Project management risks threaten even the most meticulously planned sustainable construction initiatives, with 70% of construction projects experiencing significant delays or cost overruns due to inadequate risk management. In today’s complex building landscape, where sustainable construction practices increasingly define industry standards, understanding and anticipating potential risks becomes paramount for project success.
From supply chain disruptions and material price volatility to regulatory compliance challenges and technological integration hurdles, construction project managers must navigate an intricate web of potential threats. These risks not only impact project timelines and budgets but can also compromise sustainability goals and stakeholder relationships.
This comprehensive guide examines critical project management risks through real-world examples, providing practical insights and proven mitigation strategies. Whether you’re managing a large-scale green building development or retrofitting existing structures for improved sustainability, understanding these risk patterns and their solutions will help safeguard your project’s success and environmental objectives.
By analyzing specific risk scenarios and their impact on sustainable construction projects, we’ll explore effective approaches to risk identification, assessment, and mitigation that align with both project delivery requirements and environmental responsibility. Our focus remains on actionable strategies that construction professionals can implement immediately to enhance their risk management capabilities.
Environmental Risk Factors in Sustainable Construction
Climate-Related Construction Delays
Climate-related delays represent an increasingly significant risk factor in construction project management, with weather patterns becoming more unpredictable and extreme weather events more frequent. These disruptions can substantially impact project timelines and budgets, requiring careful consideration during the planning phase.
Recent industry data indicates that weather-related delays account for approximately 21% of construction project overruns. Extreme temperatures, excessive rainfall, and severe storms can halt outdoor construction activities, affect material curing times, and compromise worker safety. For instance, concrete pouring operations require specific temperature ranges for optimal results, while high winds can prevent crane operations and exterior installations.
To mitigate these risks, project managers are implementing sophisticated weather monitoring systems and developing flexible scheduling strategies. Advanced weather forecasting technology allows teams to anticipate potential disruptions and adjust work schedules accordingly. Some effective mitigation strategies include:
– Building weather contingency days into project schedules
– Implementing temporary climate control measures
– Using rapid-drying materials and advanced curing compounds
– Developing indoor alternatives for weather-sensitive tasks
– Creating detailed severe weather response protocols
Climate risk assessment has become an essential component of project planning, with many firms now incorporating historical weather data and climate change projections into their risk management strategies. This proactive approach helps teams better prepare for and respond to weather-related challenges while maintaining project momentum and ensuring quality standards are met.
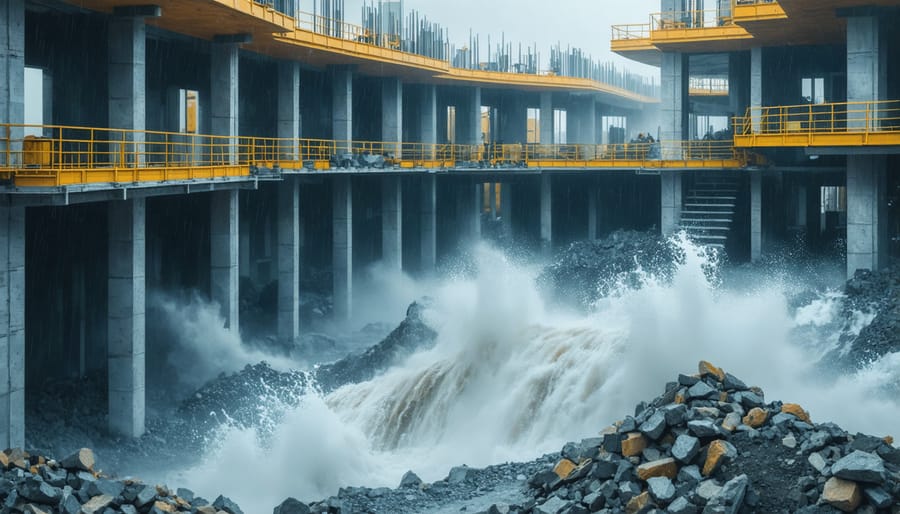
Site Contamination and Remediation Challenges
Site contamination and remediation challenges represent significant risks in construction project management, often emerging unexpectedly during excavation or site preparation phases. These environmental issues can range from discovering hazardous materials and contaminated soil to encountering underground storage tanks or historical industrial waste.
A recent case study from the Brighton Development Project revealed how unexpected asbestos contamination led to a three-month delay and a 15% budget increase. The discovery required specialized remediation teams, additional environmental assessments, and extensive documentation to ensure compliance with regulatory requirements.
Project managers must implement comprehensive site investigation protocols before breaking ground, including:
– Historical land use research
– Geological surveys
– Environmental impact assessments
– Soil testing at multiple depths
– Groundwater analysis
When contamination is discovered, immediate action is crucial. This includes:
– Securing the affected area
– Notifying relevant authorities
– Engaging environmental specialists
– Developing remediation strategies
– Adjusting project timelines and budgets
To mitigate these risks, successful project managers incorporate contingency plans and environmental risk assessments into their initial project planning. This includes allocating budget reserves specifically for potential remediation activities and maintaining relationships with environmental consultants who can respond quickly when issues arise.
Insurance coverage specifically for environmental risks should be secured, and contracts should clearly define responsibilities and procedures for handling contamination discoveries. Regular monitoring and documentation throughout the project help ensure compliance and protect against future liability claims.
Technical Performance Risks
Innovative Material Performance Uncertainty
The adoption of innovative sustainable materials in construction projects introduces unique performance uncertainties that project managers must carefully evaluate and mitigate. While these materials offer promising environmental benefits, their long-term durability and behavior under various conditions may not be fully understood due to limited historical performance data.
Key uncertainty factors include material degradation rates, weathering resistance, and structural integrity over extended periods. For instance, bio-based composites may exhibit unexpected aging characteristics, while recycled aggregates might demonstrate varying strength properties depending on their source and processing methods.
Project managers face particular challenges when integrating these materials into critical building components. Performance warranties and insurance coverage may be limited or unavailable for newer materials, potentially exposing projects to increased liability risks. Additionally, local building codes and standards may not fully address these materials, creating regulatory compliance uncertainties.
To manage these risks effectively, project managers should:
– Conduct extensive material testing before full-scale implementation
– Document performance metrics through pilot installations
– Establish robust monitoring systems for early detection of potential issues
– Maintain detailed performance records for future reference
– Develop contingency plans for material replacement if necessary
Industry experience shows that successful risk mitigation often requires collaboration with material manufacturers, testing laboratories, and insurance providers. Regular assessment of material performance against established benchmarks helps identify potential issues before they become critical problems, enabling proactive intervention and adjustment of implementation strategies.
System Integration Challenges
The integration of traditional and sustainable building systems presents significant project management challenges that can impact timeline, budget, and overall project success. A primary concern lies in the compatibility between existing infrastructure and new sustainable technologies. For instance, retrofitting modern energy management systems into conventional HVAC frameworks often requires extensive modification of control interfaces and operating protocols.
Technical conflicts frequently arise when merging renewable energy systems with traditional power distribution networks. Project managers must carefully coordinate the installation of solar panels or wind turbines while maintaining uninterrupted power supply, often necessitating temporary systems and careful phasing of integration work.
Material compatibility poses another substantial risk. Sustainable materials may interact differently with conventional building components, potentially affecting structural integrity or system performance. For example, eco-friendly insulation materials might require different vapor barriers or installation techniques than traditional options, demanding additional expertise and quality control measures.
Performance verification becomes more complex when combining different system types. Traditional metrics may not adequately capture the effectiveness of hybrid solutions, requiring new testing protocols and monitoring systems. This challenge is particularly evident in projects involving smart building technologies integrated with conventional mechanical systems.
Risk mitigation strategies should include:
– Detailed compatibility assessments during design phase
– Comprehensive testing protocols for integrated systems
– Specialized training for installation teams
– Clear documentation of system interfaces
– Regular monitoring of system performance post-integration
Success in managing these risks requires early stakeholder engagement, thorough planning, and continuous adaptation of project management strategies to address emerging challenges in real-time.
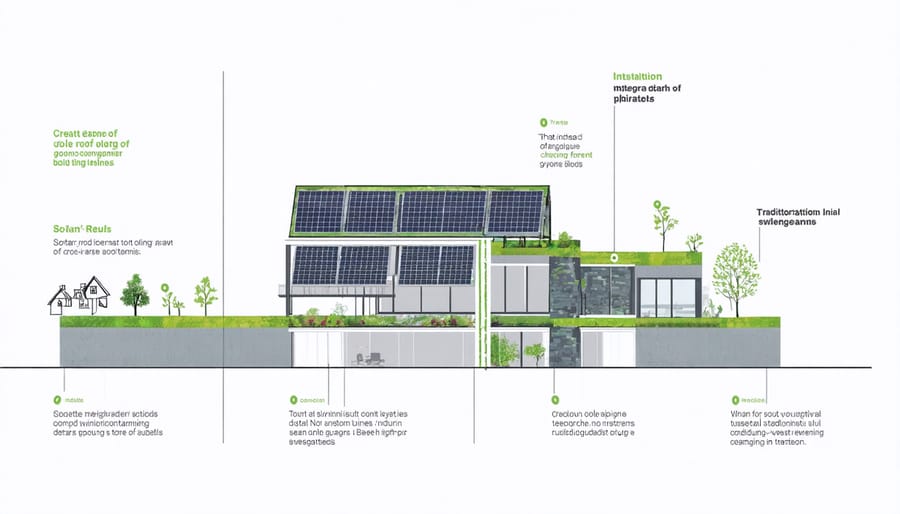
Financial Risk Management
Cost Overrun Prevention
Effective managing construction costs in green building projects requires a comprehensive approach to risk prevention and mitigation. Implementation of a robust cost control system begins with detailed pre-construction planning and accurate initial cost estimation, incorporating contingencies for sustainable materials and specialized green building requirements.
Key prevention strategies include establishing clear scope definitions with sustainability targets, implementing value engineering processes focused on long-term efficiency, and maintaining detailed cost tracking systems. Regular budget reviews should be conducted at predetermined project milestones, with particular attention to green certification requirements and their associated costs.
Project managers should implement a change order management system that evaluates the impact of modifications on both immediate costs and long-term sustainability goals. This includes assessing the financial implications of alternative materials or methods while ensuring compliance with green building standards.
Risk transfer mechanisms, such as performance bonds and insurance coverage specific to sustainable construction, can help protect against unexpected cost escalations. Additionally, developing strong relationships with suppliers of sustainable materials and maintaining accurate pricing databases helps prevent supply chain-related cost overruns.
Early identification of potential cost risks through regular team meetings and stakeholder communications allows for proactive rather than reactive management. Implementation of earned value management systems provides real-time insights into project performance and helps identify potential budget variances before they become significant issues.
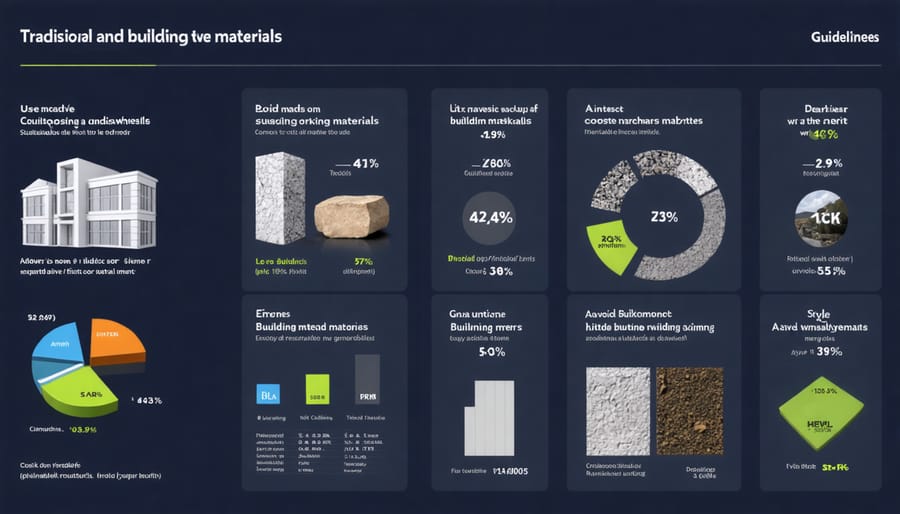
Certification and Compliance Costs
Certification and compliance costs represent a significant risk factor in sustainable construction projects, often impacting both budget and timeline considerations. According to industry data, certification-related expenses can account for 2-5% of the total project cost, varying based on the certification level sought and project complexity.
LEED, BREEAM, and other green building certifications require substantial documentation, third-party verification, and specialized consultants. These requirements can lead to unexpected cost escalations, particularly when certification criteria change mid-project or when additional testing becomes necessary to demonstrate compliance.
A notable challenge lies in the precise estimation of certification costs during the planning phase. Project managers must account for various components, including:
– Registration and certification fees
– Documentation preparation and submission
– Energy modeling and performance testing
– Commissioning services
– Specialized sustainable materials testing
– Consultant fees for certification guidance
Risk mitigation strategies should include:
– Early engagement with certification bodies
– Building contingency funds specifically for certification processes
– Regular updates on certification requirement changes
– Detailed tracking of documentation requirements
– Partnership with experienced sustainability consultants
Case studies indicate that projects incorporating certification costs into initial budgets and maintaining dedicated compliance teams experience fewer budget overruns. Additionally, establishing clear communication channels with certification bodies helps prevent costly delays and rework. Success in managing these costs often depends on maintaining comprehensive documentation systems and regular compliance audits throughout the project lifecycle.
Supply Chain and Resource Risks
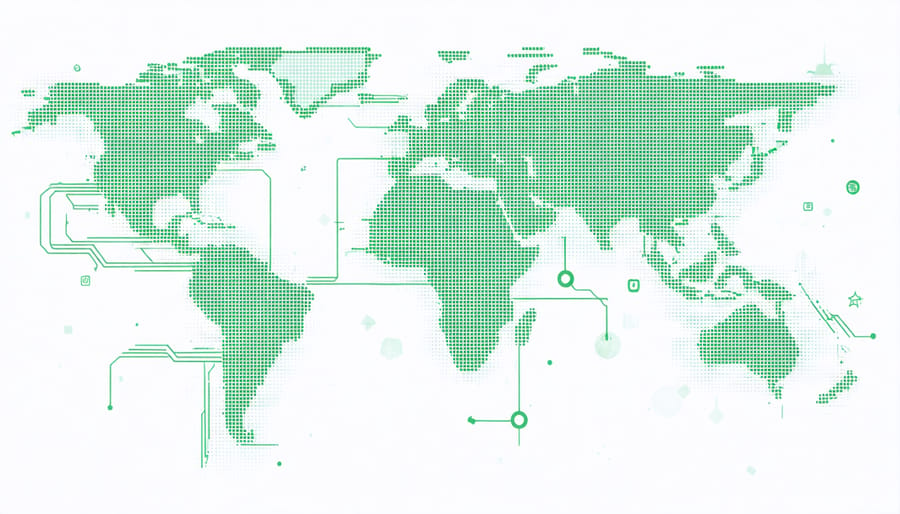
Sustainable Material Availability
In today’s construction landscape, managing the availability of sustainable materials presents a significant project risk that requires careful consideration and strategic planning. Effective sustainable supply chain management becomes crucial as demand for eco-friendly materials continues to rise.
Key risk factors include fluctuating availability of certified sustainable timber, recycled materials, and low-carbon alternatives to traditional construction materials. Recent industry data shows that 68% of construction projects face delays due to sustainable material procurement challenges, while 42% experience cost overruns related to material availability issues.
To mitigate these risks, project managers should implement several strategic measures:
1. Develop relationships with multiple suppliers to ensure alternative sourcing options
2. Maintain detailed material forecasting systems that account for seasonal variations
3. Include buffer times in project schedules for potential supply chain disruptions
4. Consider local sourcing options to reduce dependency on long-distance transportation
5. Implement early procurement strategies for critical sustainable materials
Case Study: The Henderson Green Building Project successfully navigated material shortages by establishing early agreements with suppliers and maintaining a flexible specification approach that allowed for alternative certified materials when primary choices became unavailable.
Proactive risk assessment and regular supplier audits remain essential components of managing sustainable material availability. Projects should maintain detailed contingency plans and regularly update them based on market conditions and supplier capabilities.
Skilled Labor Shortages
The sustainable construction sector faces a significant challenge in securing qualified workers with specialized skills in green building practices, energy-efficient systems, and sustainable materials installation. According to industry surveys, 78% of construction firms report difficulty finding workers with adequate sustainability expertise, creating substantial project delays and increased costs.
This shortage particularly affects critical roles such as LEED-certified professionals, renewable energy system installers, and energy efficiency specialists. The gap between available talent and project demands often results in extended timelines, compromised quality, and increased labor costs as companies compete for limited skilled workers.
To mitigate these risks, successful project managers implement multi-faceted strategies. These include developing partnerships with technical schools and universities, creating in-house training programs focused on sustainable construction practices, and establishing mentor-apprentice relationships within their organizations. Some firms have found success in cross-training existing workers in sustainable practices while gradually building specialized teams.
Project planning should account for this challenge by incorporating longer lead times for specialized work packages and budgeting for higher labor costs. Additionally, maintaining relationships with staffing agencies specializing in sustainable construction and developing a network of reliable subcontractors can provide flexibility when internal resources are stretched thin. Documentation of critical procedures and standardization of sustainable practices can help transfer knowledge effectively and reduce dependence on individual expertise.
Risk Mitigation Strategies
Implementing effective risk mitigation strategies requires a systematic approach that combines preventive measures with responsive actions. For environmental risks, establishing comprehensive site assessment protocols and maintaining flexible scheduling to accommodate weather-related delays can significantly reduce impact. This includes developing detailed contingency plans for extreme weather events and ensuring proper drainage systems are in place before construction begins.
Technical risks can be addressed through rigorous quality control measures and regular equipment maintenance schedules. Implementing Building Information Modeling (BIM) technology helps identify potential conflicts early in the design phase, while systematic documentation of technical specifications ensures alignment with sustainable construction requirements.
Financial risk management involves creating detailed cost contingency reserves, typically 5-15% of the project budget, depending on complexity. Regular cost monitoring and establishing clear change order procedures help maintain budget control. Performance bonds and insurance coverage should be carefully structured to protect against major financial setbacks.
Supply chain risks require developing relationships with multiple suppliers and maintaining buffer stock for critical materials. Creating a vendor rating system helps identify reliable suppliers while monitoring market conditions enables proactive response to potential shortages or price fluctuations.
For regulatory compliance risks, staying current with sustainable construction regulations through membership in industry associations and regular staff training is essential. Maintaining open communication channels with regulatory bodies and conducting periodic compliance audits helps prevent violations.
Stakeholder-related risks can be minimized through transparent communication protocols and regular progress updates. Establishing clear escalation procedures and maintaining detailed documentation of all stakeholder interactions helps prevent misunderstandings and supports conflict resolution.
These strategies should be regularly reviewed and updated based on project performance metrics and changing conditions, ensuring their continued effectiveness throughout the project lifecycle.
Effective risk management in sustainable construction projects requires a proactive, comprehensive approach that evolves with industry developments. As demonstrated throughout this analysis, successful project managers must balance traditional construction risks with emerging challenges specific to sustainable building practices. The increasing complexity of green building technologies and stringent environmental regulations demands sophisticated risk assessment frameworks and mitigation strategies.
Looking ahead, the construction industry faces new challenges and opportunities in risk management. Climate change considerations, evolving sustainability standards, and technological advancements will continue to reshape risk landscapes. Project managers must stay informed about emerging risks while maintaining flexibility in their management approaches. This includes investing in advanced risk assessment tools, strengthening supply chain resilience, and developing team expertise in sustainable construction methods.
Key to future success will be the integration of data analytics and digital tools in risk management processes, enabling more accurate risk prediction and real-time monitoring. Additionally, collaboration between stakeholders, from designers to contractors, will become increasingly crucial in managing complex sustainability-related risks effectively.
As the industry continues to embrace sustainable practices, organizations that develop robust risk management frameworks while maintaining adaptability will be better positioned to deliver successful projects. This includes regular updates to risk assessment protocols, continuous team training, and strong communication channels with all project stakeholders. The future of sustainable construction risk management lies in balancing innovation with proven risk mitigation strategies.