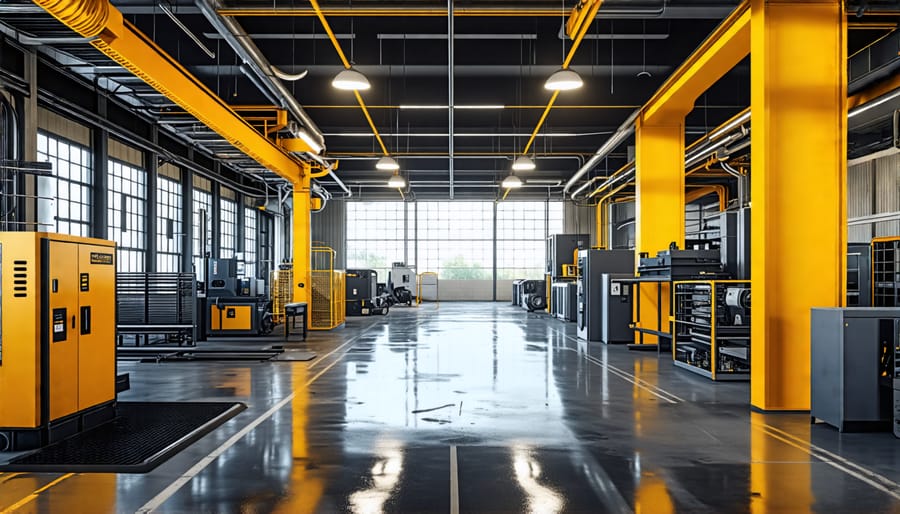
Flexibility and Adaptability
Flexibility and adaptability are crucial considerations in the design of modern industrial buildings. To accommodate evolving business needs, the facility should incorporate modular elements and moveable interior walls that enable easy reconfiguration of the space. This allows for seamless changes to production lines, storage areas, and office layouts as the company grows or pivots.
The structure itself should be designed with future expansion in mind, such as the ability to add additional floors or extend the building footprint. Utility connections and key systems should be strategically placed to facilitate these potential changes. Equipment requirements may also shift over time, so the building must provide ample clearance heights, load-bearing capacity, and power supplies to handle new machinery or technology. By prioritizing flexibility and modularity, industrial buildings can adapt to the dynamic needs of the businesses they house, maximizing long-term value and functionality.
4. Utilities and Building Systems
Proper design of utilities and building systems is crucial for creating an efficient and sustainable industrial facility. The HVAC system should be designed to maintain optimal indoor air quality and temperature control while minimizing energy consumption. This can be achieved through the use of high-efficiency equipment, smart controls, and heat recovery systems. The electrical system must be robust, reliable, and able to handle the facility’s power requirements. Consideration should be given to the use of energy-efficient lighting, such as LED fixtures, and the incorporation of renewable energy sources like solar panels.
Plumbing and fire suppression systems are critical for ensuring the safety and functionality of the building. The plumbing system should be designed to minimize water usage and incorporate water-saving fixtures. The fire suppression system, including sprinklers and alarms, must be designed to meet local building codes and ensure rapid response in case of an emergency. Lighting design should prioritize both energy efficiency and the creation of a comfortable, productive work environment. This can be achieved through the use of natural daylight, task lighting, and smart controls that adjust lighting levels based on occupancy and time of day. By carefully designing and integrating these building systems, industrial facilities can optimize their operational efficiency, reduce costs, and minimize their environmental impact.
5. Safety and Code Compliance
Ensuring the safety and code compliance of an industrial facility is paramount. Architects and engineers must adhere to strict building codes and safety standards throughout the design process. Fire protection systems, including sprinklers, alarms, and fire-rated materials, are essential to safeguard the building and its occupants. Well-designed emergency egress routes, clearly marked exits, and accessible pathways ensure efficient evacuation in case of emergencies. Special consideration must be given to the proper storage, handling, and disposal of any hazardous materials used in the industrial processes. Ventilation systems and containment measures are crucial to maintain a safe working environment. Regular safety audits and inspections should be conducted to identify and address any potential risks or code violations. By prioritizing safety and code compliance, industrial facility designers create structures that protect both the workers and the surrounding community.
6. Employee Comfort and Productivity
Designing industrial facilities with employee comfort and productivity in mind is crucial for creating a positive work environment. Architects and engineers should prioritize natural lighting, as it has been shown to boost mood, alertness, and overall employee well-being. Incorporating large windows, skylights, and light shelves can help maximize daylight penetration while minimizing glare. Maintaining optimal air quality is another key factor, which can be achieved through proper ventilation, air filtration systems, and the use of low-emitting materials. Noise control measures, such as sound-absorbing panels, acoustic baffles, and designated quiet zones, can help reduce distractions and stress levels. Additionally, providing amenities like ergonomic workstations, breakout areas, and green spaces can further enhance employee comfort and foster a sense of community within the workplace. By prioritizing these elements, industrial facility designers can create environments that not only support employee well-being but also contribute to increased productivity and job satisfaction.
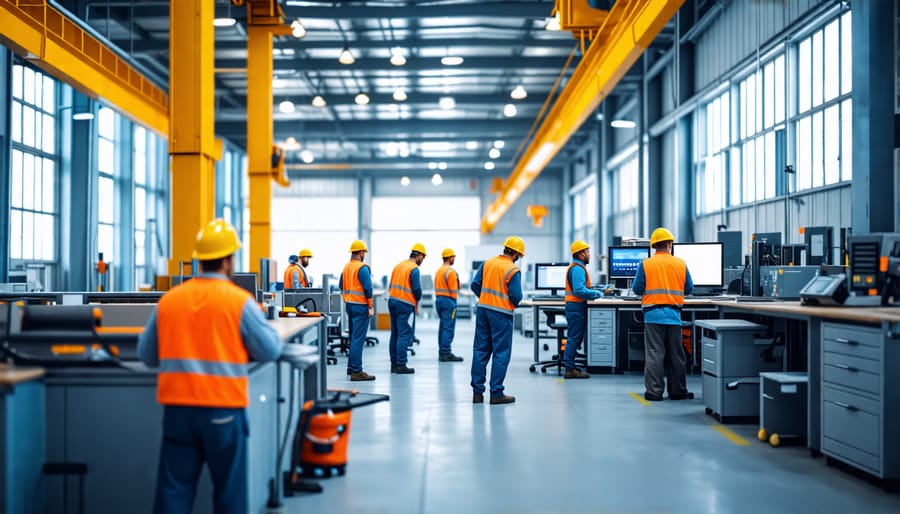
7. Sustainability and Energy Efficiency
Sustainability and energy efficiency are critical considerations in modern industrial building design. By incorporating green building practices, architects and engineers can significantly reduce environmental impact while also minimizing long-term operational costs. One key strategy is to integrate renewable energy systems, such as solar panels or wind turbines, which can generate clean power for the facility and reduce reliance on fossil fuels. Water conservation is another essential aspect, achievable through the use of low-flow fixtures, rainwater harvesting, and efficient landscaping. Selecting sustainable materials, such as recycled steel, low-VOC paints, and responsibly sourced timber, further contributes to the building’s eco-friendly profile. By conducting thorough energy modeling and life-cycle assessments, designers can optimize the facility’s performance and ensure it meets the highest standards of sustainability. Ultimately, by prioritizing green design principles, industrial buildings can serve as exemplars of responsible development, demonstrating that environmental stewardship and economic success can go hand in hand.
Conclusion
In conclusion, designing an efficient and optimized industrial building requires careful consideration of seven key aspects: site selection and planning, building layout and workflow, structural engineering, building envelope, mechanical and electrical systems, interior design, and sustainability and energy efficiency. By taking a thoughtful, holistic approach that addresses each of these vital elements, architects, engineers, and project stakeholders can create industrial facilities that maximize productivity, minimize operating costs, and provide a safe, comfortable working environment for employees. A well-designed industrial building not only supports the specific needs of the business it houses but also contributes to the long-term success and growth of the company. By prioritizing these essential design factors and working collaboratively with experienced professionals, decision-makers can ensure that their industrial building projects are delivered on time, within budget, and to the highest standards of quality and performance.