In an era where resource scarcity meets environmental urgency, the circular economy business model emerges as a transformative force reshaping the construction industry’s future. This regenerative approach challenges traditional linear “take-make-dispose” practices, offering construction professionals a framework to create sustainable value while minimizing waste and maximizing resource efficiency.
Leading construction firms worldwide are revolutionizing their operations by implementing closed-loop systems, where materials, components, and resources maintain their highest utility throughout the project lifecycle. From adaptive reuse of existing structures to innovative material recovery processes, the circular economy model presents compelling opportunities for both environmental stewardship and economic growth.
Research indicates that circular economy principles in construction can reduce raw material consumption by up to 40% while generating significant cost savings through improved resource management and waste reduction. For industry leaders and project managers, adopting these principles isn’t merely an environmental choice—it’s a strategic imperative that drives innovation, enhances competitive advantage, and ensures long-term business sustainability.
This comprehensive guide explores how construction professionals can effectively integrate circular economy principles into their projects, supported by real-world case studies and practical implementation strategies that deliver measurable results in today’s demanding market conditions.
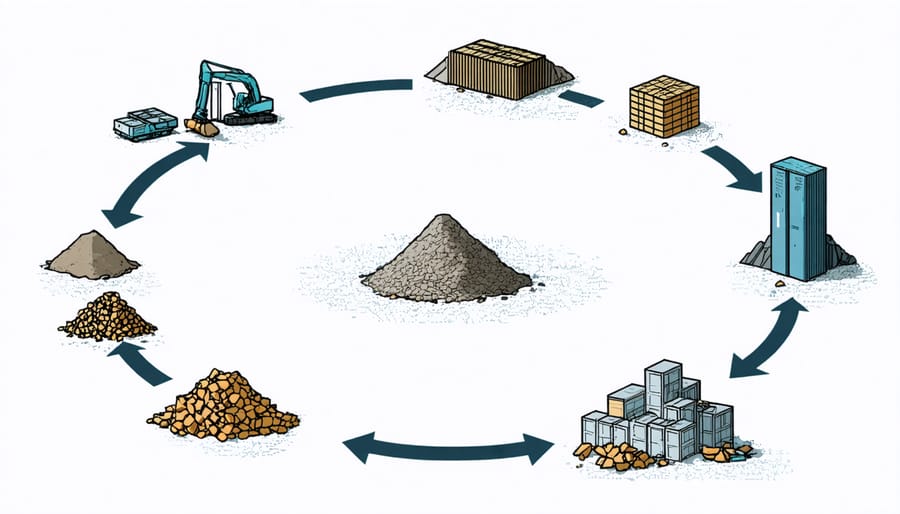
The Core Principles of Circular Economy in Construction
Design for Disassembly and Reuse
Design for Disassembly and Reuse (DfDR) represents a fundamental shift in construction methodology, emphasizing modular components and recyclable materials that can be easily separated and repurposed at the end of a building’s life cycle. This approach incorporates reversible connections, standardized components, and mechanical fastening systems instead of adhesive-based joining methods.
Key strategies include the use of prefabricated elements that can be dismantled without damage, allowing for future reuse in different projects. For example, steel frame structures with bolted connections enable efficient deconstruction, while modular interior wall systems facilitate space reconfiguration without generating waste.
Materials selection plays a crucial role, with emphasis on recyclable options such as aluminum, steel, and certain engineered wood products. Leading architects are now specifying materials based on their potential for future recovery and reprocessing. Documentation of material composition and assembly methods through Building Information Modeling (BIM) ensures that future teams can effectively disassemble structures.
Recent projects demonstrate that DfDR can reduce end-of-life disposal costs by up to 50% while creating a valuable material bank for future construction. This approach not only supports environmental sustainability but also creates new revenue streams through the resale of quality building components.
Resource Optimization and Waste Reduction
Effective resource optimization and waste reduction strategies form the cornerstone of circular construction practices. Construction firms can significantly reduce material waste through precise quantity surveying, digital modeling, and prefabrication techniques. BIM technology enables accurate material estimation, reducing over-ordering and excess inventory by up to 30%.
Key optimization methods include implementing closed-loop material management systems, where construction waste is sorted on-site for immediate reuse or recycling. Advanced crushing and screening equipment can process concrete and masonry waste into high-quality aggregates, while wood waste can be repurposed for temporary structures or processed into biomass fuel.
Material passport systems track building components throughout their lifecycle, facilitating future recovery and reuse. This approach, combined with modular construction techniques, can achieve waste reduction rates of up to 90% compared to traditional methods. Leading construction firms have demonstrated that investing in resource optimization technology typically yields return on investment within 18-24 months through reduced material costs and waste disposal fees.
Implementing Circular Business Models in Urban Development
Product-as-a-Service Solutions
Product-as-a-Service (PaaS) solutions are revolutionizing how building components are procured, used, and maintained in construction projects. This innovative approach transforms traditional ownership models into service-based arrangements, where manufacturers retain ownership of their products while providing ongoing maintenance and performance guarantees.
In building systems, PaaS models are particularly effective for mechanical, electrical, and lighting installations. For instance, Philips’ “Light as a Service” program allows buildings to pay for lighting performance rather than purchasing fixtures outright. This arrangement ensures optimal energy efficiency while transferring maintenance responsibilities to the manufacturer.
Similar models are emerging in facade systems and modular construction approaches, where suppliers lease entire building components with integrated maintenance contracts. These arrangements incentivize manufacturers to design for longevity and recyclability, as they maintain responsibility for the product’s entire lifecycle.
The benefits include reduced upfront costs, guaranteed performance standards, and simplified maintenance procedures. Building owners can focus on core operations while providers ensure optimal component performance. This model also promotes resource efficiency, as manufacturers are motivated to implement preventive maintenance and extend product lifespans.
Financial institutions are increasingly supporting PaaS arrangements, recognizing their potential to reduce risk and enhance building performance. As the construction industry embraces circular principles, these service-based models are becoming essential tools for sustainable development.
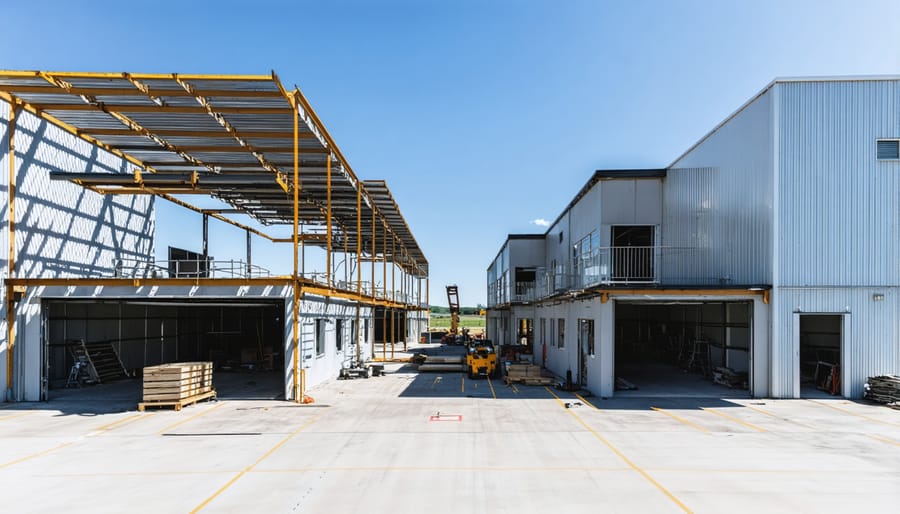
Material Banks and Digital Passports
Material banks and digital passports represent groundbreaking innovations in the construction industry’s transition toward circular economy practices. These digital tools enable comprehensive tracking of building materials throughout their lifecycle, from initial installation to eventual reuse or recycling.
Digital material passports serve as detailed repositories of information about building components, including their composition, location, condition, and maintenance history. This data-driven approach allows construction professionals to make informed decisions about material recovery and reuse when buildings reach their end of life. Leading construction firms are implementing these systems to maintain detailed records of high-value materials such as structural steel, glass panels, and architectural elements.
The concept of material banks takes this further by treating buildings as temporary storage facilities for valuable resources. By documenting materials in a structured database, future projects can identify and source reclaimed materials more efficiently. Several European cities have pioneered material bank platforms, successfully facilitating the exchange of recovered building materials between demolition and construction projects.
Integration with Building Information Modeling (BIM) systems enhances the effectiveness of these tools. Real-time tracking and updates ensure accurate material documentation throughout a building’s lifecycle. This systematic approach not only supports circular economy principles but also provides significant cost advantages through improved resource management and reduced waste disposal expenses.
For maximum effectiveness, material banks and digital passports require industry-wide standardization and collaboration. Construction companies adopting these technologies early are positioning themselves as leaders in sustainable construction practices while creating new value streams from previously discarded materials.
Collaborative Consumption Models
In urban development, collaborative consumption models are revolutionizing how spaces and resources are utilized, maximizing efficiency while reducing environmental impact. These models facilitate the sharing of facilities, equipment, and infrastructure among multiple stakeholders, creating a more sustainable urban ecosystem.
Shared spaces in commercial buildings have become increasingly prevalent, with flexible office arrangements and co-working facilities leading the way. These spaces optimize resource usage by accommodating multiple businesses within the same footprint, reducing the need for individual buildings and their associated environmental costs.
Community-focused developments are incorporating shared amenities such as meeting rooms, recreational facilities, and garden spaces that serve multiple residential or commercial units. This approach not only reduces construction material requirements but also creates opportunities for social interaction and community building.
Resource sharing extends beyond physical spaces to include construction equipment, tools, and even energy systems. Smart building management systems enable the efficient allocation of resources based on real-time demand, while district heating and cooling systems serve multiple buildings through shared infrastructure.
Notable examples include Stockholm’s Hammarby Sjöstad district, where shared waste management systems and energy infrastructure serve multiple buildings, reducing individual building requirements while improving overall efficiency. Similarly, Amsterdam’s Circle City initiative demonstrates how shared spaces can facilitate material reuse and recycling at the district level.
These collaborative models require careful planning and coordination among stakeholders but deliver significant benefits in terms of resource efficiency, cost reduction, and environmental impact minimization.
Case Studies: Successful Circular Economy Projects
The Amsterdam Circular City Initiative
Amsterdam has emerged as a pioneering force in circular construction, implementing one of the most comprehensive urban circular economy programs globally. The city’s initiative, launched in 2020, aims to reduce primary raw material use by 50% by 2030 and achieve complete circularity by 2050.
The program’s cornerstone is its material passport system, which tracks and documents all construction materials used in new buildings. This digital tracking enables future recovery and reuse of materials, effectively treating buildings as material banks. The city requires all construction projects above 500 square meters to submit a material passport and demonstrate their circular design strategies.
A notable success story is the transformation of the former Bijlmerbajes prison complex, where 98% of demolition materials were successfully recovered and repurposed. The project showcases how careful deconstruction and material sorting can create significant economic value while reducing environmental impact.
The initiative also mandates that 20% of all construction materials in new projects must be recycled or bio-based. To facilitate this, Amsterdam has established a digital marketplace where contractors can source and trade recovered building materials. The platform has facilitated over €5 million in material exchanges since its launch.
The program’s success relies heavily on collaboration between public and private sectors, with the municipality providing incentives through preferential building permits and reduced fees for projects demonstrating strong circular principles.
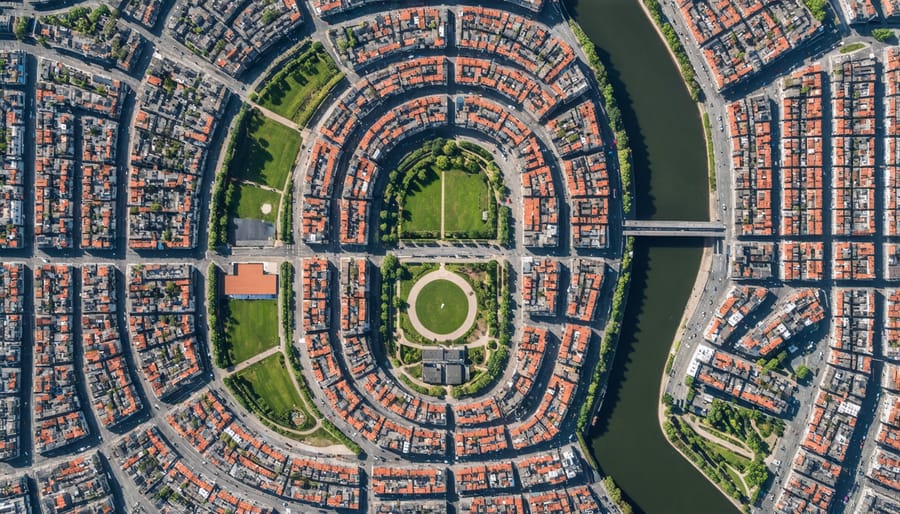
Circle House Project in Denmark
The Circle House project in Lisbjerg, Aarhus, Denmark stands as a groundbreaking demonstration of circular construction principles at scale. Completed in 2020, this 60-unit social housing development showcases how 90% of its building materials can be disassembled and reused without losing significant value, setting new standards for sustainable construction.
The project’s innovative design features mechanical joints instead of adhesive-based connections, allowing for future disassembly. Concrete elements, steel components, and wooden structures are assembled using standardized, reversible connections that facilitate easy separation and reuse. This approach extends the lifecycle of building materials while significantly reducing construction waste and carbon emissions.
Key technical innovations include prefabricated concrete elements with exposed connection points, modular facade systems, and detailed material passports that track the composition and future reuse potential of all components. The project demonstrates that circular principles can be implemented without compromising architectural quality or increasing construction costs significantly.
The Circle House has become a learning laboratory for the construction industry, proving that circular building practices are commercially viable at scale. The project’s success has influenced Danish building regulations and inspired similar initiatives across Europe, marking a significant shift toward circular construction methods in mainstream building practices.
Economic Benefits and Future Opportunities
The economic benefits of circular construction are becoming increasingly evident as more organizations embrace this innovative approach. Recent industry analysis indicates that implementing circular principles can reduce construction costs by 15-25% while simultaneously increasing project value through material recovery and reuse.
Companies adopting circular practices report significant reductions in raw material costs, with savings ranging from 20-40% through systematic material recovery and repurposing. Waste management expenses typically decrease by 30-50%, contributing directly to improved project margins. Additionally, buildings designed for disassembly and material recovery command premium prices in the market, with studies showing value increases of up to 15% compared to traditional constructions.
Future opportunities in circular construction are particularly promising. The global market for recovered building materials is projected to reach $340 billion by 2025, growing at an annual rate of 6.8%. Emerging technologies such as digital material passports and blockchain-based tracking systems are creating new revenue streams through improved material verification and trading.
Investment in circular construction technologies is surging, with venture capital funding increasing by 125% since 2020. Key growth areas include advanced recycling technologies, modular construction systems, and digital platforms for material exchange. Early adopters are gaining competitive advantages through reduced regulatory compliance costs and enhanced brand value.
Looking ahead, the integration of artificial intelligence and IoT sensors in building components will further optimize material recovery and reuse. Market analysts predict that companies implementing comprehensive circular strategies could achieve cost reductions of up to 35% by 2030, while significantly improving their environmental performance and market position. These developments suggest that circular construction is not just an environmental imperative but a compelling business opportunity with substantial financial returns.
The transition to a circular economy business model in construction represents a fundamental shift in how we approach urban development and resource management. Industry professionals must recognize that implementing these principles is not just an environmental imperative but a competitive advantage in an increasingly resource-conscious market.
To successfully adopt circular economy practices, construction professionals should focus on several key action steps. First, conduct thorough material audits of existing projects and establish baseline measurements for waste reduction targets. Second, invest in digital technologies and Building Information Modeling (BIM) to optimize material use and facilitate future deconstruction. Third, develop partnerships with suppliers and waste management companies that share circular economy objectives.
Project managers and decision-makers should prioritize early stakeholder engagement and ensure circular principles are integrated into the initial design phase. This includes specifying recycled materials, designing for disassembly, and incorporating modularity into building systems. Additionally, establish clear metrics for measuring circular performance and implement monitoring systems to track progress.
For immediate implementation, focus on quick wins such as improving waste segregation on-site, implementing take-back schemes with suppliers, and training staff in circular economy principles. Long-term success requires systematic change, including updating procurement policies, revising contract frameworks, and developing new business models that capitalize on material recovery and reuse.
Remember that the transition to a circular economy is an iterative process. Start with pilot projects, measure outcomes, and scale successful initiatives across your operations. The future of construction lies in circular thinking, and early adopters will be best positioned to thrive in this evolving landscape.