Project procurement management stands as the cornerstone of construction project success, orchestrating the complex process of acquiring goods, services, and resources essential for project completion. In today’s dynamic construction landscape, achieving successful procurement management requires a strategic blend of planning, execution, and control measures that align with project objectives while maintaining cost-effectiveness.
As a formalized discipline within project management, procurement management encompasses vendor selection, contract administration, and supply chain oversight—critical elements that directly impact project timelines, budgets, and quality outcomes. Industry leaders recognize it as the systematic approach to planning purchases and acquisitions, from initial vendor evaluation through contract closure, ensuring every resource acquisition supports project deliverables efficiently.
This strategic framework not only safeguards project investments but also establishes clear accountability measures, risk management protocols, and quality control standards throughout the procurement lifecycle. For construction professionals, mastering procurement management principles becomes increasingly crucial as projects grow in complexity and scale, demanding more sophisticated approaches to resource acquisition and vendor relationships.
The Core Elements of Project Procurement Management
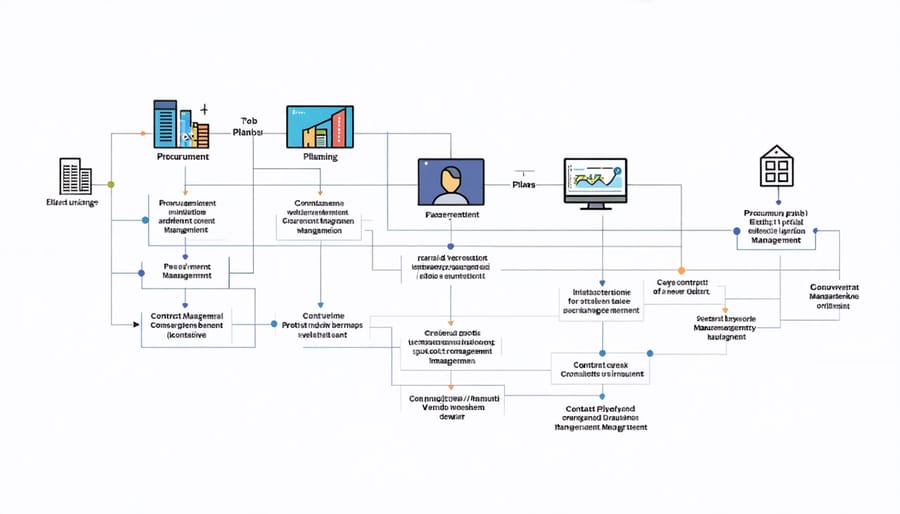
Planning and Strategy Development
Project procurement management planning begins with a thorough analysis of project requirements and objectives. This critical phase involves identifying what needs to be procured, when items are needed, and how they will be acquired. A comprehensive procurement strategy should outline vendor selection criteria, contract types, risk allocation, and timeline considerations.
Key strategic elements include market analysis to understand supplier capabilities and pricing trends, evaluation of make-or-buy decisions, and assessment of potential procurement risks. Construction professionals must consider factors such as material availability, lead times, regulatory requirements, and budget constraints while developing their procurement strategy.
The planning process typically involves creating detailed procurement documentation, including statements of work (SOW), request for proposals (RFP), and evaluation criteria. Project teams should establish clear procurement procedures, defining roles and responsibilities, approval processes, and quality control measures.
Successful procurement planning requires collaboration between project stakeholders, including architects, engineers, and financial controllers. The strategy should align with overall project objectives while maintaining flexibility to adapt to changing market conditions or project requirements. Regular review and updates of the procurement strategy ensure its continued effectiveness throughout the project lifecycle.
Vendor Selection and Management
Effective vendor selection and management forms the cornerstone of successful project procurement. The process begins with establishing clear evaluation criteria, including financial stability, technical capabilities, past performance, and industry reputation. Construction professionals should develop a comprehensive scoring matrix that weighs these factors according to project-specific requirements.
Key evaluation metrics typically include pricing competitiveness, quality management systems, safety records, and resource availability. When assessing potential vendors, it’s crucial to verify their licenses, certifications, and insurance coverage to ensure compliance with industry standards and regulations.
Once vendors are selected, relationship management becomes paramount. This involves regular performance reviews, clear communication channels, and established dispute resolution procedures. Successful vendor management requires maintaining detailed documentation of all interactions, deliverables, and performance metrics.
Construction firms should implement a vendor rating system that tracks key performance indicators (KPIs) such as on-time delivery, quality compliance, and responsiveness to issues. This data helps inform future procurement decisions and enables continuous improvement in vendor relationships. Regular vendor audits and feedback sessions ensure alignment with project goals and maintain quality standards throughout the procurement lifecycle.
Key Processes in Construction Procurement Management
Contract Administration
Contract administration forms a critical component of project procurement management, encompassing various contract types and management procedures essential for successful project delivery. The selection of appropriate contract types – including fixed-price, cost-reimbursable, and time-and-materials agreements – directly impacts project outcomes and aligns with broader cost management strategies.
Effective contract negotiation requires thorough understanding of scope, deliverables, and risk allocation between parties. Construction professionals must establish clear terms and conditions, payment schedules, and performance metrics while ensuring compliance with regulatory requirements and industry standards. The negotiation process should address potential change orders, dispute resolution mechanisms, and warranty provisions.
Contract management procedures involve systematic monitoring of contractor performance, documentation of deliverables, and management of contract modifications. This includes regular progress reviews, quality assurance checks, and verification of compliance with contractual obligations. Professional contract administrators must maintain detailed records of all communications, changes, and approvals throughout the project lifecycle.
Risk management within contract administration requires proactive identification and mitigation of potential issues, including schedule delays, cost overruns, and quality concerns. Successful contract administration also depends on establishing clear lines of communication between all stakeholders and maintaining transparent reporting mechanisms to track contract performance and milestone achievements.
Risk Management in Procurement
Effective risk management in procurement requires a systematic approach to identifying, assessing, and mitigating potential threats throughout the procurement lifecycle. In construction projects, procurement risks typically manifest in several key areas: supplier reliability, cost volatility, quality control, delivery delays, and contractual disputes.
To manage these risks effectively, organizations should implement a comprehensive risk assessment matrix that evaluates both the likelihood and potential impact of each risk factor. This includes conducting thorough vendor due diligence, establishing clear performance metrics, and maintaining detailed documentation of all procurement activities.
Common risk mitigation strategies include:
– Developing relationships with multiple qualified suppliers to reduce dependency
– Including appropriate contingency clauses in contracts
– Implementing regular supplier performance monitoring systems
– Establishing clear quality control protocols
– Maintaining adequate insurance coverage
– Creating detailed dispute resolution procedures
Financial risks can be managed through careful contract structuring, including provisions for price escalation, payment terms, and performance bonds. Quality-related risks are typically addressed through strict specification requirements and regular inspections throughout the procurement process.
Regular risk reviews and updates to procurement strategies ensure that mitigation measures remain effective and relevant. This dynamic approach allows organizations to adapt to changing market conditions while maintaining project objectives and protecting stakeholder interests.
Quality Control and Compliance
Quality control in procurement management requires a systematic approach to ensure materials, services, and contractors meet specified standards while complying with regulatory requirements. This involves implementing robust inspection protocols, establishing clear acceptance criteria, and maintaining comprehensive documentation throughout the procurement process.
Key quality assurance measures include pre-qualification assessments of vendors, regular performance evaluations, and systematic inspection of delivered materials or services. Construction professionals should establish detailed quality metrics aligned with project specifications and industry standards, incorporating these requirements into procurement contracts and vendor agreements.
Regulatory compliance encompasses adherence to local building codes, environmental regulations, safety standards, and labor laws. Procurement managers must ensure all vendors and contractors maintain current certifications, licenses, and insurance coverage as required by jurisdiction. This includes monitoring compliance with sustainability requirements, worker safety regulations, and fair labor practices.
Documentation plays a crucial role in quality control and compliance. Maintain detailed records of:
– Vendor certifications and qualifications
– Material testing results and inspection reports
– Non-conformance reports and corrective actions
– Regulatory submissions and approvals
– Safety compliance documentation
– Quality control test results
Regular audits of procurement processes help identify potential compliance gaps and opportunities for improvement. Establishing a clear chain of responsibility for quality control measures ensures consistent implementation across all procurement activities, ultimately contributing to project success and risk mitigation.
Technology and Innovation in Modern Procurement
Digital Procurement Solutions
Modern procurement management has been transformed by digital solutions that streamline processes and enhance efficiency. Cloud-based procurement platforms enable real-time collaboration, automated workflows, and enhanced visibility across the supply chain. These systems integrate seamlessly with existing project management software, offering features like vendor management, contract lifecycle management, and automated purchase order processing.
AI-powered procurement solutions are increasingly being adopted to analyze spending patterns, predict material needs, and optimize supplier selection. These tools leverage machine learning algorithms to identify cost-saving opportunities and minimize procurement risks.
E-procurement systems have revolutionized traditional buying processes by digitalizing everything from requisition to payment. Key features include electronic bidding platforms, digital signature capabilities, and automated compliance checking. Construction firms are particularly benefiting from integrated materials tracking systems that provide real-time updates on deliveries and inventory levels.
Mobile applications have further enhanced procurement efficiency by allowing on-site teams to initiate purchase requests, approve orders, and track deliveries directly from their devices. This mobility ensures continuous procurement operations even when key stakeholders are away from their desks.
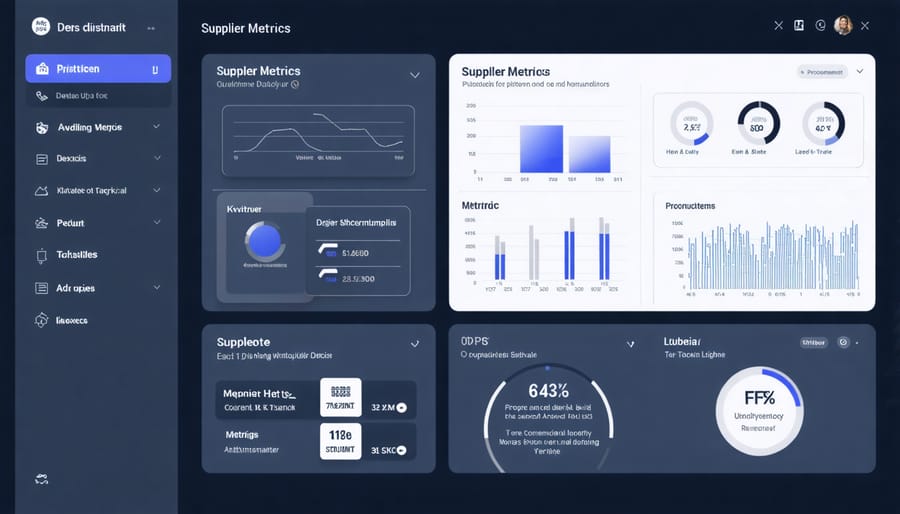
Sustainable Procurement Practices
In today’s construction industry, sustainable procurement practices have become increasingly critical for project success and environmental responsibility. Organizations must balance cost-effectiveness with environmental stewardship when sourcing materials and services. This involves evaluating suppliers based on their environmental certifications, waste management protocols, and commitment to sustainable practices.
Key considerations include selecting materials with recycled content, minimal environmental impact, and local sourcing to reduce transportation emissions. Projects should prioritize vendors who demonstrate responsible resource management and maintain transparent sustainability reporting. Implementation of green procurement policies often includes lifecycle cost analysis, which considers not just initial purchase prices but long-term environmental impacts and disposal costs.
Successful sustainable procurement requires establishing clear environmental criteria in RFPs and contracts, monitoring supplier compliance, and maintaining documentation of sustainable practices. Many organizations now utilize sustainability rating systems and environmental management standards (such as ISO 14001) to evaluate and select vendors. This approach not only supports environmental goals but often leads to cost savings through reduced waste, improved efficiency, and enhanced project reputation.
Construction firms should develop comprehensive sustainable procurement guidelines that align with both project objectives and broader environmental commitments, ensuring long-term value creation for all stakeholders.
Measuring Procurement Success
Performance Metrics
Effective procurement management relies heavily on measurable performance indicators that enable project managers to evaluate supplier performance, cost efficiency, and process effectiveness. Key performance metrics in construction procurement typically include:
Delivery Performance measures the percentage of materials delivered on time and in full (OTIF). Industry standards typically aim for a 95% or higher OTIF rate to maintain project schedules and prevent costly delays.
Cost Variance Analysis tracks the difference between budgeted and actual procurement costs, including both direct material costs and associated handling expenses. Successful projects typically maintain variances within ±5% of the original budget.
Quality Compliance Rate evaluates the percentage of received materials meeting specified quality standards. This metric should maintain a minimum threshold of 98% to ensure project integrity and minimize rework.
Supplier Response Time measures the average duration between purchase order submission and supplier confirmation. Best practices suggest a maximum 24-hour response window for standard orders and 4 hours for urgent requests.
Purchase Order Accuracy tracks the percentage of error-free purchase orders, including specifications, quantities, and delivery requirements. Industry leaders maintain accuracy rates above 97%.
Contract Compliance measures adherence to negotiated terms, including pricing, payment terms, and service levels. Regular audits should demonstrate at least 95% compliance across all active contracts.
Procurement Cycle Time evaluates the total duration from requisition to delivery, with top-performing organizations achieving average cycles of 10-15 days for standard orders in construction projects.
These metrics should be regularly monitored and reported through procurement management software or dedicated tracking systems, enabling data-driven decision-making and continuous process improvement.
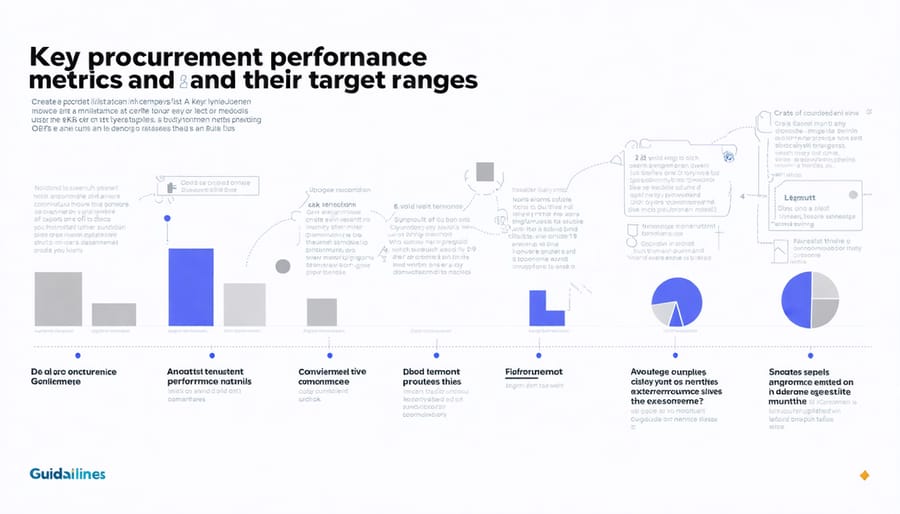
Best Practices and Common Pitfalls
Successful project procurement management hinges on following established project management best practices while avoiding common pitfalls that can derail construction projects. Key best practices include maintaining detailed documentation of all procurement decisions, establishing clear evaluation criteria before vendor selection, and implementing robust change management procedures.
Industry experience shows that successful procurement managers consistently conduct thorough market research, develop comprehensive risk management strategies, and maintain strong supplier relationships. Regular vendor performance evaluations and transparent communication channels are essential for maintaining project momentum.
Common pitfalls to avoid include rushing the vendor selection process, neglecting to perform adequate due diligence, and failing to align procurement strategies with overall project objectives. Construction professionals should be particularly vigilant about incomplete contract documentation, inadequate risk allocation, and poor scope definition, as these issues frequently lead to disputes and cost overruns.
Another critical mistake is overlooking the importance of procurement timing. Late procurement decisions can cause significant project delays and increased costs. Additionally, failing to consider local market conditions and supply chain constraints can result in unrealistic expectations and missed deadlines.
To ensure success, maintain a balanced approach between cost optimization and quality requirements, while fostering collaborative relationships with suppliers and stakeholders. Regular monitoring and adjustment of procurement strategies helps maintain project alignment and ensures optimal outcomes.
Project procurement management stands as a cornerstone of successful construction project delivery, integrating strategic planning, supplier relationships, and risk management into a cohesive framework. Throughout this exploration, we’ve seen how effective procurement management directly impacts project outcomes, cost efficiency, and timeline adherence.
The key takeaways emphasize that successful procurement management requires a systematic approach, from initial planning and vendor selection to contract administration and closure. Construction professionals must maintain a delicate balance between cost optimization and quality assurance while ensuring compliance with regulatory requirements and industry standards.
The evolution of procurement management, particularly with the integration of digital tools and sustainable practices, demonstrates its dynamic nature in modern construction. Organizations that embrace these advancements while maintaining strong fundamental procurement principles position themselves for greater project success.
For construction industry leaders, the message is clear: investing in robust procurement management systems and developing skilled procurement teams is not optional but essential for competitive advantage. The return on investment manifests in reduced risks, improved supplier relationships, better cost control, and enhanced project delivery capabilities.
As the construction industry continues to evolve, procurement management will remain a critical function that demands ongoing attention, refinement, and innovation. Success in this domain requires commitment to best practices, continuous learning, and adaptation to emerging trends and technologies.