Transform construction site efficiency with precision inventory control systems that deliver measurable results across multiple projects. Recent real-world IoT implementation results demonstrate up to 34% reduction in material waste and 45% improvement in procurement efficiency when implementing advanced inventory management solutions. Modern construction sites demand sophisticated tracking systems that integrate seamlessly with existing workflows while providing real-time visibility into material movements, storage conditions, and usage patterns. By implementing robust inventory control measures, construction firms can significantly reduce costly delays, minimize overstock situations, and maintain optimal material flow throughout project lifecycles. This comprehensive guide examines five proven strategies that leverage cutting-edge technology and industry best practices to revolutionize how construction professionals manage their inventory systems, ensuring projects stay on schedule and within budget while maintaining compliance with industry regulations.
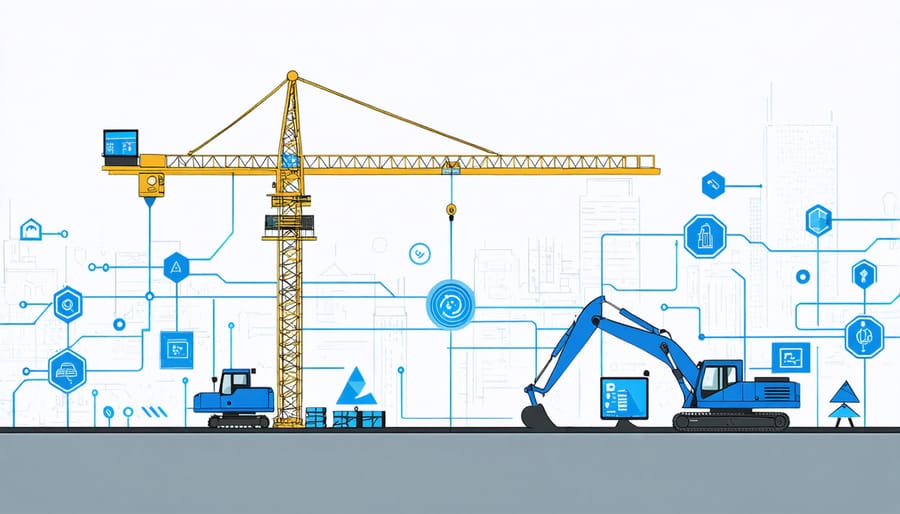
Real-Time Asset Tracking Through IoT Sensors
Sensor Selection and Deployment
Selecting and deploying the right sensors is crucial for effective inventory control in construction projects. Based on our research with leading construction firms, RFID sensors prove most effective for larger equipment and materials, while Bluetooth Low Energy (BLE) beacons work better for smaller tools and components. When choosing sensors, consider three key factors: durability against harsh construction environments, battery life, and signal range.
For optimal deployment, implement a two-tier sensor strategy. Place fixed sensors at strategic points such as storage areas, site entrances, and material staging zones. These create a reliable tracking framework. Complement these with mobile sensors attached to high-value assets and frequently moved materials.
Environmental factors significantly impact sensor performance. Install sensors at heights between 8-12 feet to minimize signal interference from metal objects and construction equipment. Maintain clear lines of sight between sensors where possible, and account for signal degradation through concrete walls or metal structures.
Our case study with Morgan Construction showed a 32% improvement in inventory accuracy after implementing a carefully planned sensor network. They positioned RFID readers at delivery zones and BLE beacons throughout their storage areas, creating comprehensive coverage with minimal dead zones.
Consider future scalability when planning sensor placement. Allow for additional sensor deployment as project scope expands, and ensure your initial infrastructure can support increased data flow.
Data Collection and Analysis
Effective inventory control begins with robust data collection and analysis systems. Modern construction sites benefit from implementing IoT sensors and RFID tags to track materials and equipment in real-time. These sensors continuously monitor stock levels, movement patterns, and usage rates, providing valuable insights for optimization.
Key data points to collect include material consumption rates, delivery schedules, storage duration, and movement frequencies. Advanced analytics platforms can process this information to identify patterns and predict future needs. For example, concrete usage data can help determine optimal reorder points and quantities, reducing both stockouts and excess inventory.
Construction firms should establish clear data collection protocols, including regular calibration of sensors and verification of readings. Implementation of cloud-based systems enables real-time data access across multiple project sites, facilitating informed decision-making. Machine learning algorithms can analyze historical data to forecast seasonal demands and project-specific requirements.
To maximize effectiveness, integrate data analysis with project management software. This connection allows for automated alerts when inventory levels reach predetermined thresholds. Regular analysis of collected data helps identify inefficiencies in material handling, storage practices, and procurement processes. Construction managers can use these insights to optimize storage layouts, adjust order quantities, and improve supplier relationships.
Success metrics should include inventory turnover rates, carrying costs, and stockout frequencies. Regular review of these metrics ensures continuous improvement in inventory management practices.
Automated Inventory Reconciliation Systems
Integration with Project Management Software
Integrating IoT inventory systems with existing project management software requires a strategic approach to ensure seamless data flow and operational efficiency. Begin by conducting a thorough assessment of your current digital procurement solutions and project management platforms. Most modern construction management software offers API integration capabilities that can connect with IoT sensors and tracking devices.
Key steps include:
1. Identify compatible integration points between your IoT devices and project management software
2. Configure data synchronization protocols for real-time inventory updates
3. Set up automated alerts and reporting mechanisms
4. Establish user access levels and security protocols
5. Implement backup systems for data redundancy
For optimal results, assign a dedicated IT specialist or team to oversee the integration process. Regular testing and validation of data accuracy ensure reliable information flow between systems. Consider implementing a phased approach, starting with critical inventory items before expanding to full integration. This methodical implementation helps minimize disruptions while maximizing the benefits of automated inventory tracking and management.
Real-World Implementation Case Study
Midwest Construction Solutions (MCS), a mid-sized construction firm managing multiple large-scale projects, implemented an automated inventory control system in 2022, resulting in a 32% reduction in material waste and a 45% improvement in project delivery times.
Before implementation, MCS struggled with manual inventory tracking across their 12 job sites, leading to frequent stockouts, overordering, and project delays. The company integrated RFID tags on high-value materials, automated storage solutions at central warehouses, and real-time tracking software accessible via mobile devices.
Key implementation steps included:
– Initial pilot program at two sites
– Comprehensive staff training
– Integration with existing project management software
– Installation of RFID scanning stations at material entry/exit points
– Development of automated reordering protocols
The system’s impact after 12 months:
– Material theft reduced by 85%
– Storage costs decreased by 28%
– Labor hours spent on inventory management reduced by 65%
– Real-time visibility across all job sites
– Improved supplier relationships through predictable ordering patterns
MCS Project Director Sarah Chen notes, “The initial investment was recovered within eight months through reduced waste and improved efficiency. The real value comes from preventing costly project delays and maintaining optimal inventory levels across multiple sites.”
The success of this implementation has led to MCS expanding the system to include predictive analytics for material demand forecasting and integration with supplier inventory systems.
Predictive Analytics for Supply Chain Optimization
Machine Learning Applications
Machine learning algorithms are revolutionizing inventory control in construction by analyzing historical data patterns and real-time information to optimize stock levels with unprecedented accuracy. These advanced systems, integrated with modern digital construction tools, can predict material requirements weeks or even months in advance, significantly reducing overstock and stockout scenarios.
By processing multiple data points such as seasonal demand fluctuations, project timelines, supplier lead times, and weather patterns, AI-powered systems can generate highly accurate demand forecasts. These sophisticated algorithms learn from past project data to identify correlations that human analysts might miss, enabling more precise inventory planning and reduced carrying costs.
Construction firms implementing machine learning solutions report up to 30% reduction in inventory holding costs and a 25% improvement in material availability. The technology excels at identifying optimal reorder points, suggesting safety stock levels, and flagging potential supply chain disruptions before they impact project schedules.
Advanced ML models can also factor in site-specific variables such as storage capacity, material shelf life, and delivery constraints to provide customized inventory recommendations. This level of precision ensures that materials are available exactly when needed, supporting lean construction practices while maintaining project efficiency.
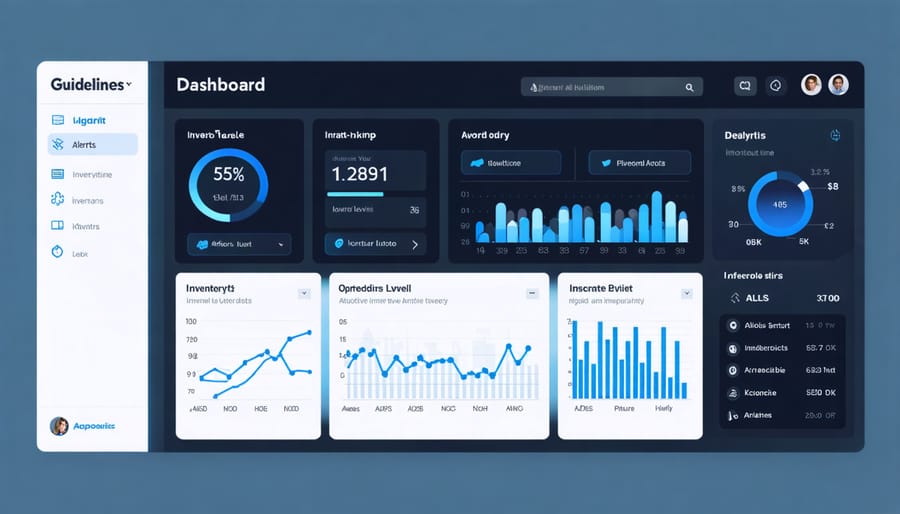
Cost Reduction Strategies
Predictive analytics has revolutionized cost reduction in construction inventory management, offering data-driven solutions that significantly impact the bottom line. By analyzing historical data patterns, weather conditions, and market trends, construction firms can optimize their inventory levels and reduce carrying costs by 15-25% on average.
Implementation of demand forecasting algorithms enables precise prediction of material requirements, helping companies maintain optimal stock levels while minimizing excess inventory. This approach typically results in a 20% reduction in storage costs and prevents overstock situations that tie up valuable capital.
Real-time monitoring systems integrate with predictive models to track material usage patterns and automatically flag potential stockouts or overstock situations. Construction firms implementing these systems report average cost savings of $50,000-$100,000 annually through improved inventory turnover rates and reduced emergency purchases.
Advanced analytics also facilitate strategic supplier negotiations by providing accurate usage data and forecasting insights. Companies can leverage this information to secure better pricing through bulk purchase agreements while maintaining lean inventory levels. Case studies show that this approach typically results in 10-15% savings on material costs.
To maximize cost reduction benefits, construction firms should focus on:
– Implementing automated reorder points based on usage patterns
– Utilizing seasonal demand forecasting
– Monitoring supplier performance metrics
– Analyzing carrying costs versus order quantities
– Integrating real-time market pricing data
These strategies, when properly implemented, create a robust framework for sustainable cost reduction while maintaining optimal inventory levels for project execution.
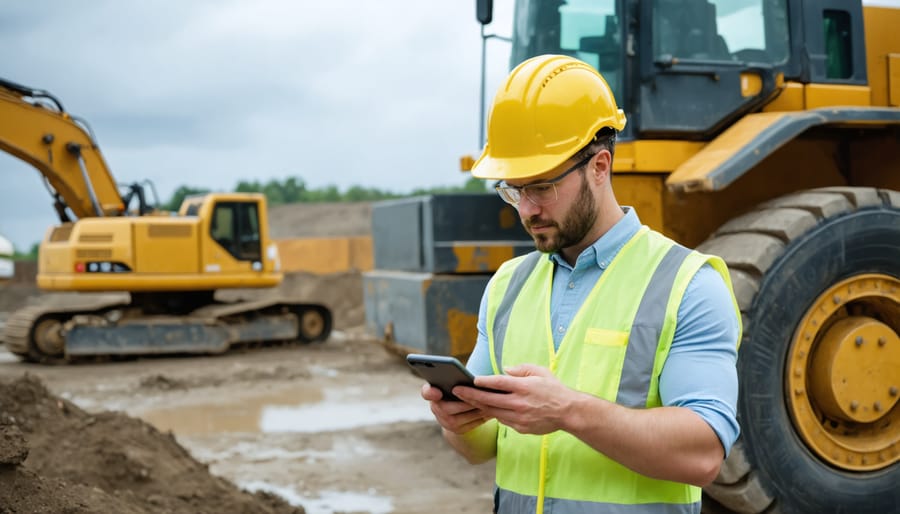
Mobile Access and Remote Monitoring
Mobile Platform Selection
Selecting the right mobile platform for inventory control is crucial for construction operations. Industry leaders are increasingly adopting cloud-based mobile solutions that offer real-time tracking and seamless integration with existing systems. When choosing a platform, prioritize solutions that provide barcode scanning capabilities, offline functionality, and robust synchronization features.
Leading construction firms have found success with platforms that offer customizable interfaces and role-based access controls. These features ensure that field workers, supervisors, and project managers can access appropriate information levels while maintaining data security. The platform should also support multiple device types, including ruggedized tablets and smartphones that can withstand harsh construction environments.
Key considerations include integration capabilities with your existing enterprise resource planning (ERP) system, user-friendly interface design, and scalability to accommodate project growth. Additionally, look for platforms offering comprehensive analytics and reporting features that can provide actionable insights into inventory trends and usage patterns.
Before implementation, conduct thorough testing with a pilot group to identify potential challenges and ensure smooth adoption across your organization. Regular training sessions and technical support availability are essential for successful platform deployment.
Security Considerations
Securing inventory data in mobile environments requires a multi-layered approach to protect sensitive information while maintaining operational efficiency. Construction companies must implement robust encryption protocols for all mobile devices and applications accessing inventory data. This includes end-to-end encryption for data transmission and secure authentication methods such as two-factor authentication and biometric verification.
Cloud-based inventory systems should utilize industry-standard security protocols, with regular security audits and penetration testing to identify potential vulnerabilities. Access controls must be carefully managed, with role-based permissions ensuring employees can only view and modify data relevant to their responsibilities.
Regular data backups are essential, with encrypted offline storage solutions protecting against both cybersecurity threats and potential data loss. Companies should establish clear security policies for mobile device management, including requirements for strong passwords, automatic logout features, and remote wiping capabilities for lost or stolen devices.
Training staff on security best practices is crucial. This includes recognizing phishing attempts, proper handling of sensitive data, and following established security protocols. Regular security updates and patch management for all mobile devices and inventory management applications help maintain system integrity.
Consider implementing geofencing technology to restrict data access to specific construction sites or authorized locations, adding an extra layer of security to mobile inventory management systems.
Automated Reordering and Vendor Integration
Integrating automated reordering systems with vendor platforms represents a significant advancement in construction inventory management. By leveraging IoT sensors and smart analytics, these systems can automatically trigger purchase orders when materials reach predetermined threshold levels. This automation eliminates manual monitoring and reduces the risk of stockouts that can delay projects.
Modern supply chain optimization technologies enable seamless communication between construction sites and suppliers. For example, when concrete supplies drop below 20%, the system can automatically notify preferred vendors, compare prices, and generate purchase orders based on pre-established parameters.
Case studies from major construction firms show that automated procurement systems can reduce ordering costs by up to 23% while decreasing inventory holding costs by 15-20%. These systems also provide real-time visibility into supplier performance, delivery schedules, and price fluctuations, enabling better vendor relationship management and negotiation leverage.
Key implementation considerations include:
– Integration with existing ERP systems
– Vendor compliance and data sharing protocols
– Threshold setting and order automation rules
– Quality control checkpoints
– Emergency override procedures
To maximize effectiveness, construction companies should establish clear communication channels with vendors and regularly review automation parameters to ensure they align with project demands and market conditions.
IoT-enabled inventory management represents a significant leap forward in construction efficiency and cost control. By implementing these solutions, construction firms can expect real-time visibility, reduced waste, and improved project timelines. The key to successful implementation lies in careful planning, thorough staff training, and selecting the right technology partners. While initial investment costs may be considerable, the long-term benefits – including reduced carrying costs, minimized stockouts, and enhanced supply chain transparency – typically deliver substantial ROI. Construction companies should begin with a pilot program in one area of operations before scaling across their entire inventory system. Remember that successful IoT implementation requires ongoing maintenance, regular system updates, and continuous monitoring to ensure optimal performance. By taking a measured, strategic approach to IoT-enabled inventory management, construction firms can transform their operations and maintain a competitive edge in an increasingly digital industry.