Revolutionary advances in construction engineering are fundamentally transforming how we design, build, and optimize modern structures. From artificial intelligence-driven project management to breakthrough energy efficiency solutions, the industry is experiencing an unprecedented technological renaissance. Smart materials with self-healing properties, robotics-enabled construction processes, and digital twin technology are driving productivity gains of up to 50% while reducing project timelines by one-third.
The convergence of sustainable building practices and advanced automation has created a new paradigm in construction methodology. Building Information Modeling (BIM) integration with Internet of Things (IoT) sensors now enables real-time monitoring and predictive maintenance, fundamentally changing how structures are maintained throughout their lifecycle. These innovations aren’t just incremental improvements—they represent a complete reimagining of construction possibilities.
Industry leaders implementing these cutting-edge solutions report significant improvements in project outcomes: 40% reduction in construction waste, 35% decrease in energy consumption, and 25% improvement in worker safety metrics. As we stand at the cusp of this technological revolution, these advancements are setting new standards for efficiency, sustainability, and precision in construction engineering.
Advanced Building Envelope Technologies
Smart Thermal Materials
Smart thermal materials represent a significant advancement in building envelope technology, with phase-change materials (PCMs) leading the innovation frontier. These sophisticated materials can absorb, store, and release thermal energy during phase transitions, effectively regulating indoor temperatures and reducing HVAC energy consumption by up to 30%.
Contemporary PCM applications include microencapsulated materials integrated into building materials like gypsum wallboards and concrete. When ambient temperatures rise, these materials absorb excess heat by transitioning from solid to liquid state within their microscopic containers. Conversely, as temperatures drop, they solidify and release stored heat, maintaining optimal thermal comfort.
Dynamic insulation systems complement PCMs by actively responding to environmental conditions. These systems utilize smart materials that can modify their thermal resistance properties based on temperature fluctuations or external stimuli. For instance, thermochromic materials change their optical properties with temperature variations, controlling solar heat gain through windows and facades.
Recent developments include hybrid systems combining PCMs with traditional insulation materials, creating adaptive building envelopes that optimize energy performance year-round. A notable example is the implementation in the Edge Olympic building in Amsterdam, where smart thermal materials reduced energy costs by 25% while improving occupant comfort.
The integration of IoT sensors with these materials enables real-time monitoring and adjustment of thermal properties, marking a significant step toward truly intelligent building systems.
Adaptive Façade Systems
Adaptive façade systems represent a significant advancement in building envelope technology, offering dynamic responses to environmental conditions while optimizing energy efficiency. These intelligent building skins incorporate automated systems that adjust in real-time to changing weather patterns, solar angles, and occupant needs.
At the forefront of this technology are electrochromic glazing systems, which can transition from transparent to tinted states based on solar radiation levels. These smart windows reduce cooling loads by up to 20% while maintaining optimal natural daylight levels. Similarly, kinetic shading elements, such as automated louvers and dynamic solar screens, adjust their position throughout the day to maximize thermal comfort and minimize energy consumption.
Recent implementations include the Al Bahar Towers in Abu Dhabi, featuring a responsive mashrabiya-inspired facade that reduces solar gain by 50%. The system comprises thousands of geometric panels that open and close in response to the sun’s movement, demonstrating how traditional architectural elements can be reimagined through modern technology.
The integration of advanced sensors and artificial intelligence enables these systems to learn and predict optimal configurations based on historical performance data. Building management systems can now anticipate weather changes and adjust facade elements proactively, rather than merely reacting to current conditions.
Material innovations in this field include phase-change materials and smart polymers that automatically modify their properties based on temperature fluctuations, providing passive adaptation capabilities alongside active systems.
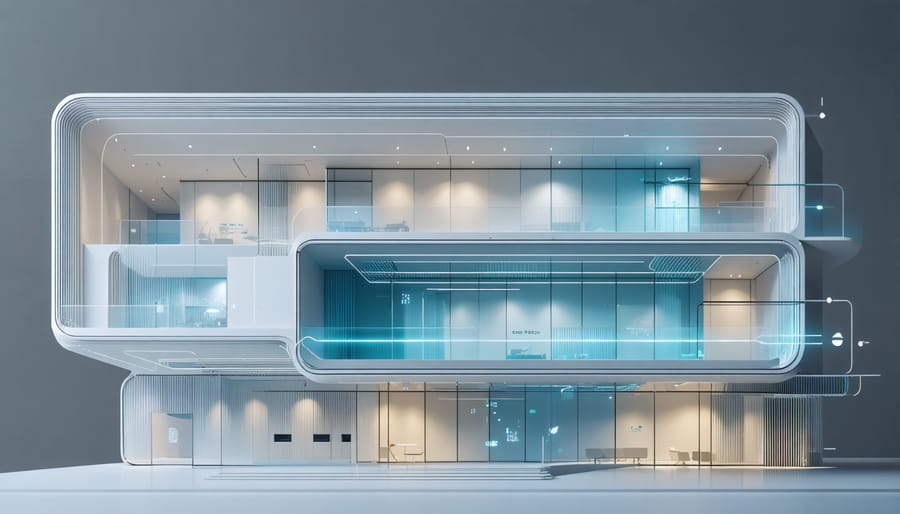
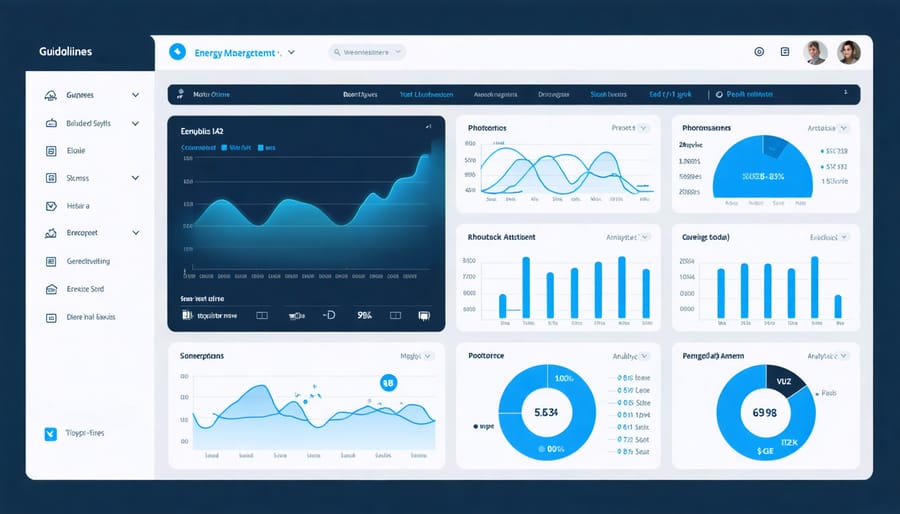
Intelligent Energy Management Systems
Predictive Energy Analytics
Predictive energy analytics represents a transformative approach in construction engineering, leveraging machine learning algorithms to optimize building energy consumption patterns. By analyzing vast datasets from building management systems, IoT sensors, and historical usage patterns, these systems can forecast energy demands with remarkable accuracy.
Recent implementations have demonstrated energy savings of 15-30% in commercial buildings through predictive analytics. For instance, the Landmark Tower project in Singapore achieved a 22% reduction in HVAC energy consumption by implementing ML-based predictive controls that anticipate occupancy patterns and weather conditions.
These systems operate by processing multiple data streams, including:
– Occupancy patterns and space utilization
– Weather forecasts and seasonal variations
– Equipment performance metrics
– Historical energy consumption data
– Real-time utility pricing
The integration of artificial intelligence enables buildings to self-adjust their energy systems proactively rather than reactively. Advanced algorithms can predict peak demand periods, optimize start-up times for HVAC systems, and adjust lighting controls based on natural light availability and occupancy predictions.
A notable case study from the Northwestern Medical Center demonstrates how predictive analytics reduced annual energy costs by $800,000 through intelligent load management and automated system optimization. The facility’s ML system learns from daily operations, continuously improving its prediction accuracy and energy-saving strategies.
Construction firms are increasingly incorporating these analytics platforms during the design phase, enabling better equipment sizing and system configuration. This proactive approach ensures optimal energy performance throughout the building’s lifecycle while reducing operational costs and environmental impact.
IoT Integration
The integration of Internet of Things (IoT) technology has revolutionized construction site monitoring and management, enabling unprecedented levels of data collection and real-time decision-making capabilities. Advanced sensor networks now form the backbone of modern construction projects, providing continuous streams of critical information about structural integrity, environmental conditions, and equipment performance.
These sophisticated monitoring systems utilize a combination of wireless sensors, including accelerometers, strain gauges, and environmental monitors, to create a comprehensive digital overview of construction progress. Project managers can access real-time data on concrete curing conditions, structural load distributions, and potential safety hazards through centralized dashboards, enabling swift responses to emerging issues.
Recent implementations have demonstrated significant improvements in project efficiency and safety. For instance, major infrastructure projects are now employing smart sensors that monitor vibration levels during foundation work, helping to prevent damage to adjacent structures. Temperature and humidity sensors ensure optimal conditions for material curing, while movement sensors track potential structural shifts with millimeter-level precision.
The true power of IoT integration lies in its predictive capabilities. By analyzing patterns in collected data, these systems can forecast maintenance needs, identify potential structural issues before they become critical, and optimize resource allocation. Construction firms report up to 20% reduction in maintenance costs and 15% improvement in project completion times through strategic IoT deployment.
Cloud-based platforms aggregate sensor data with project management tools, creating a unified ecosystem for construction monitoring. This integration enables automated alerts, detailed reporting, and enhanced collaboration between site teams, engineers, and stakeholders, fundamentally transforming how construction projects are executed and monitored in real-time.
Renewable Energy Integration
Building-Integrated Photovoltaics
Building-integrated photovoltaics (BIPV) represent a significant advancement in sustainable construction, seamlessly incorporating solar power generation into building materials rather than treating them as separate components. Recent innovations have produced solar glass facades that achieve up to 12% transparency while maintaining impressive power generation capabilities, making them ideal for commercial buildings with extensive glazing.
Notable developments include high-efficiency crystalline silicon cells embedded within structural glass panels, capable of generating 120-150 watts per square meter while serving as functional building elements. These systems now feature enhanced durability and weather resistance, with manufacturers offering warranties up to 25 years.
The latest BIPV solutions extend beyond traditional window applications to include solar roof tiles, cladding systems, and even solar-active concrete surfaces. For instance, the recently completed Swiss Tech Convention Center showcases multi-colored solar panels that serve both aesthetic and functional purposes, generating approximately 145,000 kWh annually while maintaining architectural integrity.
Cost-effectiveness has improved significantly, with current BIPV systems showing a return on investment period of 8-12 years, depending on location and energy prices. This improvement is largely due to advanced manufacturing processes and increased efficiency in power conversion, making BIPV increasingly attractive for both new construction and renovation projects.
Integration capabilities have also evolved, with smart building management systems now able to optimize power generation and distribution based on real-time usage patterns and weather conditions.
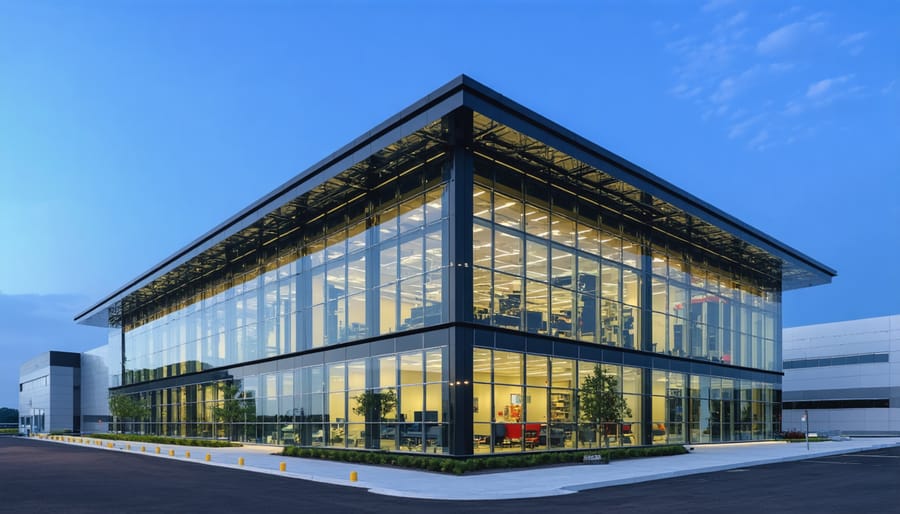
Energy Storage Solutions
The construction industry is witnessing a transformative shift in how energy is stored and utilized on-site through advanced energy storage technologies. Leading this revolution are high-capacity lithium-ion battery systems, specifically designed for construction applications, which can store excess energy generated during off-peak hours and provide reliable power during peak demand periods.
Thermal energy storage (TES) systems have emerged as another crucial innovation, utilizing phase-change materials (PCMs) to capture and release thermal energy efficiently. These systems are particularly valuable in large-scale commercial projects, where they can reduce HVAC energy consumption by up to 30%. Recent implementations in the Dubai Museum of the Future demonstrate how PCM-based storage can maintain stable indoor temperatures while significantly reducing grid dependency.
Flow battery technology represents the latest advancement in construction energy storage, offering extended lifecycle and improved safety compared to traditional battery systems. These systems are especially beneficial for remote construction sites, where reliable power supply is crucial for continuous operations. Industry leaders like Skanska have successfully integrated flow batteries in their sustainable building projects, achieving remarkable energy autonomy and cost savings.
The integration of smart energy management systems with these storage solutions enables real-time monitoring and optimization, ensuring maximum efficiency and reduced environmental impact across construction operations.
Case Studies and Implementation
The Seattle Tower Project stands as a prime example of innovative energy-efficient construction implementation. Completed in 2022, this 45-story commercial building achieved LEED Platinum certification through the integration of advanced building automation systems and a double-skin façade that reduced energy consumption by 47% compared to conventional buildings of similar size.
In Copenhagen, the Green Circle Development showcases how adaptive reuse can merge with cutting-edge sustainability. The project transformed an abandoned industrial complex into a mixed-use development, incorporating geothermal heating systems and smart windows that automatically adjust tint based on sunlight intensity. Energy monitoring data shows a remarkable 62% reduction in heating and cooling costs.
The Dubai Sustainable City project demonstrates large-scale implementation of multiple energy-efficient innovations. The development features 500 residential units equipped with solar panels, smart home systems, and gray water recycling. Notable achievements include achieving net-zero energy status for common areas and reducing overall energy consumption by 40% through innovative building envelope design.
One particularly successful case study is the Melbourne Innovation Hub, where contractors utilized prefabricated components with integrated energy management systems. The project shortened construction time by 30% while achieving exceptional energy performance. The building’s smart grid integration allows it to operate 85% below standard energy consumption levels.
The Frankfurt Tower renovation project exemplifies successful retrofitting of existing structures. Engineers implemented a combination of phase-change materials in walls, AI-driven HVAC controls, and regenerative elevator systems. Post-renovation monitoring reveals a 55% reduction in energy costs and improved occupant comfort scores.
These case studies demonstrate that while initial investment in energy-efficient innovations may be higher, the long-term benefits significantly outweigh costs. Key success factors include early integration of energy efficiency goals in project planning, careful selection of compatible technologies, and robust monitoring systems to verify performance. The data from these projects continues to inform best practices and drive innovation in sustainable construction worldwide.
The construction engineering sector stands at the cusp of a transformative era, driven by groundbreaking innovations that are reshaping traditional building practices. From AI-powered project management systems to sustainable building materials and advanced robotics, these technological advancements are significantly improving efficiency, safety, and environmental sustainability across construction projects worldwide.
The integration of digital twins, smart sensors, and IoT devices has enabled unprecedented levels of real-time monitoring and predictive maintenance, while modular construction techniques continue to reduce project timelines and costs. As we look toward the future, emerging technologies like 3D-printed buildings, self-healing materials, and carbon-capturing concrete promise to further revolutionize the industry.
The construction sector’s commitment to innovation shows no signs of slowing. Industry experts predict that the next decade will bring even more sophisticated automation solutions, enhanced sustainability practices, and improved integration of virtual and augmented reality in construction processes. These developments, combined with increasing focus on environmental responsibility and worker safety, suggest a future where construction projects are faster, safer, more sustainable, and more cost-effective than ever before.