The transformation of construction waste into new building materials exemplifies how the circular economy in construction drives innovation and sustainability. Leading construction firms worldwide have demonstrated remarkable success through closed-loop material cycles, reducing raw material consumption by up to 40% while generating significant cost savings. From Heidelberg Cement’s concrete recycling initiatives to Interface’s carbon-negative flooring solutions, these pioneering examples showcase the practical implementation of circular principles across the construction value chain.
Industry leaders are revolutionizing traditional practices through innovative material passports, designing buildings for disassembly, and implementing smart waste management systems that track and optimize resource flows. These strategies not only minimize environmental impact but also create new revenue streams through material recovery and reuse. The construction sector’s transition to circular models represents a $4.5 trillion economic opportunity by 2030, with early adopters already reporting 15-25% improvements in project efficiency and resource utilization.
The evidence is clear: circular economy principles in construction deliver measurable environmental benefits while enhancing business performance through reduced material costs, improved operational efficiency, and strengthened market positioning.
Revolutionizing Concrete: The Circular Success Story
From Demolition to New Foundations
Several pioneering companies are revolutionizing the construction industry by transforming concrete waste into valuable new building materials. HeidelbergCement, through its subsidiary Recycling Park Renewi, has implemented a sophisticated sorting and processing system that recovers high-quality aggregates from demolition waste. In 2022, they successfully recycled over 500,000 tons of concrete debris, reducing landfill waste by 75% while producing certified recycled aggregates for new construction projects.
CarbonCure Technologies demonstrates another innovative approach by injecting captured CO2 into recycled concrete during the mixing process. This not only strengthens the final product but also permanently sequesters carbon dioxide, creating a double environmental benefit. Their technology has been implemented in over 400 concrete plants worldwide, with documented strength improvements of 10-20% in recycled concrete products.
The Dutch company StoneCycling has developed a groundbreaking method for transforming mixed demolition waste into new construction materials. Their “WasteBasedBricks” contain up to 60% recycled content and have been used in prestigious projects across Europe, including the CircularPavilion in Amsterdam. These bricks demonstrate comparable or superior performance metrics to traditional materials while reducing the carbon footprint by approximately 35%.
These success stories highlight how technological innovation and strategic partnerships can transform construction waste from a liability into a valuable resource, supporting both environmental sustainability and economic viability.
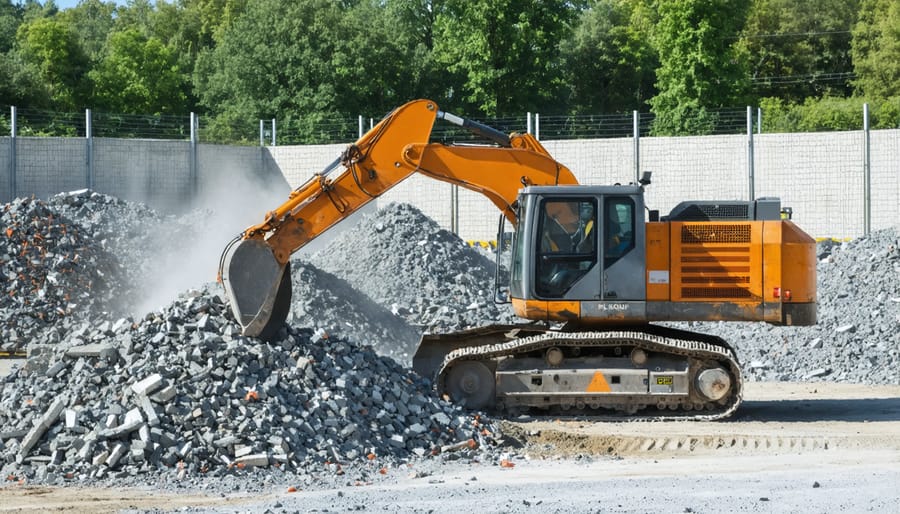
Advanced Concrete Recycling Technologies
Recent advancements in concrete recycling technologies have revolutionized how the construction industry approaches waste management and material recovery. Leading the way are state-of-the-art crushing systems equipped with smart sorting capabilities that can separate concrete from steel reinforcement with unprecedented precision. These systems utilize artificial intelligence and machine learning algorithms to optimize the recycling process, ensuring higher quality recycled aggregates.
Among the most promising developments are innovative concrete solutions that incorporate advanced mineral processing techniques. Smart crushing technologies now enable the separation of hydrated and unhydrated cement particles, allowing for the recovery of valuable binding materials that can be reused in new concrete production.
Specialized chemical treatment processes have emerged that can effectively remove contaminants and improve the quality of recycled concrete aggregates (RCA). These treatments enhance the mechanical properties of recycled materials, making them suitable for high-performance applications. Furthermore, new mobile recycling units equipped with multiple-stage crushing and cleaning systems allow for on-site processing, significantly reducing transportation costs and carbon emissions.
The integration of these technologies has demonstrated that recycled concrete can achieve performance characteristics comparable to virgin materials, meeting stringent industry standards while supporting circular economy principles in construction.
Steel’s Circular Revolution in Modern Construction
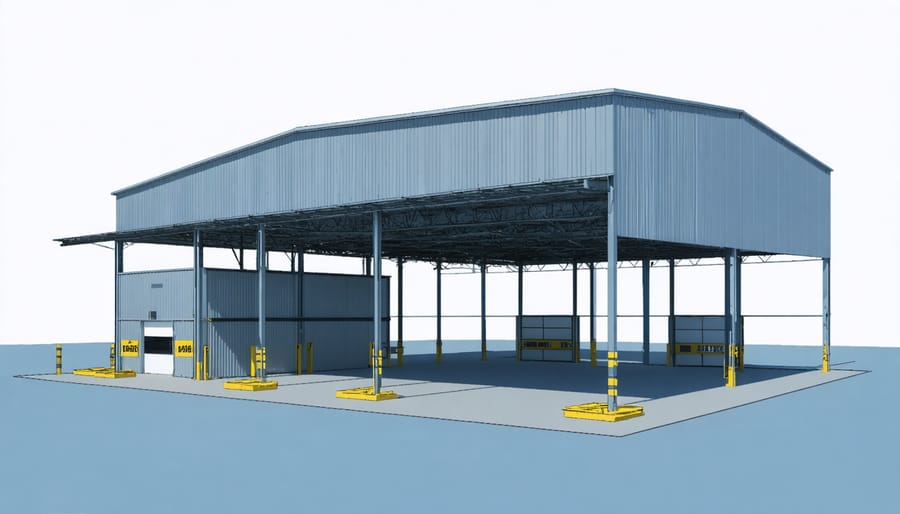
Modular Design: Building for Deconstruction
Leading construction companies are revolutionizing the industry through modular design principles that prioritize future material recovery and reuse. Steel structures, in particular, have become the focal point of this transformation, with innovative approaches to bolted connections replacing traditional welded joints.
A pioneering example is the Edge Olympic building in Amsterdam, designed by G30 Architects, which implements a fully demountable steel framework. The structure utilizes standardized bolt patterns and reversible connections, allowing for complete disassembly and reconstruction at end-of-life. This approach has resulted in an estimated 90% recovery potential for structural elements.
Major steel manufacturers are now producing standardized sections specifically designed for deconstruction. These components feature pre-engineered connection points and detailed material passports that track the steel’s properties and usage history. Companies like Tata Steel have developed dedicated product lines that incorporate these circular principles, ensuring their structural elements maintain value beyond their initial use.
The financial benefits are compelling: projects implementing these designs report 15-20% higher residual value compared to traditional construction methods. Furthermore, insurance companies are beginning to offer preferential rates for buildings designed with documented deconstruction plans, recognizing their reduced environmental risk and higher future asset value.
This shift toward modular design represents a significant step in transforming construction waste into valuable resources, creating a more sustainable and economically viable building industry.
Steel Upcycling Innovations
Recent innovations in steel upcycling have revolutionized the construction industry’s approach to material circularity. Advanced magnetic separation technologies now enable the recovery of high-grade steel from demolition waste with up to 99% purity, significantly reducing the need for virgin materials. This process has been particularly successful in markets like Germany and Japan, where automated sorting systems can process up to 200 tons of mixed construction waste per hour.
Electric arc furnace (EAF) technology has evolved to accommodate varying grades of reclaimed steel, allowing for more efficient reprocessing of construction waste into new structural materials. These furnaces now incorporate AI-driven quality control systems that optimize the melting process based on the input material’s composition, resulting in consistently high-quality output.
Notable developments include the implementation of blockchain-based material tracking systems, ensuring complete transparency in the steel recycling supply chain. Construction firms can now verify the origin and quality of recycled steel products, meeting increasingly stringent building codes and sustainability requirements.
Case studies from major European construction projects demonstrate that upcycled steel can achieve comparable structural properties to virgin materials while reducing carbon emissions by up to 70%. Several leading manufacturers have developed specialized treatment processes that enhance the durability of recycled steel, making it suitable for high-performance applications in modern building projects.
The economic viability of these innovations has improved significantly, with processing costs decreasing by approximately 30% over the past five years, making steel upcycling an increasingly attractive option for construction projects of all scales.
Timber’s Second Life in Construction
Engineered Wood Products from Recycled Timber
The transformation of construction waste wood into engineered wood products represents one of the most promising developments in circular construction practices. Leading this innovation is Urban Mining Northeast, which has pioneered a process for converting reclaimed timber into mass timber panels and structural elements that meet rigorous building standards.
Their flagship project in Brooklyn demonstrates how recovered wood from demolished warehouses can be processed, graded, and engineered into cross-laminated timber (CLT) panels that rival virgin wood products in both strength and durability. The company reports a 60% reduction in carbon footprint compared to traditional CLT manufacturing processes.
Another notable example is Kebony, a Norwegian company that has developed a revolutionary bio-based modification process for recycled softwood. Their technology enhances the properties of reclaimed timber through a patented treatment process, creating high-performance products suitable for both structural and decorative applications. Their products have been successfully used in numerous commercial projects across Europe, achieving a 90% waste reduction in the timber supply chain.
In Australia, Kennedy’s Timber has established a comprehensive recycling program that processes construction waste wood into engineered flooring and architectural elements. Their innovative grading system ensures that even heavily weathered timber can be repurposed into valuable building materials. The company’s process has diverted over 10,000 tons of timber waste from landfills annually.
These initiatives demonstrate the technical feasibility and commercial viability of incorporating recycled timber into engineered wood products. Key benefits include:
– Reduced pressure on virgin forest resources
– Lower embodied carbon in construction materials
– Creation of high-value products from waste materials
– Preservation of old-growth timber characteristics
– Economic advantages through waste reduction
The success of these programs has led to increased adoption by major construction firms and has influenced building codes to accommodate recycled engineered wood products. Industry experts predict this sector will grow by 25% annually over the next five years, driven by sustainability requirements and improving technology for wood waste processing.
Digital Solutions Driving Material Circularity
Material Passports and Digital Tracking
Material passports and digital tracking systems represent a significant advancement in the circular economy approach to construction materials. These digital tools enable comprehensive documentation of material compositions, properties, and locations throughout a building’s lifecycle, facilitating future reuse and recycling opportunities.
The implementation of Building Information Modeling (BIM) alongside digital construction management systems has made it possible to create detailed material inventories that track everything from structural steel to interior finishes. Leading construction firms are now embedding RFID tags and QR codes into building components, creating a digital thread that follows materials from manufacture through installation and eventual deconstruction.
For example, the Madaster Platform in the Netherlands has pioneered the implementation of material passports for entire buildings, documenting over €1 billion worth of construction materials. This system allows building owners to maintain real-time inventories of their material assets and plan for future material recovery.
The technology also enables precise tracking of embodied carbon and other environmental impacts throughout the material lifecycle. Construction companies can now make data-driven decisions about material sourcing, reuse potential, and end-of-life scenarios. This level of transparency and traceability is proving essential for achieving circular economy objectives and meeting increasingly stringent sustainability requirements in the construction sector.
By 2025, experts predict that digital material tracking will become standard practice in major construction projects, driven by both environmental regulations and economic benefits.
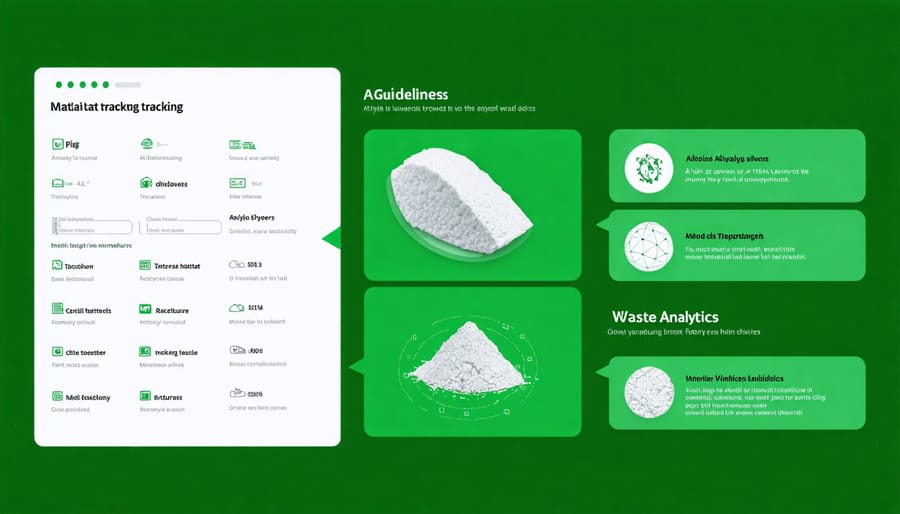
AI-Powered Waste Reduction
Artificial Intelligence is revolutionizing waste reduction in construction through sophisticated algorithms and machine learning systems that optimize material usage and recycling processes. These AI-powered solutions are transforming traditional waste management approaches into data-driven, efficient operations that significantly reduce material waste and environmental impact.
Leading construction firms are implementing AI systems that can predict material requirements with unprecedented accuracy, reducing over-ordering and waste generation. For example, AECOM’s implementation of predictive AI analytics has resulted in a 30% reduction in material waste across their European projects, while simultaneously improving project timelines and cost efficiency.
Computer vision technology, coupled with AI algorithms, enables automated waste sorting and classification on construction sites. These systems can identify different types of construction materials with up to 95% accuracy, streamlining the recycling process and ensuring maximum material recovery. The integration of these technologies with smart waste management systems provides real-time monitoring and optimization of waste streams.
AI-driven platforms are also being used to create digital material passports, tracking construction materials throughout their lifecycle and facilitating their future reuse or recycling. Companies like Buildera have developed AI systems that maintain detailed records of material properties, location, and condition, enabling efficient material recovery and repurposing in future projects.
The economic benefits are substantial, with AI-powered waste reduction systems typically delivering ROI within 12-18 months through reduced material costs, improved operational efficiency, and decreased disposal fees.
The transition to a circular economy in construction represents a fundamental shift in how we approach building projects, material usage, and waste management. As demonstrated through numerous successful implementations, circular principles not only reduce environmental impact but also create tangible economic benefits for construction companies and stakeholders.
Key success factors include early planning for circularity, strong collaboration across the supply chain, and investment in innovative technologies. The industry has shown that implementing circular strategies, from material recycling to modular design, can lead to cost savings of 15-25% while significantly reducing carbon emissions and waste.
Looking ahead, the construction sector is poised for further circular innovation. Emerging technologies like digital material passports, AI-powered waste sorting, and advanced recycling processes will continue to facilitate circular practices. Additionally, growing regulatory pressure and client demand for sustainable construction will accelerate adoption.
However, challenges remain. The industry must address issues such as standardization of circular practices, scaling of recycling infrastructure, and development of reliable measurement metrics. Success will require continued commitment from industry leaders, policy support, and sustained investment in research and development.
As we move forward, the circular economy will become increasingly central to construction practices, driven by both environmental necessity and economic opportunity. Companies that embrace these principles early will gain competitive advantages while contributing to a more sustainable built environment.