Transform your construction projects with groundbreaking sustainable innovations that deliver measurable ROI and environmental impact. Leading firms implementing sustainable construction principles are achieving 30-40% reduction in energy consumption while increasing property values by up to 25%.
Advanced materials technology, including self-healing concrete and transparent solar panels, is revolutionizing building envelope performance. These innovations, combined with AI-powered building management systems, are creating structures that actively respond to environmental conditions, optimizing resource usage in real-time.
Industry leaders integrating these solutions report significant competitive advantages: reduced operational costs, enhanced tenant satisfaction, and improved regulatory compliance. From modular green roof systems that reduce urban heat island effects to water recycling technologies that cut consumption by 75%, today’s sustainable solutions offer unprecedented opportunities for construction professionals to deliver high-performance buildings that meet growing market demands for environmental responsibility.
The most successful implementations share a common framework: strategic material selection, integrated design approaches, and data-driven performance monitoring. This comprehensive guide examines cutting-edge sustainable technologies, their practical applications, and proven strategies for successful implementation in commercial construction projects.
Smart Materials Revolutionizing Building Performance
Self-Healing Construction Materials
Self-healing construction materials represent a groundbreaking advancement in sustainable building technology, with bio-concrete leading the innovation frontier. This remarkable material contains dormant bacteria that activate when cracks appear, producing limestone to fill the gaps autonomously. Studies conducted by Delft University of Technology demonstrate that bio-concrete can extend structure lifespans by up to 30% while reducing maintenance costs by 50%.
Beyond bio-concrete, researchers have developed polymer-based self-healing materials that utilize microcapsules containing healing agents. When damage occurs, these capsules rupture and release compounds that solidify, effectively sealing cracks and preventing further deterioration. This technology has shown particular promise in infrastructure applications, where continuous monitoring and repair can be challenging and costly.
Recent developments include shape-memory materials that can return to their original form after deformation, and self-healing coatings that protect against corrosion. According to industry data, implementing these materials can reduce repair and maintenance expenses by up to 60% over a structure’s lifetime.
The commercial adoption of self-healing materials has accelerated, with several major construction projects in Europe and Asia incorporating these innovations. For instance, the Rotterdam Harbor Bridge renovation project demonstrated a 40% reduction in maintenance interventions after implementing self-healing coating systems.
While initial costs remain higher than traditional materials, the long-term benefits in reduced maintenance, extended service life, and improved sustainability make self-healing materials an increasingly attractive option for forward-thinking construction professionals.
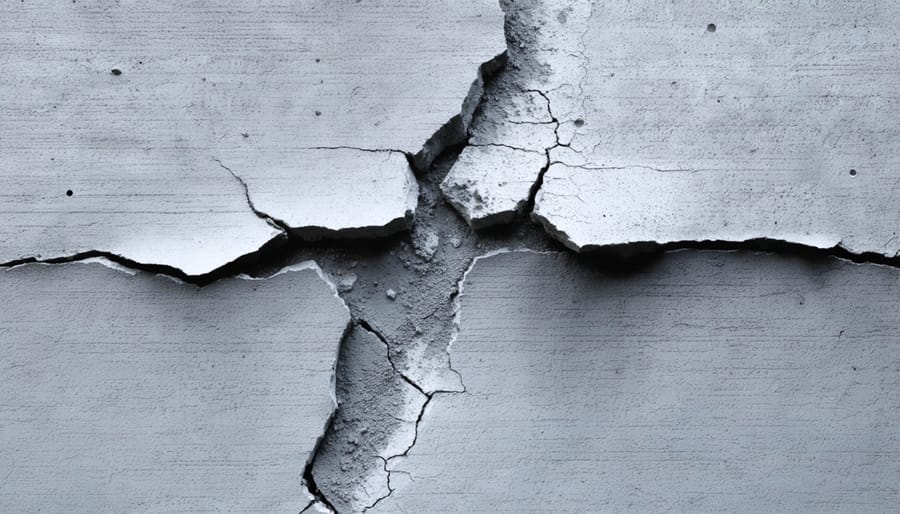
Energy-Generating Building Components
The integration of energy-generating components into building materials represents a significant advancement in sustainable construction. Building-integrated photovoltaics (BIPV) have evolved beyond traditional solar panels, now incorporating transparent solar cells within windows and photovoltaic materials seamlessly embedded in façade elements. These solutions generate clean energy while maintaining architectural aesthetics and structural integrity.
Recent innovations include solar tiles that match conventional roofing materials in appearance while producing up to 98% of the power output of traditional panels. Manufacturers have also developed semi-transparent solar glass that allows natural light transmission while generating electricity, making it ideal for curtain walls and skylights in commercial buildings.
Kinetic energy harvesting systems are emerging as complementary power sources. Floor tiles that convert footsteps into electrical energy have been successfully implemented in high-traffic areas, generating up to 8 watts per step. Similarly, revolving doors equipped with energy-harvesting mechanisms can produce up to 4.5 kWh annually per door.
The integration of these technologies offers multiple benefits beyond energy generation. They contribute to building energy efficiency ratings, reduce operational costs, and can help achieve LEED certification points. Case studies from commercial installations demonstrate ROI periods of 5-7 years, with some systems maintaining 80% efficiency for up to 25 years.
For optimal implementation, architects and engineers should consider factors such as building orientation, climate conditions, and usage patterns when selecting energy-generating components. This ensures maximum energy yield and system longevity while meeting aesthetic and functional requirements.
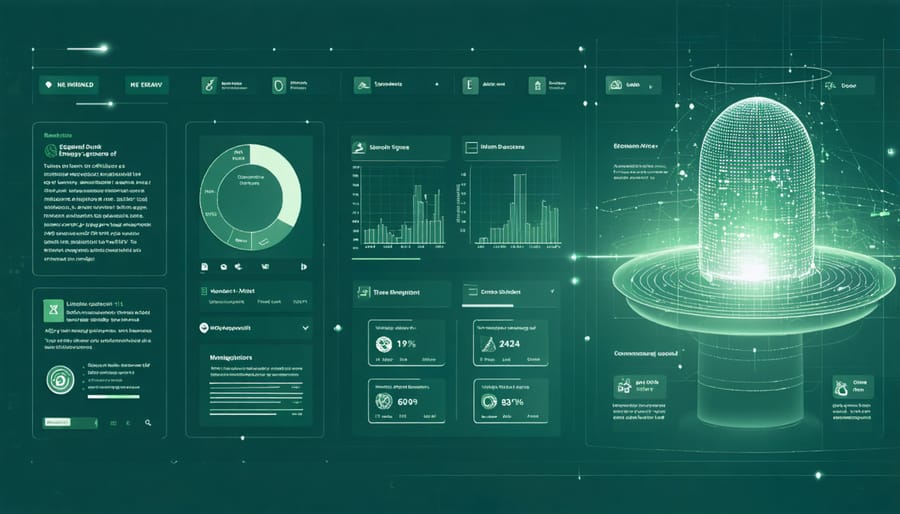
AI-Powered Energy Management Systems
Predictive Maintenance Technology
Predictive maintenance technology, powered by artificial intelligence and machine learning algorithms, represents a significant advancement in sustainable building operations. These sophisticated systems continuously monitor building components through a network of IoT sensors, analyzing performance patterns to detect potential failures before they occur.
By leveraging real-time data analysis, predictive maintenance platforms can identify energy inefficiencies, optimize HVAC operations, and reduce unnecessary power consumption. For example, the implementation of these systems at the Bloomberg European Headquarters in London resulted in a 35% reduction in maintenance-related energy waste within the first year.
Industry experts estimate that predictive maintenance can reduce energy consumption by 10-15% compared to traditional maintenance approaches. The technology utilizes machine learning models that become increasingly accurate over time, learning from historical performance data to fine-tune predictions and maintenance schedules.
Recent developments include integration with building management systems (BMS) and the ability to automatically adjust system parameters based on predicted outcomes. These capabilities not only prevent equipment failures but also optimize energy usage patterns, resulting in reduced carbon emissions and lower operational costs. Construction firms implementing these solutions report average annual energy savings of $0.50-$0.75 per square foot in commercial buildings.
Smart Grid Integration
Smart grid integration represents a significant advancement in building energy management, enabling two-way communication between buildings and utility providers. This sophisticated system allows buildings to respond dynamically to grid conditions, optimizing energy consumption and costs while supporting grid stability.
Modern building management systems (BMS) incorporate advanced metering infrastructure (AMI) that provides real-time data on energy usage patterns. These systems enable demand response programs, where buildings can automatically adjust their energy consumption during peak demand periods, helping to prevent grid overload and reduce operational costs.
Recent implementations have demonstrated significant benefits, with commercial buildings achieving 15-20% reduction in peak energy demand through smart grid integration. For example, a 50-story office building in Singapore implemented smart grid technology, resulting in annual energy savings of approximately $400,000 while contributing to grid resilience.
Key components of smart grid integration include automated load management systems, power quality monitoring, and distributed energy resource integration. These systems work cohesively to balance on-site generation, storage, and grid power consumption, creating a more resilient and efficient energy ecosystem.
The technology also facilitates the integration of renewable energy sources, enabling buildings to optimize their use of solar, wind, and other sustainable power sources based on real-time grid conditions and energy prices.
Circular Construction Methods
Design for Deconstruction
Design for Deconstruction (DfD) represents a paradigm shift in sustainable construction, incorporating modular construction techniques that facilitate the eventual recovery and reuse of building materials. This approach addresses the entire lifecycle of a structure, from initial assembly to final dismantling, ensuring that valuable resources can be efficiently reclaimed and repurposed.
Key elements of DfD include mechanical connections instead of adhesive bonds, standardized component sizes, and clearly documented material specifications. These features enable building elements to be easily separated, sorted, and salvaged when a structure reaches the end of its intended use. For example, bolt-connected steel frameworks can be disassembled with minimal damage, while prefabricated wall panels can be removed intact for immediate reuse in other projects.
Leading construction firms have reported up to 90% material recovery rates using DfD principles, compared to traditional demolition methods that typically achieve only 30-40% recovery. Furthermore, buildings designed for deconstruction have demonstrated 15-20% lower end-of-life management costs.
The implementation of DfD principles requires careful planning during the design phase, including detailed documentation of assembly methods and materials used. This information becomes invaluable during the eventual deconstruction process, ensuring maximum resource recovery and minimal waste generation. As circular economy principles gain traction in the construction industry, DfD is increasingly recognized as a crucial strategy for sustainable development.
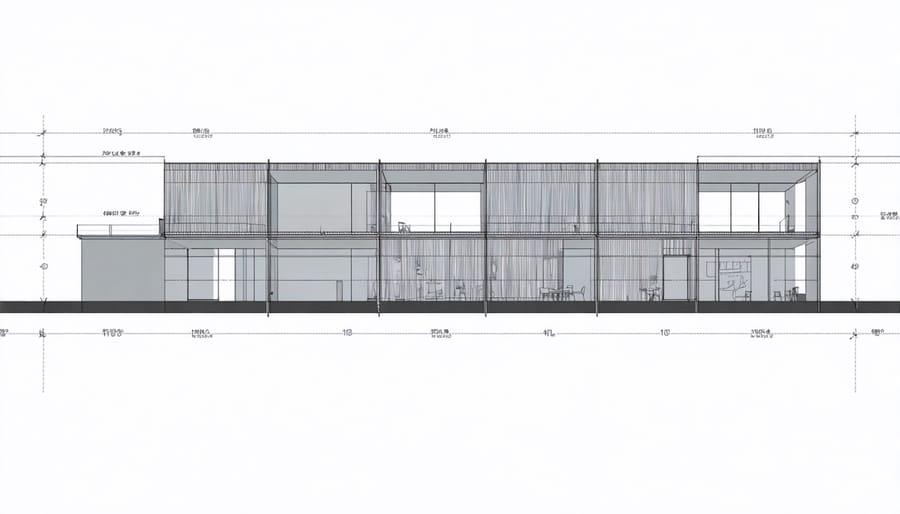
Waste-to-Resource Innovation
The construction industry is witnessing a paradigm shift in waste management through innovative technologies that transform debris into valuable resources. Advanced material recovery facilities now employ AI-powered sorting systems and specialized crushing equipment to process construction waste with unprecedented precision, achieving recovery rates of up to 95%.
Concrete recycling has evolved significantly, with new chemical processes enabling the separation of cement paste from aggregates, producing high-grade materials suitable for new concrete production. This technology reduces landfill waste while decreasing the demand for virgin materials by up to 40%.
Recent developments in mineral carbonation technology allow crushed concrete waste to capture CO2, effectively creating carbon-negative construction materials. Several pioneering projects in Europe have demonstrated that this process can sequester up to 20kg of CO2 per ton of processed waste.
Glass and ceramic waste are being transformed into high-performance pozzolanic materials through advanced grinding and activation processes. These materials serve as partial cement replacements, reducing both waste and carbon emissions in new construction projects.
Construction companies implementing these waste-to-resource technologies report average cost savings of 15-25% on material expenses, while meeting increasingly stringent environmental regulations. The market for recovered construction materials is projected to reach $142 billion by 2025, driven by growing demand for sustainable building materials and circular economy initiatives.
Case Study: The Future in Action
The Edge in Amsterdam stands as a testament to what’s possible when innovative sustainable design meets cutting-edge technology. This 40,000-square-meter commercial building, completed in 2015, has maintained its position as one of the world’s most sustainable office buildings, achieving the highest BREEAM sustainability score ever recorded: 98.36%.
The project showcases multiple integrated urban sustainability solutions, starting with its energy-positive design. The building generates more electricity than it consumes through a combination of solar panels, geothermal energy storage, and rainwater harvesting systems. Over 28,000 sensors monitor occupancy, movement, lighting levels, humidity, and temperature, creating a responsive environment that adjusts in real-time to occupant needs.
The building’s envelope employs triple-glazed windows with automated solar shading, significantly reducing heating and cooling demands. LED lighting panels, connected to Ethernet-powered cables, reduce energy consumption by 80% compared to conventional systems. These panels work in tandem with the building’s IoT platform, adjusting brightness based on natural light availability and occupancy patterns.
What sets The Edge apart is its holistic approach to sustainability. The structure utilizes recycled and sustainable materials throughout, including concrete with recycled aggregate and FSC-certified timber. Rainwater collection systems supply water for toilet flushing and irrigation, while gray water is recycled for additional uses, reducing water consumption by 70%.
The results speak volumes: energy consumption is 70% lower than typical office buildings, while productivity and employee satisfaction have increased significantly. The project’s success has influenced numerous developments worldwide, proving that sustainable design can deliver both environmental and economic benefits.
Key performance metrics include:
– Net-zero energy consumption
– 70% reduction in water usage
– 98.36% BREEAM certification score
– €2.5 million annual energy cost savings
– 60% reduction in maintenance costs
– 25% increase in workplace productivity
The Edge demonstrates that sustainable construction isn’t just about environmental responsibility—it’s about creating intelligent, efficient spaces that enhance user experience while delivering substantial operational cost savings. This project has become a blueprint for future commercial developments, showing how integrated technology and sustainable design can create buildings that are both environmentally responsible and commercially successful.
The construction industry stands at a pivotal moment in its evolution toward sustainability. The innovative solutions discussed throughout this article demonstrate that sustainable construction is not just an environmental imperative but a commercially viable path forward. From advanced materials and smart building technologies to renewable energy integration and waste reduction systems, these innovations are reshaping how we approach construction projects.
Industry data shows that early adopters of these sustainable solutions are already seeing significant returns on investment, with average energy savings of 30-50% and substantial reductions in carbon emissions. The success of projects implementing these innovations has created a ripple effect, influencing building codes, industry standards, and client expectations across the sector.
Looking ahead, we can expect continued acceleration in sustainable innovation. Emerging technologies like artificial intelligence and advanced robotics will further optimize resource usage and construction processes. The integration of circular economy principles is likely to become standard practice, while new materials science breakthroughs will continue to push the boundaries of what’s possible in sustainable construction.
For construction professionals, staying informed and adaptable to these changes is crucial. The transition to sustainable practices is no longer optional but essential for maintaining competitiveness in an evolving market. As regulatory pressures increase and client demands evolve, those who embrace these innovations today will be better positioned to lead the industry tomorrow.