Digital twin technology is revolutionizing the construction industry, enabling smarter, more efficient project management from conceptualization to completion. By creating virtual replicas of physical assets, processes, and systems, digital twins empower construction technology companies to optimize designs, simulate scenarios, monitor progress, and make data-driven decisions in real-time. This transformative approach harnesses the power of IoT sensors, BIM, and AI to streamline collaboration, minimize risks, and maximize value across the project lifecycle. As the industry embraces digital transformation, digital twins are emerging as a game-changer, paving the way for more sustainable, resilient, and profitable construction projects in the future.
What are Digital Twins?
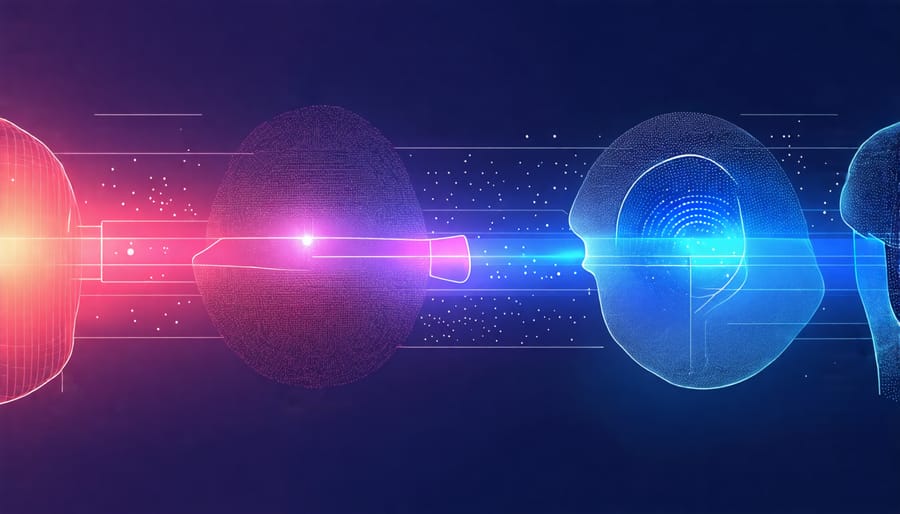
The Fusion of Physical and Digital Worlds
The integration of sensors and Internet of Things (IoT) devices in construction projects enables a seamless, bi-directional data flow between the physical and virtual worlds. Sensors embedded in buildings, equipment, and materials collect real-time data on various parameters such as temperature, humidity, stress, and movement. This data is transmitted to the digital twin, updating the virtual model with accurate, up-to-date information about the physical asset’s performance and condition. Conversely, changes made to the digital twin can be communicated back to the physical world through connected devices, allowing for remote monitoring, control, and optimization of construction processes. This fusion of physical and digital worlds through IoT technology enhances the accuracy and reliability of digital twins, enabling stakeholders to make informed decisions based on real-world data. By leveraging this bi-directional data flow, construction professionals can identify potential issues, optimize resource allocation, and improve overall project efficiency and quality.
Beyond BIM: The Evolution of Digital Twins
While BIM has revolutionized construction by providing a digital representation of buildings, digital twins take it a step further. Digital twins are dynamic, real-time replicas that integrate IoT data, AI, and machine learning to create a living, evolving model. Unlike static BIM models, digital twins continuously update based on real-world data, enabling more accurate simulations, predictive maintenance, and optimized decision-making. As Priya Sharma, VP of Digital Twin Solutions at Oracle, explains, “Digital twins provide a holistic view of assets, processes, and systems, allowing for real-time monitoring, analysis, and optimization.” This level of insight and adaptability sets digital twins apart from traditional BIM, making them a powerful tool for improving construction efficiency, reducing risks, and driving innovation throughout the project lifecycle. As the industry embraces digital transformation, the shift from BIM to digital twins represents a significant leap forward in how we design, build, and operate our built environment.
Transforming Construction with Digital Twins
Design and Planning Optimization
Digital twin technology revolutionizes design and planning in construction by enabling virtual simulations and optimizations. By creating accurate digital replicas of buildings and infrastructure, architects and engineers can explore various design options, identify potential issues, and optimize layouts for functionality, aesthetics, and sustainability. Digital twins facilitate collaborative design reviews, allowing stakeholders to provide feedback and make informed decisions early in the process.
Moreover, digital twins enable the simulation of construction sequences, helping project managers identify the most efficient and cost-effective approaches. By virtually testing different construction scenarios, teams can optimize resource allocation, minimize delays, and reduce waste. This proactive planning leads to streamlined workflows, improved coordination among trades, and enhanced overall project efficiency.
Real-world case studies demonstrate the tangible benefits of using digital twins for design and planning optimization. For example, the XYZ Construction Company leveraged digital twin technology to optimize the design of a high-rise building, resulting in a 15% reduction in construction time and a 10% decrease in material costs. By simulating various design alternatives and construction sequences, they identified the most efficient approach, minimizing rework and maximizing productivity.
As construction projects become increasingly complex, digital twin technology offers a powerful tool for design and planning optimization, enabling teams to make data-driven decisions and deliver projects with greater efficiency and precision.
Enhanced Collaboration and Coordination
Digital twin technology serves as a centralized repository for project data, enabling enhanced collaboration and coordination among project stakeholders. By providing a single source of truth, digital twins ensure that all parties have access to the same up-to-date information, reducing the risk of miscommunication and errors. This shared digital environment facilitates seamless data exchange and real-time updates, allowing architects, engineers, contractors, and clients to work together more efficiently. With the ability to visualize and interact with the digital twin, stakeholders can easily communicate design intent, identify potential issues, and make informed decisions collaboratively. Furthermore, the centralized nature of digital twin data fosters transparency and accountability, as all changes and updates are tracked and visible to the entire project team. This enhanced collaboration and coordination ultimately leads to improved project outcomes, reduced rework, and faster decision-making processes. By breaking down silos and promoting a collaborative approach, digital twin technology transforms the way construction professionals work together, resulting in more successful and efficient projects.
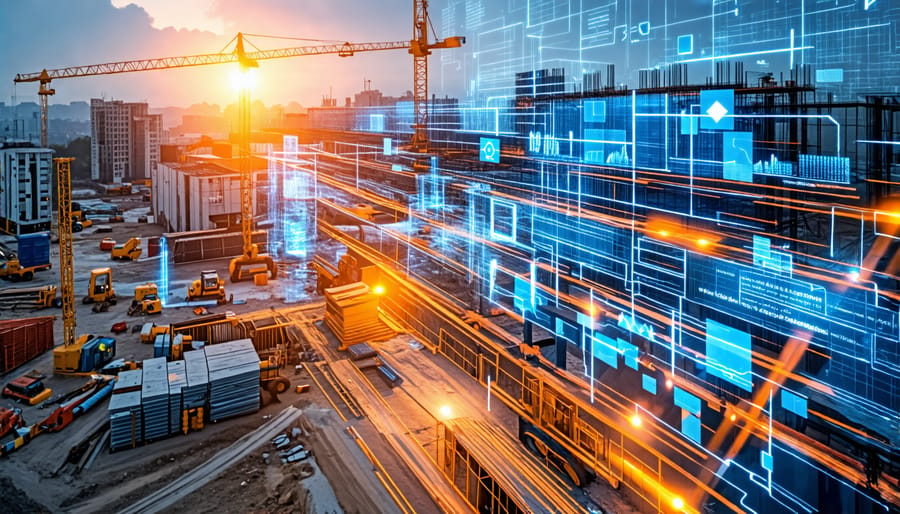
Real-Time Project Monitoring and Control
Digital twin technology enables real-time project monitoring and control by providing a virtual replica of the construction site. By integrating data from various sources, such as sensors, drones, and IoT devices, digital twins offer a comprehensive view of the project’s progress. This live data allows project managers to proactively identify potential issues, such as schedule delays or quality control concerns, and take corrective actions before they escalate. Real-time monitoring also facilitates better decision-making by providing stakeholders with up-to-date information on resource allocation, material procurement, and workforce management. Digital twins can automatically generate progress reports, highlighting areas that require attention and enabling more efficient communication among team members. By leveraging the power of real-time data, construction professionals can optimize project performance, minimize risks, and ensure timely delivery within budget constraints. The ability to monitor and control projects remotely through digital twins is particularly valuable in the face of unforeseen challenges, such as the COVID-19 pandemic, allowing for effective collaboration and oversight even when physical presence on-site is limited.
Predictive Maintenance and Operations
Digital twin technology extends its benefits beyond the construction phase, revolutionizing building operations and maintenance. By creating a virtual replica of the completed structure, digital twins enable predictive maintenance, allowing facility managers to anticipate and address potential issues before they escalate. Real-time data from sensors and IoT devices integrated into the building feed into the digital twin, providing insights into energy consumption, system performance, and occupant behavior. This data-driven approach optimizes building performance, reduces energy waste, and enhances occupant comfort. Facility managers can simulate various scenarios, such as equipment failures or extreme weather events, to develop proactive maintenance strategies and contingency plans. Furthermore, digital twins facilitate seamless collaboration between maintenance teams, enabling remote monitoring, troubleshooting, and guided repairs. As the building evolves over time, the digital twin is updated to reflect any modifications or renovations, ensuring an accurate and up-to-date virtual representation. This lifecycle approach to building management, powered by digital twins, results in reduced operational costs, improved energy efficiency, and extended building lifespan. As the construction industry embraces digital twin technology beyond the build phase, it unlocks new opportunities for sustainable, resilient, and intelligent buildings that deliver long-term value to owners and occupants alike.
Real-World Case Studies
Digital twin technology has been successfully implemented in several high-profile construction projects, demonstrating its potential to revolutionize the industry. One notable example is the new Istanbul Airport, which utilized digital twins to optimize design, construction, and operations. By creating a virtual replica of the entire airport complex, the project team was able to simulate various scenarios, identify potential issues, and make data-driven decisions. This led to improved efficiency, reduced costs, and enhanced safety throughout the construction process.
Another impressive case study is the Crossrail project in London, one of Europe’s largest infrastructure projects. The use of digital twins allowed for seamless collaboration among the various stakeholders, including designers, engineers, and contractors. The virtual model facilitated real-time monitoring of progress, early detection of clashes, and optimization of resource allocation. As a result, the project team was able to mitigate risks, minimize delays, and ensure the successful delivery of this complex underground railway system.
The Zhengzhou Greenland Plaza in China is yet another example of digital twin technology’s impact on construction. This 280-meter-tall skyscraper was built using a comprehensive digital twin that integrated BIM, IoT sensors, and real-time data analytics. The virtual model enabled the project team to optimize the building’s design for energy efficiency, simulate construction sequences, and monitor the structure’s performance throughout its lifecycle. The use of digital twins contributed to the project’s timely completion and its achievement of sustainability goals.
These real-world case studies showcase the transformative power of digital twin technology in the construction industry. By leveraging virtual replicas to inform decision-making, optimize processes, and enhance collaboration, construction professionals can deliver projects more efficiently, cost-effectively, and with greater precision. As more organizations adopt digital twins, the industry is poised to experience significant improvements in productivity, quality, and sustainability.
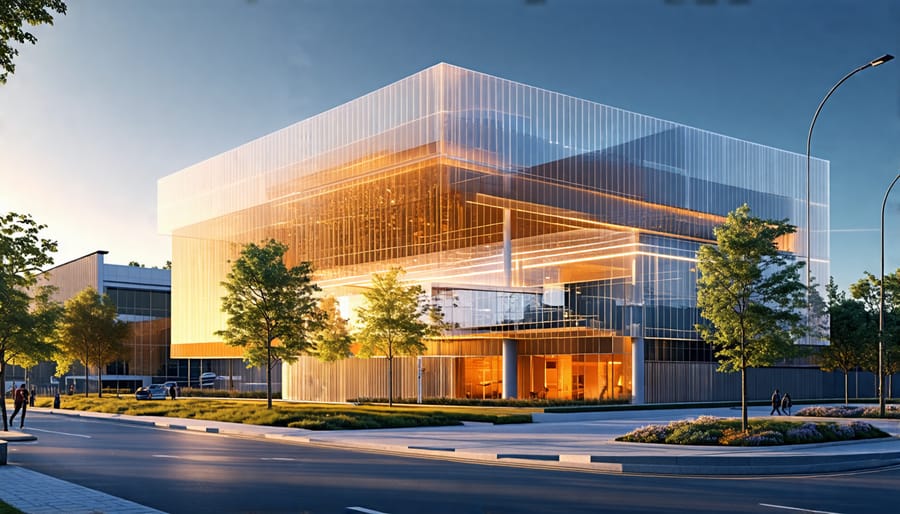
Overcoming Adoption Challenges
While digital twin technology offers significant benefits for the construction industry, adoption challenges must be addressed to ensure successful implementation. One of the primary barriers is the initial cost of investing in the necessary hardware, software, and skilled personnel. However, the long-term savings and efficiency gains often outweigh these upfront expenses, as demonstrated by case studies of companies that have successfully integrated digital twins into their workflows.
Technical complexity can also hinder adoption, as creating and maintaining accurate digital twins requires expertise in data collection, modeling, and analysis. To overcome this challenge, construction firms can partner with experienced technology providers or invest in training programs to build in-house capabilities. Change management is another crucial aspect, as implementing digital twins often requires a shift in organizational culture and processes. Effective communication, stakeholder engagement, and a clear vision of the benefits can help facilitate a smooth transition.
Despite these challenges, industry leaders are increasingly recognizing the value of digital twins and taking steps to embrace this transformative technology. By addressing cost concerns, technical hurdles, and change management issues head-on, construction companies can position themselves to reap the benefits of digital twins and stay competitive in an evolving industry landscape.
Conclusion
Digital twin technology is poised to revolutionize the construction industry in the coming years. As the technology continues to evolve and become more accessible, an increasing number of construction firms will adopt digital twins to optimize project planning, execution, and maintenance. By leveraging real-time data, advanced simulations, and predictive analytics, digital twins will enable construction professionals to make data-driven decisions, minimize risks, and improve overall project outcomes.
Key takeaways for industry professionals include the importance of embracing digital transformation, investing in the necessary infrastructure and talent to support digital twin implementation, and fostering a culture of innovation and collaboration. As the construction industry becomes more competitive and complex, those who successfully harness the power of digital twins will be well-positioned to deliver projects more efficiently, cost-effectively, and sustainably. By staying informed about the latest developments in digital twin technology and its applications, construction professionals can unlock new opportunities for growth and success in the years ahead.