Develop a comprehensive asset management framework that aligns with ISO 55000 standards to maximize your real estate ROI and operational efficiency. Implement data-driven maintenance strategies through predictive analytics and condition monitoring systems to optimize asset lifecycle costs and prevent unexpected failures. Structure your asset hierarchy using a standardized classification system that enables precise tracking, valuation, and performance measurement across your entire portfolio.
Asset management excellence demands systematic risk assessment protocols, strategic capital planning, and real-time monitoring capabilities. Modern facility managers must leverage integrated management platforms to streamline operations, ensure compliance, and drive informed decision-making. Today’s competitive market requires organizations to adopt sophisticated asset management guidelines that balance cost optimization with performance enhancement and risk mitigation.
This comprehensive guide explores proven methodologies for developing robust asset management systems that align with international best practices while delivering measurable results in operational efficiency, cost reduction, and asset longevity. From establishing clear governance structures to implementing advanced technological solutions, these guidelines provide a blueprint for excellence in institutional asset management.
Creating a Robust Asset Management Framework
Asset Inventory and Classification
Effective asset inventory and classification forms the foundation of successful property management. Begin by conducting a comprehensive audit of all physical assets, documenting their location, condition, and operational status. Each asset should be assigned a unique identifier and categorized based on its function, criticality, and lifecycle stage.
Primary classification categories typically include structural elements, mechanical systems, electrical infrastructure, and technological components. Further subcategorization helps organize assets by their maintenance requirements, replacement costs, and operational importance. For instance, HVAC systems might be classified as critical infrastructure due to their direct impact on occupant comfort and building functionality.
Implement a standardized naming convention and hierarchical structure that reflects the relationship between different asset types. This systematic approach enables efficient tracking and reporting while facilitating maintenance planning and resource allocation.
Document key asset attributes including manufacturer specifications, installation dates, warranty information, and maintenance history. Modern asset management systems can automate this process through digital platforms that integrate with building information modeling (BIM) and computerized maintenance management systems (CMMS).
Regular updates to the inventory ensure accurate asset tracking and inform strategic decision-making regarding maintenance, upgrades, or replacements. This dynamic approach to asset classification supports both operational efficiency and long-term property value optimization.
Performance Metrics and KPIs
Effective asset management relies heavily on monitoring and measuring key performance indicators (KPIs) that provide insights into asset utilization, maintenance efficiency, and sustainable asset performance. Essential metrics include:
Asset Availability Rate (AAR): Measures the percentage of time assets are available for use, targeting 95% or higher for critical equipment.
Mean Time Between Failures (MTBF): Tracks the average time between asset breakdowns, helping predict maintenance needs and assess reliability.
Return on Asset Investment (ROAI): Calculates the financial return generated by assets relative to their acquisition and maintenance costs.
Maintenance Cost Ratio (MCR): Compares maintenance expenses to asset replacement value, typically aiming for 2-4% in well-managed facilities.
Asset Utilization Rate: Evaluates how effectively assets are being used against their maximum capacity.
Energy Efficiency Index: Monitors energy consumption patterns and identifies opportunities for optimization.
Compliance Score: Tracks adherence to regulatory requirements and industry standards.
These KPIs should be regularly monitored through automated systems and dashboard reporting, enabling proactive decision-making and continuous improvement in asset management strategies. Regular benchmarking against industry standards helps maintain competitive performance levels and identifies areas for enhancement.
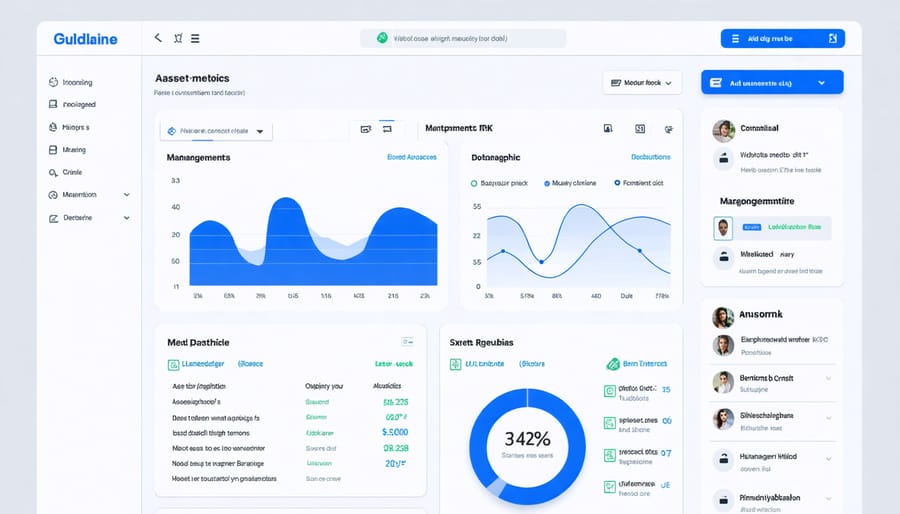
Preventive Maintenance Strategies
Scheduled Maintenance Programs
Effective scheduled maintenance programs form the cornerstone of successful asset management, ensuring optimal performance and longevity of building systems and equipment. These programs should be structured around three key timeframes: preventive maintenance conducted at regular intervals, predictive maintenance based on condition monitoring, and reactive maintenance for unexpected issues.
To develop a comprehensive maintenance schedule, begin by cataloging all assets and their recommended maintenance frequencies according to manufacturer specifications. Create a hierarchical system that prioritizes critical equipment and systems that directly impact operations and safety. This approach should include detailed protocols for inspection, testing, and servicing of each asset type.
Implementation requires clear documentation of maintenance procedures, including step-by-step instructions, required tools and materials, safety precautions, and expected completion times. Digital maintenance management systems can automate scheduling, track completion rates, and generate performance reports.
Key components of an effective maintenance program include:
– Regular equipment inspection schedules
– Preventive maintenance tasks and frequencies
– Resource allocation planning
– Documentation requirements
– Quality control procedures
– Performance metrics and KPIs
Monitor and evaluate program effectiveness through maintenance metrics such as mean time between failures (MTBF), maintenance completion rates, and cost analysis. Regular review and adjustment of maintenance schedules ensure optimal resource utilization and minimize operational disruptions while maximizing asset lifecycle value.
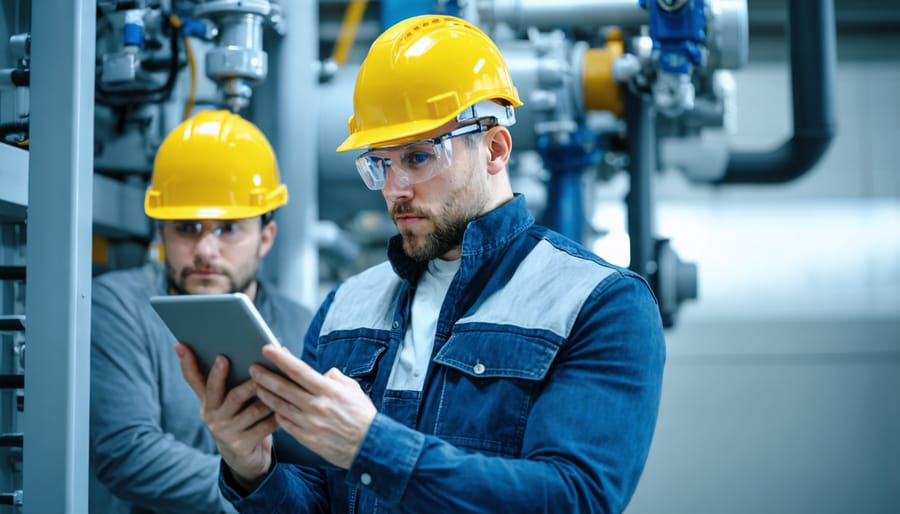
Condition Monitoring Systems
Modern asset management relies heavily on condition monitoring systems to provide real-time insights into asset performance and maintenance needs. These advanced monitoring solutions utilize sensors, data analytics, and IoT technology to continuously track asset conditions, enabling proactive maintenance decisions and reducing unexpected failures.
Key components of effective condition monitoring systems include vibration analysis sensors, thermal imaging cameras, ultrasonic detection devices, and oil analysis tools. These technologies work in concert to measure critical parameters such as temperature, pressure, vibration, and equipment wear, providing a comprehensive view of asset health.
Data collected through these monitoring systems is processed through sophisticated analytics platforms that can identify patterns and predict potential failures before they occur. This predictive capability allows maintenance teams to schedule interventions at optimal times, minimizing downtime and maximizing asset life span.
Implementation of condition monitoring systems requires careful planning and integration with existing asset management frameworks. Organizations should consider factors such as sensor placement, data collection frequency, and alert thresholds when designing their monitoring strategy. Regular calibration and maintenance of monitoring equipment ensure accurate and reliable data collection.
The return on investment for condition monitoring systems is typically realized through reduced maintenance costs, extended asset life, and prevented catastrophic failures. However, success depends on proper staff training and the development of clear procedures for responding to system alerts and analyzing trending data.
Risk Management and Compliance
Risk Assessment Protocols
Risk assessment protocols form the cornerstone of effective asset management, requiring a systematic approach to identify, evaluate, and mitigate potential threats to asset performance and value. The process begins with comprehensive asset identification and categorization, followed by detailed vulnerability analysis across multiple risk dimensions.
Organizations should implement a structured risk matrix that evaluates both the likelihood and potential impact of various risk factors. These typically include physical deterioration, functional obsolescence, environmental hazards, regulatory compliance issues, and financial exposure. Each risk factor should be assigned a numerical score based on predetermined criteria, enabling prioritization of risk mitigation efforts.
Regular risk audits should be conducted at prescribed intervals, with more frequent assessments for critical assets. These audits should incorporate both quantitative data from condition monitoring systems and qualitative input from facility managers and maintenance personnel. Documentation of findings, including photographic evidence and measurement data, provides a reliable basis for tracking risk trends over time.
Risk mitigation strategies should be developed based on cost-benefit analysis, considering both immediate intervention needs and long-term risk reduction goals. This approach ensures resource allocation aligns with organizational objectives while maintaining optimal asset performance and reliability. Implementation of automated monitoring systems can provide early warning indicators of emerging risks, enabling proactive rather than reactive risk management.
Compliance Documentation
Maintaining regulatory compliance in asset management requires comprehensive documentation and regular auditing processes. Organizations must establish clear record-keeping systems that track asset acquisition, maintenance history, disposal procedures, and financial transactions. These records should be readily accessible for internal reviews and external audits.
Key compliance documentation requirements include detailed asset registers, maintenance logs, inspection reports, and certification records. Organizations must maintain up-to-date records of safety inspections, environmental compliance assessments, and any regulatory permits or licenses associated with their assets.
Financial documentation should include purchase records, depreciation schedules, maintenance costs, and disposal values. This information is crucial for accurate reporting and tax compliance. Organizations must also maintain records of asset-related insurance policies, warranties, and service contracts.
Documentation should be stored in both physical and digital formats, with appropriate backup systems in place. Regular reviews of documentation processes ensure alignment with current regulations and industry standards. Organizations should implement version control systems and maintain audit trails for all documentation changes.
Training records for staff involved in asset management must be maintained, demonstrating compliance with required certifications and competency standards. This includes documentation of safety training, operational procedures, and emergency response protocols.
Technology Integration in Asset Management
Asset Management Software Solutions
Modern asset management demands sophisticated digital solutions to streamline operations and enhance decision-making processes. As we look toward the future of property management, technology integration has become essential for maintaining competitive advantage and operational efficiency.
Leading property portfolio software solutions now offer comprehensive features including real-time asset tracking, predictive maintenance scheduling, and automated reporting capabilities. These platforms typically incorporate:
• Cloud-based asset databases with secure access from any location
• Mobile applications for field inspections and immediate data entry
• Advanced analytics tools for performance monitoring and optimization
• Automated maintenance scheduling and work order management
• Integration capabilities with existing enterprise systems
• Compliance tracking and documentation management
• Financial planning and budgeting tools
When selecting asset management software, organizations should consider scalability, user interface complexity, integration capabilities, and vendor support quality. Implementation should be approached strategically, with clear objectives and adequate staff training to ensure successful adoption.
Key benefits of implementing digital asset management solutions include reduced operational costs, improved maintenance efficiency, enhanced data accuracy, and better compliance management. Organizations report up to 25% reduction in maintenance costs and 20% improvement in asset utilization after implementing comprehensive digital solutions.
For optimal results, asset management software should align with organizational processes and integrate seamlessly with existing systems. Regular updates and maintenance ensure the software continues to meet evolving business needs and industry standards.
IoT and Predictive Analytics
The integration of Internet of Things (IoT) technology and predictive analytics has revolutionized modern asset management practices in the construction industry. Smart sensors and connected devices now provide real-time monitoring of critical assets, delivering valuable data on performance metrics, usage patterns, and environmental conditions.
These IoT devices can track various parameters including temperature, vibration, pressure, and energy consumption, enabling facility managers to detect potential issues before they escalate into costly problems. For example, vibration sensors on HVAC systems can identify bearing wear patterns that indicate imminent failure, allowing maintenance teams to schedule repairs during planned downtime.
Predictive analytics platforms process this continuous stream of data using sophisticated algorithms and machine learning models. These systems analyze historical performance data alongside real-time measurements to forecast maintenance needs and potential equipment failures. This approach shifts maintenance strategies from reactive or scheduled interventions to condition-based maintenance, significantly reducing operational costs and extending asset lifecycles.
Implementation of IoT solutions requires careful planning and infrastructure development. Key considerations include sensor placement, network connectivity, data security, and integration with existing building management systems. Organizations should also invest in training maintenance teams to effectively utilize these advanced monitoring tools and interpret analytical insights.
The return on investment for IoT and predictive analytics typically manifests through reduced emergency repairs, optimized maintenance scheduling, and improved asset reliability. Industry studies show that predictive maintenance can reduce maintenance costs by 25-30% and eliminate up to 75% of breakdowns. This technology-driven approach also provides valuable insights for capital planning and asset replacement decisions, enabling more informed long-term investment strategies.
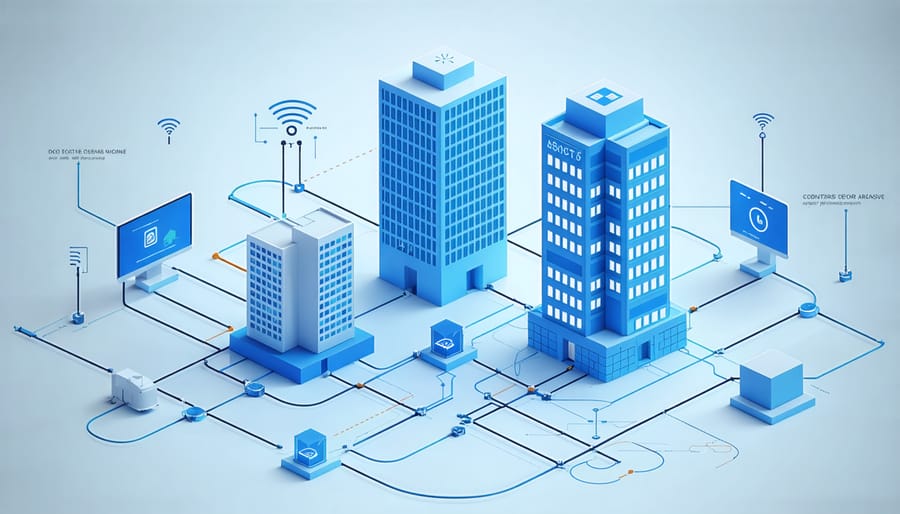
As we look to the future of asset management in the construction industry, the importance of adopting comprehensive guidelines becomes increasingly evident. The integration of digital technologies, sustainable practices, and data-driven decision-making has transformed traditional asset management approaches into sophisticated systems that deliver measurable value.
Key takeaways from these guidelines emphasize the critical nature of establishing clear frameworks, implementing preventive maintenance strategies, and utilizing advanced analytics for informed decision-making. Organizations that successfully implement these guidelines typically report significant improvements in asset performance, reduced operational costs, and enhanced lifecycle management.
Looking ahead, the asset management landscape will continue to evolve with emerging technologies such as artificial intelligence, IoT sensors, and blockchain solutions. These innovations will further streamline operations, improve predictive maintenance capabilities, and enhance real-time monitoring of asset performance.
To remain competitive and efficient, organizations must stay adaptable and ready to embrace new methodologies while maintaining core asset management principles. The future success of asset management will depend on balancing technological advancement with practical implementation, ensuring sustainable practices, and maintaining a skilled workforce capable of managing increasingly complex systems.
By following these guidelines and staying informed about industry developments, organizations can build robust asset management programs that drive long-term value and operational excellence in an ever-changing construction landscape.