The Q Model Quonset hut represents a groundbreaking convergence of innovative construction methods and sustainable architecture, delivering up to 40% cost savings compared to traditional building structures. This prefabricated steel design, engineered for maximum structural efficiency, combines rapid deployment capabilities with exceptional durability, withstanding wind loads up to 180 mph and snow loads exceeding 100 pounds per square foot. Industry professionals increasingly leverage these versatile structures across commercial, industrial, and agricultural applications, capitalizing on their modular design and streamlined financing options through specialized construction lenders. The Q Model’s standardized components and simplified assembly process reduce labor costs by 30-50% while maintaining compliance with international building codes, making it a compelling solution for forward-thinking developers and project managers seeking to optimize their construction portfolio’s ROI. Recent advancements in thermal insulation and customizable end-wall systems have positioned the Q Model as a premier choice for sustainable building projects, particularly in regions with extreme weather conditions or stringent environmental regulations.
Understanding the Q Model Quonset Innovation
Technical Specifications and Design Features
The Q Model Quonset hut features a distinctive semi-circular arch design constructed from corrugated galvanized steel panels, typically ranging from 20 to 40 feet in width and customizable lengths in 20-foot increments. The primary structural framework consists of interlocking steel ribs spaced at 4-foot intervals, providing optimal load distribution and structural integrity.
The foundation system employs reinforced concrete footings with embedded anchor bolts, designed to accommodate various soil conditions and wind loads. The standard roof pitch is 1:2, offering effective water drainage while maintaining maximum interior clearance. The corrugated panels, typically 22-gauge steel, are coated with zinc-aluminum alloy for enhanced corrosion resistance and durability.
Key architectural elements include end-wall configurations available in straight or sectional designs, with options for personnel doors, roll-up doors, and windows. The interior clear span ranges from 16 to 36 feet, creating unobstructed floor space ideal for various applications. Thermal performance is achieved through optional spray foam insulation (R-value up to R-30) and vapor barrier systems.
Advanced features include integrated ventilation systems, skylight panels for natural illumination, and modular expansion capabilities. The structure meets or exceeds building codes for snow loads up to 40 psf and wind speeds of 120 mph.
Environmental Performance Metrics
The Q Model Quonset hut demonstrates exceptional environmental performance metrics, particularly in energy efficiency and sustainable resource utilization. These structures achieve a remarkable thermal performance through their curved design, which naturally promotes air circulation and reduces heating and cooling requirements by up to 25% compared to traditional rectangular buildings.
The galvanized steel construction incorporates recycled materials, typically containing 25-30% post-consumer content, significantly reducing the structure’s carbon footprint. When properly insulated, Q Model Quonset huts can achieve R-values ranging from R-30 to R-40, exceeding standard building code requirements in most regions.
Solar heat gain is effectively managed through the archway design, while strategic placement of ventilation systems can reduce energy consumption for climate control by 15-20%. The prefabricated components result in minimal construction waste, with typically less than 5% material wastage during assembly.
Water management is another key strength, as the curved roof design naturally channels precipitation for efficient collection and potential reuse. The structure’s durability ensures a longer lifecycle, reducing the need for replacement materials and maintaining optimal performance for 50+ years with proper maintenance.
Additionally, the building’s design allows for easy integration of sustainable technologies, including solar panels, green roof systems, and rainwater harvesting equipment, further enhancing its environmental credentials.
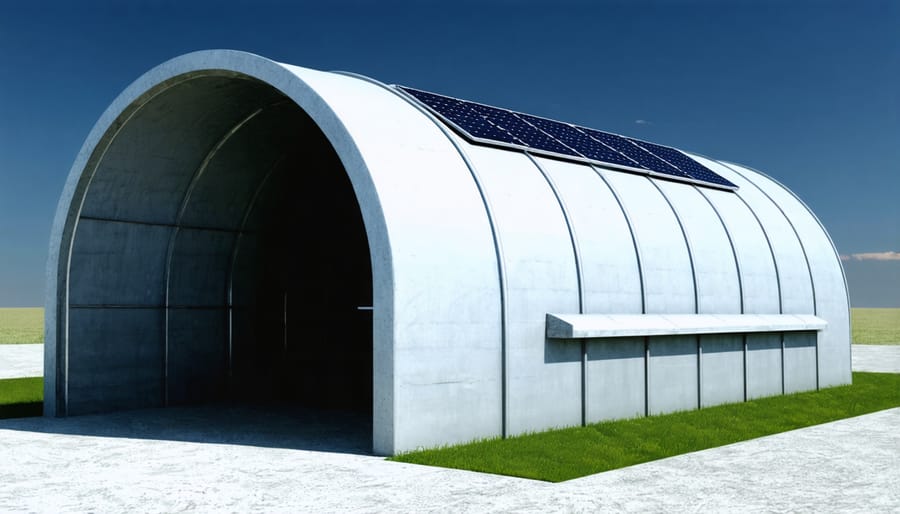
Innovative Financing Solutions
Green Building Incentives and Tax Benefits
Q model Quonset huts offer significant opportunities for sustainable construction incentives and tax benefits, particularly when integrated with modern green building practices. Projects implementing these structures can benefit from various federal, state, and local programs designed to encourage environmentally responsible construction.
The LEED certification program provides a framework for financing energy efficiency projects, with Quonset huts often qualifying for points in multiple categories including materials and resources, energy performance, and innovation in design. Buildings achieving LEED certification may be eligible for tax deductions of up to $1.80 per square foot through the Energy-Efficient Commercial Buildings Tax Deduction.
Many states offer additional incentives for sustainable Quonset hut construction, including property tax exemptions, expedited permitting, and density bonuses. The Environmental Protection Agency’s ENERGY STAR program provides certification opportunities that can lead to utility rebates and enhanced market value.
Key financial benefits include:
– Accelerated depreciation for energy-efficient building components
– Solar Investment Tax Credit (ITC) when incorporating renewable energy systems
– Local government grants for sustainable building practices
– Reduced insurance premiums through green building certification
Project developers should consult with qualified tax professionals and sustainability consultants to maximize available incentives while ensuring compliance with current regulations and certification requirements.
Alternative Financing Structures
In today’s dynamic construction market, Quonset hut projects benefit from several alternative funding options that make these versatile structures more accessible to businesses and organizations. Lease-to-own arrangements have emerged as a popular financing solution, allowing organizations to acquire Quonset huts with minimal upfront capital while building equity through monthly payments.
Performance contracting presents another innovative approach, particularly for energy-efficient Quonset installations. Under this model, energy savings from the building’s operation offset the initial construction costs, making it especially attractive for climate-controlled storage facilities and manufacturing spaces.
Equipment financing and vendor partnerships have also evolved to accommodate Quonset construction projects. Many manufacturers now offer direct financing programs with competitive terms, often including warranties and maintenance packages within the funding structure.
For public sector applications, public-private partnerships (P3s) provide a framework for sharing costs and risks between government entities and private developers. These arrangements typically incorporate long-term maintenance agreements and performance guarantees, ensuring sustainable operation throughout the structure’s lifecycle.
Agricultural cooperatives and business consortiums have developed shared-cost models, where multiple stakeholders pool resources to fund larger Quonset installations, reducing individual financial burden while maximizing facility utilization. These collaborative approaches often include predetermined buy-out options and clear governance structures for facility management.
ROI Analysis and Cost Comparisons
A comprehensive ROI analysis reveals that Q model Quonset huts typically deliver a return on investment within 3-5 years, significantly faster than traditional construction methods. Initial construction costs average $30-45 per square foot, approximately 40% lower than conventional building structures, while maintaining comparable durability and functionality.
Cost comparisons demonstrate substantial savings across multiple areas. Labor costs are reduced by 30-40% due to simplified assembly processes and shorter construction timelines. Material costs benefit from the standardized steel components, with bulk purchasing options further reducing expenses by 15-20%. Additionally, long-term maintenance costs average just $0.50-0.75 per square foot annually, compared to $1.50-2.00 for traditional buildings.
Energy efficiency calculations show Q model Quonset huts can reduce heating and cooling costs by up to 25% when properly insulated, contributing to operational savings. Insurance premiums are typically 15-20% lower due to the structure’s superior wind and snow load resistance.
For a 40′ x 60′ Q model Quonset hut, the total investment, including foundation and finishing, ranges from $72,000 to $108,000. This same footprint in traditional construction would cost $120,000-180,000. When factoring in reduced maintenance requirements and energy savings, the lifetime cost advantage becomes even more pronounced, with potential savings exceeding $100,000 over a 20-year period.
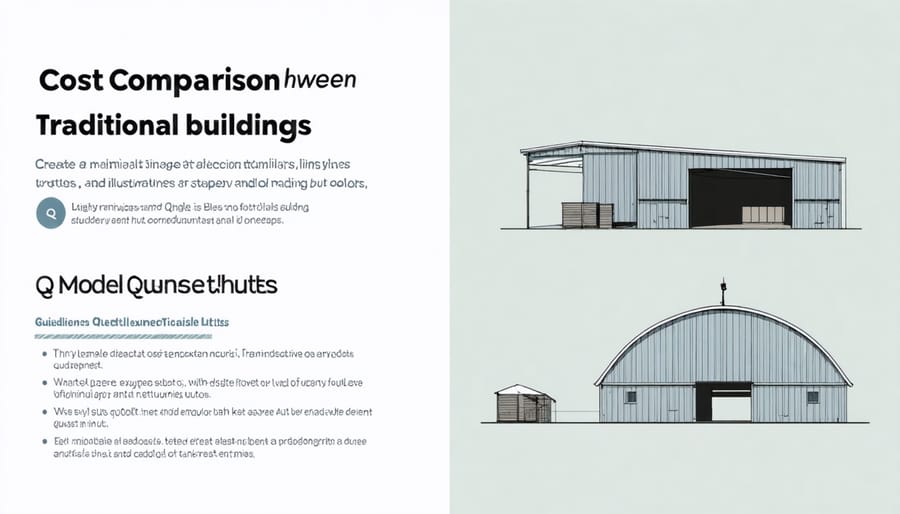
Implementation Case Studies
Commercial Applications
Q model Quonset huts have proven highly versatile in commercial applications, demonstrating significant return on investment across various business sectors. Manufacturing facilities particularly benefit from these structures, with their clear-span design allowing for unrestricted equipment placement and efficient workflow optimization. Several Fortune 500 companies have implemented Q model facilities as distribution centers, reducing construction timelines by up to 40% compared to traditional buildings.
In the agricultural sector, Q model structures serve as equipment storage, processing facilities, and climate-controlled storage units. Their superior moisture resistance and durability make them ideal for protecting valuable machinery and maintaining optimal conditions for agricultural products. Recent case studies show that agricultural businesses using Q model structures report maintenance cost reductions of approximately 30% over five years.
The retail sector has also embraced Q model Quonset huts, particularly in rural and expanding suburban areas. These structures can be rapidly deployed as pop-up stores, showrooms, and warehouse retail spaces. Their distinctive architectural profile often becomes a recognizable brand element, while their energy efficiency contributes to reduced operational costs.
Industrial parks and business complexes increasingly incorporate Q model structures for their adaptability and cost-effectiveness. The modular nature of these buildings allows for easy expansion as businesses grow, while their steel construction meets stringent commercial building codes. Companies report average energy savings of 25% compared to conventional commercial buildings, primarily due to superior insulation options and natural ventilation capabilities.
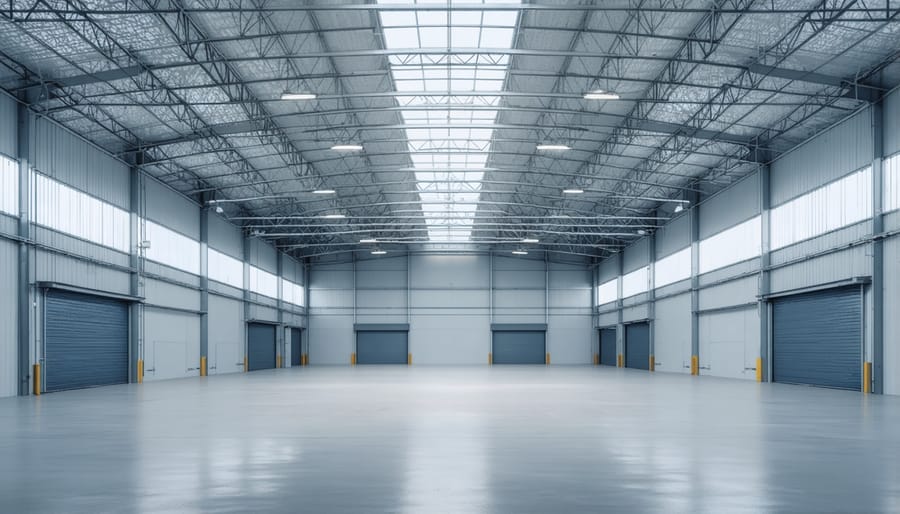
Industrial Solutions
Q model Quonset huts have proven exceptionally valuable across various industrial applications, demonstrating remarkable versatility and cost-effectiveness. Manufacturing facilities particularly benefit from these structures’ column-free interior spaces, which optimize workflow efficiency and accommodate large equipment installations. The standardized design allows for rapid deployment, with typical assembly times ranging from 2-4 weeks depending on size specifications.
Recent case studies highlight successful implementations in warehousing operations, where companies report up to 40% reduction in construction costs compared to traditional building methods. The structures’ durability against harsh industrial conditions, including chemical exposure and heavy machinery vibrations, makes them ideal for manufacturing environments. Their superior load-bearing capacity supports overhead crane systems up to 20 tons, essential for modern production facilities.
The aerospace industry has embraced Q model Quonset huts for aircraft maintenance facilities, utilizing their high ceiling clearance and wide spans. Agricultural processing plants benefit from the buildings’ natural ventilation properties and ability to maintain consistent internal temperatures, reducing HVAC costs by approximately 25%.
Industrial clients consistently report significant advantages in maintenance requirements, with the galvanized steel construction requiring minimal upkeep over decades of service. The structures’ modular nature allows for future expansion without disrupting existing operations, providing valuable flexibility for growing businesses. Energy efficiency studies demonstrate that proper insulation installation in Q model Quonset huts can result in 30-35% lower energy consumption compared to conventional industrial buildings, contributing to both environmental sustainability and operational cost reduction.
Future Outlook and Recommendations
The Q Model Quonset hut market is projected to experience significant growth over the next decade, driven by increasing demand for sustainable, cost-effective building solutions. Market analysis indicates a compound annual growth rate of 5.7% through 2030, with particular expansion in agricultural, industrial, and emergency response sectors.
Several emerging trends are shaping the future of Q Model Quonset construction. Advanced manufacturing techniques, including automated welding and precision cutting, are improving production efficiency while maintaining structural integrity. Integration of smart building technologies and IoT sensors is enabling better facility management and helping to mitigate construction risks.
For optimal implementation, we recommend:
1. Conducting thorough site analysis and soil testing before construction
2. Investing in high-quality galvanized steel with appropriate coating systems
3. Incorporating energy-efficient insulation and ventilation systems
4. Planning for future expansion possibilities during initial design
5. Implementing regular maintenance protocols to extend structure lifespan
The adaptation of Building Information Modeling (BIM) technology is revolutionizing Q Model Quonset planning and construction. This digital transformation enables better collaboration between stakeholders and more precise cost estimation.
Sustainability considerations will continue to drive innovation in Q Model Quonset design. We’re seeing increased integration of solar panels, rainwater harvesting systems, and eco-friendly materials. These adaptations not only reduce environmental impact but also offer significant operational cost savings over time.
Investment in prefabrication facilities and streamlined supply chains will likely reduce construction timelines and costs further. As municipalities update building codes to accommodate modern Quonset designs, we anticipate greater adoption in urban and suburban settings, particularly for commercial and light industrial applications.
Organizations considering Q Model Quonset implementation should focus on long-term value rather than initial costs, as these structures consistently demonstrate superior return on investment through reduced maintenance requirements and operational efficiency.
The Q Model Quonset hut represents a significant advancement in sustainable construction, combining time-tested durability with modern efficiency. As demonstrated throughout this analysis, these structures offer exceptional value through their cost-effective construction, minimal maintenance requirements, and adaptability to various commercial and industrial applications. Industry professionals should carefully consider the Q Model’s potential to reduce project timelines and operational costs while meeting sustainability goals. We encourage architects, engineers, and project managers to explore the financing options presented and conduct thorough site-specific assessments. By embracing these innovative structures, the construction industry can move forward with solutions that balance economic viability with environmental responsibility. Take the next step by consulting with qualified manufacturers and financial advisors to determine how the Q Model Quonset hut can benefit your next project.