Industrial zoning stands as the cornerstone of sustainable urban development, shaping the economic landscape while safeguarding community interests. Modern zoning regulations determine not just where manufacturing facilities can operate, but how they interact with surrounding neighborhoods, environmental resources, and infrastructure networks. As cities evolve and manufacturing technologies advance, these regulations have become increasingly sophisticated, balancing economic growth with environmental stewardship and quality of life considerations.
For construction professionals and developers, understanding industrial zoning requirements represents both a challenge and an opportunity. Strategic site selection, compliance with emissions standards, and integration of sustainable practices now define successful industrial development projects. The latest amendments to industrial zoning codes reflect growing emphasis on mixed-use compatibility, environmental impact mitigation, and smart growth principles.
This comprehensive examination of industrial zoning practices explores current regulations, emerging trends, and practical implications for development projects. From site assessment criteria to compliance strategies, we’ll analyze how modern zoning frameworks are reshaping industrial development while creating more resilient and sustainable urban environments. Understanding these dynamics is crucial for professionals navigating the complex landscape of industrial real estate development and urban planning.
The Framework of Industrial Zoning Regulations
Classification of Industrial Zones
Industrial zones are typically categorized into distinct classifications based on their operational impact, environmental considerations, and building code classifications. Light Industrial (I-1) zones accommodate manufacturing processes with minimal environmental impact, such as assembly plants, warehousing, and research facilities. These zones require buffer zones of 50-100 feet from residential areas and must maintain noise levels below 65 decibels at property boundaries.
Heavy Industrial (I-2) zones are designated for operations involving intensive manufacturing, processing, and storage activities. These zones demand larger setbacks (typically 200-500 feet), enhanced environmental controls, and specialized infrastructure for managing emissions and waste. Storage yards, chemical processing plants, and heavy machinery operations fall under this category.
Special Industrial (I-3) zones are reserved for unique industrial operations requiring additional safety measures or environmental considerations. These include hazardous material handling facilities, waste treatment plants, and specialized manufacturing centers. These zones must implement comprehensive safety protocols and maintain extensive buffer zones of 1,000 feet or more from sensitive areas.
Flex Industrial zones represent a modern approach, allowing for mixed-use industrial developments that combine light manufacturing, office space, and warehousing. These zones typically require 30% minimum industrial use while permitting complementary commercial activities, reflecting evolving industrial landscape needs.
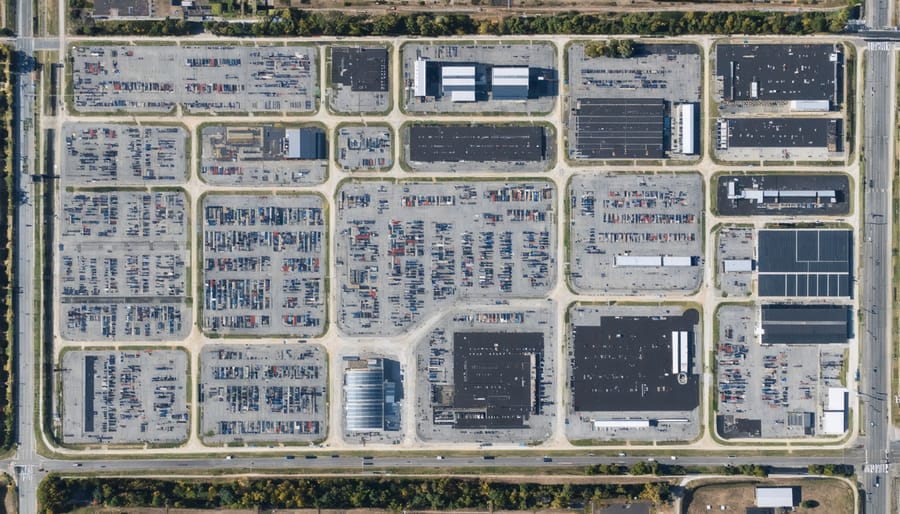
Compliance Requirements and Standards
Each industrial zone type requires strict adherence to specific compliance standards and regulations. Light industrial zones typically mandate noise levels below 65 decibels during operational hours, with stringent air quality controls and waste management protocols. Building coverage ratios usually cannot exceed 50% of the total lot area, and structures must maintain specific setbacks from residential boundaries.
Heavy industrial zones require more rigorous environmental safeguards, including advanced emission control systems, comprehensive environmental impact assessments, and regular monitoring of soil and groundwater conditions. These zones must implement industrial-grade fire suppression systems and maintain emergency response protocols that align with OSHA requirements.
For special industrial zones, compliance focuses on industry-specific requirements. Biotechnology facilities must adhere to biosafety levels (BSL) protocols, while chemical processing plants require specialized containment systems and safety buffer zones. Height restrictions vary by municipality but typically range from 45 to 75 feet for light industrial and up to 120 feet for heavy industrial structures.
All industrial zones must implement stormwater management systems, maintain minimum parking requirements based on gross floor area, and ensure adequate loading dock facilities. Regular environmental audits and safety inspections are mandatory, with documentation requirements varying by jurisdiction and industry type. Non-compliance can result in substantial fines and potential operational shutdowns.
Strategic Planning for Industrial Construction
Site Selection and Assessment
The selection and assessment of industrial sites requires careful consideration of multiple critical factors to ensure optimal functionality and compliance with zoning regulations. Environmental conditions play a primary role, including soil composition, topography, drainage patterns, and potential contamination history. These factors directly impact construction costs and long-term site viability.
Transportation access stands as a crucial consideration, encompassing proximity to major highways, railways, and ports. The site must accommodate both employee access and logistics operations, with sufficient space for parking, loading docks, and vehicle maneuvering. Infrastructure capacity assessment is equally vital, focusing on utilities such as power supply, water availability, waste management systems, and telecommunications networks.
Community impact factors must be evaluated thoroughly, including buffer zones between industrial operations and residential areas, noise pollution potential, and traffic impact on local roads. Environmental regulations and permit requirements vary by jurisdiction, necessitating early consultation with local authorities to understand specific restrictions and requirements.
Site dimensions and configuration should allow for current operational needs while providing expansion potential. The topographical features must support the intended industrial use without requiring excessive grading or engineering interventions. Natural hazard risks, including flood zones, seismic activity, and soil stability, require thorough assessment during the selection process.
Cost considerations extend beyond initial purchase price to include site preparation expenses, utility connection fees, and potential environmental remediation costs. Long-term operational efficiency often justifies higher initial investment in sites with superior characteristics. Professional site assessment services, including environmental studies, geotechnical surveys, and traffic impact analyses, provide crucial data for informed decision-making.
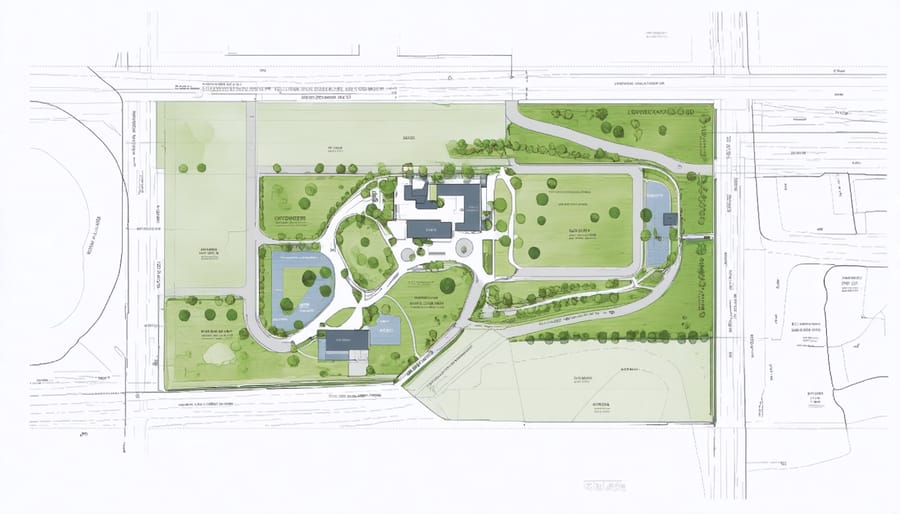
Environmental Impact Considerations
Environmental regulations play a crucial role in shaping industrial construction and zoning decisions. Modern industrial developments must comply with stringent environmental impact assessment (EIA) requirements, which evaluate potential effects on air quality, water resources, soil contamination, and local ecosystems.
Key environmental considerations include emissions control systems, wastewater management infrastructure, and noise pollution mitigation measures. Industrial facilities must implement comprehensive strategies for reducing environmental impact through advanced filtration systems, proper waste disposal protocols, and sustainable resource management practices.
Buffer zones between industrial areas and sensitive ecosystems or residential neighborhoods are mandatory in most jurisdictions. These zones typically incorporate green spaces, natural barriers, and drainage systems designed to protect surrounding areas from potential industrial contamination.
Stormwater management has become increasingly important, with regulations requiring industrial sites to implement sophisticated drainage systems and retention ponds. These features help prevent contaminated runoff from entering local waterways and protect groundwater resources.
Recent trends show a shift toward sustainable industrial development, incorporating renewable energy systems, energy-efficient building designs, and green infrastructure. Many jurisdictions now require industrial facilities to meet specific sustainability benchmarks and maintain ongoing environmental monitoring programs.
Construction professionals must carefully consider these environmental regulations during the initial planning phases, as retrofitting existing facilities to meet new standards can be significantly more costly than incorporating them into the original design. Regular environmental audits and compliance reviews are essential for maintaining necessary permits and avoiding potential penalties or operational disruptions.
Navigating Zoning Challenges
Variance Applications
Obtaining a zoning variance for industrial properties requires navigating a complex administrative process designed to maintain community standards while accommodating necessary business operations. The application typically begins with a formal submission to the local zoning board or planning commission, accompanied by detailed site plans, operational specifications, and impact assessments.
Key requirements generally include demonstrating that strict application of existing zoning regulations would create undue hardship, and that the proposed variance won’t adversely affect neighboring properties or public interest. Applicants must provide evidence of unique property characteristics or circumstances that justify the variance request.
The review process involves multiple stages, including:
– Initial application review by planning staff
– Technical evaluation of environmental and infrastructure impacts
– Public notification and comment period
– Zoning board hearing and deliberation
– Final determination and conditions
Successful variance applications often require professional assistance from architects, engineers, or land-use attorneys who can effectively present technical arguments and address potential concerns. The timeline typically ranges from 3-6 months, though complex cases may take longer.
To strengthen an application, businesses should:
– Document specific hardships clearly
– Provide comprehensive site analysis
– Present alternative solutions considered
– Demonstrate community benefit
– Include mitigation strategies for potential impacts
Most jurisdictions require regular renewal of variances, making compliance monitoring and documentation essential for long-term operations.
Legal Considerations
Industrial zoning regulations present numerous legal complexities that require careful navigation. Property owners and developers must comply with multiple layers of regulatory requirements, including federal, state, and local ordinances. Non-compliance can result in significant penalties, project delays, or complete shutdowns.
Key legal considerations include environmental impact assessments, noise regulations, emission standards, and waste management protocols. Property owners must obtain proper permits and certifications before commencing operations, with requirements varying by jurisdiction and industrial classification.
Setback requirements, height restrictions, and floor area ratios (FAR) constitute crucial legal parameters that affect facility design and operation. These specifications often intersect with fire safety codes and emergency access requirements, necessitating careful planning during the development phase.
When legal challenges arise, understanding zoning dispute resolution mechanisms becomes essential. Common legal issues include non-conforming use claims, variance requests, and challenges from neighboring properties regarding environmental or quality-of-life impacts.
Property owners should maintain detailed documentation of compliance measures and regularly review zoning ordinances for amendments that might affect their operations. Engaging qualified legal counsel during property acquisition and development phases can help prevent costly violations and ensure smooth operational continuity.
Overlay districts and special use permits may impose additional requirements beyond basic industrial zoning regulations. Understanding these requirements early in the planning process helps avoid legal complications and ensures project viability.
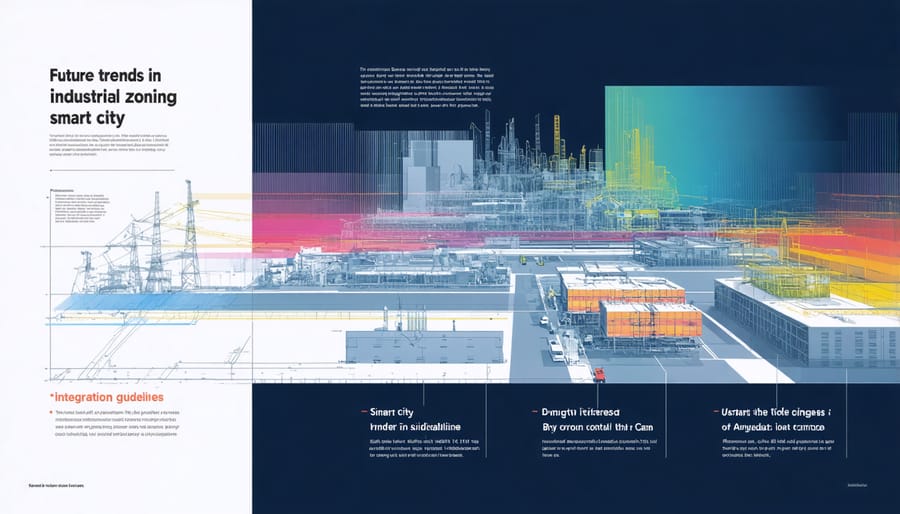
Future Trends in Industrial Zoning
Industrial zoning is undergoing significant transformation as cities adapt to evolving economic and technological demands. Smart manufacturing facilities are driving the need for more flexible zoning regulations that accommodate both traditional industrial operations and advanced technology centers. Many municipalities are now implementing mixed-use industrial zones that allow for research and development facilities alongside manufacturing operations.
Sustainability requirements are becoming increasingly prominent in industrial zoning regulations. New standards often mandate green building practices, renewable energy integration, and improved waste management systems. Cities are also introducing buffer zone requirements that utilize green infrastructure to minimize environmental impact on neighboring areas.
The rise of e-commerce has sparked a trend toward last-mile delivery facilities in urban areas, prompting zoning boards to reconsider traditional industrial district boundaries. Some jurisdictions are creating specialized zones for logistics hubs that balance operational efficiency with urban planning objectives.
Vertical industrial development is gaining traction in land-constrained urban areas. Multi-story warehouses and manufacturing facilities are becoming more common, necessitating updates to height restrictions and floor area ratio requirements in industrial zones.
Industry 4.0 technologies are influencing zoning policies, with many jurisdictions updating regulations to accommodate automated systems, data centers, and advanced manufacturing processes. These changes often include provisions for improved digital infrastructure and reduced parking requirements due to automated operations.
Environmental justice considerations are playing a larger role in industrial zoning decisions. New regulations increasingly require environmental impact assessments and community benefit agreements, particularly in areas historically affected by industrial pollution.
Looking ahead, experts anticipate more emphasis on circular economy principles in industrial zoning, with regulations encouraging industrial symbiosis parks where businesses can share resources and minimize waste. Additionally, climate resilience requirements are expected to become standard features of industrial zoning codes, addressing flood risks, extreme weather events, and other climate-related challenges.
Industrial zoning remains a critical component of urban development and economic growth, shaping the future of manufacturing, logistics, and commercial operations. Through our comprehensive analysis, we’ve seen how effective zoning practices can create sustainable industrial environments while minimizing conflicts with neighboring land uses.
Key takeaways from our examination include the importance of understanding local zoning ordinances, maintaining compliance with environmental regulations, and anticipating future development needs. Success in industrial development requires a balanced approach that considers both economic objectives and community impact.
To implement effective industrial zoning strategies, consider these actionable steps:
1. Conduct thorough site assessments before property acquisition
2. Engage early with local planning authorities
3. Develop comprehensive environmental impact mitigation plans
4. Establish clear communication channels with surrounding communities
5. Plan for future expansion and technological advancement
The evolving nature of industry, particularly with the rise of smart manufacturing and sustainable practices, necessitates flexible zoning approaches. Forward-thinking organizations should stay informed about emerging trends and regulations while maintaining adaptable development strategies.
Remember that successful industrial zoning isn’t just about compliance – it’s about creating sustainable, efficient, and productive spaces that benefit both businesses and communities. By incorporating these insights into your planning process, you can better position your industrial development projects for long-term success while ensuring regulatory compliance and community acceptance.