Transform construction project outcomes through comprehensive smart building energy management systems that integrate real-time monitoring, predictive analytics, and automated control mechanisms. Modern total energy management revolutionizes how construction professionals approach resource optimization, delivering up to 40% reduction in operational costs while ensuring maximum building performance.
Industry leaders leverage advanced building management systems (BMS) to orchestrate HVAC, lighting, and power distribution systems in perfect harmony, creating intelligent environments that respond dynamically to occupancy patterns and environmental conditions. This systematic approach transforms traditional construction projects into high-performance assets that consistently outperform industry benchmarks.
The convergence of IoT sensors, machine learning algorithms, and enterprise-level energy management platforms enables unprecedented control over building operations, establishing new standards for sustainability and operational excellence in contemporary construction. Forward-thinking organizations implementing total energy management solutions position themselves at the forefront of sustainable building practices while securing significant competitive advantages through reduced operational expenses and enhanced building value.
By integrating these sophisticated systems during the design phase, construction professionals can deliver buildings that not only meet current energy efficiency standards but exceed them, creating lasting value for stakeholders and setting new benchmarks for environmental stewardship in the built environment.
Understanding Total Energy Management in Construction
Key Components of Total Energy Management
Total energy management relies on three fundamental components that work in synergy to deliver optimal results: monitoring systems, optimization protocols, and control mechanisms.
Advanced monitoring systems form the foundation, utilizing sensors and smart meters to collect real-time data on energy consumption patterns, peak usage periods, and system performance metrics. These systems typically integrate with building management software to provide comprehensive analytics and reporting capabilities.
Optimization protocols represent the strategic layer, where collected data transforms into actionable insights. This includes load balancing algorithms, demand response strategies, and predictive maintenance schedules. Energy managers use these protocols to identify inefficiencies, forecast future consumption patterns, and implement corrective measures before issues escalate.
Control systems serve as the operational backbone, enabling automated responses to changing conditions. Modern control systems incorporate programmable logic controllers (PLCs), building automation systems (BAS), and smart grid integration capabilities. These components work together to maintain optimal environmental conditions while minimizing energy waste.
The integration of these components requires careful consideration of system compatibility, scalability, and user interface design. Successful implementation depends on selecting appropriate technology solutions that align with facility requirements and operational goals. Regular calibration and updates ensure these systems maintain peak performance and adapt to evolving energy management standards.
Integration with Building Information Modeling (BIM)
The integration of Total Energy Management (TEM) systems with Building Information Modeling (BIM) represents a significant advancement in construction project efficiency and energy optimization. BIM’s comprehensive 3D modeling capabilities, combined with TEM’s analytical tools, enable project teams to simulate and optimize energy consumption patterns throughout a building’s lifecycle.
During the design phase, this integration allows architects and engineers to perform detailed energy analysis using actual building data. Teams can evaluate different design alternatives, material selections, and system configurations to determine their impact on energy performance. The BIM model serves as a central repository for all energy-related information, including HVAC specifications, lighting systems, and thermal properties of building materials.
Real-time data integration between TEM systems and BIM enables continuous monitoring and verification of energy performance against design targets. Facility managers can visualize energy usage patterns within the BIM environment, making it easier to identify inefficiencies and implement corrective measures. This visualization capability extends to retrofitting projects, where existing buildings can be modeled and analyzed for energy optimization opportunities.
The BIM-TEM integration also facilitates better collaboration among project stakeholders. Energy consultants, architects, and facility managers can share insights and make informed decisions based on accurate, model-based data. This collaborative approach ensures that energy management strategies are aligned with overall building performance objectives from conception through operation.
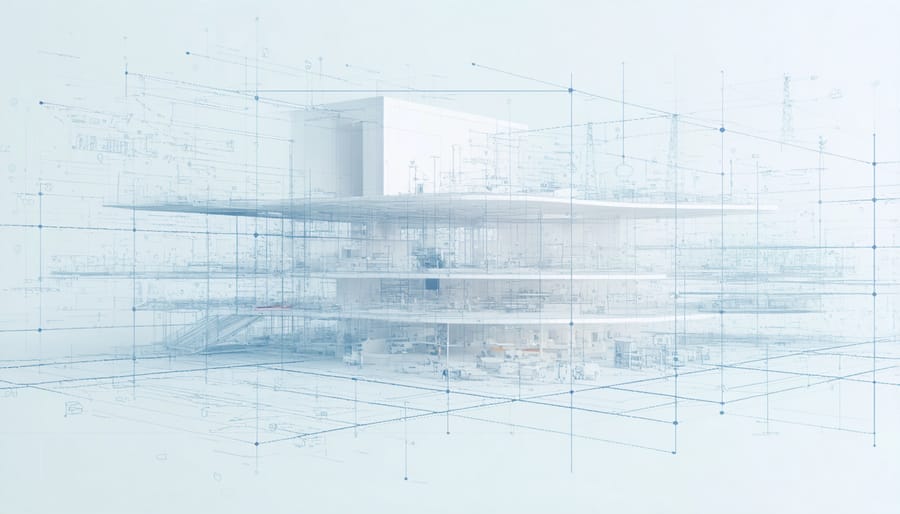
Implementation Strategies for Construction Sites
Pre-construction Energy Planning
Pre-construction energy planning serves as the foundation for successful total energy management in construction projects. This critical phase involves comprehensive analysis of energy requirements, consumption patterns, and optimization opportunities before breaking ground. Industry experts recommend conducting detailed energy modeling simulations to predict building performance and identify potential efficiency improvements during the design phase.
Key components of pre-construction energy planning include site analysis for renewable energy potential, building orientation optimization, and evaluation of passive design strategies. Project managers should assess local climate conditions, solar exposure, and prevailing winds to maximize natural resources. This data informs decisions about building envelope specifications, HVAC system selection, and lighting design.
Energy load calculations must account for anticipated occupancy patterns, equipment usage, and seasonal variations. Construction professionals should collaborate with energy consultants to establish baseline energy consumption targets and develop strategies to achieve them. This includes selecting energy-efficient materials, specifying high-performance building systems, and integrating smart building technologies.
Cost-benefit analysis of various energy solutions should consider initial investment, operational costs, maintenance requirements, and expected return on investment. Leading construction firms typically create detailed energy management plans that outline implementation schedules, monitoring protocols, and performance verification methods. These plans should align with relevant building codes, energy standards, and certification requirements while maintaining flexibility for future modifications.
Real-time Monitoring Systems
Modern construction projects rely heavily on real-time monitoring systems to track and optimize energy consumption throughout the building process. These sophisticated systems utilize a network of IoT sensors, smart meters, and data analytics platforms to provide continuous insights into energy usage patterns.
Key components typically include power meters for electrical consumption monitoring, thermal sensors for HVAC system optimization, and occupancy sensors to regulate lighting and equipment usage. Advanced systems also incorporate weather data integration to anticipate and adjust for environmental factors affecting energy consumption.
Data visualization dashboards enable project managers to identify consumption peaks, equipment inefficiencies, and potential energy waste immediately. Mobile applications allow stakeholders to receive instant alerts about unusual energy patterns or equipment malfunctions, facilitating rapid response to potential issues.
Implementation of these monitoring systems has shown remarkable results across various construction projects. For instance, a recent commercial development in Singapore achieved 23% energy savings during construction by implementing automated monitoring and response protocols.
The collected data serves multiple purposes beyond immediate monitoring, including compliance reporting, performance benchmarking, and predictive maintenance scheduling. This comprehensive approach to energy tracking has become essential for achieving sustainability goals and maintaining cost-effective operations throughout the construction phase.
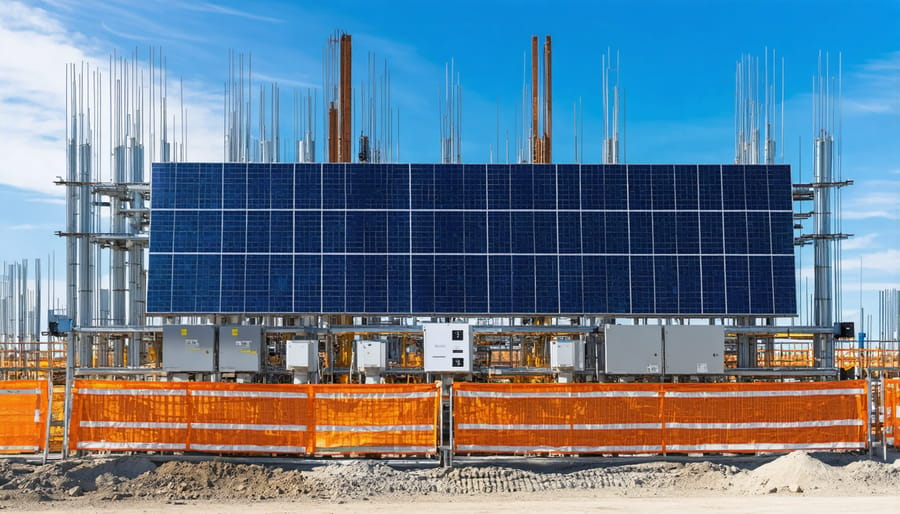
Data Analysis and Optimization
Modern total energy management relies heavily on data analysis and optimization to drive informed decision-making and achieve maximum efficiency. Advanced building management systems (BMS) collect vast amounts of data from multiple sources, including smart meters, sensors, and IoT devices, providing real-time insights into energy consumption patterns.
These systems analyze historical and current data to identify trends, anomalies, and opportunities for improvement. Machine learning algorithms process this information to predict peak usage periods, optimize HVAC operations, and adjust lighting systems based on occupancy patterns. The resulting analytics enable facility managers to implement data-driven strategies that significantly reduce energy waste.
Key optimization strategies include load balancing, demand response management, and predictive maintenance scheduling. By analyzing equipment performance data, managers can identify units operating below optimal efficiency and schedule preventive maintenance before failures occur. This proactive approach not only reduces energy waste but also extends equipment lifespan and minimizes downtime.
Real-time monitoring and automated alerts help identify sudden spikes in energy consumption or system inefficiencies, allowing for immediate corrective action. Regular performance reports and benchmarking against industry standards provide valuable metrics for continuous improvement and ROI validation. This data-driven approach typically results in 15-30% energy savings when properly implemented and maintained.
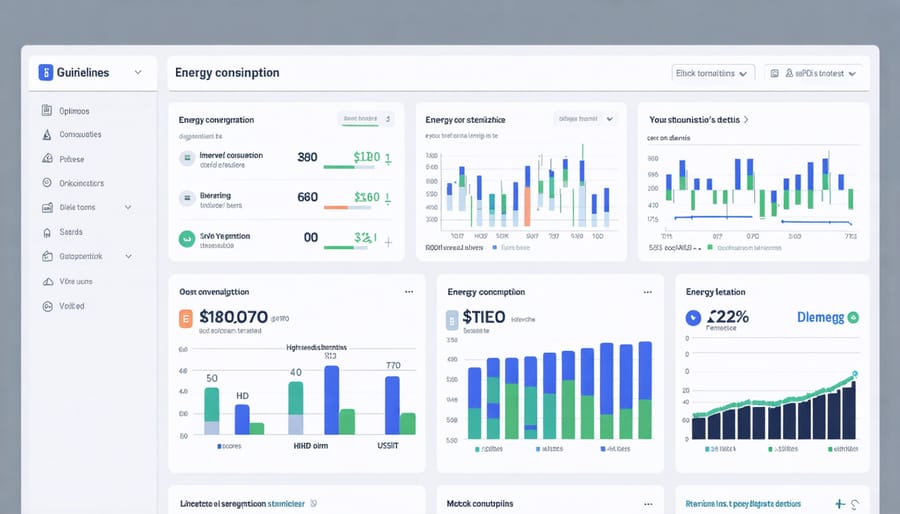
Cost-Benefit Analysis
Initial Investment Requirements
Implementing a total energy management system requires significant upfront investment in both infrastructure and technology. The initial setup typically involves three main cost categories: hardware installation, software systems, and professional services. For a medium-sized commercial building, hardware costs—including sensors, meters, and control systems—generally range from $50,000 to $150,000, depending on the building’s complexity and existing infrastructure.
The integration of energy efficient construction technologies requires specialized equipment such as Building Management Systems (BMS), smart meters, and automated control interfaces. Software licensing and implementation costs typically add another $30,000 to $75,000, covering energy management platforms, data analytics tools, and user interfaces.
Professional services, including system design, installation, and initial commissioning, usually account for 20-30% of the total investment. Additional costs may include staff training, documentation, and system optimization, typically ranging from $15,000 to $25,000.
While these figures might seem substantial, it’s important to note that many organizations recover their initial investment within 2-4 years through reduced energy consumption, improved operational efficiency, and decreased maintenance costs. Government incentives and energy efficiency rebates can also significantly offset initial costs, sometimes covering up to 30% of the total investment.
Long-term Returns and Benefits
Implementing total energy management systems delivers substantial returns over the long term, with most projects achieving ROI within 3-5 years of implementation. Organizations that have adopted comprehensive cost-saving energy solutions typically report energy expenditure reductions of 20-30% annually.
Analysis of multiple case studies reveals that initial investments in energy management infrastructure, while significant, are offset by cumulative savings that continue to grow throughout the building’s lifecycle. For example, a typical commercial building implementing total energy management can expect to save $0.50-$1.50 per square foot annually in operating costs.
Beyond direct cost savings, long-term benefits include increased property value, enhanced tenant satisfaction, and improved building performance. Buildings with comprehensive energy management systems commonly command 7-10% higher rental rates and maintain higher occupancy levels compared to conventional properties.
Environmental returns are equally significant, with most buildings reducing their carbon footprint by 25-40% over ten years. This reduction not only supports corporate sustainability goals but also ensures compliance with increasingly stringent environmental regulations, potentially avoiding future retrofit costs.
The financial impact becomes more pronounced when considering the rising energy costs and stricter building regulations. Organizations that implement total energy management today position themselves advantageously for future market conditions while benefiting from immediate operational improvements.
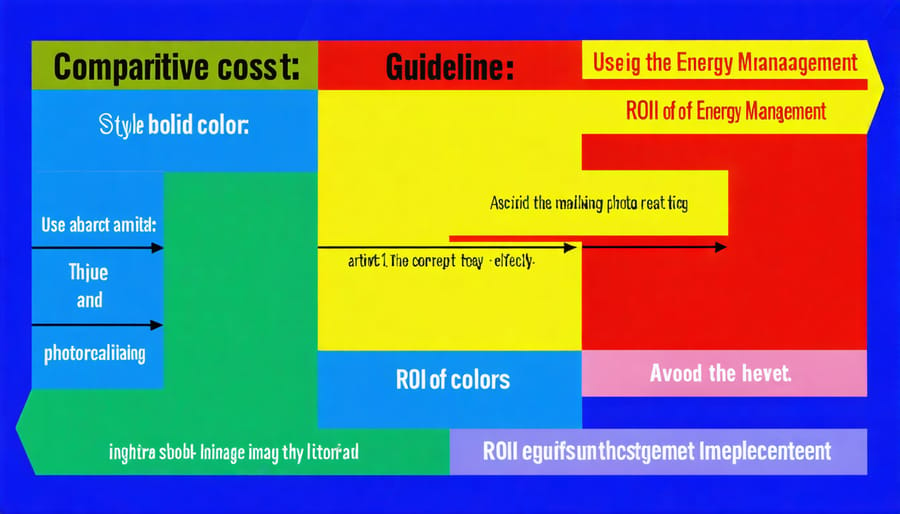
Case Study: Successful Implementation
The implementation of total energy management at the Riverside Business Complex in Denver, Colorado, stands as a benchmark for successful energy optimization in modern construction. This $180 million commercial development project, completed in 2021, demonstrates how comprehensive energy management strategies can deliver substantial returns on investment while setting new standards for sustainable construction.
The project team, led by Morrison Construction Group, implemented a multi-faceted energy management approach from the initial design phase through construction and post-occupancy operations. The strategy began with extensive energy modeling using advanced simulation software to optimize building orientation, envelope design, and mechanical systems integration.
Key implementation elements included:
– Installation of a building automation system (BAS) with over 2,500 monitoring points
– Integration of renewable energy systems, including a 450kW rooftop solar array
– Implementation of smart lighting controls with daylight harvesting
– Development of a real-time energy consumption dashboard
– Installation of energy-efficient HVAC systems with heat recovery
The construction phase utilized prefabricated components to reduce on-site energy consumption and waste. The project team employed just-in-time delivery methods to minimize equipment idle time and fuel consumption. During construction, temporary power solutions were carefully managed through smart metering and scheduling of high-energy activities during off-peak hours.
Results after the first year of operation showed:
– 47% reduction in overall energy consumption compared to baseline
– $380,000 annual energy cost savings
– 35% decrease in peak demand charges
– LEED Platinum certification achievement
– ROI period reduced from projected 7 years to 5.2 years
Critical to the project’s success was the establishment of a dedicated energy management team that included facilities managers, engineers, and sustainability consultants. This team developed comprehensive operation protocols and training programs for building occupants and maintenance staff.
Challenges encountered during implementation included initial resistance from subcontractors regarding new procedures and higher upfront costs for energy-efficient systems. These were overcome through targeted training programs and detailed cost-benefit analyses that demonstrated long-term savings.
The project’s success has led to its recognition as a model for total energy management implementation, with the approach being adopted by similar developments across the country. The Riverside Complex continues to serve as a living laboratory for energy efficiency innovations, with ongoing monitoring and optimization providing valuable data for future projects.
This case study demonstrates that successful total energy management requires careful planning, stakeholder engagement, and a long-term perspective on return on investment. The project’s achievements have set new benchmarks for energy efficiency in commercial construction while providing a practical roadmap for future implementations.
Total energy management has emerged as a cornerstone of modern construction practices, transforming how we approach building efficiency and sustainability. As demonstrated throughout this analysis, successful implementation requires a strategic combination of advanced technology, skilled personnel, and comprehensive planning. The integration of smart building systems, renewable energy solutions, and real-time monitoring capabilities has proven to deliver substantial returns on investment while significantly reducing environmental impact.
Looking ahead, the construction industry is poised for even greater advancements in energy management. Artificial intelligence and machine learning are expected to revolutionize how buildings operate, with predictive analytics enabling unprecedented levels of efficiency. The growing adoption of Internet of Things (IoT) devices will further enhance our ability to monitor and optimize energy consumption in real-time.
Key success factors for organizations implementing total energy management include securing leadership buy-in, investing in proper training and certification for staff, and maintaining a long-term perspective on energy efficiency investments. Case studies have consistently shown that organizations achieving the best results are those that view energy management as an ongoing process rather than a one-time initiative.
The future outlook for total energy management is particularly promising, with emerging technologies and stricter regulatory requirements driving innovation. Construction professionals should prepare for increased integration of renewable energy systems, more sophisticated building automation, and growing demands for net-zero energy buildings. Those who embrace these changes early will be better positioned to meet future challenges and capitalize on new opportunities.
As the industry continues to evolve, total energy management will remain essential for achieving both environmental sustainability and operational efficiency in construction projects.