In today’s construction landscape, sustainability isn’t just an environmental imperative—it’s a critical business strategy driving profitability, compliance, and competitive advantage. Leading construction firms are revolutionizing project delivery through comprehensive sustainability plans that reduce environmental impact while delivering superior ROI. From LEED certification requirements to stringent environmental regulations and increasing client demands, sustainable construction practices have evolved from optional considerations to essential project components. This transformation demands a structured approach that integrates environmental stewardship with practical building methodologies and financial performance metrics.
A well-designed construction sustainability plan addresses three fundamental pillars: environmental protection, economic efficiency, and social responsibility. By implementing strategic waste reduction protocols, energy-efficient building techniques, and responsible material sourcing, forward-thinking construction companies are achieving remarkable results—reducing operational costs by up to 30% while meeting increasingly strict environmental standards. These initiatives not only minimize ecological footprints but also enhance project marketability, strengthen stakeholder relationships, and ensure long-term business viability in an industry rapidly adapting to climate change challenges.
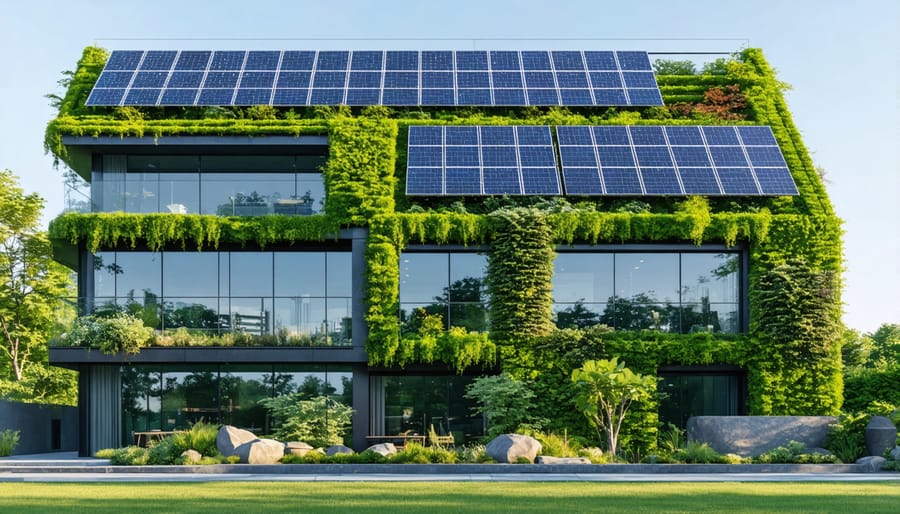
The Business Case for Sustainable Construction
ROI of Green Building Practices
Recent industry studies demonstrate that investing in sustainable construction practices yields significant financial returns. Analysis of over 200 green building projects reveals an average ROI of 7-12% within the first five years of operation. Energy-efficient systems typically reduce operational costs by 20-30%, while water conservation measures cut utility expenses by 30-50% annually.
Green buildings command premium rental rates, averaging 6% higher than conventional properties, and maintain consistently higher occupancy rates. The initial cost premium for green construction, typically 2-7% above traditional methods, is recovered within 3-5 years through reduced operational expenses and increased property value.
Case studies from major commercial developments demonstrate that LEED-certified buildings achieve 25% lower energy consumption and 11% lower water usage, translating to annual savings of $0.75-$1.50 per square foot. Additionally, green buildings report 27% higher occupant satisfaction rates, leading to reduced tenant turnover and decreased vacancy periods, further enhancing long-term financial performance.
Meeting Environmental Regulations
Construction projects must navigate an increasingly complex landscape of environmental regulations at local, national, and international levels. Key regulations include building energy codes, waste management requirements, and emissions standards. The International Green Construction Code (IgCC) sets comprehensive sustainability requirements, while LEED certification guidelines continue to influence regulatory frameworks worldwide.
Recent updates to environmental regulations emphasize carbon reduction targets, with many jurisdictions implementing mandatory reporting of embodied carbon in construction materials. Projects must also comply with stricter water management protocols and enhanced biodiversity protection measures. Construction firms should particularly note upcoming regulations on circular economy principles, which will require increased material recycling and waste reduction.
To ensure compliance, construction teams should maintain updated regulatory databases, conduct regular compliance audits, and engage environmental consultants during project planning phases. Early integration of regulatory requirements into project designs can prevent costly modifications later. Additionally, staying ahead of emerging regulations through industry association memberships and participation in sustainability forums can provide competitive advantages while ensuring seamless regulatory alignment.
Core Elements of a Construction Sustainability Plan
Material Selection and Waste Management
Material selection and waste management form critical components of sustainable construction practices. The selection of eco-friendly materials begins with a comprehensive lifecycle assessment, evaluating environmental impact from extraction through disposal. Priority should be given to materials with high recycled content, local sourcing to reduce transportation emissions, and those carrying recognized environmental certifications such as FSC for timber or EPDs for manufactured products.
Implementing a robust waste management strategy requires establishing a construction waste management plan (CWMP) before project commencement. This plan should target a minimum 75% waste diversion rate through systematic sorting and recycling protocols. Key practices include establishing designated on-site recycling zones, training workers in proper waste segregation, and partnering with certified recycling facilities.
Effective material management also involves precise quantity takeoffs to prevent overordering, implementing just-in-time delivery schedules, and utilizing Building Information Modeling (BIM) to optimize material usage. Consider implementing a closed-loop material system where possible, incorporating salvaged materials from demolition into new construction.
Storage and handling procedures should be optimized to prevent material damage and waste. This includes proper weather protection, organized storage areas, and careful handling protocols. Regular waste audits help track progress and identify areas for improvement, while detailed documentation of diverted materials can contribute to green building certification requirements and demonstrate environmental commitment to stakeholders.
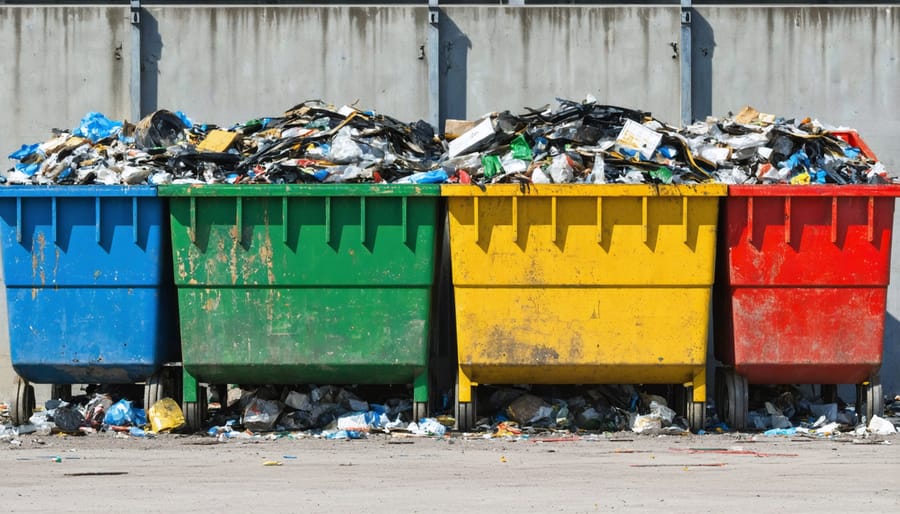
Energy Efficiency Measures
Implementing effective energy efficiency measures is crucial for achieving sustainability goals in construction projects. Modern buildings should incorporate advanced building automation systems (BAS) to optimize HVAC operations, lighting controls, and power distribution. High-performance building envelopes featuring superior insulation, low-E glazing, and air barrier systems significantly reduce energy consumption while maintaining occupant comfort.
Smart lighting solutions, including LED fixtures with daylight harvesting and occupancy sensors, can reduce electricity usage by up to 75% compared to traditional systems. Variable frequency drives (VFDs) for HVAC equipment and smart motors enable precise control of mechanical systems, optimizing energy consumption based on real-time demand.
Energy recovery ventilation (ERV) systems capture and reuse waste heat from exhaust air, while solar passive design principles maximize natural light and thermal regulation. Advanced metering infrastructure (AMI) enables continuous monitoring and analysis of energy usage patterns, allowing facility managers to identify optimization opportunities.
Integration of renewable energy systems, such as rooftop solar panels or geothermal heat pumps, can significantly offset grid electricity consumption. Combined with energy storage solutions, these systems provide reliable power while reducing peak demand charges and environmental impact.
Remember to consider lifecycle costs when selecting energy-efficient technologies, as initial investments often deliver substantial long-term savings through reduced operational expenses and improved building performance.
Water Conservation Strategies
Water conservation in construction projects requires a multi-faceted approach addressing both construction activities and long-term building operations. During construction, implementing a comprehensive water monitoring system helps track usage patterns and identify potential leaks or wastage points. Key strategies include using high-pressure cleaning equipment with water-efficient nozzles, installing temporary water meters, and implementing dust suppression methods that minimize water consumption.
For operational efficiency, specify water-efficient fixtures and equipment rated by WaterSense or similar certification programs. Low-flow faucets, dual-flush toilets, and sensor-operated systems can reduce water consumption by up to 30% compared to conventional fixtures. Incorporating rainwater harvesting systems and greywater recycling facilities provides sustainable water sources for non-potable applications like landscape irrigation and toilet flushing.
Smart irrigation systems with moisture sensors and weather-based controllers optimize landscape water usage. Native and drought-resistant plants require minimal irrigation once established, significantly reducing outdoor water consumption. Consider implementing condensate recovery systems from HVAC equipment to supplement water needs.
Regular maintenance schedules for plumbing systems prevent leaks and ensure optimal performance. Training construction workers and building occupants on water conservation practices is crucial for long-term success. Document water-saving strategies in the building operations manual and establish clear protocols for monitoring and maintaining water-efficient systems throughout the building’s lifecycle.
Digital Tools for Sustainability Management
BIM for Sustainable Design
BIM for sustainable design has revolutionized how construction teams approach environmental efficiency in building projects. This powerful digital tool enables teams to analyze and optimize sustainability factors throughout the project lifecycle, from initial concept to operational performance.
Through BIM’s integrated modeling capabilities, designers can simulate and evaluate multiple sustainability scenarios, including energy consumption patterns, daylighting analysis, and thermal performance. This data-driven approach allows for informed decision-making during the early design phases when sustainability choices have the most significant impact and are most cost-effective to implement.
Key advantages include the ability to perform detailed energy modeling, calculate carbon footprints, and assess material lifecycle impacts before construction begins. BIM also facilitates better coordination between mechanical, electrical, and plumbing systems, ensuring optimal performance and reduced energy waste. By identifying potential conflicts and inefficiencies early, teams can make adjustments that enhance both environmental performance and long-term operational costs.
The platform’s capability to track and document sustainable materials and systems throughout construction also supports green building certification processes, such as LEED and BREEAM.
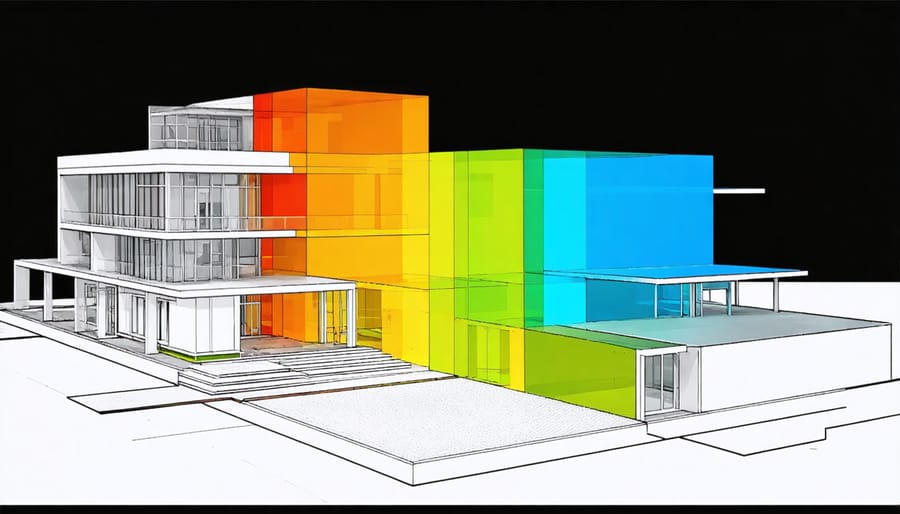
Sustainability Tracking Software
Modern sustainability tracking software has revolutionized how construction projects monitor and manage their environmental impact. Leading platforms like Green Building Studio, Tally, and One Click LCA enable real-time tracking of key sustainability metrics, including carbon emissions, energy consumption, and waste management data. These digital solutions integrate seamlessly with Building Information Modeling (BIM) systems, providing comprehensive environmental performance analysis throughout the project lifecycle.
Construction teams can leverage these tools to generate detailed sustainability reports, track LEED certification progress, and identify areas for improvement. Advanced features include material lifecycle assessment, energy modeling, and water usage optimization. Cloud-based platforms allow multiple stakeholders to access and update sustainability data simultaneously, enhancing collaboration and transparency.
The most effective software solutions offer customizable dashboards that display key performance indicators (KPIs) and automatically alert teams when sustainability targets are at risk. This proactive approach enables quick interventions and helps maintain compliance with environmental regulations. Many platforms also include benchmarking capabilities, allowing companies to compare their performance against industry standards and best practices.
Implementation Framework
Team Structure and Responsibilities
A successful construction sustainability plan requires a well-structured team with clearly defined roles and responsibilities to ensure effective sustainability implementation. The core team typically consists of a Sustainability Director or Manager who oversees the entire program and coordinates with various departments.
Working alongside the Sustainability Director, project managers integrate sustainable practices into construction workflows and timelines. They collaborate with sustainability coordinators who monitor compliance with green building standards and track performance metrics. Environmental specialists provide technical expertise on materials selection, waste management, and emissions reduction strategies.
The procurement team plays a crucial role in sourcing sustainable materials and managing relationships with eco-conscious suppliers. Site supervisors ensure that sustainability practices are properly executed on the ground, while quality control teams verify compliance with environmental standards and certification requirements.
To maximize effectiveness, establish clear communication channels between team members and create accountability frameworks. Regular cross-functional meetings help identify challenges and opportunities for improvement. Document specific responsibilities in role descriptions and include sustainability KPIs in performance evaluations.
Training coordinators should be appointed to ensure all team members understand their roles in achieving sustainability goals and are updated on the latest green building practices and technologies. This structured approach ensures comprehensive coverage of sustainability initiatives while maintaining operational efficiency.
Performance Metrics and Reporting
Effective performance monitoring and reporting are crucial elements of any construction sustainability plan. Key Performance Indicators (KPIs) should align with both project-specific goals and broader organizational sustainability objectives. Essential metrics typically include energy efficiency ratings, water consumption, waste diversion rates, and carbon emissions during construction.
To establish meaningful KPIs, organizations should follow the SMART framework: Specific, Measurable, Achievable, Relevant, and Time-bound. Common quantitative metrics include percentage reduction in energy use, volume of recycled materials used, and water conservation rates. Qualitative indicators might encompass supplier compliance with sustainability standards and community engagement levels.
Regular reporting intervals should be established, typically monthly for project-level metrics and quarterly for organizational sustainability goals. Modern construction management software can automate data collection and analysis, providing real-time insights through customizable dashboards. This technology enables prompt identification of areas requiring improvement and facilitates data-driven decision-making.
Documentation should include detailed environmental impact assessments, energy performance certificates, and waste management records. Third-party verification of sustainability metrics adds credibility to reporting and supports certification requirements for programs like LEED and BREEAM. Stakeholder communication should be transparent, featuring both achievements and areas for improvement in sustainability performance.
Annual sustainability reports should compile key metrics, highlight successful initiatives, and outline strategies for continued improvement. This comprehensive approach ensures accountability and demonstrates commitment to sustainable construction practices.
Implementing a robust construction sustainability plan requires a systematic approach and unwavering commitment from all stakeholders. Throughout this guide, we’ve explored the essential components of successful sustainable construction practices, from initial planning and material selection to waste management and energy efficiency measures.
The key to success lies in starting with a clear vision and measurable objectives, supported by detailed documentation and regular monitoring. Construction professionals must prioritize early stakeholder engagement, comprehensive risk assessment, and the integration of sustainable practices into every phase of the project lifecycle.
To begin implementing these measures, take these immediate steps:
1. Conduct a sustainability audit of current practices
2. Establish baseline measurements for energy use, waste, and resource consumption
3. Develop specific, time-bound sustainability goals
4. Create a detailed implementation timeline
5. Assign responsibility to key team members
6. Set up monitoring and reporting systems
Remember that sustainability in construction is not just an environmental imperative but a business opportunity. By embracing sustainable practices, organizations can reduce operational costs, enhance their competitive position, and contribute to a more resilient built environment.
Moving forward, stay informed about emerging technologies and evolving regulations while maintaining flexibility in your sustainability strategy. Success requires continuous improvement and adaptation to changing market conditions and environmental requirements.