Digital transformation is revolutionizing the construction industry, driving unprecedented improvements in project efficiency, safety, and profitability. From artificial intelligence-powered project management platforms to autonomous equipment and drone-based site surveillance, technology adoption has become a critical differentiator between industry leaders and laggards. Recent studies indicate that construction firms implementing integrated digital solutions report up to 35% reduction in project delivery times and 20% decrease in overall costs.
The convergence of Building Information Modeling (BIM), Internet of Things (IoT) sensors, and cloud-based collaboration tools is creating a connected construction ecosystem that enables real-time decision-making and predictive analytics. Forward-thinking organizations are leveraging these technologies to address traditional industry challenges such as project delays, cost overruns, and safety incidents while simultaneously improving sustainability and quality control.
As the construction sector continues its digital evolution, professionals must understand and adapt to these technological advances to remain competitive. This transformation isn’t just about adopting new tools – it’s about fundamentally reimagining construction processes for the digital age. The companies that successfully integrate these technologies while maintaining focus on practical implementation and measurable outcomes will define the future of construction.
Real-Time Project Management Platforms
BIM Integration and Digital Twin Technology
Building Information Modeling (BIM) and digital twin technology are revolutionizing how construction projects are planned, executed, and managed. Modern BIM modeling technologies enable stakeholders to create detailed virtual representations of buildings before breaking ground, facilitating better coordination and decision-making throughout the project lifecycle.
Digital twins take this concept further by creating real-time virtual replicas of physical structures, complete with IoT sensor integration and live data feeds. This technology allows project managers to monitor construction progress, analyze performance metrics, and identify potential issues before they become costly problems. For instance, the recent development of Singapore’s Marina Bay Sands utilized digital twin technology to optimize energy consumption and maintenance schedules, resulting in a 25% reduction in operational costs.
The integration of BIM and digital twins is particularly powerful in renovation and retrofit projects, where existing structures must be carefully documented and analyzed. Project teams can simulate various scenarios and their impacts, from structural modifications to systems upgrades, ensuring optimal outcomes while minimizing risks. This capability has proven invaluable in complex projects like hospital renovations, where maintaining operational continuity is crucial.
As these technologies mature, they’re becoming increasingly accessible to mid-sized construction firms, democratizing access to advanced project management and visualization tools that were once the domain of only the largest organizations.
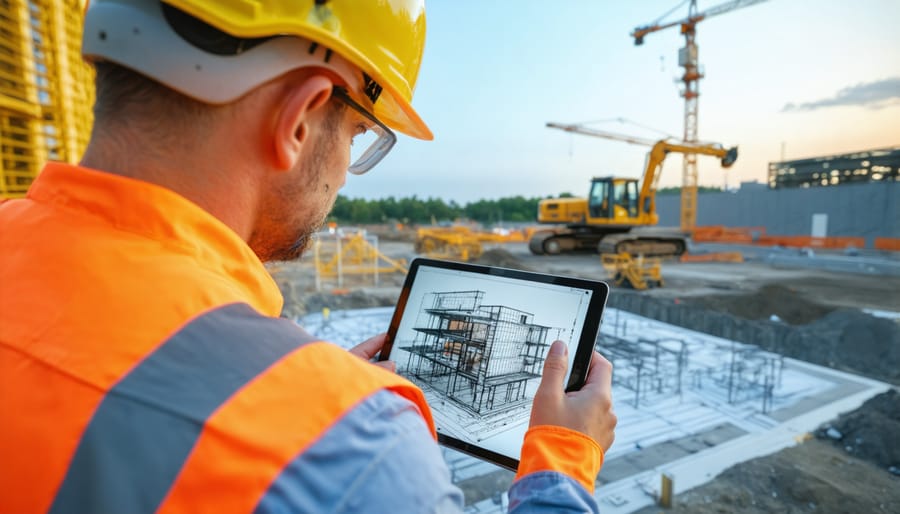
Mobile-First Solutions
The construction industry has embraced mobile-first solutions as essential tools for streamlining operations and enhancing field-to-office communication. Modern construction professionals rely on purpose-built mobile applications that enable real-time collaboration, document sharing, and project management from any location.
Field-ready apps now offer comprehensive functionality, including digital blueprints, BIM model viewing, punch list management, and safety inspection tools. Project managers can instantly update schedules, assign tasks, and track progress using intuitive mobile interfaces, while field workers can document site conditions, submit RFIs, and access critical project information without returning to the office.
Leading construction firms report significant efficiency gains through mobile solution adoption. For instance, McCarthy Building Companies achieved a 75% reduction in documentation time after implementing a mobile-first approach to field reporting. Similarly, Gilbane Building Company enhanced their quality control processes by enabling real-time photo documentation and issue tracking through mobile devices.
Cloud-based mobile platforms ensure that all stakeholders work with the latest project information, reducing errors and minimizing delays. These solutions typically include offline capabilities, allowing teams to maintain productivity even in areas with limited connectivity. Advanced features such as augmented reality (AR) viewing, voice-to-text documentation, and GPS-enabled asset tracking are becoming standard offerings, further enhancing field operations efficiency.
For successful implementation, companies should prioritize user-friendly interfaces, robust security measures, and seamless integration with existing project management systems.
AI and Machine Learning Applications
Predictive Analytics for Risk Management
Predictive analytics powered by artificial intelligence is revolutionizing risk management in construction projects. By analyzing vast amounts of historical project data, weather patterns, equipment performance metrics, and workforce productivity indicators, AI algorithms can now forecast potential risks before they materialize on construction sites.
These advanced systems continuously monitor real-time data from IoT sensors, project management software, and environmental monitoring devices to identify patterns that might indicate impending issues. For instance, machine learning models can predict equipment failures by analyzing performance data, enabling proactive maintenance and reducing costly downtime.
Safety risk prediction has seen significant advancement, with AI systems analyzing worker behavior patterns, site conditions, and historical accident data to identify high-risk scenarios. Some construction firms report up to a 30% reduction in workplace incidents after implementing these predictive safety solutions.
Financial risk assessment has also been transformed through predictive analytics. AI models can now forecast cost overruns and project delays by analyzing factors such as material price fluctuations, labor availability, and weather forecasts. Leading construction companies are using these insights to optimize resource allocation and maintain project timelines.
The integration of Building Information Modeling (BIM) with predictive analytics enables contractors to simulate various construction scenarios and identify potential structural or design risks before breaking ground. This proactive approach to risk management has proven particularly valuable in complex urban construction projects where margins for error are minimal.
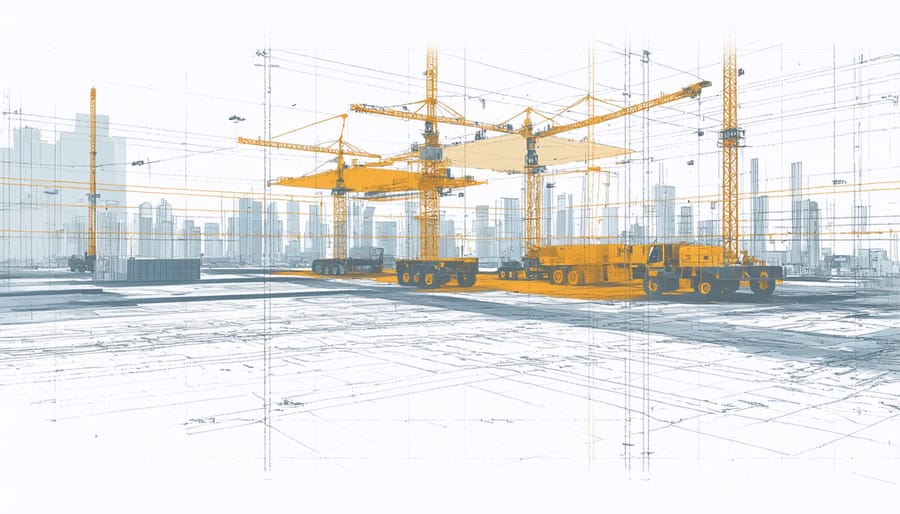
Automated Progress Monitoring
Computer vision and artificial intelligence are revolutionizing construction progress monitoring, offering unprecedented accuracy and efficiency in project tracking. These technologies utilize strategically placed cameras and sensors throughout construction sites to capture real-time data and compare it against project schedules and BIM models.
Advanced AI algorithms analyze thousands of images daily, automatically identifying completed work, detecting deviations from plans, and measuring progress across multiple project components. This continuous monitoring enables project managers to make data-driven decisions and address potential delays before they impact the schedule.
Real-world implementations have shown remarkable results. A recent case study of a 40-story commercial building project demonstrated that automated progress monitoring reduced reporting time by 80% while increasing accuracy to 95%. The system successfully tracked structural elements, MEP installations, and finishing work simultaneously.
Key benefits include:
– Real-time progress visualization
– Automatic generation of daily reports
– Early detection of construction defects
– Enhanced collaboration between stakeholders
– Improved resource allocation
– Precise documentation for payment verification
The technology also integrates with existing project management software, creating a comprehensive digital ecosystem for construction monitoring. Machine learning capabilities enable the system to improve its accuracy over time, learning from project-specific patterns and requirements.
While initial setup costs can be significant, the return on investment typically materializes within the first year through reduced labor costs, improved productivity, and minimized rework.
IoT and Sensor Technology
Equipment Monitoring Systems
Modern construction equipment now incorporates sophisticated IoT sensors and monitoring systems that provide real-time insights into machine performance and health. These advanced systems continuously track critical parameters such as fuel consumption, engine temperature, hydraulic pressure, and operational hours, enabling proactive maintenance scheduling and reduced downtime.
Integration with predictive maintenance systems allows fleet managers to anticipate potential failures before they occur, optimizing equipment lifecycle management. Data analytics platforms process this information to generate actionable insights, helping construction companies make informed decisions about equipment deployment and maintenance schedules.
Leading construction firms report up to 30% reduction in equipment maintenance costs and 25% improvement in operational efficiency through IoT monitoring implementation. These systems also enhance safety by alerting operators to potential hazards and tracking equipment location and usage patterns. The integration of GPS tracking further enables efficient resource allocation and prevents unauthorized equipment use, contributing to better asset management and project timeline adherence.
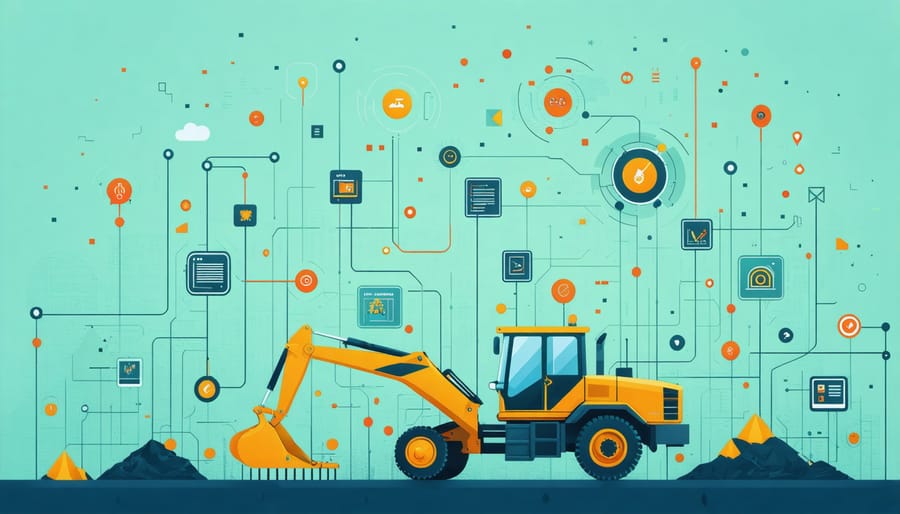
Environmental and Safety Monitoring
Advanced sensor technology is revolutionizing workplace safety monitoring in construction sites, providing real-time data and early warning systems that protect workers and assets. Environmental sensors continuously track air quality, temperature, humidity, and harmful gas levels, enabling immediate response to potentially hazardous conditions. Wearable devices equipped with biometric sensors monitor workers’ vital signs, physical strain, and fatigue levels, helping prevent accidents caused by overexertion.
IoT-enabled safety systems now integrate multiple sensor types to create comprehensive monitoring networks. Motion sensors and proximity detectors alert workers to dangerous equipment movements, while structural sensors monitor building stability during construction phases. Many of these systems feature AI-powered analytics that can predict potential safety issues before they occur.
According to recent industry studies, construction sites implementing comprehensive sensor-based monitoring systems have reported up to 45% reduction in workplace incidents. These technologies also assist in maintaining regulatory compliance by automatically documenting environmental conditions and safety metrics. Project managers can access real-time dashboards showing site-wide safety status, enabling faster decision-making and more effective resource allocation for hazard mitigation.
Implementation Strategies
Cost-Benefit Analysis
A comprehensive cost-benefit analysis is essential for construction firms considering technology investments. This framework helps organizations evaluate potential returns while accounting for both direct and indirect costs associated with implementation.
The initial investment typically encompasses hardware, software licenses, installation costs, and necessary infrastructure upgrades. Companies must also factor in ongoing expenses such as maintenance, updates, training programs, and technical support. Hidden costs often include temporary productivity dips during the transition period and potential system downtime.
On the benefits side, technology implementations generally yield both quantifiable and qualitative returns. Quantifiable benefits include reduced labor costs, decreased material waste, improved project completion times, and lower rework expenses. Studies indicate that construction firms implementing integrated project management solutions typically see a 15-25% reduction in project delays and a 10-20% decrease in material waste.
Qualitative benefits, while harder to measure, are equally important. These include enhanced collaboration, improved safety compliance, better quality control, and increased client satisfaction. Companies report higher employee retention rates and improved ability to attract skilled workers when utilizing modern construction technologies.
To conduct an effective analysis, organizations should:
– Document current processes and associated costs
– Identify specific pain points and improvement opportunities
– Calculate total cost of ownership (TCO) over 3-5 years
– Estimate both immediate and long-term ROI
– Consider scalability and future integration needs
– Evaluate competitive advantages gained
Industry best practices suggest using a phased implementation approach to manage risks and validate benefits before full-scale deployment. This method allows organizations to adjust their strategy based on early results and maximize their technology investment returns.
Training and Integration
Successful implementation of construction technology requires a strategic approach to training and workforce integration. Organizations must develop comprehensive onboarding programs that address both technical competencies and cultural adaptation to new digital workflows.
Initial assessment of workforce digital literacy is crucial for tailoring training programs effectively. Construction companies should create role-specific training modules that focus on practical applications rather than theoretical knowledge. This approach helps workers understand how technology directly benefits their daily tasks and improves job site efficiency.
Integration success often hinges on identifying technology champions within the organization. These individuals serve as mentors and facilitate peer-to-peer learning, making adoption more organic and sustainable. Companies should also consider partnering with technology vendors who offer ongoing support and training resources, ensuring teams can maximize the potential of project management automation tools and other digital solutions.
Best practices include implementing pilot programs before full-scale deployment, allowing teams to familiarize themselves with new systems in a controlled environment. Regular feedback sessions help identify challenges early and enable necessary adjustments to training approaches.
Documentation and standardization of processes are essential components of technology integration. Creating clear standard operating procedures (SOPs) and maintaining updated digital training materials ensures consistency across projects and helps new team members adapt quickly to technological solutions.
Continuous evaluation of training effectiveness through performance metrics and user feedback helps organizations refine their integration strategies and maintain competitive advantage in an increasingly digital construction landscape.
The construction industry stands at a pivotal moment of technological transformation. As we’ve explored throughout this article, the integration of digital solutions, automation, and advanced analytics is reshaping traditional construction practices. The adoption of Building Information Modeling (BIM), artificial intelligence, and IoT sensors has demonstrated significant improvements in project efficiency, cost reduction, and safety standards across the sector.
Looking ahead, the construction technology landscape will continue to evolve rapidly. Emerging technologies such as autonomous equipment, advanced robotics, and digital twins are poised to further revolutionize construction processes. The industry can expect to see increased integration of sustainable building technologies, enhanced data analytics capabilities, and more sophisticated project management platforms.
However, successful technology implementation requires a strategic approach. Construction firms must focus on comprehensive training programs, establish clear digital transformation roadmaps, and maintain cybersecurity protocols. The key to maximizing ROI lies in selecting technologies that align with specific organizational needs while ensuring seamless integration with existing systems.
As we move forward, the construction industry’s competitive advantage will increasingly depend on technological prowess. Organizations that embrace innovation while maintaining a balanced approach to implementation will be best positioned for success. The future of construction technology isn’t just about adopting new tools – it’s about fundamentally transforming how we plan, execute, and deliver construction projects in an increasingly digital world.