Implement real-time cost tracking systems across all project phases to detect variances within 24 hours of occurrence, enabling immediate corrective action. Establish comprehensive baseline estimates incorporating detailed quantity takeoffs, current market rates, and risk contingencies before breaking ground. Master cost management fundamentals through rigorous change order protocols and value engineering strategies that maintain project scope while reducing unnecessary expenditures.
Construction cost overruns, averaging 28% globally, threaten project viability and stakeholder relationships. Yet systematic cost control measures, when properly implemented, consistently deliver projects within 3% of initial budgets. This precision requires integrating advanced monitoring technologies, lean construction principles, and proactive risk management strategies throughout the project lifecycle.
Modern construction demands sophisticated cost control approaches that balance innovation with fiscal responsibility. Digital twin technology, predictive analytics, and real-time financial reporting now enable unprecedented visibility into project expenses, transforming traditional cost management into a dynamic, data-driven discipline essential for project success.
Establishing Effective Cost Control Systems
Budget Development and Baseline Setting
Effective budget development and baseline setting form the foundation of successful cost control in construction projects. The process begins with a comprehensive analysis of project scope, including detailed quantity takeoffs, material specifications, and labor requirements. Project managers must consider both direct costs, such as materials and labor, and indirect costs like overhead, insurance, and contingencies.
A crucial aspect of budget development is the implementation of smart procurement strategies that optimize resource allocation and minimize waste. Historical data from similar projects serves as a valuable reference point, while current market conditions and regional cost variations must be factored into the calculations.
The establishment of cost baselines requires careful consideration of project phasing and milestone-based financial planning. Industry best practices recommend allocating contingency funds of 5-10% for standard projects and up to 15% for complex or high-risk endeavors. These baselines should be documented in a detailed cost management plan that includes specific metrics for performance measurement and variance analysis.
Cost estimation tools and software can enhance accuracy, but human expertise remains essential for validating assumptions and adjusting forecasts based on project-specific factors. Regular review and refinement of these baselines ensure they remain relevant throughout the project lifecycle, particularly during the pre-construction and early construction phases when cost certainty is still evolving.
Cost Breakdown Structure Implementation
A Cost Breakdown Structure (CBS) provides a systematic framework for organizing and tracking project costs across all construction components. The implementation begins with dividing the project into manageable cost centers, typically aligned with work packages and major deliverables. Each cost center should be assigned a unique code that integrates with the project’s Work Breakdown Structure (WBS).
The CBS should be established during the pre-construction phase and incorporate direct costs (labor, materials, equipment), indirect costs (overhead, supervision), and contingency allowances. Project managers must ensure that cost codes are consistently applied across all project documentation, including purchase orders, invoices, and progress reports.
Modern construction management software facilitates CBS implementation through automated cost tracking and real-time reporting capabilities. This technology enables project teams to monitor costs at various levels of detail, from individual work packages to overall project performance.
Key implementation steps include:
– Developing a hierarchical cost coding system
– Establishing cost baseline estimates for each component
– Creating standardized reporting templates
– Setting up approval workflows for cost-related transactions
– Implementing regular cost review meetings
Regular monitoring and updates to the CBS ensure that cost variances are identified early and corrective actions can be implemented promptly. The system should be flexible enough to accommodate project changes while maintaining consistent cost tracking throughout the project lifecycle.
Real-Time Cost Monitoring and Analysis
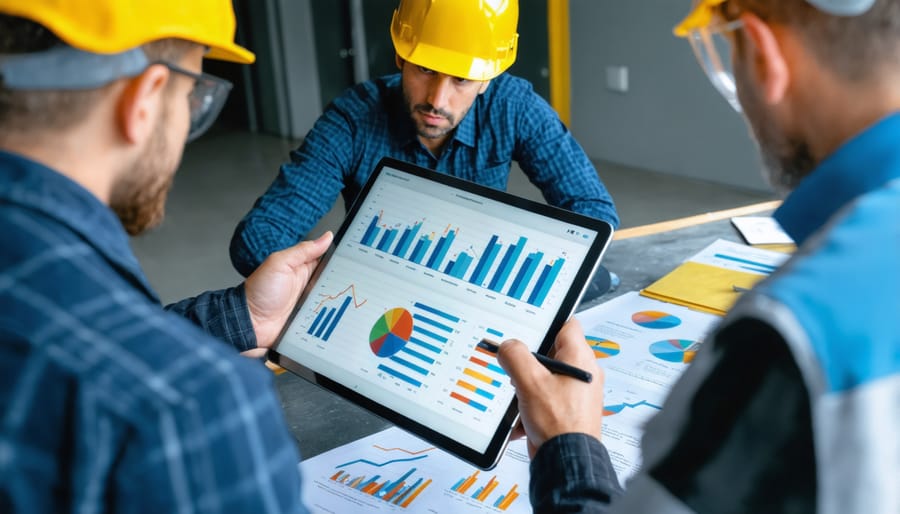
Digital Tools and Software Solutions
Modern construction projects benefit significantly from digital tools and software solutions designed specifically for cost control and management. Project management platforms like Procore, PlanGrid, and Autodesk BIM 360 offer comprehensive features for budget tracking, cost forecasting, and real-time financial monitoring. These platforms integrate various aspects of construction management, from document control to change order management, providing a centralized system for cost-related decisions.
Cloud-based construction accounting software enables real-time financial tracking and reporting, allowing project managers to monitor expenses, labor costs, and material usage instantly. Advanced solutions like AI-powered cost monitoring tools can analyze historical data to predict cost overruns and suggest preventive measures before issues escalate.
Enterprise Resource Planning (ERP) systems tailored for construction businesses help integrate various operational aspects, including procurement, inventory management, and financial control. These systems provide valuable insights through data analytics and customizable dashboards, enabling better decision-making and cost optimization.
Mobile applications have revolutionized on-site cost tracking, allowing field teams to record expenses, track material deliveries, and manage timesheets directly from their devices. This real-time data collection minimizes errors and delays in cost reporting while improving accountability across the project team.
Building Information Modeling (BIM) software with integrated cost estimation capabilities helps teams visualize project costs during the design phase, enabling better cost planning and reducing expensive changes during construction. These tools also facilitate quantity takeoffs and material cost calculations, streamlining the estimation process and improving accuracy.
Key Performance Indicators (KPIs)
Effective cost control in construction projects relies on monitoring specific Key Performance Indicators (KPIs) that provide insights into project financial health and performance. The most critical KPIs include Cost Performance Index (CPI), which measures the efficiency of resources utilized by comparing earned value to actual costs. A CPI greater than 1.0 indicates the project is under budget, while values below 1.0 signal cost overruns.
Schedule Performance Index (SPI) complements CPI by tracking progress against planned timelines, as delays often correlate with increased costs. Project managers should monitor Variance at Completion (VAC) to forecast final cost variations from the original budget, enabling proactive corrective measures.
Cost variance percentage, calculated by comparing actual costs to budgeted amounts, helps identify specific areas requiring attention. The burn rate, which tracks the speed of budget consumption, provides early warnings of potential overruns. Return on Investment (ROI) and Net Present Value (NPV) offer broader perspectives on project financial viability.
Productivity metrics, such as units completed per labor hour and equipment utilization rates, directly impact cost performance. Change order tracking is essential, measuring both the frequency and financial impact of scope modifications. Materials waste percentage and procurement cost variance help optimize resource allocation and purchasing strategies.
Regular monitoring of these KPIs through integrated project management systems enables data-driven decision-making. Construction managers should establish baseline metrics at project initiation and conduct weekly or monthly reviews to identify trends and implement corrective actions promptly. Success thresholds should be clearly defined, with escalation protocols for metrics falling outside acceptable ranges.
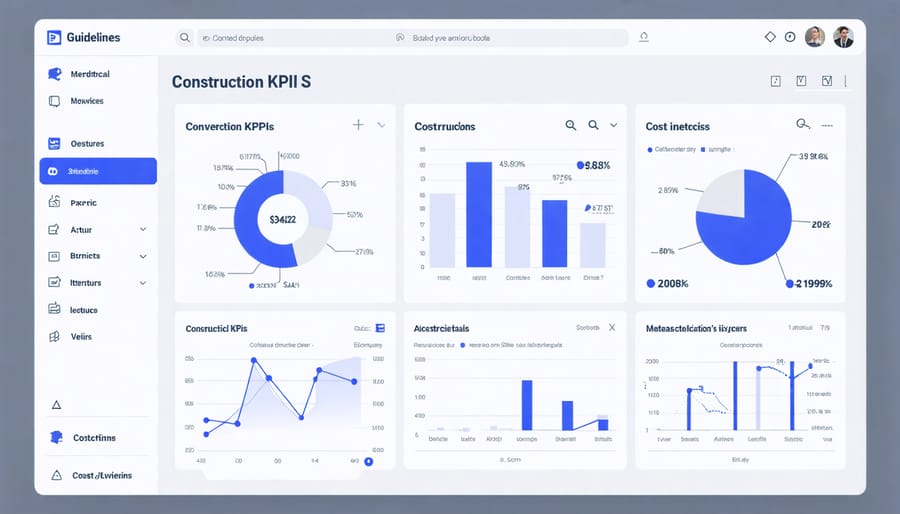
Proactive Cost Control Measures
Risk Assessment and Mitigation
Effective risk assessment and mitigation are crucial components of construction cost control. The process begins with systematic identification of potential cost risks through detailed project analysis, historical data review, and expert consultation. Common risk factors include material price fluctuations, labor shortages, weather delays, regulatory changes, and unforeseen site conditions.
Once identified, risks should be categorized based on their probability and potential impact on project costs. This assessment enables project teams to prioritize risks and allocate resources effectively. High-priority risks typically require immediate attention and comprehensive mitigation strategies, while lower-priority risks may be monitored with basic contingency plans.
Successful mitigation strategies often include:
– Establishing contingency reserves based on quantitative risk analysis
– Implementing contractual risk-sharing arrangements with suppliers and subcontractors
– Developing alternative procurement strategies for critical materials
– Creating flexible scheduling to accommodate potential delays
– Maintaining comprehensive insurance coverage
– Implementing robust change management procedures
Regular risk review meetings should be conducted throughout the project lifecycle to assess the effectiveness of mitigation strategies and identify emerging risks. Documentation of risk-related decisions and outcomes helps build organizational knowledge for future projects.
It’s essential to maintain a balanced approach between risk mitigation costs and potential impact. Over-investment in risk mitigation can be as detrimental to project economics as inadequate risk management. The key is finding the optimal balance through careful analysis and experienced judgment.
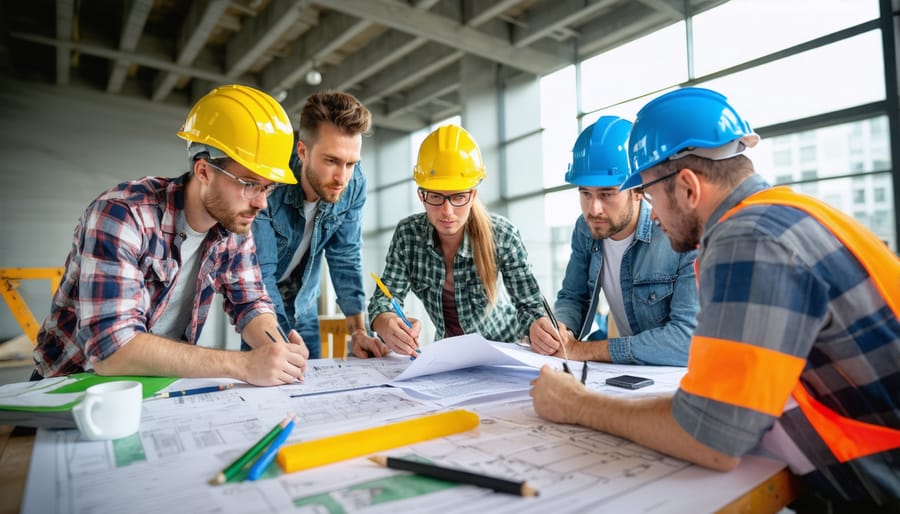
Change Order Management
Effective change order management is crucial for maintaining cost control throughout project management phases. A robust change order system begins with establishing clear procedures for identifying, documenting, and approving scope changes. This process should include detailed cost impact analysis, schedule implications, and required approvals before implementation.
Key elements of successful change order management include:
– Immediate documentation of proposed changes
– Detailed cost estimation of direct and indirect impacts
– Timeline analysis for implementation
– Risk assessment of the proposed modifications
– Formal approval process with designated authority levels
To minimize cost overruns, implement a standardized change order form that captures essential information such as the change description, justification, cost breakdown, and schedule impact. This documentation serves as a crucial reference point for project stakeholders and helps prevent disputes.
Establish clear communication channels between all parties involved, including contractors, subcontractors, and clients. Regular meetings to review pending change orders ensure timely decisions and prevent work delays. Consider implementing a digital change order tracking system to streamline the process and maintain accurate records.
Set up a change order contingency fund during the initial project planning stage to accommodate legitimate scope changes without derailing the overall budget. This proactive approach helps maintain financial stability while allowing necessary project modifications.
Value Engineering Opportunities
Value engineering presents significant opportunities for cost reduction while maintaining project quality and functionality. This systematic approach involves analyzing project components and exploring alternative solutions that optimize value without compromising performance.
Key opportunities include material substitution, where traditional materials can be replaced with more cost-effective alternatives that meet or exceed specifications. For example, using precast concrete elements instead of cast-in-place concrete can reduce labor costs and accelerate construction schedules while maintaining structural integrity.
Design optimization offers another avenue for cost savings. This might involve simplifying complex architectural features, standardizing building components, or revising structural systems to achieve the same performance with less material. Mechanical and electrical systems often present substantial value engineering opportunities through equipment selection, system configuration, and energy efficiency improvements.
Construction methodology alternatives should also be evaluated. Modern construction techniques, such as modular construction or prefabrication, can significantly reduce on-site labor costs and project duration. These approaches often result in better quality control and fewer material waste.
Timing is crucial in value engineering. The greatest potential for cost savings occurs during the early design phases, where changes can be implemented with minimal impact on project schedule and existing work. However, opportunities should be continuously evaluated throughout the project lifecycle, with careful consideration of long-term operational costs alongside initial savings.
Successful value engineering requires collaboration between project stakeholders, including designers, contractors, and suppliers, to identify and implement innovative solutions that benefit the project’s bottom line while meeting all performance requirements.
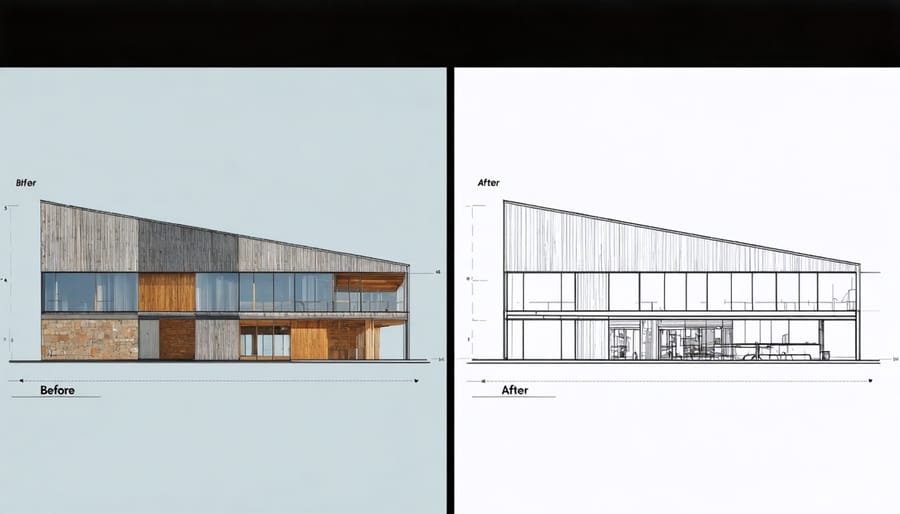
Case Study: Successful Cost Control Implementation
The Gateway Towers project in Singapore serves as a compelling example of successful cost control implementation in modern construction. This $280 million mixed-use development, completed in 2022, demonstrated how strategic cost control measures could save 15% of the initial budget while maintaining project quality and timeline objectives.
The project team implemented a comprehensive cost control system from the outset, focusing on three key areas: procurement optimization, real-time monitoring, and proactive risk management. The procurement strategy involved early contractor involvement (ECI) and bulk purchasing agreements, which resulted in a 12% reduction in material costs compared to market rates.
Digital tools played a crucial role in the project’s success. The team utilized Building Information Modeling (BIM) integrated with cost management software to track expenses in real-time. This integration enabled project managers to identify cost variances immediately and implement corrective actions before minor issues escalated into major problems.
A significant challenge arose when steel prices increased by 30% during the construction phase. The project team responded by:
– Reviewing and optimizing structural designs without compromising integrity
– Negotiating with suppliers for long-term price agreements
– Accelerating procurement of critical materials
– Implementing value engineering solutions
These measures resulted in containing the impact of price escalation to just 8% of the affected components, significantly below market increases.
The project also established a rigorous change order management process. All proposed changes underwent thorough cost-benefit analysis before approval. This approach resulted in managing change orders to less than 3% of the total project cost, compared to the industry average of 8-10%.
Labor costs were controlled through careful workforce planning and productivity monitoring. The implementation of lean construction principles reduced waste and improved efficiency, leading to a 20% improvement in labor productivity compared to similar projects.
The project’s success can be attributed to:
– Clear communication channels between all stakeholders
– Regular cost performance reviews
– Implementation of earned value management
– Strong documentation and reporting systems
– Proactive risk identification and mitigation
The Gateway Towers project demonstrates that effective cost control requires a combination of strategic planning, technological integration, and responsive management practices. The lessons learned continue to influence cost control practices in similar large-scale construction projects across the region.
Best Practices for Construction Cost Control
Effective cost control in construction projects requires a systematic approach combining proven methodologies with modern technology. Start by establishing a comprehensive cost baseline during the planning phase, incorporating detailed estimates, construction management fees, and contingency allowances.
Implement real-time cost tracking systems to monitor expenses against budgets, utilizing construction management software for accurate data collection and analysis. Regular cost variance analysis should be conducted weekly or bi-weekly, with immediate investigation of significant deviations from planned expenditure.
Maintain stringent change order management protocols, requiring thorough documentation and approval processes for all scope modifications. Create a dedicated cost control team responsible for monitoring, reporting, and implementing corrective actions when necessary.
Establish clear communication channels between stakeholders, ensuring that cost-related information flows efficiently between site management, procurement teams, and project executives. Schedule regular cost review meetings to discuss financial performance and address potential issues proactively.
Utilize value engineering throughout the project lifecycle, particularly during the design and procurement phases. Implement strategic procurement practices, including bulk purchasing and early contractor involvement, to optimize costs without compromising quality.
Maintain detailed documentation of all cost-related decisions and their impacts. Regular cost forecasting should be performed to anticipate potential overruns and implement mitigation strategies early. Finally, conduct post-project cost analysis to identify lessons learned and improve future cost control practices.
Remember that successful cost control requires continuous monitoring, proactive management, and swift corrective action when deviations occur. Regular training and updates on cost control procedures ensure team members remain aligned with project objectives and financial goals.
Effective cost control is fundamental to the success of any construction project, requiring a comprehensive approach that combines strategic planning, continuous monitoring, and proactive management. Throughout this article, we’ve explored essential components of successful cost control, from establishing robust baseline budgets to implementing real-time tracking systems and utilizing advanced technology solutions.
The key to successful cost control lies in creating a balanced framework that incorporates both preventive measures and responsive strategies. This includes detailed initial planning, regular progress monitoring, comprehensive risk management, and the strategic use of modern construction management tools. The implementation of these measures, supported by clear communication channels and standardized reporting procedures, creates a solid foundation for maintaining project costs within defined parameters.
As the construction industry continues to evolve, the importance of adopting sophisticated cost control measures becomes increasingly critical. Organizations that invest in developing comprehensive cost control systems, training their personnel, and leveraging technology will be better positioned to deliver projects successfully and maintain their competitive edge. Remember that effective cost control is not a one-time effort but a continuous process that requires commitment, vigilance, and adaptation throughout the project lifecycle.