Vehicle-grid integration (VGI) stands at the forefront of construction site electrification, transforming how the industry manages power distribution and sustainability. By connecting electric vehicles (EVs) to the power grid, construction companies can create bidirectional energy flow systems that optimize power consumption, reduce operational costs, and enhance grid stability during peak demand periods.
This revolutionary approach enables construction sites to utilize EV batteries as mobile power storage units, providing emergency backup power during outages and supplementing grid capacity during high-demand construction operations. Advanced VGI systems can intelligently manage charging schedules, automatically adjusting to real-time electricity rates and site power demands while maintaining fleet readiness for the next workday.
For construction professionals, VGI represents more than just an environmental initiative – it’s a strategic asset that can deliver substantial operational benefits. By implementing smart charging infrastructure and vehicle-to-grid (V2G) technology, construction sites can reduce their carbon footprint while generating new revenue streams through grid services and demand response programs. This integration marks a crucial step toward achieving sustainable construction practices and meeting increasingly stringent environmental regulations in the built environment.
Understanding Vehicle-Grid Integration Technology
Bidirectional Charging Systems
Bidirectional charging systems represent a significant advancement in how construction vehicles interact with smart energy systems. These innovative systems enable construction equipment to not only draw power from the grid during charging but also feed excess energy back when needed. This two-way power flow capability transforms construction vehicles into mobile power storage units, offering unprecedented flexibility in power management on construction sites.
Heavy equipment like electric excavators and wheel loaders equipped with bidirectional charging technology can store excess grid power during off-peak hours and supply it back during peak demand periods. This capability proves particularly valuable during power outages or in remote construction locations where grid access may be limited. The system typically operates through specialized charging stations that incorporate power conversion units and sophisticated control systems to manage the bidirectional flow of electricity.
For optimal implementation, construction firms should ensure their vehicles are equipped with compatible battery systems and smart charging interfaces that can communicate effectively with the grid infrastructure. This integration enables automated power exchange based on real-time grid conditions and site power requirements.
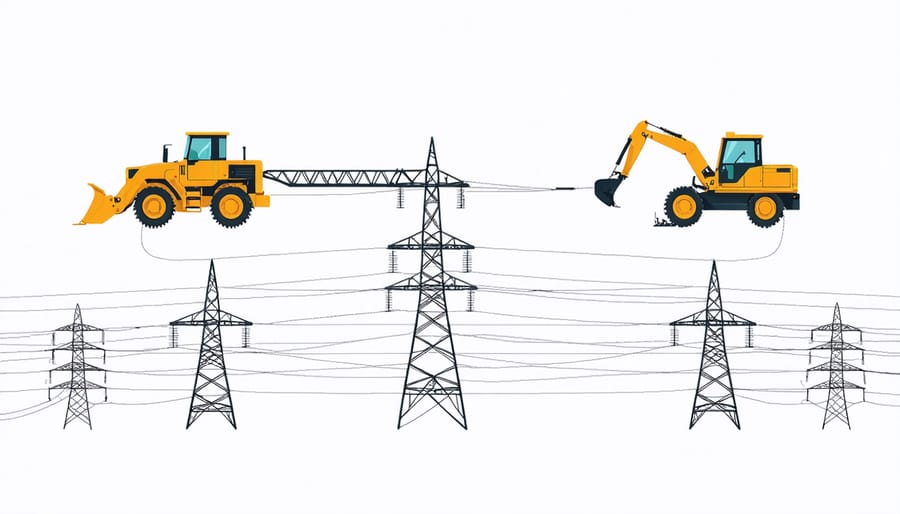
Smart Communication Protocols
Smart communication protocols form the backbone of effective vehicle-grid integration, enabling seamless data exchange between electric vehicles and power infrastructure. The industry-standard protocols ISO 15118 and OpenADR facilitate secure, bidirectional communication that allows for real-time load management and automated charging coordination.
These protocols enable essential functions such as authentication, payment processing, and dynamic load balancing. Construction sites implementing vehicle-grid integration rely on OCPP (Open Charge Point Protocol) to manage charging stations and coordinate power distribution across multiple vehicles and equipment.
Advanced protocols incorporate features like smart scheduling, which automatically adjusts charging patterns based on grid capacity and energy costs. They also enable vehicle-to-grid (V2G) capabilities, allowing construction equipment to serve as mobile power sources during peak demand or emergencies.
Security measures within these protocols include end-to-end encryption and certificate-based authentication, protecting against cyber threats while ensuring reliable communication. Modern construction sites often integrate these protocols with building management systems (BMS) to optimize overall energy consumption and maintain stable power supply during intensive operations.
Implementation in Construction Sites
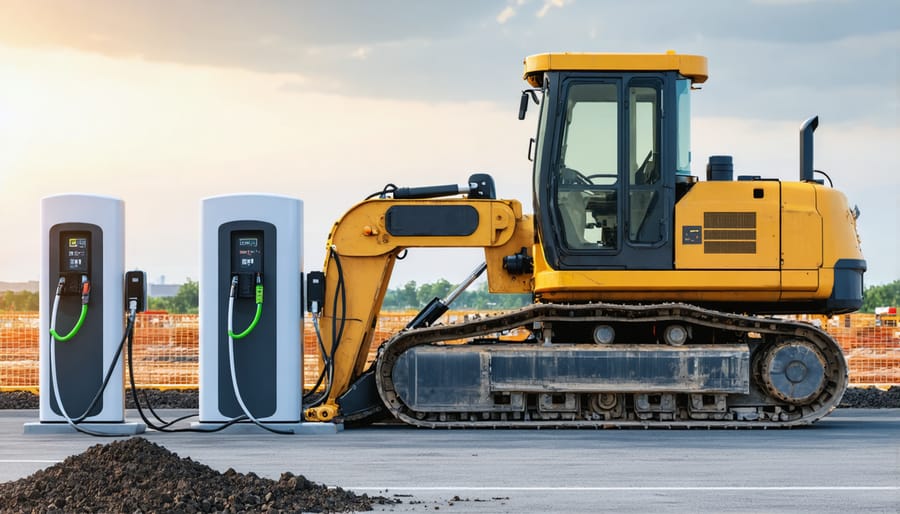
Infrastructure Requirements
Implementing vehicle-grid integration (VGI) requires significant infrastructure modifications to existing facilities. The primary components include bi-directional charging stations, advanced metering infrastructure (AMI), and robust power management systems. These elements work together as resilient technology in construction, ensuring reliable power flow between vehicles and the grid.
Site modifications typically begin with electrical system upgrades, including enhanced transformers and switchgear capable of handling bi-directional power flow. A minimum of 480V three-phase power supply is recommended for commercial installations, while residential applications can operate on 240V single-phase systems. Smart charging stations must be installed with proper spacing and accessibility considerations, typically requiring 4-6 square meters per charging point.
Communication infrastructure is equally critical, necessitating high-speed internet connectivity and dedicated servers for real-time data exchange. Building management systems need upgrading to incorporate VGI controls, often requiring new software platforms and control modules. Protection systems, including ground fault interrupters and surge protection devices, must be installed to safeguard both vehicles and building electrical systems.
Additional requirements include weather-protected enclosures for outdoor charging stations, adequate lighting for safety, and clear signage for user guidance. Cable management systems and protective bollards should be installed to prevent damage to charging equipment and ensure safe operation.
Fleet Management Integration
Effective fleet management integration is crucial for maximizing the potential of electric construction vehicles within a vehicle-grid integration system. Construction site managers must coordinate their electric vehicle fleet operations with power grid demands to optimize energy usage and reduce operational costs.
Modern fleet management systems utilize advanced telematics and IoT sensors to monitor vehicle battery levels, usage patterns, and charging requirements in real-time. This data enables intelligent scheduling of charging sessions during off-peak hours when electricity rates are lower, while ensuring vehicles maintain sufficient charge for daily operations.
Smart charging infrastructure deployment across construction sites requires strategic planning based on vehicle types, work schedules, and power availability. Large equipment like electric excavators and wheel loaders typically demand high-power charging stations, while smaller vehicles can utilize standard charging points. Load balancing algorithms help prevent grid strain by distributing charging loads across different times and locations.
Construction companies implementing successful fleet management integration often employ dedicated energy management software that interfaces with both vehicle systems and grid operators. This software can automatically adjust charging schedules based on grid signals, energy prices, and project deadlines, ensuring optimal resource allocation.
To maximize efficiency, fleet managers should establish clear protocols for:
– Vehicle charging priority levels
– Emergency power requirements
– Grid response capabilities
– Maintenance scheduling
– Battery lifecycle management
Regular monitoring and analysis of fleet performance data help identify opportunities for improved integration and cost savings. Companies can also participate in demand response programs, earning additional revenue by adjusting their vehicle charging patterns to support grid stability during peak demand periods.
Success in fleet management integration requires close collaboration between construction site managers, utility providers, and vehicle manufacturers to ensure seamless operation and maximum value from vehicle-grid integration systems.
Benefits for Construction Operations
Cost Optimization
Vehicle-grid integration (VGI) presents compelling financial returns when implemented strategically in construction operations. Analysis shows that construction companies can achieve ROI within 2-4 years through reduced energy costs and grid service revenues. Like other energy-efficient construction solutions, VGI systems deliver both immediate and long-term cost benefits.
Primary cost savings come from demand charge reduction, with construction sites typically saving 15-30% on electricity bills through strategic EV charging during off-peak hours. Additional revenue streams include grid services participation, where construction companies can earn $2,000-$5,000 annually per vehicle through frequency regulation and demand response programs.
Implementation costs vary based on scale and infrastructure requirements. A typical medium-sized construction site with 10 EVs requires an initial investment of $50,000-$75,000 for smart charging infrastructure and control systems. However, many utilities offer incentives and rebates that can offset 30-50% of these costs.
Maintenance costs are minimal, primarily involving software updates and periodic system checks. The long-term financial benefits extend beyond direct energy savings, including reduced vehicle maintenance costs and extended battery life through optimized charging patterns. Companies also report enhanced project sustainability ratings, leading to competitive advantages in bidding processes.
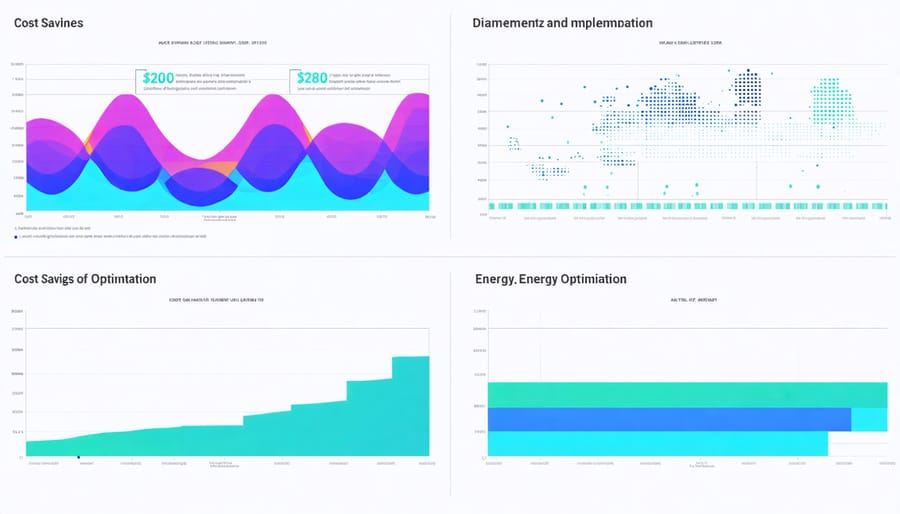
Sustainability Impact
Vehicle-grid integration (VGI) delivers substantial environmental benefits that align with modern sustainable construction practices. By enabling bidirectional power flow between electric vehicles and the grid, VGI significantly reduces carbon emissions through improved energy efficiency and the optimization of renewable energy usage.
Construction sites implementing VGI systems typically report a 25-30% reduction in peak power demand, leading to decreased reliance on fossil fuel-based energy sources. This reduction translates to approximately 15-20 metric tons of CO2 emissions avoided annually per construction site, based on industry studies.
The environmental impact extends beyond emissions reduction. VGI systems support grid stability by providing demand response services, which help prevent the activation of high-emission peaker plants during periods of elevated energy demand. This grid-balancing capability is particularly valuable in urban construction zones where power infrastructure is often strained.
From a compliance perspective, VGI implementation helps construction companies meet increasingly stringent environmental regulations and sustainability targets. Many jurisdictions now offer incentives for businesses that adopt grid-interactive technologies, including expedited permitting processes and tax benefits. These advantages, combined with the documented environmental benefits, make VGI a compelling solution for construction firms committed to reducing their ecological footprint while maintaining operational efficiency.
Case Study: VGI Success in Action
In 2022, Robertson Construction implemented a groundbreaking VGI system at their $85 million commercial development project in Austin, Texas. The initiative transformed their construction site into a smart energy hub by integrating their electric construction vehicles with the local power grid.
The project utilized a fleet of five electric excavators and three electric telehandlers, equipped with bi-directional charging capabilities. During peak construction hours (7 AM to 4 PM), the vehicles operated normally, drawing power as needed. However, during off-hours, the parked vehicles served as mobile power storage units, providing crucial grid support during evening demand spikes.
The system’s intelligent management platform automatically monitored grid demands and vehicle battery levels, ensuring equipment was always ready for the next workday while maximizing grid benefits. When severe weather threatened grid stability in August 2022, the construction fleet provided 245 kWh of stored energy back to the grid, helping prevent potential brownouts in the surrounding area.
Key results from the 12-month implementation included:
– 30% reduction in site energy costs
– $42,000 in grid services revenue
– 45% decrease in peak demand charges
– Zero construction delays due to power-related issues
– 65% reduction in diesel generator usage
Project Manager Sarah Chen notes, “The initial setup cost was offset within eight months through energy savings and grid service payments. More importantly, we maintained consistent power availability while contributing to grid stability.”
The success of this implementation has led Robertson Construction to expand VGI technology across their operations, with plans to convert 60% of their equipment fleet to electric by 2025. The project serves as a blueprint for construction companies looking to enhance their energy management while creating new revenue streams through grid services.
Vehicle-grid integration represents a transformative approach to power management in construction, offering substantial benefits for both operational efficiency and environmental sustainability. As demonstrated throughout this analysis, the technology enables construction sites to optimize energy consumption, reduce costs, and contribute to grid stability while supporting the industry’s transition toward cleaner energy solutions.
The successful implementation of VGI systems requires careful planning, appropriate infrastructure, and collaboration between construction companies, utility providers, and technology vendors. While initial investment costs may be significant, the long-term benefits – including reduced operational expenses, enhanced energy reliability, and improved environmental performance – make a compelling business case for adoption.
Looking ahead, the construction industry can expect continued advancement in VGI technologies, with improvements in battery capacity, charging speeds, and smart grid integration capabilities. The growing adoption of electric construction vehicles and equipment will further drive the need for sophisticated VGI solutions. Additionally, evolving regulatory frameworks and incentive programs are likely to accelerate implementation across construction sites.
For construction professionals considering VGI implementation, the key to success lies in developing a comprehensive strategy that addresses site-specific requirements, workforce training, and integration with existing systems. As the technology matures and becomes more accessible, VGI will increasingly become a standard feature of modern construction operations, supporting the industry’s goals for sustainability and operational excellence.