The construction industry faces an unprecedented challenge to slash its 11% contribution to global greenhouse gas emissions through reducing building emissions, with embodied carbon emerging as a critical focal point. Smart material selection, optimized structural design, and innovative construction methodologies now offer concrete pathways to significantly decrease carbon footprints across building lifecycles.
Leading construction firms have demonstrated that embodied carbon reductions of 30-50% are achievable through strategic interventions during early design phases. By analyzing Environmental Product Declarations (EPDs), implementing carbon calculation tools, and leveraging emerging low-carbon alternatives like supplementary cementitious materials, project teams can systematically reduce their environmental impact while maintaining structural integrity and cost-effectiveness.
The urgency of this transformation cannot be overstated. With building stock expected to double by 2060, decisions made today about materials, design approaches, and construction methods will lock in emissions for decades. Industry professionals must act now to integrate carbon reduction strategies into their standard practices, positioning their organizations at the forefront of sustainable construction while meeting increasingly stringent regulatory requirements and client demands for environmental responsibility.
Understanding Embodied Carbon in Construction Materials
Primary Sources of Embodied Carbon
Concrete and steel remain the largest contributors to embodied carbon in construction, accounting for approximately 16% and 7% of global carbon emissions respectively. Concrete’s high carbon footprint stems primarily from cement production, where the calcination process releases significant CO2. Steel manufacturing requires extensive energy consumption and coal usage in blast furnaces, resulting in substantial emissions during production.
Other significant sources include aluminum (high-energy intensive production), glass (heat-intensive manufacturing), and traditional insulation materials. Building envelope materials, particularly those derived from petroleum products like certain membranes and synthetic insulations, also contribute notably to a project’s carbon footprint.
Transportation of materials to construction sites adds another layer of embodied carbon, with heavy materials shipped over long distances having particularly high impacts. Manufacturing processes, including extraction of raw materials and factory operations, constitute a significant portion of these emissions.
Recent industry analyses indicate that foundation systems and structural elements typically represent 50-70% of a building’s total embodied carbon, highlighting the critical importance of material selection and design optimization in these areas.
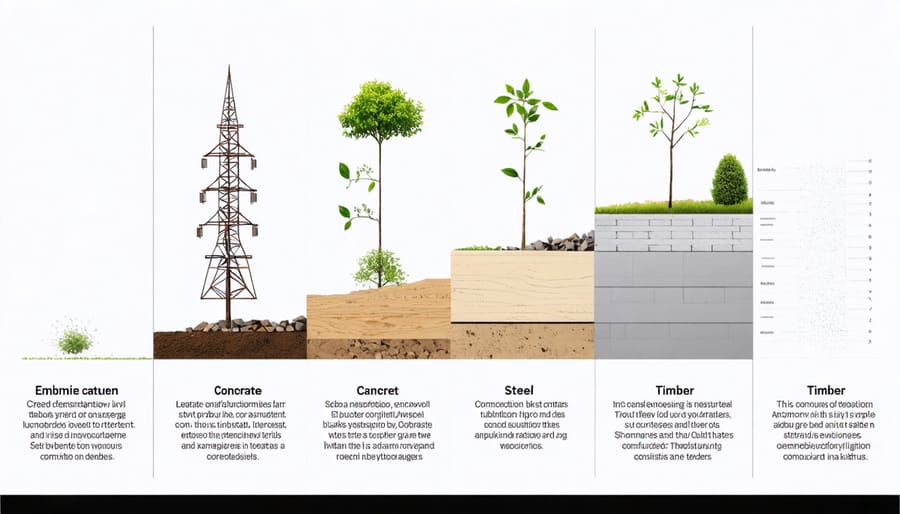
Measuring and Calculating Embodied Carbon
Measuring embodied carbon requires a systematic approach combining data collection, analysis, and standardized calculation methods. The most widely adopted tool is Life Cycle Assessment (LCA), which evaluates environmental impacts throughout a material’s lifecycle from extraction to disposal. Industry professionals typically use specialized software like One Click LCA, Tally, or EC3 to perform these calculations efficiently.
The process begins with gathering Environmental Product Declarations (EPDs) from material suppliers, which provide verified data about products’ environmental impact. These declarations serve as crucial inputs for accurate carbon calculations. Project teams must also consider transportation distances, construction methods, and waste factors in their assessments.
Key stages for measurement include product stage (A1-A3), construction process (A4-A5), use stage (B1-B7), and end-of-life (C1-C4). The World Green Building Council and other regulatory bodies have established standardized methodologies for these calculations, ensuring consistency across projects.
For optimal accuracy, measurements should be conducted throughout the project lifecycle, from early design stages through construction completion, allowing for real-time adjustments and improvements in carbon reduction strategies.
Innovative Material Solutions
Low-Carbon Concrete Alternatives
Recent advancements in low-carbon concrete alternatives have revolutionized the construction industry’s approach to reducing embodied carbon. Geopolymer concrete, which replaces traditional Portland cement with industrial by-products like fly ash and slag, can reduce carbon emissions by up to 80% compared to conventional concrete mixtures. Similarly, carbon-cured concrete technology actively sequesters CO2 during the curing process, transforming it into calcium carbonate that enhances the material’s strength.
Innovative supplementary cementitious materials (SCMs) are gaining traction, with ground glass pozzolan and calcined clay showing promising results in both environmental performance and structural integrity. These alternatives not only reduce the carbon footprint but often deliver superior durability and chemical resistance.
Recent case studies demonstrate the practical application of these technologies. The One Bangkok development successfully utilized concrete with a 50% cement replacement, achieving both structural requirements and significant carbon reductions. Additionally, emerging research into bio-based alternatives, such as mycelium-enhanced concrete and algae-infused mixtures, suggests future possibilities for even lower-carbon solutions.
However, adoption challenges remain, including material availability, code compliance, and initial cost considerations. Construction professionals must carefully evaluate these alternatives based on project-specific requirements, local regulations, and long-term performance criteria.
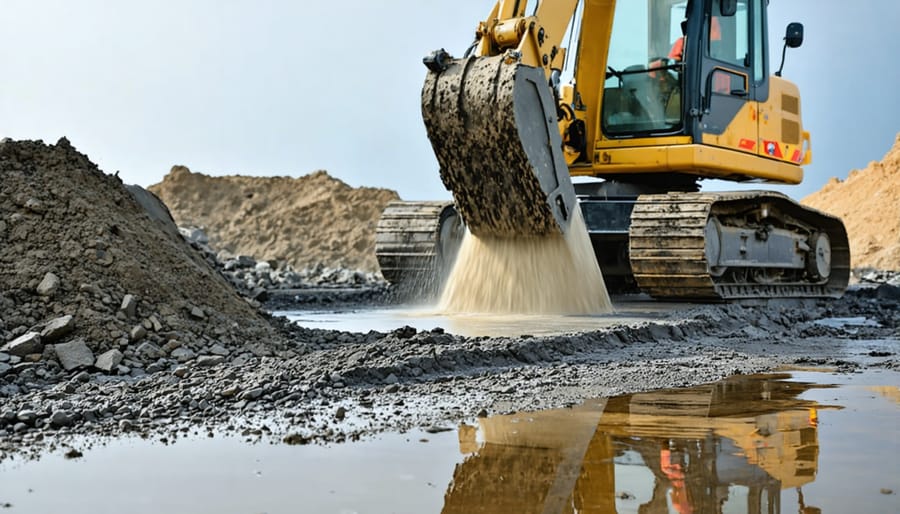
Sustainable Steel and Timber Options
Structural steel and timber represent two of the most promising sustainable building materials for reducing embodied carbon in construction projects. Advanced steel manufacturing processes now incorporate recycled content and electric arc furnaces, significantly lowering carbon emissions compared to traditional blast furnace production. High-strength steel grades enable designers to achieve the same structural performance with less material, further reducing the carbon footprint.
Mass timber has emerged as a revolutionary alternative, offering carbon sequestration benefits while maintaining structural integrity. Cross-laminated timber (CLT) and glue-laminated timber (glulam) products enable the construction of tall buildings previously only possible with steel and concrete. Studies indicate that mass timber buildings can reduce embodied carbon by 25-45% compared to conventional steel and concrete structures.
Hybrid solutions combining steel and timber are gaining traction, leveraging the strengths of both materials. Steel connections enhance timber’s structural capabilities, while timber elements reduce the overall steel quantity required. This approach has proven particularly effective in mid-rise commercial buildings, where optimal material selection can maximize carbon reduction while meeting performance requirements.
Recent innovations in steel recycling and sustainable forestry practices continue to improve these materials’ environmental credentials, making them increasingly attractive options for carbon-conscious construction projects.
Design Strategies for Carbon Reduction
Early-Stage Design Considerations
Early-stage design decisions have the most significant impact on a project’s embodied carbon footprint, often determining up to 80% of the building’s lifetime carbon emissions. Project teams must prioritize carbon reduction strategies during the conceptual and schematic design phases, integrating circular economy principles in construction from the outset.
Key considerations include building orientation, form factor optimization, and structural system selection. Teams should conduct preliminary life cycle assessments to evaluate different design options and their carbon implications. Material selection plays a crucial role, with emphasis on locally sourced materials, recycled content, and low-carbon alternatives to traditional building materials.
The implementation of modular design strategies and standardized components can significantly reduce material waste while facilitating future adaptability and deconstruction. Design teams should also consider the building’s projected lifespan and potential for future modifications, ensuring that the initial carbon investment delivers long-term value.
Collaboration between architects, engineers, and sustainability consultants during these early stages is essential for identifying innovative solutions and optimizing design decisions for maximum carbon reduction potential. This integrated approach ensures that embodied carbon considerations are embedded in the project’s DNA rather than treated as an afterthought.
Material Efficiency and Optimization
Material efficiency and optimization stand as crucial strategies in reducing embodied carbon, focusing on using fewer materials while maintaining structural performance. Advanced design techniques, such as topology optimization and parametric modeling, enable engineers to identify and eliminate excess material without compromising structural integrity.
Lean construction methods play a vital role, emphasizing precise material quantity calculations and minimizing waste through careful planning. Building Information Modeling (BIM) technology facilitates accurate material quantity takeoffs and helps identify potential conflicts before construction begins, reducing material waste from rework.
Innovative structural solutions include void formers in concrete slabs, lightweight composite materials, and optimized steel sections that reduce material volume while meeting load requirements. The implementation of high-strength materials allows for smaller structural elements, effectively decreasing the overall material quantity needed.
Design standardization and modular construction contribute significantly to material efficiency by reducing cutting waste and enabling more precise material ordering. Prefabrication in controlled environments typically results in 20-30% less material waste compared to traditional on-site construction.
Regular material audits and waste tracking systems help identify opportunities for further optimization. Construction teams can implement closed-loop material management systems, ensuring excess materials from one project can be effectively utilized in another, maximizing resource efficiency.
Real-World Implementation
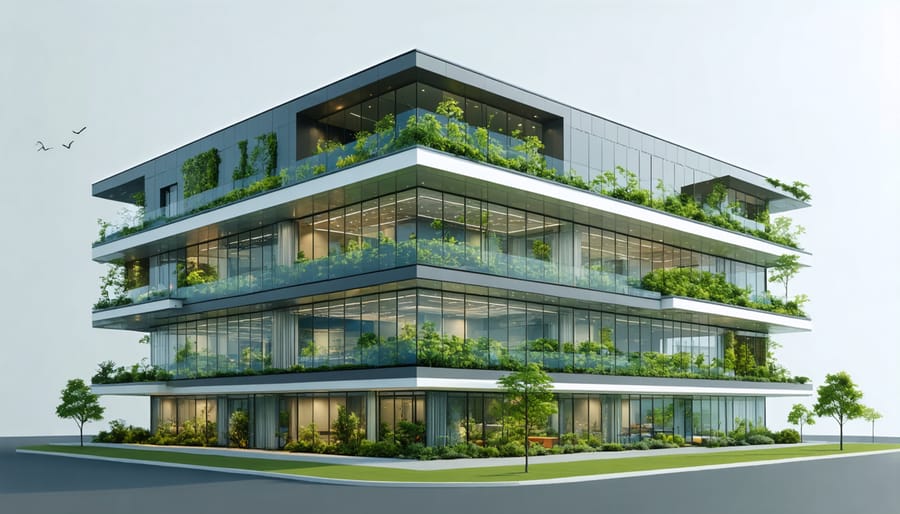
Case Study: Commercial Building Success
The Commerce Square project in Seattle stands as a compelling example of successful embodied carbon reduction in commercial construction. This 12-story, 280,000-square-foot office building achieved a remarkable 30% reduction in embodied carbon compared to conventional construction methods.
The project team prioritized carbon reduction from the outset, implementing several key strategies. They utilized low-carbon concrete mixes, reducing cement content by 40% through the incorporation of ground granulated blast furnace slag and fly ash. The structural design optimized steel usage, resulting in a 25% reduction in steel tonnage while maintaining structural integrity.
Material sourcing played a crucial role, with 80% of materials sourced within 500 miles of the construction site. The team selected suppliers based on Environmental Product Declarations (EPDs) and verified carbon footprint data. Notably, they specified mass timber for interior elements, sequestering approximately 1,200 metric tons of CO2.
The project’s success was documented through comprehensive carbon tracking throughout construction. Final calculations showed total embodied carbon savings of 3,500 metric tons CO2e compared to baseline designs. The additional cost premium was just 2.3%, which was offset by enhanced marketability and higher occupancy rates.
This case study demonstrates that significant embodied carbon reductions are achievable in commercial construction while maintaining project viability and financial performance. The strategies employed have since been adopted as best practices by several other commercial developments in the region.
Implementation Challenges and Solutions
Implementing embodied carbon reduction strategies often faces several significant challenges in the construction industry. Cost implications remain a primary concern, as low-carbon materials and technologies may require higher initial investments. However, many organizations have successfully addressed this through life-cycle cost analysis, demonstrating long-term financial benefits and improved project value.
Data availability and measurement accuracy present another substantial hurdle. Construction teams frequently struggle with incomplete environmental product declarations (EPDs) and inconsistent calculation methodologies. To combat this, industry leaders are developing standardized carbon measurement protocols and establishing comprehensive materials databases, enabling more accurate carbon assessments.
Supply chain complexity often impedes carbon reduction efforts, particularly when sourcing alternative materials. Successful projects have overcome this by engaging suppliers early in the design phase and establishing clear carbon requirements in procurement specifications. Some organizations have created preferred supplier networks based on verified environmental performance.
Regulatory uncertainty and varying regional standards can also complicate implementation. Forward-thinking companies are addressing this by adopting science-based targets and international best practices, often exceeding local requirements. This proactive approach helps future-proof projects against evolving regulations.
Technical knowledge gaps among project teams can slow progress. Leading firms are investing in staff training programs and partnering with carbon specialists to build internal expertise. Regular workshops and collaborative learning sessions have proven effective in developing team capabilities and maintaining momentum in carbon reduction initiatives.
Future Outlook and Industry Trends
The construction industry is witnessing a transformative shift towards innovative technologies and methodologies aimed at reducing embodied carbon. Advanced materials science is leading the development of low-carbon alternatives, including carbon-negative concrete formulations and bio-based building materials. Artificial Intelligence and machine learning are increasingly being deployed to optimize material selection and construction processes, enabling more precise carbon calculations and better decision-making during the design phase.
Emerging trends indicate a growing focus on circular economy principles, with manufacturers developing new ways to incorporate recycled materials and design for deconstruction. Digital twin technology is expected to play a crucial role in monitoring and managing embodied carbon throughout a building’s lifecycle, while blockchain solutions are being explored to enhance supply chain transparency and carbon tracking.
Industry experts predict that policy frameworks will continue to evolve, with more regions implementing mandatory embodied carbon reporting and setting increasingly stringent reduction targets. The development of standardized measurement protocols and improved data accessibility will facilitate more accurate carbon accounting across the construction sector.
Looking ahead, the integration of robotics and automated construction methods promises to optimize material usage and reduce waste. Additionally, the rise of carbon capture and utilization technologies may create new opportunities for incorporating sequestered carbon into building materials, potentially transforming construction products from carbon sources to carbon sinks.
Reducing embodied carbon in construction projects requires a comprehensive, multi-faceted approach that begins at the planning stage and continues throughout the building lifecycle. Construction professionals must prioritize material selection, focusing on low-carbon alternatives, recycled content, and locally sourced options. Implementation of carbon calculation tools and life cycle assessments should become standard practice in project planning.
Key actionable steps include establishing baseline carbon measurements for projects, setting specific reduction targets, and maintaining detailed documentation of carbon reduction strategies. Professionals should also invest in upskilling their teams in carbon literacy and sustainable construction practices.
Success in embodied carbon reduction depends on collaboration across the supply chain and early engagement with stakeholders. Project managers should integrate carbon considerations into procurement decisions and maintain open communication with suppliers about carbon reduction goals.
Moving forward, industry professionals must stay informed about emerging technologies, updated building codes, and evolving best practices. By combining traditional construction expertise with innovative sustainable solutions, we can significantly impact the industry’s carbon footprint while maintaining project efficiency and cost-effectiveness.
The transition to low-carbon construction is not just an environmental imperative but a business opportunity that positions firms for future success in an increasingly carbon-conscious market.