The construction industry stands at a pivotal crossroads, where traditional linear “take-make-dispose” models are giving way to revolutionary sustainable building practices centered on circular economy principles. With construction and demolition waste accounting for approximately 40% of global waste production, the transition to circular economy construction represents not just an environmental imperative, but a $4.5 trillion economic opportunity by 2030.
This paradigm shift fundamentally transforms how we approach building design, material selection, and waste management. By incorporating principles of regenerative design, material passports, and advanced recycling technologies, the construction sector is reimagining its entire value chain. From modular components designed for disassembly to AI-powered material tracking systems, innovative solutions are emerging that promise to close the loop on construction waste while creating new revenue streams and competitive advantages.
As leading construction firms worldwide embrace these circular principles, they’re discovering that environmental responsibility and profitability aren’t mutually exclusive. The challenge now lies in scaling these solutions across the industry, establishing new standards, and creating the infrastructure necessary to support a truly circular construction economy.
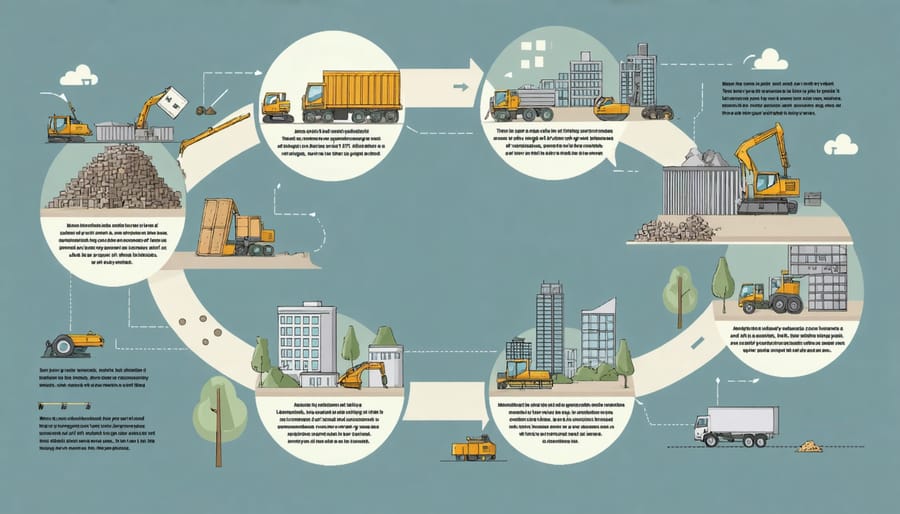
The Business Case for Circular Construction Materials
Cost Reduction Through Material Recovery
Material recovery in construction projects can significantly reduce overall project costs while supporting sustainability goals. Studies indicate that effective material recovery strategies can lower construction costs by 15-25% through various mechanisms. By implementing systematic demolition and careful material sorting, contractors can salvage valuable resources like steel, copper, and timber for resale or reuse in future projects.
The financial benefits extend beyond direct material savings. Reduced waste disposal fees, lower transportation costs, and decreased raw material purchases contribute to substantial cost reductions. For example, crushing and reusing concrete on-site as aggregate can save up to 50% compared to purchasing new materials while eliminating disposal fees.
Recent industry analysis shows that companies implementing comprehensive material recovery programs typically achieve ROI within 12-18 months. This includes investments in sorting equipment, storage facilities, and training. Additionally, tax incentives and environmental compliance credits in many jurisdictions further enhance the economic advantages of material recovery practices.
Smart material recovery also helps buffer against market volatility and supply chain disruptions by reducing dependence on new raw materials. This strategic approach to resource management provides both immediate cost benefits and long-term financial resilience.
Market Growth and Investment Opportunities
The circular economy construction market is experiencing remarkable growth, with projections indicating a compound annual growth rate of 12.3% through 2028. This expansion is driven by increasing awareness of construction sustainability metrics and stricter environmental regulations worldwide. Investment opportunities are particularly robust in building material recovery and recycling infrastructure, with venture capital funding in circular construction technologies reaching $2.8 billion in 2022 alone.
Key growth areas include modular construction systems, material passport platforms, and waste-to-resource technologies. Government incentives, including tax benefits and grants for sustainable building practices, are creating favorable conditions for investors. The European Union’s Green Deal and similar initiatives worldwide are channeling significant funding into circular construction projects, while institutional investors are increasingly prioritizing projects that demonstrate strong circular economy principles.
Market analysis reveals that early adopters of circular construction methods are experiencing 15-20% cost reductions in material procurement and waste management, making these investments particularly attractive for long-term returns. The renovation and retrofit sector presents especially promising opportunities, with growing demand for circular solutions in urban regeneration projects.
Key Principles of Circular Material Design
Design for Disassembly
Design for Disassembly (DfD) represents a crucial strategy in circular economy construction, focusing on creating buildings and components that can be easily separated, recovered, and reused at the end of their initial lifecycle. This approach requires careful consideration during the planning and design phases to ensure components can be efficiently dismantled without damage.
Key principles include using mechanical connections instead of adhesives, implementing standardized and modular components, and clearly documenting assembly methods. For example, bolt-and-nut connections are preferred over welded joints, while click-fit systems and reversible fasteners enable straightforward separation of materials.
Successful DfD implementation requires careful material selection and connection detailing. Designers should specify durable materials that maintain their value through multiple use cycles and avoid composite materials that are difficult to separate. Documentation plays a vital role, with Building Information Modeling (BIM) systems tracking component locations, assembly sequences, and disassembly instructions.
Recent innovations in DfD include prefabricated wall systems with magnetic connections, reversible concrete connections using specialized bolts, and modular floor systems designed for quick assembly and disassembly. These solutions not only facilitate future material recovery but also reduce construction time and waste during initial assembly.
The economic benefits of DfD become apparent during renovation or demolition phases, with reduced labor costs and higher material recovery rates. Additionally, buildings designed for disassembly typically command higher end-of-life value, as components can be effectively recovered and redirected to new construction projects.
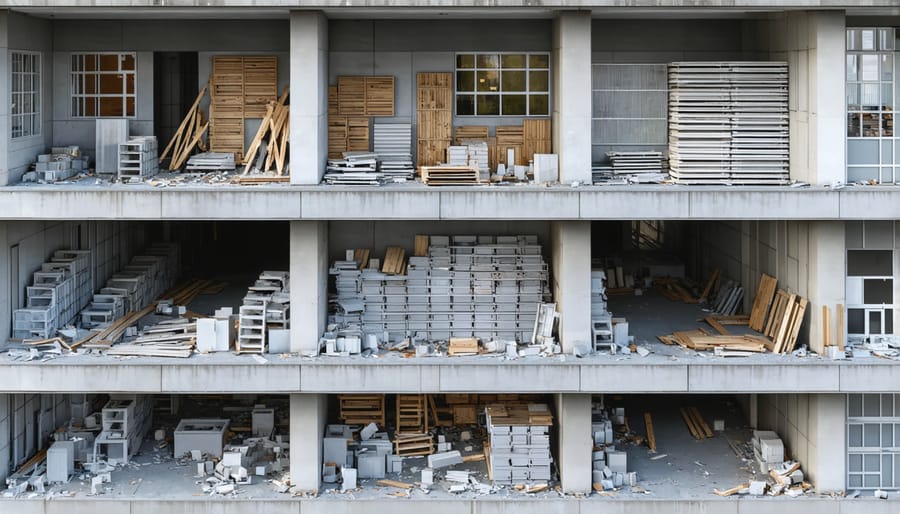
Material Passport Systems
Material passport systems represent a transformative approach to tracking and managing construction materials throughout their lifecycle. These digital documentation systems maintain detailed records of materials’ properties, location, and condition, enabling efficient recovery and reuse in future projects. By creating a comprehensive database of material information, construction professionals can make informed decisions about resource allocation and end-of-life strategies.
The implementation of material passports typically involves three key components: data collection, digital storage, and material tracking. During the construction phase, teams document essential information including material composition, structural properties, installation methods, and maintenance requirements. This data is then stored in secure digital platforms, often utilizing blockchain technology to ensure data integrity and accessibility.
Leading construction firms have reported significant benefits from material passport adoption, including improved resource efficiency and reduced waste management costs. For example, a recent European commercial project achieved a 30% reduction in virgin material use by effectively tracking and reusing materials through their passport system.
To successfully implement a material passport system, organizations should:
– Establish standardized documentation protocols
– Invest in reliable digital infrastructure
– Train staff in proper data collection and management
– Integrate the system with existing building information modeling (BIM) platforms
– Maintain regular updates throughout the building’s lifecycle
As circular economy principles gain traction, material passport systems are becoming increasingly essential for sustainable construction practices and effective material recovery strategies.
Innovative Circular Materials in Practice
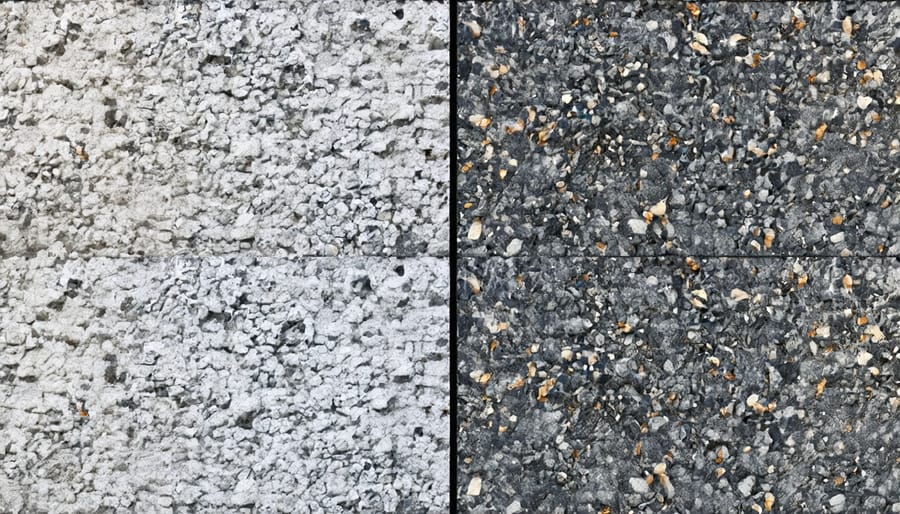
Recycled Concrete Aggregates
Recycled concrete aggregates (RCA) have emerged as a cornerstone of sustainable construction practices, with successful implementations demonstrating both environmental benefits and economic viability. Studies show that RCA can effectively replace up to 30% of natural aggregates in structural concrete without compromising performance, while some non-structural applications can utilize up to 100% RCA.
A notable example is the Oslo Airport Terminal 2 project, which incorporated 90% recycled concrete from demolished buildings in its foundation work. This implementation not only diverted thousands of tons of waste from landfills but also reduced the project’s carbon footprint by approximately 35% compared to conventional methods.
Quality control remains crucial for successful RCA implementation. Leading construction firms have developed sophisticated processing techniques, including advanced crushing methods and contamination removal systems, to ensure consistent aggregate quality. These processes typically involve multiple stages of crushing, screening, and washing to achieve optimal particle size distribution and remove impurities.
Recent technological advances have enhanced RCA performance through carbonation treatment, where recycled aggregates are exposed to CO2 during the crushing process. This treatment improves the material’s mechanical properties and effectively sequesters carbon dioxide, creating a dual environmental benefit.
Cost analysis from multiple projects indicates that using RCA can reduce aggregate costs by 15-25% compared to virgin materials, particularly in urban areas where transportation distances for natural aggregates are significant. However, the economic viability varies by region and depends largely on local availability of processing facilities and transportation infrastructure.
The success of RCA implementation relies heavily on proper specification and testing protocols. Industry leaders recommend comprehensive material characterization and performance testing to ensure compliance with relevant standards and project requirements.
Bio-based Building Materials
Bio-based building materials represent a significant advancement in sustainable construction, offering renewable alternatives to traditional materials while supporting circular economy principles. These materials, derived from organic sources, provide both environmental benefits and compelling performance characteristics that make them increasingly attractive for modern construction projects.
Engineered wood products, such as cross-laminated timber (CLT) and mass timber, lead the bio-based revolution. These materials sequester carbon throughout their lifecycle while offering structural properties comparable to steel and concrete. Hemp-based materials, including hempcrete, deliver excellent thermal insulation properties and moisture regulation, contributing to energy-efficient building transformation.
Mycelium-based materials, developed from fungal networks, are emerging as innovative insulation and structural components. These materials are completely biodegradable and can be grown to specific shapes, reducing waste in the manufacturing process. Agricultural waste products, such as rice hulls and corn stalks, are being transformed into high-performance building panels and insulation materials.
Recent developments include bio-based adhesives and finishes that eliminate volatile organic compounds (VOCs) while maintaining durability standards. Bamboo composites offer rapid renewability and superior strength-to-weight ratios, making them ideal for both structural and decorative applications.
The adoption of these materials is accelerating as manufacturers improve scalability and standardization. Construction professionals are increasingly specifying bio-based materials in projects, driven by enhanced building codes, environmental certifications, and client demand for sustainable solutions. As research continues, these materials are expected to play a crucial role in achieving circular economy goals in construction.
Implementation Challenges and Solutions
Supply Chain Adaptation
Transforming traditional linear supply chains into circular ones requires a systematic approach that prioritizes resource efficiency and material recovery. Construction companies are increasingly adopting digital material passports and blockchain technology to track building materials throughout their lifecycle, enabling better recovery and reuse opportunities.
Key strategies include establishing reverse logistics networks that facilitate the collection and processing of recovered materials from demolition sites. These networks require collaboration between suppliers, contractors, and waste management facilities to ensure materials maintain their value and quality for future use.
Material banks and digital marketplaces are emerging as crucial infrastructure for circular supply chains. These platforms connect suppliers of recovered materials with potential buyers, creating a more efficient secondary materials market. Leading construction firms are partnering with suppliers who demonstrate commitment to circular principles, often requiring transparency in material sourcing and end-of-life management.
Integration of Building Information Modeling (BIM) with supply chain management systems enables better material tracking and forecasting. This technology allows project teams to optimize material use, reduce waste, and plan for future disassembly and recovery.
Success in supply chain adaptation relies heavily on establishing strong partnerships across the value chain. Companies are developing supplier evaluation criteria that include circular economy metrics, encouraging innovation in packaging reduction, and implementing take-back schemes for construction materials. These initiatives are supported by new contractual frameworks that facilitate shared responsibility for material stewardship throughout the building lifecycle.
Quality Assurance Standards
The implementation of robust quality assurance standards for recycled construction materials is crucial for the widespread adoption of circular economy principles. These standards ensure that recovered materials meet or exceed the performance requirements of virgin materials while maintaining safety and durability specifications.
Leading certification bodies, including ISO and national building standards organizations, have developed comprehensive frameworks for testing and validating recycled materials. These frameworks address key parameters such as mechanical strength, chemical composition, durability, and environmental impact. For concrete aggregates, standards typically focus on particle size distribution, contamination levels, and structural integrity, while for steel, the emphasis is on tensile strength, chemical composition, and corrosion resistance.
Third-party testing laboratories play a vital role in verifying compliance with these standards. They conduct rigorous assessments using standardized testing protocols, ensuring consistency and reliability across different suppliers and applications. This standardization has been instrumental in building confidence among stakeholders and facilitating the integration of recycled materials into mainstream construction projects.
Recent developments include the introduction of digital tracking systems and blockchain technology to ensure material traceability and quality verification throughout the supply chain. These innovations enable real-time monitoring of material properties and help maintain the integrity of circular economy practices in construction.
The transition to circular economy principles in construction represents a fundamental shift in how we approach building design, material usage, and waste management. Throughout this article, we’ve explored how circular economy practices can revolutionize the construction industry through innovative material selection, waste reduction strategies, and sustainable design principles.
The future of circular economy construction looks promising, with emerging technologies and methodologies continuously enhancing our ability to implement these practices effectively. Building Information Modeling (BIM), artificial intelligence, and advanced recycling technologies are making it increasingly feasible to track, manage, and optimize material usage throughout a building’s lifecycle.
Industry leaders are already demonstrating the viability of circular construction through successful projects worldwide. These implementations have shown significant reductions in waste, lower carbon emissions, and improved cost efficiency, while maintaining or exceeding traditional building standards.
However, challenges remain in scaling these practices industry-wide. Success will require continued collaboration between stakeholders, supportive regulatory frameworks, and investment in innovative technologies. The construction sector must also focus on developing standardized processes for material recovery and reuse, while building expertise in circular design principles.
As we move forward, the adoption of circular economy practices in construction isn’t just an environmental imperative—it’s becoming a competitive necessity. Organizations that embrace these principles now will be better positioned to meet increasingly stringent sustainability requirements and changing market demands, while contributing to a more sustainable built environment for future generations.