Three-dimensional concrete printing stands at the forefront of a technological revolution that is transforming construction in the next decade. This groundbreaking technology merges advanced robotics, material science, and digital design to fundamentally reshape how we construct buildings and infrastructure. By depositing concrete layers with precision previously impossible through traditional methods, 3D printing enables the creation of complex architectural forms while potentially reducing construction time by up to 70% and cutting labor costs by 50%.
For construction industry leaders and innovators, concrete 3D printing represents more than just technological advancement—it offers a viable solution to pressing challenges including labor shortages, project delays, and sustainability demands. From printing entire residential structures in 24 hours to creating customized architectural elements with zero waste, this technology is revolutionizing traditional construction paradigms.
As major construction firms worldwide integrate 3D concrete printing into their operations, understanding its capabilities, limitations, and implementation requirements has become crucial for maintaining competitive advantage in an evolving industry landscape. This comprehensive analysis examines the current state of concrete 3D printing technology, its practical applications, and its implications for the future of construction.
The Technology Behind Construction-Scale 3D Concrete Printing
Printer Systems and Components
Construction 3D concrete printing systems typically fall into three main categories: gantry-based systems, robotic arm systems, and crane-based systems. 3D house printing robots have become increasingly sophisticated, incorporating advanced control systems and precise material delivery mechanisms.
The core components of these systems include the mechanical framework, extrusion system, pumping mechanism, and control interface. The mechanical framework, whether gantry or robotic arm, provides the necessary mobility and stability for precise concrete placement. The extrusion system, comprising nozzles and material flow controllers, determines the print quality and layer consistency.
Material pumping systems must maintain consistent pressure and flow rates to ensure uniform concrete delivery. Modern systems utilize specialized pumps capable of handling various concrete mixtures while preventing premature setting. The control interface integrates sophisticated software that translates digital designs into printer movements, managing parameters such as extrusion rate, travel speed, and layer height.
Critical auxiliary components include material storage systems, mixing units, and real-time monitoring sensors. These sensors track environmental conditions, material properties, and printing parameters to maintain quality control. Advanced systems also incorporate automated cleaning mechanisms and quick-change nozzle systems to minimize maintenance downtime and enhance operational efficiency.
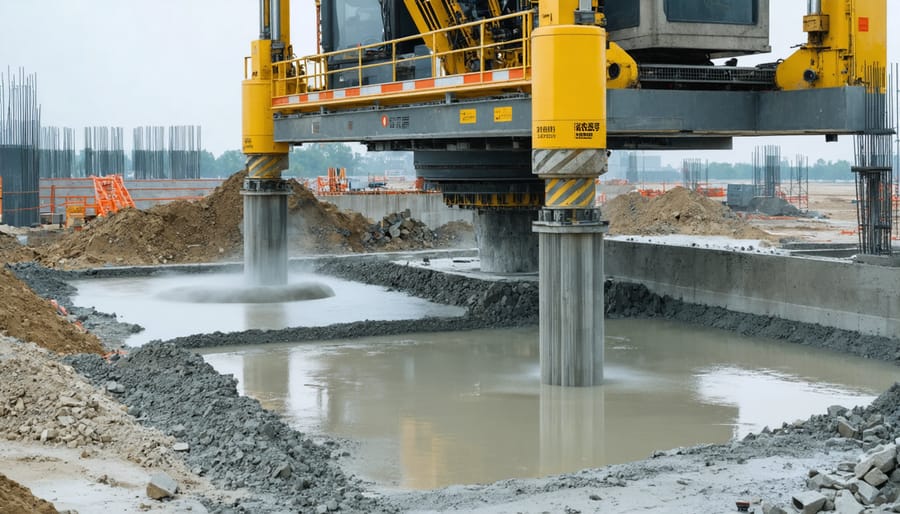
Concrete Mix Design and Materials
The success of 3D concrete printing heavily relies on specialized concrete mixtures that differ significantly from conventional concrete formulations. These mixes must possess specific rheological properties, including proper flowability for extrusion while maintaining shape stability after deposition. The optimal mix typically consists of cement, fine aggregates, supplementary cementitious materials, and chemical admixtures.
Key material requirements include high early strength development, controlled setting time, and enhanced thixotropic behavior. Portland cement serves as the primary binder, while silica fume and fly ash are commonly added to improve workability and reduce segregation. The aggregate size is limited to a maximum of 4mm to prevent nozzle blockage and ensure smooth extrusion.
Chemical admixtures play a crucial role in achieving the desired performance characteristics. Superplasticizers enhance flowability, while viscosity modifying agents help maintain mix stability. Setting accelerators are often incorporated to ensure rapid strength development and layer adhesion.
The water-to-cement ratio typically ranges from 0.35 to 0.45, significantly lower than conventional concrete. This helps achieve the necessary extrudability while maintaining shape retention. Mix designs must also account for open time requirements, as the material needs to remain workable throughout the printing process while developing sufficient strength to support subsequent layers.
Quality control and consistent material properties are essential, as variations can significantly impact print quality and structural integrity. Regular testing of fresh and hardened properties ensures optimal performance throughout the printing process.
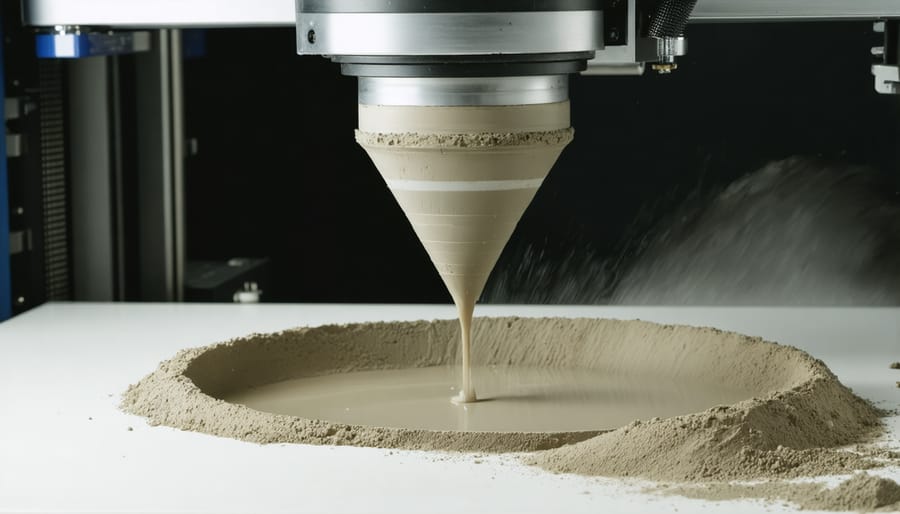
Commercial Applications and Success Stories
Residential Construction Projects
Several groundbreaking residential projects worldwide showcase the potential of 3D concrete printing in housing construction. In Mexico, the first community of 3D-printed homes was completed in 2023, featuring 50 single-story houses built in collaboration with New Story and ICON. Each 500-square-foot home was printed in under 24 hours, demonstrating significant time savings compared to traditional construction methods.
In the Netherlands, Project Milestone in Eindhoven represents Europe’s first commercially rental 3D-printed houses. The development features five uniquely designed homes that highlight the technology’s capability to create complex geometries and curved walls without additional cost implications. The project’s success has sparked similar initiatives across Europe.
Dubai’s ambitious 3D printing strategy has resulted in multiple residential developments, including a 2,690-square-foot two-story villa printed in just two weeks. The structure showcases advanced printing techniques that integrate building services during the printing process, reducing post-construction modifications.
In the United States, SQ4D completed a 1,900-square-foot home in Long Island, New York, notable for being the first 3D-printed house to receive a certificate of occupancy. The project demonstrated a 70% reduction in construction costs compared to traditional building methods, while maintaining compliance with local building codes.
COBOD’s BOD2 printer has been utilized in multiple residential projects across Denmark, Germany, and Belgium, proving the technology’s adaptability to different climate conditions and building regulations. These projects consistently show 30-60% reduction in construction time and 20-40% cost savings, particularly in labor expenses.
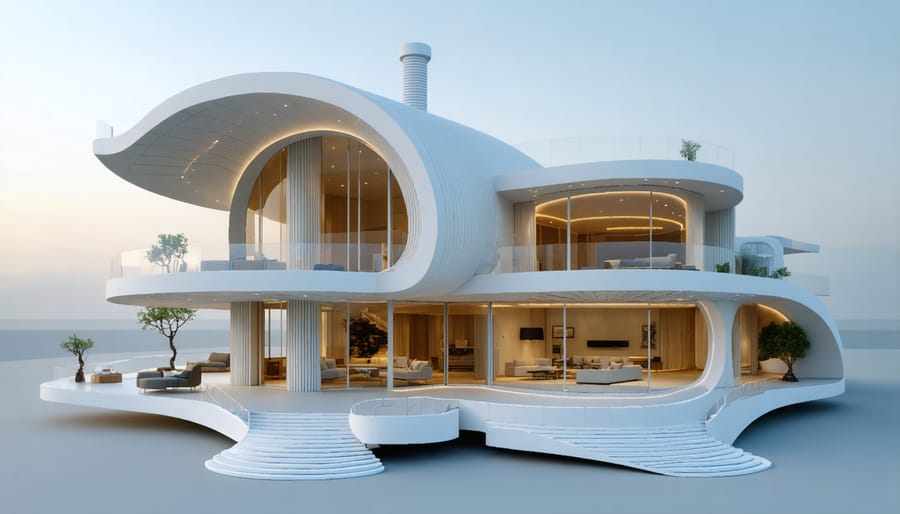
Infrastructure Applications
3D concrete printing is revolutionizing infrastructure construction through innovative applications in bridge building, safety barriers, and urban furniture. The technology’s precision and flexibility make it particularly suitable for creating complex geometric structures while reducing labor costs and construction time.
In bridge construction, 3D concrete printing has demonstrated remarkable capabilities. The world’s first 3D-printed pedestrian bridge in Madrid, Spain, showcases how this technology can create intricate designs while maintaining structural integrity. Similarly, the Netherlands’ MX3D bridge project illustrates the potential for combining reinforced concrete printing with smart sensors for real-time structural monitoring.
Safety barriers and road dividers represent another significant application area. 3D-printed barriers can be customized to specific site requirements and produced on-demand, reducing storage needs and transportation costs. These structures maintain required safety standards while offering design flexibility that traditional casting methods cannot achieve.
Urban furniture applications have expanded significantly, with cities worldwide adopting 3D-printed concrete benches, planters, and bus stops. These elements can be designed to complement specific architectural styles or cultural contexts, while their rapid production enables quick urban renewal projects. The technology allows for integrated features such as drainage systems and lighting fixtures directly within the printed structure.
Notable benefits include:
– Reduced material waste through precise material deposition
– Lower carbon footprint compared to traditional construction methods
– Ability to create complex geometries without additional cost
– Rapid deployment in urban regeneration projects
– Customization capabilities for site-specific requirements
Implementation challenges primarily revolve around scaling up operations and ensuring consistent quality across larger infrastructure projects. However, ongoing developments in printing technology and material science continue to address these limitations, making infrastructure applications increasingly viable.
Cost and Time Benefits
The implementation of 3D concrete printing technology presents significant cost and time advantages compared to traditional construction methods. Recent industry studies indicate potential cost savings of 20-40% in overall project expenses, primarily through reduced labor costs and material optimization. This aligns with the broader trend of automation in construction, where digital solutions drive efficiency improvements.
Labor costs typically represent 35-45% of traditional construction project budgets. 3D concrete printing can reduce these expenses by up to 80% through automated processes requiring minimal human intervention. Projects in Dubai and Shanghai have demonstrated completion times reduced by 50-70% compared to conventional methods, with some structures being completed in days rather than months.
Material efficiency represents another significant cost benefit. The precision of 3D printing reduces material waste by up to 30%, with computer-controlled deposition ensuring optimal material usage. Advanced mix designs specifically formulated for 3D printing contribute to both cost efficiency and structural integrity, while reducing environmental impact through lower cement consumption.
Case studies from leading construction firms reveal that the initial investment in 3D concrete printing technology can be recovered within 2-3 years, depending on project volume and complexity. A major European contractor reported a 25% reduction in overall project costs across multiple residential developments, with acceleration in project delivery timelines of up to 60%.
The technology also minimizes costly construction errors and rework through precise digital control. This precision, combined with reduced material waste and faster construction speeds, results in improved project economics and better return on investment. Furthermore, the ability to work continuously with minimal weather dependencies enhances project predictability and reduces schedule-related costs.
Regulatory Framework and Standards
The regulatory landscape for 3D concrete printing in construction continues to evolve as the technology gains wider adoption. Currently, most countries are working to integrate these innovative construction methods into existing building codes and standards. The American Concrete Institute (ACI) Committee 564 is developing comprehensive guidelines specifically for 3D printed concrete construction, addressing crucial aspects such as material properties, structural design requirements, and quality control procedures.
In Europe, the European Committee for Standardization (CEN) has established working groups focused on creating standardized testing methods and performance requirements for 3D printed concrete structures. These efforts aim to ensure consistent quality and safety across projects while promoting innovation within established regulatory frameworks.
Dubai Municipality has taken a leading role by implementing the first specialized regulations for 3D printed buildings, mandating that 25% of new buildings must use 3D printing technology by 2025. These regulations cover structural integrity, durability requirements, and construction methodology validation.
Key regulatory considerations include:
– Material composition and performance requirements
– Structural design validation methods
– Quality control and testing procedures
– Construction process documentation
– Safety protocols during printing operations
– Inspection and certification requirements
Professional certification programs are emerging to ensure operators and engineers are qualified to work with 3D concrete printing technology. These programs focus on both technical competency and safety awareness, helping to establish industry-wide standards for workforce qualification.
While some regulatory gaps remain, organizations like the International Code Council (ICC) are working closely with industry stakeholders to develop comprehensive guidelines that address the unique characteristics of 3D printed concrete structures. This collaborative approach ensures that regulations keep pace with technological advancements while maintaining construction safety and quality standards.
Practitioners should stay informed about local building codes and regulations, as requirements can vary significantly between jurisdictions. Regular consultation with local authorities and certification bodies is essential for successful project implementation.
Future Outlook and Industry Impact
The future of construction 3D concrete printing stands at a pivotal juncture, with industry experts projecting significant growth and transformation over the next decade. Market analysts forecast the global 3D concrete printing market to reach $40.6 billion by 2027, driven by increasing demand for sustainable construction methods and rapid urbanization.
As digital construction technologies continue to evolve, we can expect several breakthrough developments. Advanced AI integration will enable more precise printing algorithms, while new material innovations will expand the range of printable concrete compositions. Industry leaders anticipate the emergence of hybrid systems combining traditional construction methods with 3D printing, offering greater flexibility in project execution.
The technology’s adoption rate is expected to accelerate, particularly in residential construction and infrastructure projects. Major construction firms are already investing heavily in research and development, focusing on scaling up printing capabilities for larger structures and improving the technology’s cost-effectiveness. Experts predict that by 2025, up to 15% of new construction projects in developed markets could incorporate some form of 3D concrete printing.
Regulatory frameworks are also evolving to accommodate this technology. Several countries are developing specific building codes and standards for 3D-printed structures, which will facilitate wider industry adoption. This standardization is crucial for insurance companies and lending institutions to support 3D-printed construction projects.
The environmental impact of this technology will likely drive its adoption, as organizations seek to meet increasingly stringent sustainability targets. Studies indicate that 3D concrete printing could reduce construction waste by up to 60% and lower CO2 emissions by 30% compared to traditional methods. This alignment with global sustainability goals positions the technology as a key player in the future of construction.
Looking ahead, the integration of robotics, IoT sensors, and real-time monitoring systems will further enhance the precision and reliability of 3D concrete printing, making it an increasingly attractive option for complex architectural designs and challenging construction environments.