Transform construction project outcomes through strategic procurement management fundamentals that integrate digital innovation, risk mitigation, and sustainable practices. Modern construction procurement demands a sophisticated approach that balances cost efficiency with long-term value creation, particularly as global supply chains become increasingly complex and volatile.
Industry leaders leverage integrated project delivery (IPD) methods, real-time analytics, and collaborative contractor relationships to achieve up to 20% cost savings and 30% faster project completion rates. By implementing early contractor involvement (ECI) and advanced supply chain visibility tools, organizations significantly reduce procurement risks while enhancing project predictability.
The construction sector’s shift toward sustainable procurement practices, including circular economy principles and local sourcing strategies, has become a critical differentiator in successful project delivery. Leading firms now evaluate suppliers based on environmental performance metrics, social responsibility standards, and technological capabilities, creating a new paradigm in construction procurement excellence.
These evolutionary changes in procurement strategy require construction professionals to master both traditional negotiation skills and emerging digital tools, while maintaining strict compliance with evolving regulatory frameworks and sustainability requirements. Success in modern construction procurement hinges on this delicate balance between innovation and proven methodologies.
Digital Transformation in Construction Procurement
E-Procurement Systems
Modern construction projects increasingly rely on digital procurement solutions to streamline their purchasing processes and enhance operational efficiency. E-procurement systems have revolutionized how construction companies manage their supplier relationships, tender processes, and procurement workflows.
These platforms offer comprehensive features including automated vendor prequalification, real-time bid management, electronic document exchange, and integrated payment processing. Construction firms utilizing e-procurement systems report average cost savings of 12-18% on procurement operations and a 60% reduction in processing time for purchase orders.
Key benefits include enhanced transparency in supplier selection, standardized bidding procedures, and improved compliance tracking. The digital audit trail created by these systems helps maintain accountability and reduces the risk of errors or fraudulent activities. Additionally, advanced analytics capabilities enable procurement teams to make data-driven decisions about supplier performance and spending patterns.
Integration with Building Information Modeling (BIM) and project management software further enhances the value of e-procurement systems. This interconnectivity allows for automatic material quantity takeoffs, real-time budget tracking, and seamless coordination between design changes and procurement requirements.
For successful implementation, organizations should focus on proper staff training, establishing clear digital workflows, and ensuring system compatibility with existing enterprise software. Regular system updates and maintenance are essential for optimal performance and security.
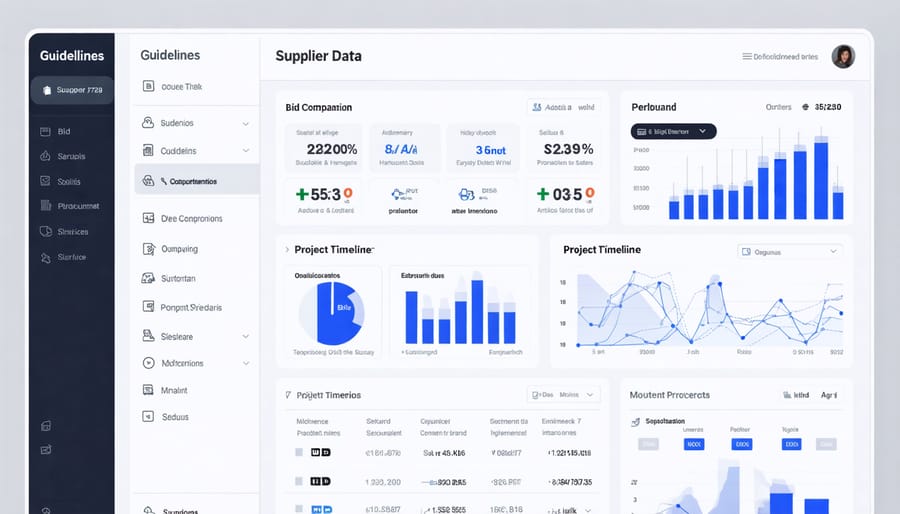
Blockchain for Supply Chain Transparency
Blockchain technology is revolutionizing supply chain transparency in construction procurement, offering an immutable and decentralized system for tracking materials, equipment, and contractual obligations. This innovative approach creates a digital ledger that records every transaction and movement throughout the procurement process, ensuring unprecedented accountability and traceability.
The implementation of blockchain in construction procurement provides several key advantages. First, it enables real-time verification of material sources and quality certifications, reducing the risk of counterfeit or substandard materials entering the supply chain. Second, smart contracts automated through blockchain technology streamline payment processes and ensure contractual compliance, significantly reducing administrative overhead and potential disputes.
Notable applications include tracking sustainable materials from source to site, verifying certifications and compliance documentation, and maintaining comprehensive audit trails for quality assurance. For instance, major construction firms have successfully implemented blockchain solutions to track steel and concrete deliveries, resulting in a 30% reduction in procurement-related delays and disputes.
To implement blockchain effectively, construction companies should focus on:
– Developing standardized data protocols
– Training procurement staff in blockchain operations
– Integrating existing procurement systems with blockchain platforms
– Establishing clear governance structures for data management
While initial implementation costs can be significant, the long-term benefits of enhanced transparency, reduced fraud risk, and improved operational efficiency make blockchain an increasingly valuable tool in modern construction procurement strategies.
Collaborative Procurement Models
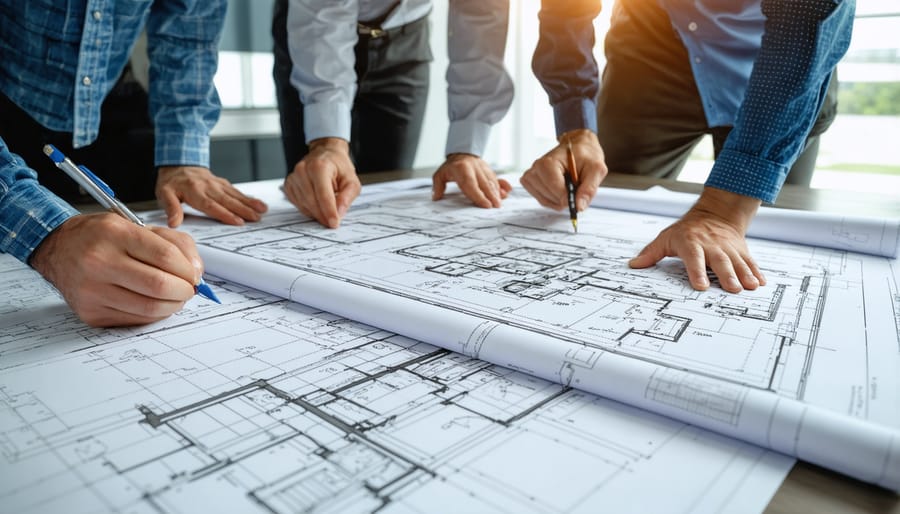
Integrated Project Delivery (IPD)
Integrated Project Delivery (IPD) represents a transformative approach to construction procurement, emphasizing collaboration, shared risk and reward, and early involvement of key stakeholders. This methodology fundamentally restructures traditional procurement relationships by aligning project objectives with team success through multi-party contracts and integrated cost management strategies.
Recent industry data indicates that IPD projects consistently demonstrate improved outcomes, with studies showing up to 15% reduction in overall project costs and 30% faster delivery times compared to traditional procurement methods. The key to IPD’s efficiency lies in its collaborative framework, where designers, contractors, and suppliers work together from the project’s inception, fostering innovation and reducing wasteful processes.
IPD procurement typically involves:
– Early formation of the core project team
– Shared risk/reward structures
– Open-book accounting practices
– Building Information Modeling (BIM) integration
– Collective decision-making protocols
The implementation of IPD requires sophisticated technological infrastructure and a cultural shift toward transparency and trust. Organizations adopting IPD report significant improvements in supply chain efficiency, with enhanced communication channels reducing procurement delays and material waste. However, successful implementation demands careful consideration of team selection, contract structuring, and technology integration.
Leading construction firms have demonstrated IPD’s effectiveness through notable projects. For instance, the Stanford Medical Center expansion project utilized IPD to achieve $20 million in savings through integrated supply chain optimization and collaborative value engineering. This approach particularly benefits complex projects where traditional procurement methods might struggle with coordination and risk management.
Early Contractor Involvement (ECI)
Early Contractor Involvement (ECI) represents a collaborative procurement approach where contractors are engaged during the project’s initial design and planning phases, typically before the final design is complete. This strategy enables contractors to contribute their expertise and practical insights when changes are most cost-effective and easiest to implement.
The primary benefits of ECI include improved constructability, more accurate cost estimates, and reduced risk of design conflicts. By involving contractors early, project teams can identify potential construction challenges and optimize designs before significant resources are committed. This proactive approach often results in shorter project timelines and reduced variation orders during construction.
Implementation of ECI requires careful consideration of several key factors. First, the selection criteria for contractors must emphasize technical capability and collaborative experience rather than just price. Second, clear communication protocols and responsibility matrices must be established to ensure effective integration of contractor input into the design process.
According to industry studies, projects utilizing ECI have demonstrated up to 20% cost savings and 15% shorter delivery times compared to traditional procurement methods. These improvements stem from enhanced supply chain integration, better risk management, and more innovative construction solutions.
However, successful ECI implementation demands a shift in traditional project relationships. Clients must be willing to invest more resources in the early stages, and design teams must be open to contractor input. The contractual framework should also support this collaborative approach, typically through two-stage contracts that clearly define roles, responsibilities, and risk allocation during both the early involvement and construction phases.
For optimal results, ECI should be supported by digital collaboration tools and regular stakeholder workshops to facilitate effective communication and decision-making throughout the project lifecycle.
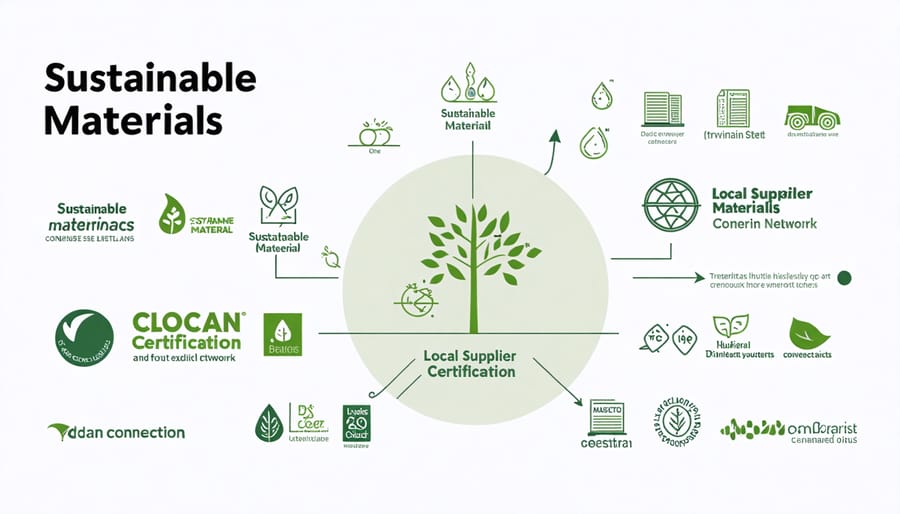
Sustainable Procurement Practices
Green Material Sourcing
Green material sourcing has become a cornerstone of modern construction procurement, driven by environmental regulations, client demands, and corporate sustainability goals. Construction firms are increasingly adopting comprehensive strategies to ensure their material choices align with environmental standards while maintaining project efficiency and cost-effectiveness.
Key to successful green procurement is the implementation of Environmental Product Declarations (EPDs) evaluation systems. These standardized documents provide transparent, verified information about the environmental impact of construction materials throughout their lifecycle. Leading construction firms are now incorporating EPD requirements into their procurement specifications, enabling data-driven decisions about material selection.
Establishing relationships with certified green suppliers forms another crucial component. Organizations should develop a pre-qualified supplier database that includes vendors committed to sustainable practices, recycled content utilization, and responsible resource management. This approach ensures consistent access to environmentally conscious materials while maintaining supply chain reliability.
Material certification programs, such as Forest Stewardship Council (FSC) for timber and LEED-compliant products, serve as valuable benchmarks in the procurement process. Construction companies should establish clear guidelines for minimum certification requirements and regularly audit their supply chain to ensure compliance.
Local sourcing has emerged as a vital strategy, reducing transportation emissions while supporting regional economies. Procurement teams should prioritize materials available within a defined radius when possible, balancing environmental benefits with project requirements and cost considerations.
Local Supply Chain Development
Local supply chain development has emerged as a critical strategy in modern construction procurement, offering numerous advantages for project efficiency and community impact. By establishing strong relationships with local suppliers, contractors can significantly reduce transportation costs, minimize delivery delays, and maintain better control over material quality.
Studies have shown that localizing procurement can reduce lead times by up to 40% while decreasing the project’s carbon footprint through reduced transportation distances. Additionally, engaging local suppliers creates economic multiplier effects, strengthening the regional construction ecosystem and fostering long-term business relationships that benefit future projects.
To develop an effective local supply chain, construction companies should begin by conducting comprehensive market research to identify capable local suppliers and manufacturers. This process includes evaluating supplier capabilities, financial stability, and quality control measures. Implementing vendor development programs can help local suppliers meet specific project requirements and quality standards.
Key strategies for successful local supply chain development include:
– Creating supplier databases with detailed capabilities and performance metrics
– Establishing mentorship programs for local suppliers
– Developing clear communication channels and feedback mechanisms
– Implementing graduated contracting approaches that allow smaller local suppliers to grow their capacity
– Building long-term partnerships through fair pricing and payment terms
For maximum effectiveness, local procurement strategies should be integrated into the early stages of project planning, allowing sufficient time for supplier development and capacity building. This approach ensures that local suppliers can effectively meet project demands while maintaining quality standards and delivery schedules.
Risk Management in Modern Procurement
Data-Driven Supplier Assessment
Modern construction procurement demands a sophisticated approach to supplier assessment, leveraging data analytics to make informed decisions. AI-driven procurement analytics has revolutionized how construction firms evaluate and select their suppliers, moving beyond traditional metrics to incorporate comprehensive performance indicators.
Key performance metrics now include historical delivery times, quality consistency scores, financial stability indices, and sustainability compliance ratings. Construction firms utilize advanced analytics platforms to process this data, creating detailed supplier scorecards that offer objective comparisons across multiple criteria.
Real-time data monitoring enables procurement teams to track supplier performance continuously, identifying potential risks before they impact project timelines. This proactive approach includes analyzing market trends, monitoring supplier financial health, and evaluating capacity constraints.
The implementation of predictive analytics has proven particularly valuable in forecasting supplier reliability and potential disruptions. For instance, leading construction firms report a 30% reduction in supply chain disruptions after implementing data-driven supplier assessment systems.
Integration with enterprise resource planning (ERP) systems allows for automated performance tracking and reporting, streamlining the evaluation process while maintaining accountability. This systematic approach ensures consistent supplier quality while optimizing cost efficiency across construction projects.
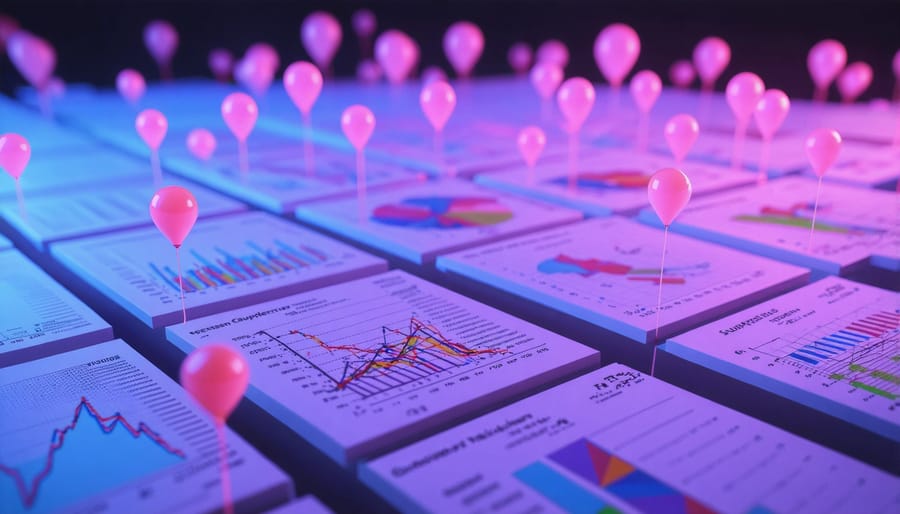
Dynamic Contract Management
Dynamic contract management has emerged as a crucial component of modern strategic procurement framework, enabling construction organizations to adapt to evolving project conditions while maintaining control over risks and costs. This approach involves implementing flexible contractual mechanisms that can accommodate changes in project scope, timeline adjustments, and unforeseen circumstances without compromising project objectives.
Key elements of dynamic contract management include sliding scale pricing models, adjustable performance metrics, and staged delivery options. These mechanisms allow project stakeholders to respond effectively to market fluctuations, supply chain disruptions, and changing client requirements. For instance, incorporating price escalation clauses helps protect both contractors and clients from volatile material costs, while performance-based incentives can be adjusted to reflect evolving project priorities.
Risk allocation in dynamic contracts is particularly noteworthy, as it enables a more balanced distribution of responsibilities between parties. Rather than rigid risk transfer, these contracts facilitate collaborative risk management through shared responsibility matrices and clearly defined trigger events for contract adjustments. This approach has proven especially valuable in complex infrastructure projects where traditional fixed-price contracts might be unsuitable.
Recent industry data suggests that projects utilizing dynamic contract management demonstrate improved outcomes in terms of dispute resolution, cost control, and timeline adherence. The flexibility inherent in these agreements helps maintain positive stakeholder relationships while protecting the interests of all parties involved.
Case Study: Innovation in Action
The transformation of the Denver International Airport’s Terminal Renovation Project stands as a compelling example of innovative procurement strategies in modern construction. In 2018, the airport authority implemented an integrated project delivery (IPD) approach combined with digital procurement solutions, resulting in remarkable outcomes for this $770 million initiative.
The procurement team utilized a cloud-based platform that centralized all vendor communications, bid submissions, and contract management. This digital transformation eliminated paper-based processes, reducing procurement cycle times by 47% and saving approximately $3.2 million in administrative costs. The platform also enabled real-time collaboration between multiple stakeholders, including contractors, suppliers, and project managers.
A key innovation was the implementation of a two-stage procurement process. The first stage involved early contractor involvement (ECI), where selected contractors participated in design development before final pricing. This approach allowed for better risk assessment and value engineering opportunities. The second stage utilized reverse auctions for specific material packages, resulting in a 12% cost reduction compared to traditional bidding methods.
The project team also incorporated blockchain technology for supply chain transparency and smart contracts. This system tracked material deliveries, automated payments upon milestone completion, and maintained an immutable record of all transactions. The result was a 60% reduction in payment processing time and enhanced trust among project participants.
Sustainability was integrated into the procurement strategy through the implementation of a vendor rating system that assessed suppliers’ environmental practices. This approach led to the selection of vendors who could provide locally sourced materials and demonstrate commitment to reducing carbon emissions in their operations.
The project’s success metrics speak volumes: completion three months ahead of schedule, 15% under budget, and zero major disputes between parties. The procurement innovation implemented at Denver International Airport has since become a benchmark for large-scale construction projects, demonstrating how modern procurement strategies can deliver significant value while maintaining quality and compliance requirements.
This case study exemplifies how strategic procurement innovation, when properly implemented, can transform project outcomes and establish new standards for efficiency in construction management.
In today’s rapidly evolving construction landscape, effective procurement strategies have become more crucial than ever. As we’ve explored throughout this article, successful procurement in construction requires a balanced approach that integrates traditional best practices with innovative solutions. The industry’s shift toward digital transformation, collaborative delivery methods, and sustainable practices demonstrates a clear trajectory for future procurement approaches.
Key takeaways indicate that successful procurement strategies must prioritize early stakeholder engagement, robust risk management frameworks, and technological integration. The adoption of Building Information Modeling (BIM), cloud-based procurement platforms, and smart contracts has shown significant potential in streamlining processes and improving project outcomes.
Looking ahead, the construction industry can expect further evolution in procurement practices. Emerging technologies like artificial intelligence and blockchain are poised to revolutionize how construction projects are procured and managed. Sustainability requirements will continue to influence procurement decisions, with increasing emphasis on circular economy principles and environmental impact considerations.
Organizations that embrace these changes while maintaining focus on relationship building, clear communication, and strategic risk allocation will be better positioned for success. The future of construction procurement lies in creating adaptive, resilient strategies that can respond to market dynamics while ensuring project objectives are met efficiently and cost-effectively.
To remain competitive, construction professionals must continue to develop their procurement capabilities, stay informed about industry innovations, and maintain flexibility in their approach to project delivery methods.