Transforming traditional supply chains through blockchain technology in construction has become imperative for modern enterprises seeking enhanced transparency, security, and efficiency. By implementing distributed ledger solutions, organizations can now track materials from source to site with unprecedented accuracy, reduce documentation errors by up to 90%, and eliminate costly verification delays. Smart contracts automatically execute predefined agreements, ensuring timely payments and maintaining compliance across complex international supply networks. Leading construction firms leveraging blockchain have reported a 35% reduction in supply chain disputes and achieved real-time visibility into material authenticity, reducing counterfeit products by 70%. This digital transformation enables project managers to maintain immutable records of every transaction, automate procurement processes, and create transparent audit trails that satisfy increasingly stringent regulatory requirements. As the industry evolves beyond traditional paper-based systems, blockchain integration represents not just an technological upgrade but a fundamental shift in how construction supply chains operate, collaborate, and deliver value.
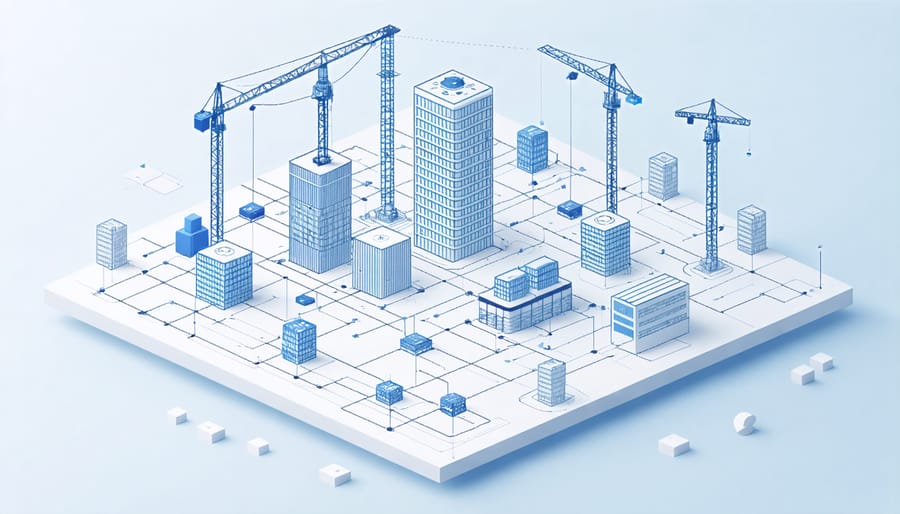
Smart Contracts Revolutionizing Material Procurement
Automated Payment Systems
Automated payment systems powered by blockchain technology are transforming traditional digital procurement processes in construction supply chains. These systems utilize smart contracts to automatically trigger payments when predefined conditions are met, such as delivery confirmation or quality verification milestones. This automation significantly reduces payment delays and administrative overhead while ensuring transparent transactions between contractors, suppliers, and subcontractors.
The verification process operates through a distributed ledger system where multiple parties can validate delivery receipts, inspection reports, and compliance documentation in real-time. When materials arrive on-site, IoT sensors and RFID tags can automatically record the delivery, while quality control personnel can digitally verify specifications. Once these conditions are met, the smart contract automatically executes the payment, eliminating the need for manual processing and reducing the risk of payment disputes.
Implementation of these systems has shown remarkable results in large-scale construction projects. For example, a recent high-rise development in Singapore reported a 60% reduction in payment processing time and a 40% decrease in payment-related disputes after implementing blockchain-based automated payments. The system’s ability to maintain an immutable record of all transactions and verifications has proven particularly valuable for regulatory compliance and audit purposes, providing stakeholders with unprecedented visibility into the payment flow throughout the supply chain.
Supplier Verification and Compliance
Blockchain technology revolutionizes supplier verification and compliance processes in construction supply chains through automated, tamper-proof credentialing systems. By implementing smart contracts, construction firms can establish transparent verification protocols that automatically validate supplier credentials, certifications, and compliance documentation in real-time.
Leading contractors are utilizing blockchain platforms to create immutable records of supplier qualifications, including safety certifications, insurance coverage, and regulatory compliance. These digital credentials are stored on the distributed ledger, allowing instant verification and reducing the administrative burden of manual checks. For example, major construction firms report up to 70% reduction in supplier verification time when using blockchain-based systems.
The technology enables automated compliance monitoring through predefined smart contract parameters. When suppliers upload documentation to the blockchain, the system automatically checks against required standards and regulations. Any non-compliance issues trigger immediate notifications to relevant stakeholders, enabling swift corrective action.
Real-world implementations demonstrate significant benefits in risk management and quality control. Construction companies can track supplier performance metrics, maintenance records, and material certifications throughout the project lifecycle. This comprehensive approach ensures continuous compliance monitoring while creating an auditable trail of supplier interactions and documentation.
The integration of IoT sensors with blockchain further enhances compliance verification by automatically recording and validating environmental conditions, material properties, and quality parameters during transportation and storage.
Real-Time Material Tracking and Authentication
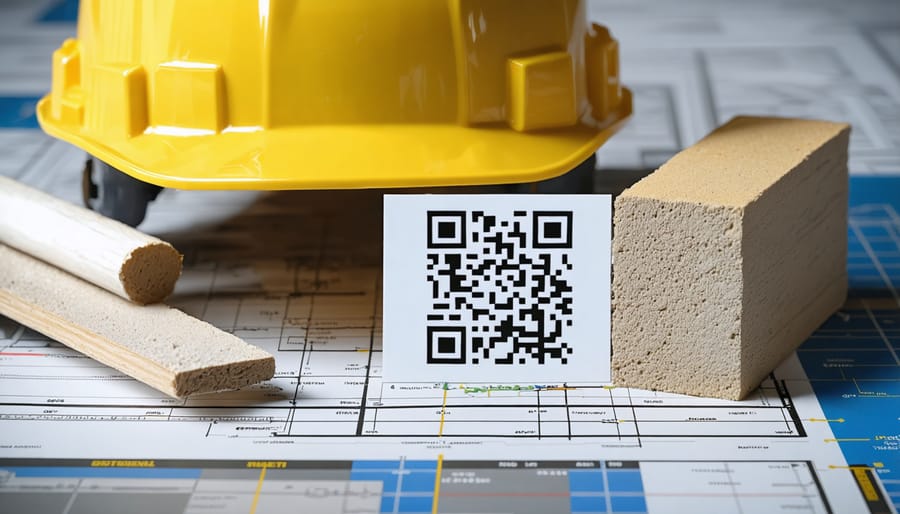
Quality Assurance Through Immutable Records
In the construction industry, material quality and authenticity are paramount to project success and safety. Blockchain technology introduces an unprecedented level of transparency and accountability through immutable digital records that track materials from source to installation. Each transaction and quality inspection is permanently recorded on the blockchain, creating an unalterable chain of custody that validates material authenticity and compliance with specifications.
For instance, when structural steel arrives at a construction site, its entire journey—from the mill’s manufacturing process to transportation and handling—is documented through blockchain entries. These entries include crucial quality certifications, test results, and handling conditions. Project managers can instantly verify that the steel meets required strength ratings and hasn’t been compromised during transit.
Quality assurance professionals benefit from real-time access to material testing data, manufacturer certifications, and environmental exposure records. This digital trail eliminates the risk of fraudulent documentation and enables swift verification of material properties. In concrete applications, for example, blockchain records can prove that specific mix designs were followed and optimal curing conditions were maintained.
The system also facilitates rapid response to quality issues. If defects are discovered, project teams can quickly trace affected materials to their source and identify other potentially compromised installations. This capability has proven particularly valuable in large-scale projects where materials from multiple suppliers are used simultaneously.
Leading construction firms report up to 45% reduction in quality-related disputes since implementing blockchain-based material tracking. The technology’s ability to maintain tamper-proof records has become especially crucial for projects requiring strict regulatory compliance or third-party certification.
Supply Chain Visibility and Transparency
In the evolving construction landscape, blockchain technology enables unprecedented supply chain visibility by creating an immutable digital ledger of all material movements and transactions. This transparency extends from raw material sourcing through final installation, providing stakeholders with crucial insights into their supply chain operations.
Construction firms implementing blockchain-based systems can achieve real-time inventory tracking while maintaining secure, verifiable records of material origins, quality certifications, and chain of custody. This enhanced visibility helps identify potential bottlenecks, reduce material waste, and ensure compliance with specifications and regulations.
Key benefits include the ability to track specialized materials from manufacture to installation, verify sustainable sourcing claims, and maintain detailed provenance records for quality assurance. For example, structural steel components can be tracked from the mill through fabrication and delivery, with each step documented and verified through smart contracts.
The system also enables better coordination between suppliers, contractors, and site teams by providing a single source of truth for material status and location. This reduces delays caused by miscommunication or missing documentation while improving forecasting accuracy and inventory management.
Construction companies implementing blockchain-based supply chain visibility solutions report significant improvements in material handling efficiency, with some achieving up to 30% reduction in storage costs and 25% decrease in material waste. The technology also supports better risk management by providing early warning of potential supply chain disruptions and enabling faster response to material quality issues.

Case Study: Major Construction Projects Using Blockchain
Several groundbreaking construction projects have successfully implemented blockchain technology to enhance supply chain management and project delivery. One notable example is the $500 million Atlantis Dubai extension project, where blockchain integration streamlined material tracking and vendor payments across 200+ suppliers. The project achieved a 30% reduction in procurement delays and eliminated nearly all payment disputes through smart contracts.
The Hong Kong-Zhuhai-Macau Bridge project demonstrates how blockchain can manage complex, multi-jurisdictional supply chains. Implementing a distributed ledger system allowed real-time tracking of over 400,000 prefabricated components, ensuring quality control and regulatory compliance across three different administrative regions. The system integrated with other digital construction tools to create a comprehensive project management platform.
In Northern Europe, the Stockholm Bypass Project utilized blockchain to manage environmental compliance and material sourcing. The system tracked the origin and transportation of 19 million tons of excavated materials, ensuring proper disposal and recycling. This implementation reduced documentation time by 75% and improved regulatory reporting accuracy to 99.9%.
Skanska’s pilot program in the United States showcases blockchain’s potential for equipment management and maintenance tracking. The company deployed a blockchain-based system across multiple sites to monitor heavy equipment usage, maintenance schedules, and parts procurement. This resulted in a 45% reduction in equipment downtime and a 25% decrease in maintenance costs.
The Dubai Future Foundation’s Office of the Future project represents another successful implementation, where blockchain technology managed the entire supply chain for 3D-printed building components. The system verified material specifications, tracked printing progress, and automated payments to suppliers, reducing the project timeline by 50% compared to traditional methods.
These case studies demonstrate blockchain’s tangible benefits in construction supply chain management, including enhanced transparency, reduced disputes, improved compliance tracking, and significant cost savings. The success of these projects has established valuable implementation frameworks for future construction initiatives.
Implementation Challenges and Solutions
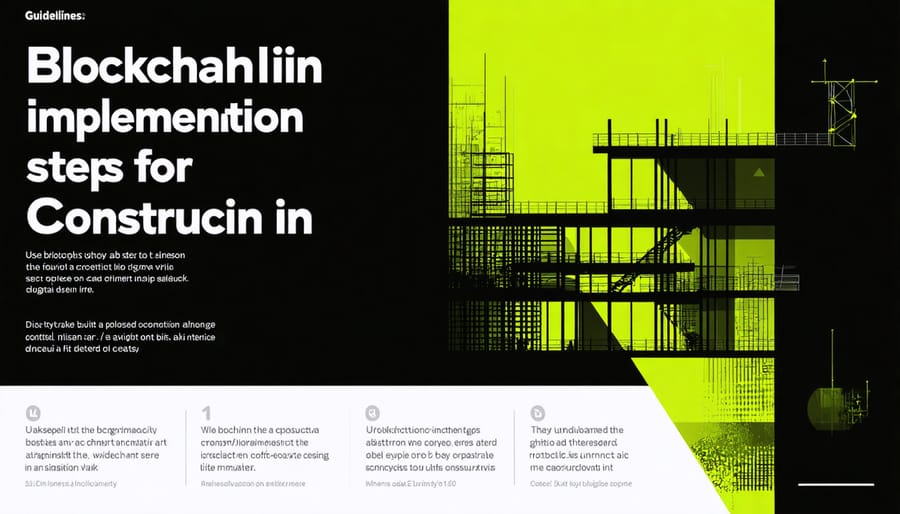
Technical Integration Considerations
Implementing blockchain in construction supply chains requires careful consideration of several technical aspects. Integration with existing Enterprise Resource Planning (ERP) systems and legacy software platforms demands robust API development and standardized data protocols. Construction firms must establish secure node networks that can handle distributed ledger transactions while maintaining data integrity across multiple stakeholders.
Key technical requirements include scalable blockchain architecture capable of processing high transaction volumes, particularly during peak construction phases. Smart contract deployment necessitates thorough testing and validation to ensure automated execution of contract terms and payment conditions. Systems must also incorporate proper authentication mechanisms and role-based access controls to manage various participant permissions.
Common integration challenges include data standardization across different suppliers and contractors, ensuring interoperability between various blockchain platforms, and maintaining system performance under heavy transaction loads. Organizations must also address connectivity issues at remote construction sites and implement reliable backup systems. Success requires a phased implementation approach, starting with pilot projects before expanding to full-scale deployment, supported by comprehensive training programs for technical staff and end-users.
Stakeholder Adoption Strategies
Successful implementation of blockchain in construction supply chains requires strategic stakeholder engagement and systematic adoption planning. Key stakeholders, including contractors, suppliers, and project owners, need clear demonstrations of ROI and operational benefits to embrace the technology. Industry leaders have found success by implementing pilot programs that showcase tangible improvements in material tracking and payment processing.
To facilitate adoption, organizations should establish comprehensive training programs and provide technical support during the transition period. Creating a phased implementation approach allows stakeholders to gradually adapt to new processes while maintaining existing operations. Regular feedback sessions and performance metrics help identify challenges early and adjust strategies accordingly.
Cross-organizational collaboration is essential, particularly when integrating multiple stakeholders into a single blockchain network. Successful adoption strategies often include establishing governance frameworks, standardizing data formats, and creating clear protocols for information sharing. Industry consortiums and partnerships have proven effective in developing shared standards and best practices, reducing individual implementation costs while maximizing network benefits.
Consider incentivizing early adopters through reduced transaction fees or preferential contract terms to build initial momentum and demonstrate system viability to hesitant stakeholders.
Future Outlook and Industry Impact
The construction industry stands at a pivotal moment as blockchain technology continues to mature and evolve. Industry experts project that by 2025, over 60% of major construction enterprises will incorporate blockchain into their supply chain operations, integrating with existing procurement automation solutions to create more robust systems.
Several transformative trends are emerging that will reshape supply chain management in construction. Smart contracts are expected to become increasingly sophisticated, incorporating artificial intelligence to automatically adjust material orders based on real-time project progress and weather conditions. This advancement could reduce material waste by up to 25% and improve project timeline accuracy by 30%.
The integration of IoT devices with blockchain networks will enable unprecedented levels of material tracking and quality assurance. Sensors embedded in construction materials will continuously feed data into blockchain networks, creating immutable records of transportation conditions, storage environments, and installation parameters. This development will particularly benefit prefabrication and modular construction sectors, where quality control throughout the supply chain is crucial.
Sustainability tracking will become more transparent and verifiable through blockchain implementation. Construction firms will be able to prove their environmental compliance and material sourcing credentials with unalterable documentation, meeting increasingly stringent regulatory requirements and client demands for sustainable construction practices.
Industry experts anticipate that blockchain will facilitate the emergence of new collaborative business models. Decentralized construction networks could enable smaller contractors to compete more effectively for large projects by forming verified, blockchain-based consortiums. These networks will streamline resource sharing and create more resilient supply chains.
The technology’s impact on risk management will be substantial. Real-time visibility into supply chain operations will enable proactive risk mitigation, potentially reducing supply-related delays by 40% and insurance costs by 20-30%. This improvement in risk management could lead to more competitive project bidding and better project outcomes.
While challenges remain, particularly in standardization and industry-wide adoption, the trajectory is clear: blockchain technology will become an integral part of construction supply chain management, driving efficiency, transparency, and innovation across the sector.
Blockchain technology represents a transformative solution for construction supply chain management, offering unprecedented transparency, security, and efficiency. The key benefits demonstrated through various use cases include reduced documentation errors, enhanced material traceability, streamlined payment processes, and improved stakeholder collaboration. Companies implementing blockchain solutions have reported up to 30% reduction in administrative costs and significant improvements in project delivery times.
To successfully implement blockchain in construction supply chains, organizations should follow a structured approach. Begin with a thorough assessment of current supply chain processes and identification of pain points. Select appropriate blockchain platforms that align with specific organizational needs and ensure compatibility with existing systems. Start with pilot projects in contained environments before scaling to larger operations.
Critical success factors include securing stakeholder buy-in, providing comprehensive training programs, and establishing clear governance structures. Investment in proper infrastructure and technology partners is essential, as is the development of standardized protocols for data sharing and smart contract execution.
Looking ahead, the construction industry stands to benefit significantly from wider blockchain adoption. Organizations that take early steps toward implementation will gain competitive advantages in efficiency, transparency, and risk management. The technology’s potential to revolutionize supply chain management makes it a crucial consideration for construction companies aiming to modernize their operations and maintain market leadership.
For optimal results, companies should focus on building cross-functional teams, establishing clear metrics for success, and maintaining flexibility in their implementation approach. This strategic investment in blockchain technology will position construction firms for success in an increasingly digital and interconnected industry landscape.