Transform traditional construction supply chains through data-driven material tracking, real-time inventory management, and intelligent waste reduction protocols to achieve true supply chain sustainability. Implement blockchain-enabled material passports to verify sustainable sourcing, track embodied carbon metrics, and ensure complete supply chain transparency from extraction to installation. Partner strategically with local suppliers who maintain ISO 14001 environmental management certification, reducing transportation emissions while supporting regional economic development. Deploy smart logistics platforms that optimize delivery routes, minimize idle time, and enable just-in-time material staging to reduce on-site waste and storage requirements.
These proven approaches have delivered measurable results across major construction projects, with industry leaders reporting up to 30% reduction in material waste and 25% decrease in transportation-related emissions. Leading construction firms integrate these practices into their core operations, creating resilient supply networks that withstand disruption while advancing environmental stewardship. The construction sector’s environmental impact demands immediate action – these strategies provide the framework for meaningful transformation while maintaining operational excellence.
Digital Integration: The Foundation of Sustainable Supply Chains
Real-time Inventory Management Systems
Real-time inventory management systems have revolutionized construction resource management, enabling unprecedented control over material flows and waste reduction. IoT sensors deployed across construction sites and warehouses provide continuous monitoring of material levels, usage patterns, and storage conditions. These smart systems integrate with cloud-based platforms to deliver actionable insights through real-time analytics.
Advanced RFID tags and GPS tracking devices monitor the movement of materials from suppliers to construction sites, ensuring optimal inventory levels while minimizing excess storage and potential waste. The system automatically triggers reorder notifications when supplies reach predetermined thresholds, preventing both stockouts and overordering.
Environmental sensors monitor storage conditions, protecting sensitive materials from deterioration and reducing waste due to improper storage. This technology has proven particularly valuable for temperature-sensitive materials like concrete additives and adhesives.
Industry leaders report up to 30% reduction in material waste and a 25% improvement in inventory turnover after implementing these systems. The real-time visibility also supports better decision-making in procurement, allowing project managers to optimize ordering schedules and quantities based on actual usage data rather than estimates.
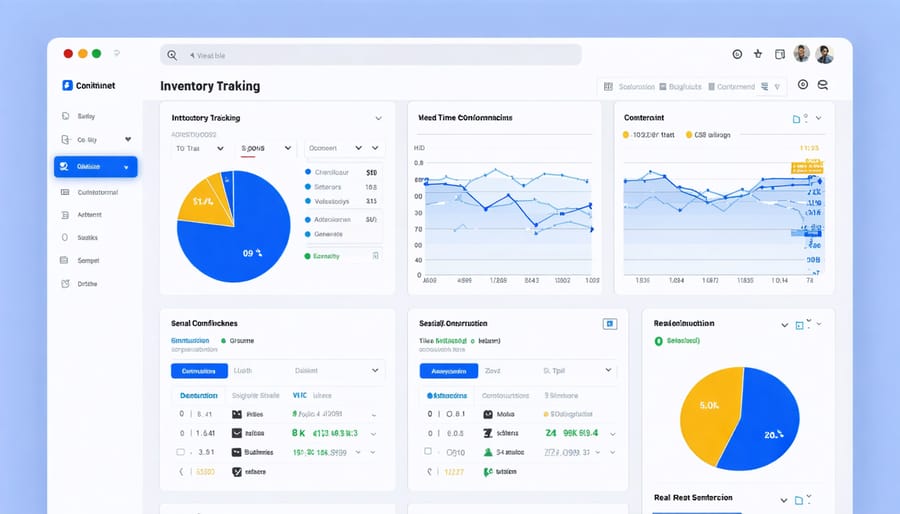
Predictive Analytics for Material Planning
Predictive analytics has revolutionized material planning in sustainable construction by leveraging historical data, machine learning algorithms, and real-time monitoring to optimize ordering processes and minimize waste. Construction firms implementing these data-driven approaches typically achieve a 15-20% reduction in material waste and a 25% improvement in inventory management efficiency.
Advanced analytics platforms now integrate multiple data sources, including weather patterns, supplier lead times, project timelines, and historical consumption rates, to generate accurate demand forecasts. This enables project managers to maintain optimal inventory levels while reducing the environmental impact of excess storage and disposal.
Case studies from leading construction companies demonstrate that AI-powered material planning systems can identify patterns in material usage, anticipate potential shortages, and automatically adjust orders based on real-time project progress. For example, a major commercial builder reduced their material waste by 30% and storage costs by 40% through implementing predictive analytics.
Key benefits include:
– Reduced overordering and associated waste
– Lower transportation emissions through optimized delivery schedules
– Improved cash flow through precise inventory management
– Enhanced supplier relationship management
– Better compliance with sustainability targets
To maximize effectiveness, these systems should be integrated with existing project management software and regularly calibrated using actual consumption data.
Circular Economy Principles in Construction
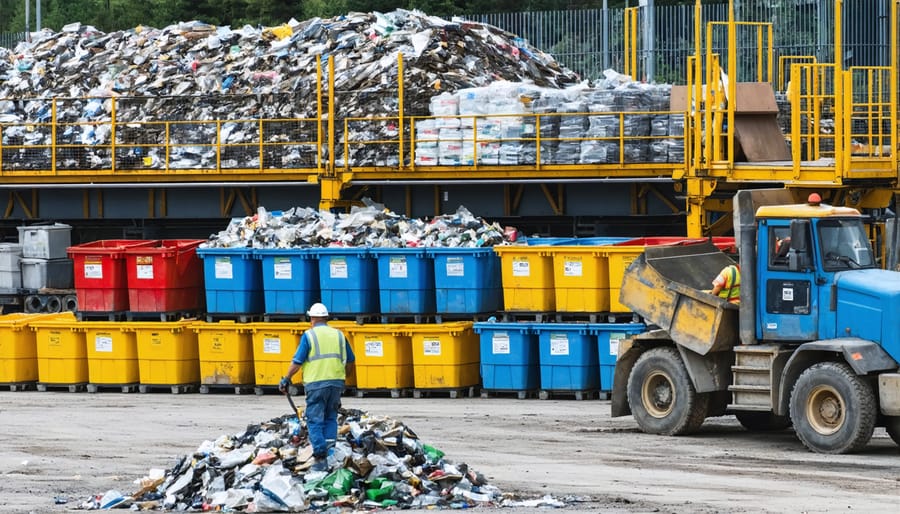
Material Recovery and Recycling Programs
Implementing effective material recovery and recycling programs on construction sites requires a systematic approach that aligns with modern zero waste initiatives. The first step is establishing a comprehensive waste sorting system with clearly marked containers for different materials: metals, wood, concrete, plastics, and mixed recyclables. This segregation at the source significantly increases recycling efficiency and material recovery rates.
Site managers should implement a materials tracking system that monitors waste generation and recycling performance. Digital tools and software can help track waste metrics, providing valuable data for optimization and reporting. Regular training sessions for workers on proper waste sorting and handling procedures are essential for program success.
Partner with certified recycling facilities that specialize in construction waste processing. These facilities should provide documentation of material recovery rates and final disposition of recycled materials. Consider implementing reverse logistics systems where suppliers take back excess materials and packaging for reuse or recycling.
For concrete and masonry waste, mobile crushing units can process materials on-site for immediate reuse as aggregate or fill. Wood waste can be processed for mulch or biomass fuel, while metals should be sorted by type to maximize recycling value. Establish clear performance indicators and regular audits to ensure continuous improvement of recycling programs.
Design for Disassembly
Design for Disassembly (DfD) represents a forward-thinking approach to sustainable construction that considers a building’s entire lifecycle, including its eventual deconstruction. This innovative methodology enables the efficient recovery and reuse of building materials, significantly reducing waste and environmental impact while creating opportunities for material recycling and repurposing.
At its core, DfD principles emphasize the use of mechanical connections over chemical bonds, making it easier to separate materials during demolition. Key strategies include utilizing standardized, modular components, avoiding composite materials where possible, and implementing reversible connections such as bolts and screws instead of adhesives or welding.
Industry leaders are increasingly adopting BIM (Building Information Modeling) technology to document material specifications and assembly methods, creating detailed “material passports” that facilitate future disassembly. These digital records ensure that future contractors can efficiently identify, separate, and salvage valuable materials.
Notable examples include the Circle House project in Denmark, where 90% of its materials can be disassembled and reused without losing value. The project demonstrates how proper material selection and innovative connection designs can support circular economy principles in construction.
To implement DfD effectively, designers must consider:
– Accessibility of connections
– Material durability and longevity
– Standardization of components
– Clear labeling and documentation
– Minimization of different material types
– Sequential assembly and disassembly processes
This approach not only supports environmental sustainability but also creates economic value through material recovery and reduced disposal costs.
Green Transportation and Logistics
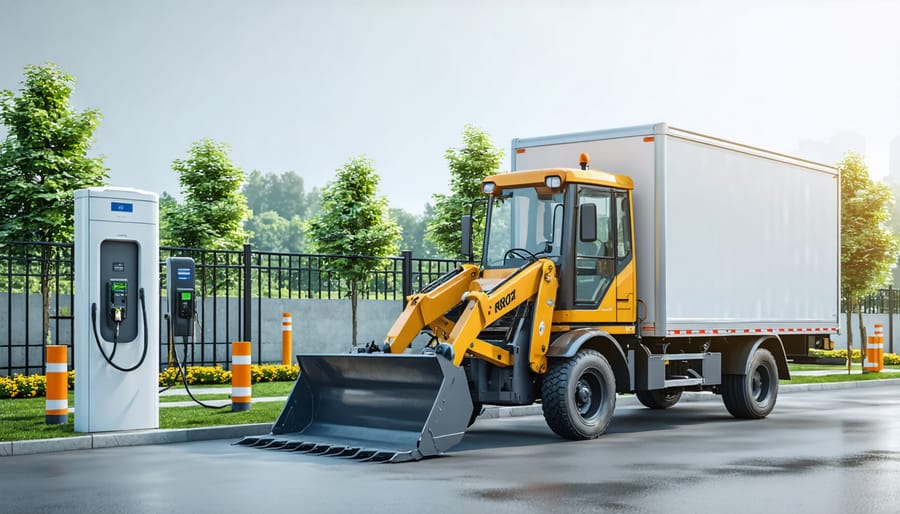
Route Optimization Technologies
Advanced route optimization technologies are revolutionizing construction supply chains by significantly reducing fuel consumption and carbon emissions. AI-powered routing systems analyze multiple variables, including traffic patterns, delivery schedules, and vehicle capacity, to determine the most efficient delivery paths. These smart systems can reduce fuel consumption by up to 20% while maintaining timely material deliveries to construction sites.
Real-time GPS tracking and dynamic route adjustment capabilities allow fleet managers to respond instantly to changing conditions, such as traffic congestion or weather events. Construction companies implementing these technologies report average reductions of 15-25% in total miles driven and corresponding decreases in carbon emissions.
Leading construction firms are integrating these routing systems with their inventory management platforms to optimize load consolidation and reduce empty return trips. This integration enables better coordination between suppliers, warehouses, and construction sites, resulting in fewer vehicle movements and improved resource utilization.
The technology also provides valuable data analytics for continuous improvement, helping companies identify patterns and opportunities for further optimization in their supply chain operations. Construction managers can use these insights to make informed decisions about supplier locations, storage facilities, and delivery schedules.
Alternative Fuel Vehicles
The construction industry is increasingly adopting alternative fuel vehicles to reduce its carbon footprint and operational costs in logistics and material transportation. Electric vehicles (EVs) and hybrid trucks are becoming prominent choices for both on-site operations and supply chain logistics. Leading construction firms report up to 40% reduction in fuel costs and significant decreases in emissions after incorporating electric forklifts and hybrid delivery trucks into their fleets.
Battery-powered construction vehicles, particularly in material handling and short-distance transport, demonstrate exceptional performance while producing zero direct emissions. Hybrid vehicles offer flexibility for longer routes and heavier loads, combining the benefits of electric power with conventional fuel efficiency. Companies implementing these solutions often utilize smart charging infrastructure and route optimization software to maximize vehicle efficiency.
Recent technological advances have extended battery life and reduced charging times, making electric vehicles more practical for construction applications. The integration of telematics systems allows fleet managers to monitor vehicle performance, optimize routes, and schedule maintenance proactively. While initial investment costs remain higher than traditional vehicles, the long-term benefits include reduced maintenance requirements, lower operating costs, and compliance with increasingly stringent environmental regulations.
Supplier Collaboration and Certification
Environmental Certification Standards
Environmental certification standards play a crucial role in validating and benchmarking sustainable supply chain practices in construction. Leading certifications such as LEED (Leadership in Energy and Environmental Design), BREEAM (Building Research Establishment Environmental Assessment Method), and FSC (Forest Stewardship Council) provide comprehensive frameworks for evaluating material sourcing, transportation, and waste management practices.
These certifications ensure compliance with stringent environmental requirements while offering tangible benefits to construction companies. For instance, FSC certification guarantees that wood products come from responsibly managed forests, while LEED certification encompasses broader supply chain considerations, including material transportation distances and recycled content percentages.
ISO 14001 certification specifically addresses environmental management systems, helping organizations systematically improve their supply chain sustainability. Meanwhile, the Green Building Initiative’s Green Globes certification offers alternative pathways for sustainable material sourcing and supply chain optimization.
To maintain certification standards, organizations must regularly audit their supply chains, document compliance, and demonstrate continuous improvement. This process often involves tracking key performance indicators (KPIs) such as carbon emissions, waste reduction, and resource efficiency. Construction companies that achieve these certifications typically experience enhanced market reputation, improved stakeholder trust, and better access to sustainable building projects.
Supplier Education Programs
Supplier education programs form a crucial component of sustainable supply chain management in construction. These initiatives equip suppliers with the knowledge and tools necessary to implement environmentally responsible practices throughout their operations. Leading construction firms are developing comprehensive training modules that cover essential topics such as waste reduction, energy efficiency, and responsible material sourcing.
Successful programs typically incorporate both online learning platforms and hands-on workshops, allowing suppliers to understand sustainable practices in theory and application. Regular assessments and certification processes ensure suppliers maintain high standards and continue to improve their environmental performance. Many organizations have found that implementing supplier mentorship programs, where experienced vendors guide newer ones, significantly accelerates the adoption of sustainable practices.
Case studies from major construction projects demonstrate that educated suppliers consistently deliver better environmental outcomes. For instance, a recent infrastructure project in Singapore achieved a 30% reduction in carbon emissions after implementing a comprehensive supplier training program. Regular feedback sessions and performance monitoring help identify areas for improvement and ensure continuous development.
To maximize impact, these education programs should align with international sustainability standards and incorporate region-specific environmental regulations. This approach ensures suppliers meet both global best practices and local compliance requirements while fostering innovation in sustainable construction methods.
Case Study: Sustainable Supply Chain Success
One of the most compelling examples of sustainable supply chain implementation comes from Skanska’s Nordic operations, where they successfully transformed their traditional supply chain into a circular model. In 2019, the company initiated a comprehensive program focusing on material sourcing, waste reduction, and supplier collaboration.
The project began by implementing digital tracking systems for all construction materials, allowing real-time monitoring of resource usage and waste generation. Skanska partnered with 47 local suppliers who committed to sustainable practices, including using recycled materials and reducing packaging waste. They established a materials passport system, documenting the composition and potential reuse of all building materials.
Key achievements after two years included:
– 45% reduction in construction waste
– 32% decrease in carbon emissions from transportation
– 28% increase in recycled material usage
– 15% cost savings in material procurement
The success factors included:
– Early supplier engagement and clear sustainability requirements
– Investment in digital infrastructure for tracking and reporting
– Employee training programs focused on sustainable practices
– Regular performance monitoring and feedback loops
The initiative faced initial challenges, particularly resistance from some suppliers and higher upfront costs. However, Skanska overcame these through transparent communication, long-term partnership agreements, and demonstrating the financial benefits of sustainable practices.
This case study demonstrates that sustainable supply chain transformation is not only environmentally beneficial but also economically viable. The project’s success has led to its implementation across other Skanska operations globally, establishing a new industry benchmark for sustainable construction practices.
The transformation of construction supply chains toward sustainability is no longer optional but essential for industry survival and growth. As demonstrated throughout this analysis, successful implementation of sustainable practices requires a holistic approach combining technological innovation, strategic partnerships, and unwavering commitment to environmental stewardship.
Key success factors include digitalization of supply chain operations, careful supplier selection based on sustainability credentials, and investment in renewable materials and circular economy principles. Companies that have embraced these changes are already seeing benefits through reduced costs, enhanced reputation, and improved regulatory compliance.
Looking ahead, the construction industry faces both challenges and opportunities in further advancing sustainable supply chain practices. Emerging technologies like blockchain for transparency and AI for optimization will play increasingly important roles. Additionally, growing pressure from stakeholders and stricter environmental regulations will continue driving innovation in sustainable materials and processes.
For construction professionals, the path forward is clear: embrace sustainability as a core business strategy, invest in appropriate technologies and partnerships, and maintain flexibility to adapt to evolving best practices. Success in tomorrow’s construction industry will belong to those who act decisively today to build truly sustainable supply chains.