The construction industry stands at the cusp of a technological revolution, with robotics emerging as a transformative force that promises to reshape how we build. From autonomous excavators navigating job sites to robotic arms precisely laying bricks at superhuman speeds, construction robotics has evolved from experimental prototypes to commercially viable solutions. Industry analysts project the construction robotics market to reach $28.5 billion by 2030, driven by escalating labor shortages, increasing safety requirements, and the pressing need for improved productivity.
As construction projects grow more complex and demanding, robotics offers a compelling solution to long-standing industry challenges. Advanced sensors, artificial intelligence, and machine learning now enable robots to perform tasks that once seemed impossible to automate. These technologies are not just augmenting human capabilities; they’re creating entirely new possibilities for construction methodologies, project planning, and execution.
For construction leaders and professionals, understanding and adapting to this technological shift isn’t just advantageous—it’s imperative for survival in an increasingly competitive market. The integration of robotics promises to address critical industry pain points: reducing workplace accidents, increasing precision, accelerating project timelines, and delivering consistent quality while controlling costs.
AI-Powered Construction Robots: The Game Changers
Autonomous Equipment and Heavy Machinery
The integration of autonomous equipment and heavy machinery represents a significant leap forward in construction automation. As AI in construction advances, self-operating vehicles and smart equipment are becoming increasingly sophisticated and reliable. Leading manufacturers have developed autonomous excavators, bulldozers, and dump trucks that can perform repetitive tasks with remarkable precision while reducing human error and improving safety conditions on construction sites.
These autonomous systems utilize a combination of sensors, GPS technology, and advanced control algorithms to navigate construction sites and perform complex operations. For instance, autonomous excavators can now precisely dig foundations and trenches according to digital plans, while robotic dozers can grade surfaces with millimeter-level accuracy. Real-world implementations have shown productivity improvements of up to 30% compared to traditional manually operated equipment.
Safety features include obstacle detection, geofencing, and emergency shutdown protocols, ensuring these machines can operate safely alongside human workers. The technology also enables 24/7 operations in suitable conditions, significantly reducing project timelines. While the initial investment in autonomous equipment remains substantial, construction companies report meaningful returns through reduced labor costs, increased efficiency, and minimized downtime.
Industry leaders predict that by 2025, autonomous equipment will handle up to 40% of standard earthmoving operations on major construction projects, marking a transformative shift in how construction sites operate.
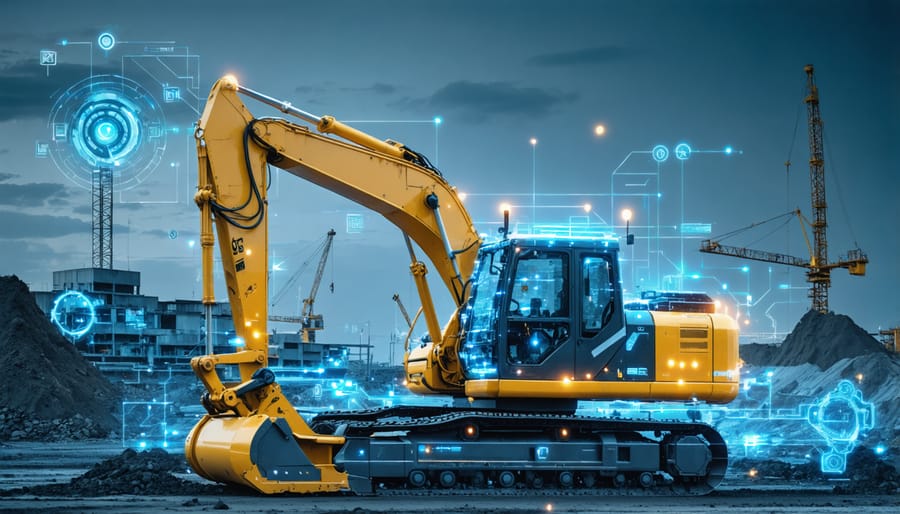
3D Printing and Additive Manufacturing Robots
The integration of 3D printing construction technologies represents a significant advancement in automated building processes. These robotic systems utilize specialized extruders and gantry-mounted mechanisms to deposit construction materials layer by layer, enabling the creation of complex architectural structures with unprecedented precision and speed.
Current implementations demonstrate capabilities ranging from printing individual building components to entire structural elements. Advanced systems can now handle multiple materials simultaneously, incorporating reinforcement structures and utilizing specialized concrete mixtures optimized for additive manufacturing processes.
Notable achievements include the successful printing of residential structures in under 24 hours and the development of mobile printing robots capable of operating autonomously on construction sites. These systems typically achieve material savings of 30-60% compared to traditional construction methods, while significantly reducing labor requirements and construction waste.
Recent innovations focus on developing multi-robot printing systems that work collaboratively, enabling the construction of larger structures and more complex geometries. Integration with BIM (Building Information Modeling) systems allows for seamless translation of digital designs into physical structures, while real-time quality control systems monitor material properties and structural integrity during the printing process.
The technology continues to evolve, with emerging capabilities in smart material integration and adaptive printing parameters that respond to environmental conditions and structural requirements in real-time.
Real-World Applications Transforming Sites Today
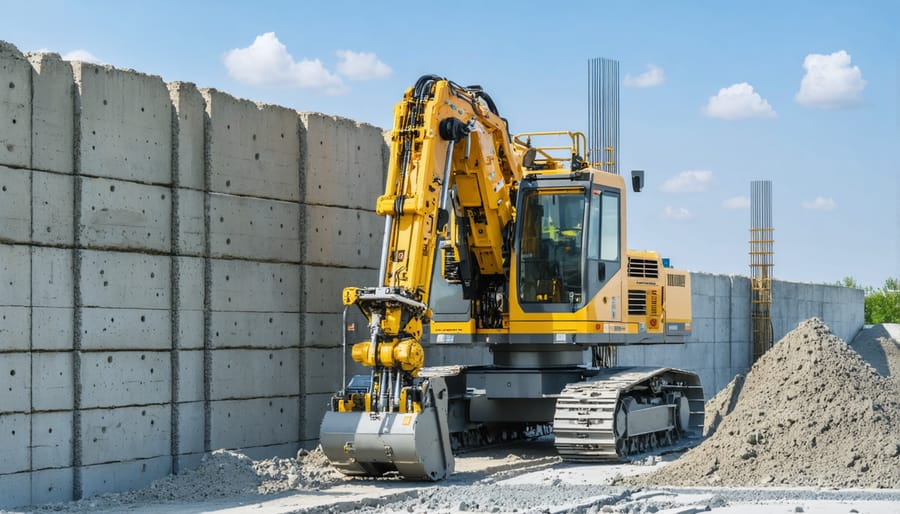
Precision Assembly and Prefabrication
Robotic systems are revolutionizing precision assembly and prefabrication in construction, delivering unprecedented levels of accuracy and efficiency. Advanced robotic arms equipped with computer vision and AI-powered controls can now assemble complex building components with tolerances as tight as 0.1 millimeters, far exceeding traditional manual capabilities.
In modern prefabrication facilities, robots are working alongside humans to manufacture standardized building elements, from wall panels to complete room modules. These systems utilize real-time quality control measures, ensuring each component meets exact specifications before leaving the factory floor. For example, the recent implementation of robotic assembly lines at several major prefabrication plants has reduced production time by up to 70% while maintaining consistent quality standards.
Automated systems are particularly effective in tasks requiring repetitive precision, such as welding structural components or installing facade elements. Multi-axis robotic arms can work continuously in controlled environments, assembling complex structures with perfect alignment and spacing. This precision translates directly to improved on-site installation, reducing fitting issues and minimizing rework.
The integration of Building Information Modeling (BIM) with robotic assembly systems has enabled seamless coordination between design and fabrication. Robots can now interpret digital models directly, ensuring exact replication of architectural specifications. This digital-to-physical workflow has significantly reduced errors and material waste, while accelerating production schedules.
Several leading construction firms have reported up to 30% cost savings in large-scale projects through robotics-assisted prefabrication, alongside marked improvements in worker safety and project timelines. As these technologies continue to evolve, they’re setting new standards for construction quality and efficiency, making precision assembly more accessible and economically viable for a broader range of projects.
Safety and Inspection Innovations
The integration of robotics in construction safety is transforming hazardous task management and quality control processes across job sites. Advanced robotic systems are now capable of performing high-risk activities such as structural inspections at extreme heights, confined space evaluations, and handling of dangerous materials, significantly reducing worker exposure to potentially harmful situations.
Autonomous drones equipped with LiDAR sensors and high-resolution cameras conduct comprehensive site inspections, creating detailed 3D maps and identifying potential safety hazards before they become critical issues. These aerial robots can access hard-to-reach areas and perform regular structural health monitoring without putting human inspectors at risk.
Ground-based robots equipped with advanced sensing technologies are revolutionizing quality control processes. These systems utilize machine learning algorithms to detect construction defects, measure dimensional accuracy, and ensure compliance with building codes in real-time. The integration of thermal imaging and concrete penetrating radar enables robots to identify hidden structural issues that might be missed during traditional inspections.
Wearable robotic systems, such as exoskeletons, are enhancing worker safety by reducing physical strain during repetitive tasks and heavy lifting operations. These devices provide real-time ergonomic feedback and collect data on worker movements, helping prevent musculoskeletal injuries and improving overall site safety metrics.
The implementation of these robotic solutions has demonstrated significant improvements in inspection accuracy and consistency while reducing workplace accidents by up to 30% on pilot projects. As these technologies continue to evolve, construction companies are experiencing enhanced quality control processes, improved documentation, and more efficient regulatory compliance procedures.
Economic Impact and ROI Considerations
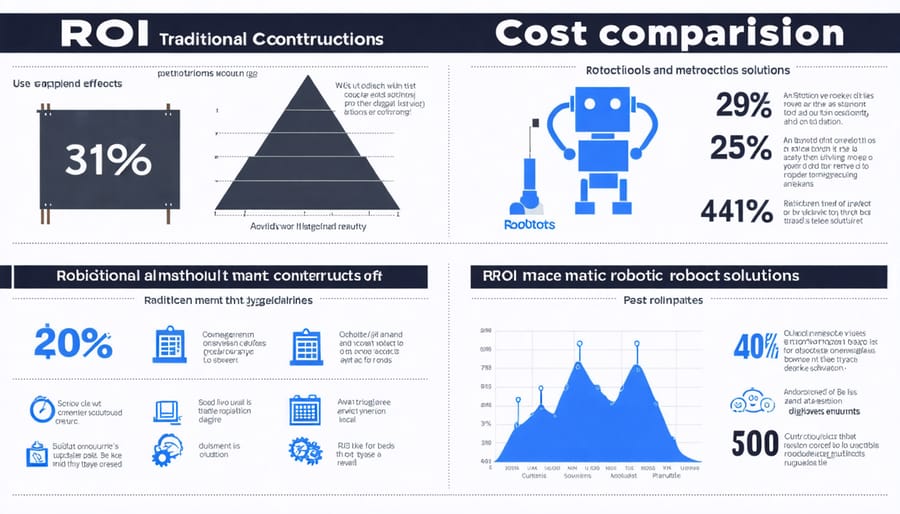
Investment and Operating Costs
The adoption of construction robotics requires careful financial planning and consideration of both initial investments and long-term operational costs. Current market analysis shows that industrial construction robots typically range from $50,000 to $400,000 per unit, depending on complexity and functionality. However, when implementing construction ROI strategies, companies often find that robotic systems can achieve positive returns within 2-3 years through increased productivity and reduced labor costs.
Operating costs include regular maintenance, software updates, and specialized training for operators, typically averaging 15-20% of the initial investment annually. Energy consumption varies significantly based on the type of robot, with autonomous vehicles requiring regular charging infrastructure and stationary robots consuming an average of 3-5 kW per hour of operation.
Insurance costs for robotic equipment generally run 1-2% of the asset value annually, while depreciation schedules typically span 5-7 years. Companies should also factor in integration costs, including site preparation, safety systems, and potential modifications to existing workflows, which can add 30-40% to the initial investment.
To optimize investment returns, construction firms increasingly opt for flexible financing options, including leasing arrangements and robotics-as-a-service models, which can reduce upfront capital requirements while maintaining access to cutting-edge technology.
Productivity and Efficiency Gains
The integration of robotics in construction has demonstrated significant measurable improvements in project efficiency and productivity. Recent industry studies show that automated systems can reduce construction time by 20-40% while improving accuracy by up to 95% compared to traditional methods.
Construction robots excel in repetitive tasks, with automated bricklaying systems capable of placing 200-300 bricks per hour, compared to the human average of 60-75 bricks. Similar efficiency gains are seen in tasks like concrete finishing, where robotic systems can process up to 2,000 square feet per hour while maintaining consistent quality standards.
Material waste reduction is another key benefit, with robotic systems achieving up to 30% reduction in material waste through precise cutting and placement. This efficiency translates directly to cost savings, with some projects reporting overall cost reductions of 15-20% when implementing robotic solutions.
Safety improvements contribute to productivity gains by reducing workplace incidents and associated downtime. Projects utilizing robotic systems report up to 50% fewer safety incidents in high-risk tasks like heavy lifting and work at height.
Time studies conducted on major construction projects reveal that automated systems can operate continuously for longer periods, effectively extending productive working hours by 30-40% compared to human-only crews. This increased operational capacity, combined with higher precision and reduced rework requirements, results in significantly accelerated project timelines and improved resource utilization.
What’s Next: Emerging Trends and Predictions
Based on extensive research and expert consultations, several transformative trends are poised to reshape construction robotics in the coming years. Artificial Intelligence integration stands out as a primary driver, with robots becoming increasingly autonomous in decision-making and problem-solving on construction sites. Industry experts predict that by 2025, AI-powered robots will be capable of real-time adaptation to changing site conditions and coordinating with human workers more effectively.
The emergence of swarm robotics technology is expected to revolutionize large-scale construction projects. These systems, comprising multiple smaller robots working in coordination, will enable faster project completion and enhanced precision in complex tasks. Leading construction technology firms are already developing prototype swarms for tasks like brick laying and structural assembly.
3D printing robotics is projected to evolve significantly, with next-generation systems capable of printing entire buildings using multiple materials simultaneously. This advancement will likely reduce construction time by up to 70% while maintaining superior structural integrity and allowing for more complex architectural designs.
Wearable robotics and exoskeletons are expected to become standard equipment on construction sites within the next five years. These devices will enhance worker capabilities while reducing physical strain and improving safety. Industry analysts predict a 300% increase in exoskeleton adoption by 2027.
Environmental sustainability is driving innovation in bio-inspired robotics, with new systems designed to use eco-friendly materials and minimize waste. Robots equipped with advanced recycling capabilities will help construction sites achieve zero-waste goals while maintaining productivity.
The integration of Internet of Things (IoT) technology with construction robots will create more connected and intelligent job sites. Experts anticipate that by 2026, most construction robots will be part of an interconnected ecosystem, sharing data and coordinating activities in real-time.
Perhaps most significantly, the development of hybrid human-robot workflows will become increasingly sophisticated. These systems will optimize the strengths of both human workers and robotic assistance, leading to more efficient and safer construction processes. Industry leaders expect this collaboration to become the new standard in construction, with robots handling repetitive or dangerous tasks while humans focus on supervision, quality control, and complex decision-making.
As these trends materialize, construction companies must prepare by investing in training programs and updating their technological infrastructure. The future of construction robotics promises not just increased efficiency and safety, but a fundamental transformation in how buildings are designed and constructed.
The integration of robotics in construction represents a transformative shift that industry professionals must actively prepare for. As we’ve explored, automated systems are revolutionizing traditional construction processes, from bricklaying to site surveying. To stay competitive, construction companies should begin by assessing their current operations and identifying areas where robotics can enhance productivity and safety. Investment in workforce training and development of robotics expertise should be prioritized. Industry leaders must also stay informed about emerging technologies and regulatory requirements while building partnerships with robotics suppliers and technology providers. The future of construction lies in the successful balance of human expertise with robotic efficiency. By taking strategic steps today, construction professionals can position themselves at the forefront of this technological revolution, ensuring their operations remain efficient, safe, and profitable in the years ahead.