Digital twinning is revolutionizing construction project delivery by creating virtual replicas that mirror physical assets in real-time, enabling unprecedented levels of oversight and optimization. Industry leaders leveraging this technology report up to 25% reduction in construction delays and 20% improvement in project efficiency through enhanced visualization, predictive maintenance, and data-driven decision-making.
The integration of digital twins in construction represents a paradigm shift from traditional project management to dynamic, data-centric operations. By combining IoT sensors, AI analytics, and 3D modeling, construction firms can now simulate scenarios, detect potential issues before they occur, and optimize resource allocation across complex project portfolios. This technology bridges the gap between design intent and as-built reality, providing stakeholders with a single source of truth throughout the project lifecycle.
Leading construction firms such as Skanska and Balfour Beatty have demonstrated how digital twins can transform project delivery, from initial design validation to ongoing facility management. The technology’s ability to integrate with Building Information Modeling (BIM), real-time monitoring systems, and project management platforms creates a comprehensive ecosystem that enhances collaboration, reduces risk, and drives operational excellence in modern construction projects.
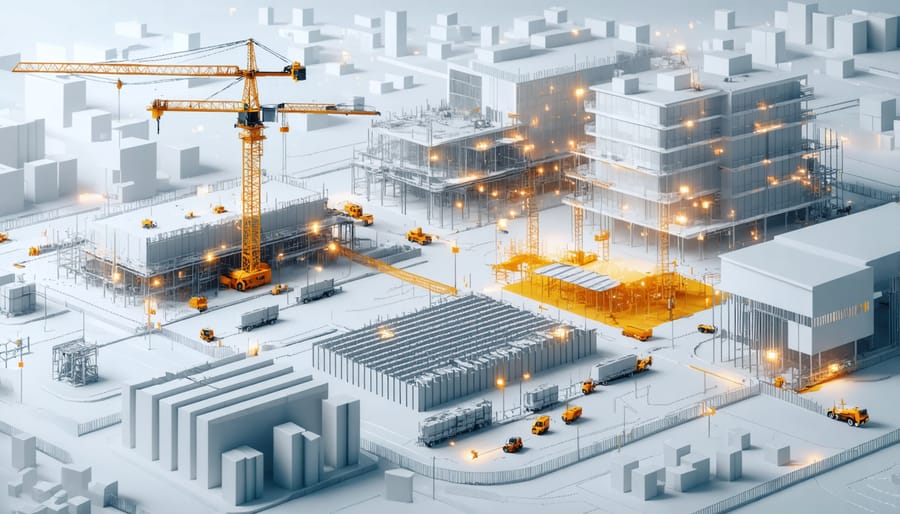
Real-Time Supply Chain Visibility Through Digital Twins
Dynamic Material Tracking and Inventory Management
Digital twin technology revolutionizes construction material tracking and inventory management by creating a real-time virtual replica of physical assets and resources. Through the integration of smart IoT devices, RFID tags, and sensors, project managers can monitor material locations, quantities, and conditions with unprecedented accuracy.
This system enables automatic updates of inventory levels as materials move through the supply chain, eliminating manual counting errors and reducing theft. Project teams receive instant notifications when stock levels fall below predetermined thresholds, ensuring timely reordering and preventing costly delays.
The digital twin also provides valuable insights into material usage patterns and waste reduction opportunities. By analyzing historical data and real-time consumption rates, the system can optimize order quantities and delivery schedules. This predictive capability helps construction firms maintain optimal inventory levels while reducing storage costs and minimizing material spoilage.
Furthermore, the technology enables better coordination between multiple project sites, allowing for efficient resource sharing and reduced overall procurement costs. Weather data integration helps protect sensitive materials by triggering protective measures when adverse conditions are forecast.
Predictive Analytics and Risk Management
Digital twins are revolutionizing supply chain risk management through advanced predictive analytics in construction. By creating virtual replicas of physical supply chains, organizations can simulate various scenarios and identify potential bottlenecks before they occur. This capability enables project managers to optimize material flow, reduce waste, and maintain better control over inventory levels.
The system continuously analyzes real-time data from multiple sources, including supplier performance metrics, logistics tracking, and market conditions. This integration allows for early warning detection of potential disruptions and automated recommendations for mitigation strategies. For instance, if weather conditions threaten to delay material delivery, the digital twin can instantly calculate the impact on project timelines and suggest alternative suppliers or routing options.
Construction firms implementing digital twin technology for supply chain management report up to 30% reduction in procurement costs and 25% improvement in delivery reliability. The technology’s ability to forecast demand patterns and optimize inventory levels has proven particularly valuable in large-scale projects where supply chain complexity can significantly impact project success.
Implementation Strategies for Construction Companies
Technology Infrastructure Requirements
Implementing digital twin technology requires a robust technological foundation comprising both hardware and software components. At its core, the system needs high-performance computers and servers capable of processing large volumes of data and running complex simulations. These must be complemented by various digital construction tools and data collection devices.
Essential hardware components include IoT sensors, scanners, and cameras for real-time data capture. LiDAR sensors and 3D scanners are crucial for creating accurate geometric representations, while environmental sensors monitor conditions such as temperature, humidity, and structural stress. Robust network infrastructure, including high-speed internet connectivity and secure local networks, is vital for seamless data transmission.
On the software side, the infrastructure requires several integrated systems: Building Information Modeling (BIM) software serves as the foundation, while specialized digital twin platforms manage the real-time data integration. Cloud computing services are essential for data storage and processing, enabling remote access and collaboration. Advanced analytics tools, powered by artificial intelligence and machine learning algorithms, process the collected data to generate actionable insights.
Cybersecurity measures must be implemented to protect sensitive project data, including encryption protocols and access control systems. Additionally, middleware solutions are necessary to ensure smooth communication between different software components and data sources.
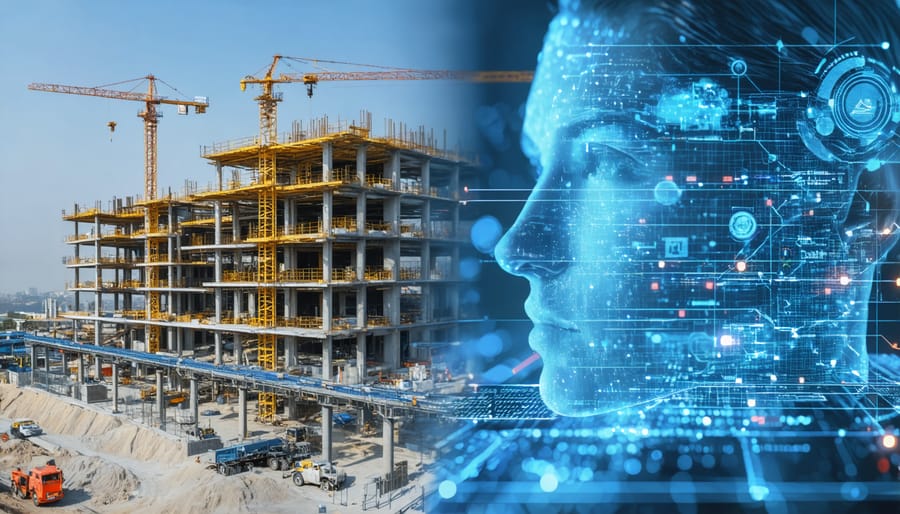
Integration with Existing Systems
Integrating digital twins with existing construction management systems requires a strategic approach and careful planning. The process typically begins with a comprehensive audit of current systems, including project management software, Building Information Modeling (BIM) platforms, and enterprise resource planning (ERP) solutions.
The first step involves establishing data integration protocols that enable seamless communication between the digital twin platform and existing software. This often requires implementing standardized APIs and data exchange formats, such as IFC (Industry Foundation Classes) or COBie (Construction Operations Building Information Exchange).
Modern digital twin platforms are increasingly compatible with blockchain in construction supply chains, creating a secure and transparent environment for data exchange. This integration ensures data integrity and real-time synchronization across all systems.
Key integration considerations include:
– Establishing clear data hierarchies and relationships
– Implementing robust security protocols
– Creating automated workflows for data synchronization
– Training staff on integrated system operations
– Developing fallback procedures for system maintenance
Success in integration often depends on choosing digital twin solutions that offer flexible connectivity options and support industry-standard protocols. Organizations should consider phased implementation approaches, starting with critical systems and gradually expanding to encompass the entire technology ecosystem.
Case Study: Digital Twin Success in Major Construction Project
The Dubai Creek Tower project serves as a compelling example of digital twin technology’s transformative impact on construction supply chain management. In 2021, the project team implemented a comprehensive digital twin solution to manage the complex supply chain of this $1 billion development, resulting in a 23% reduction in material waste and a 31% improvement in delivery scheduling accuracy.
The digital twin implementation began with creating a detailed virtual replica of the entire construction site, including real-time monitoring of material flows, equipment locations, and workforce deployment. Key sensors were installed throughout the supply chain network, collecting data on everything from concrete mixing temperatures to steel component locations.
Project managers utilized this virtual environment to simulate various supply chain scenarios before execution. For instance, when faced with a potential delay in structural steel deliveries, the team used the digital twin to model alternative routing options and adjust the construction sequence, preventing a projected three-week delay.
The system’s predictive analytics capabilities proved particularly valuable during the foundation phase. By analyzing historical data and current conditions, the digital twin accurately forecast concrete curing times and optimal delivery schedules, reducing idle time for concrete pumps by 42%.
Integration with supplier systems allowed for unprecedented visibility across the supply chain. Real-time tracking of 14,000 unique components from 27 different suppliers enabled just-in-time delivery coordination, reducing on-site storage requirements by 35% and associated costs by $2.8 million.
Most notably, the digital twin’s impact on quality control was significant. The system’s ability to monitor material conditions during transport and storage led to a 67% reduction in material rejection rates. When deviations from specifications were detected, automatic alerts triggered corrective actions before materials reached the site.
This case study demonstrates how digital twin technology can optimize construction supply chains through improved visibility, predictive capabilities, and real-time decision-making support. The project’s success has since influenced industry standards for large-scale construction supply chain management.
ROI and Business Benefits
The implementation of digital twins in construction projects delivers substantial returns on investment through multiple channels. Studies indicate that construction companies utilizing digital twin technology typically experience a 15-20% reduction in overall project costs and a 20-25% improvement in project delivery timelines.
Cost savings materialize through enhanced clash detection, reduced rework, and optimized resource allocation. For instance, a major commercial development project in Singapore reported $5 million in savings through early issue detection using digital twin technology, representing a 12x return on their initial technology investment.
Operational benefits extend beyond direct cost savings. Projects implementing digital twins demonstrate improved safety metrics, with incident rates declining by up to 30%. The technology enables better decision-making through real-time data analysis, resulting in more efficient construction sequencing and resource utilization.
Long-term benefits include reduced maintenance costs throughout the building lifecycle, with facility management expenses decreasing by 10-15% annually. Digital twins also enhance asset value by providing comprehensive building performance data and predictive maintenance capabilities.
From a business perspective, organizations leveraging digital twins report increased competitive advantage through improved client satisfaction and enhanced collaboration capabilities. The technology enables more accurate project timelines, better stakeholder communication, and improved risk management, leading to higher profit margins and stronger market positioning.
Case studies consistently show that while initial investment in digital twin technology may be significant, the ROI typically materializes within 12-18 months of implementation, making it a compelling business case for construction organizations focused on long-term growth and operational excellence.
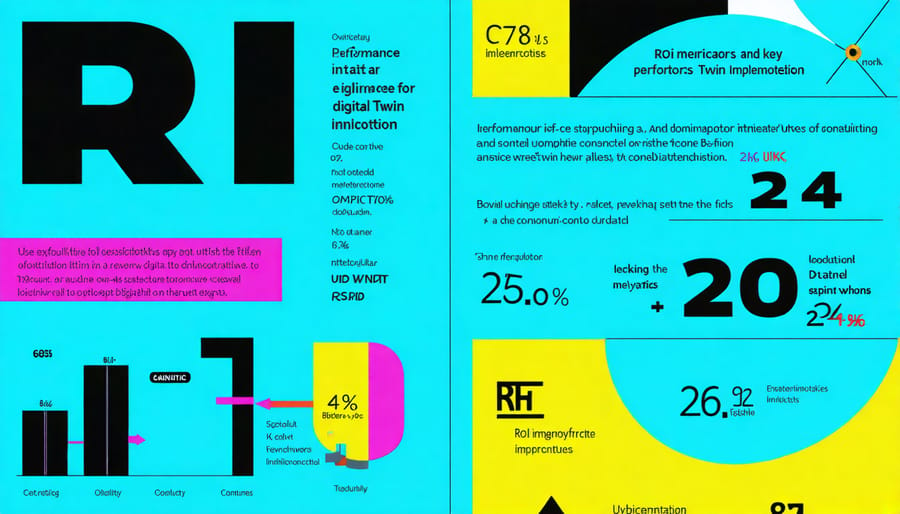
Digital twinning is revolutionizing the construction industry by bridging the gap between physical and digital realms. As demonstrated throughout this analysis, the technology offers unprecedented opportunities for optimization, risk reduction, and enhanced project delivery. The integration of IoT sensors, real-time data analytics, and AI-driven insights enables construction professionals to make informed decisions, predict potential issues, and maintain assets more effectively.
Looking ahead, the adoption of digital twins in construction is expected to accelerate, driven by advances in 5G connectivity, edge computing, and machine learning capabilities. Industry leaders who embrace this technology early will gain significant competitive advantages through improved efficiency, reduced costs, and enhanced sustainability practices. As the technology matures, we can anticipate more standardized implementation frameworks, improved interoperability, and broader integration across the entire construction lifecycle, from design to demolition.