Digital transformation is revolutionizing the construction industry at an unprecedented pace, with global investments in construction technology companies exceeding $4.5 billion annually. From artificial intelligence-driven project management to robotics-enabled construction sites, digital technologies are fundamentally reshaping how we plan, execute, and deliver construction projects.
The integration of Building Information Modeling (BIM), Internet of Things (IoT) sensors, and cloud-based collaboration platforms has created a new paradigm where real-time data drives decision-making, enhances productivity, and minimizes costly errors. This digital ecosystem enables construction professionals to achieve levels of precision, efficiency, and sustainability that were previously unattainable.
As the industry faces increasing pressure to improve productivity, reduce environmental impact, and address skilled labor shortages, digital construction technologies offer compelling solutions. Advanced analytics, autonomous equipment, and digital twins are not just technological innovations – they represent essential tools for staying competitive in an evolving marketplace. Industry leaders who embrace these digital solutions position themselves at the forefront of construction’s technological revolution, ready to tackle the complex challenges of modern building projects.
BIM and Digital Twin Technologies
Real-Time Project Visualization
Real-time project visualization has revolutionized how construction teams plan, execute, and monitor their projects. Through advanced 3D modeling and virtual reality (VR) applications, stakeholders can now interact with detailed digital representations of buildings before breaking ground.
Building Information Modeling (BIM) serves as the foundation for these visualization capabilities, creating comprehensive digital twins that incorporate every aspect of the construction project. Project teams can navigate through virtual structures, identify potential conflicts, and make informed decisions about design modifications well before physical construction begins.
Virtual reality applications have particularly transformed project planning by enabling immersive walkthroughs. Construction managers and clients can experience spaces in true-to-scale environments, leading to better design decisions and fewer costly changes during construction. This technology has proven especially valuable for complex projects where spatial relationships and user experience are critical factors.
Augmented reality (AR) supplements these visualization tools by overlaying digital information onto real-world construction sites. Field teams can view BIM models superimposed on actual work areas through mobile devices or AR headsets, ensuring precise installation and reducing errors.
Recent advancements in real-time rendering have made it possible to visualize design changes instantaneously during collaborative sessions. This capability facilitates more efficient decision-making processes and enables remote stakeholders to participate meaningfully in project reviews, regardless of their physical location.
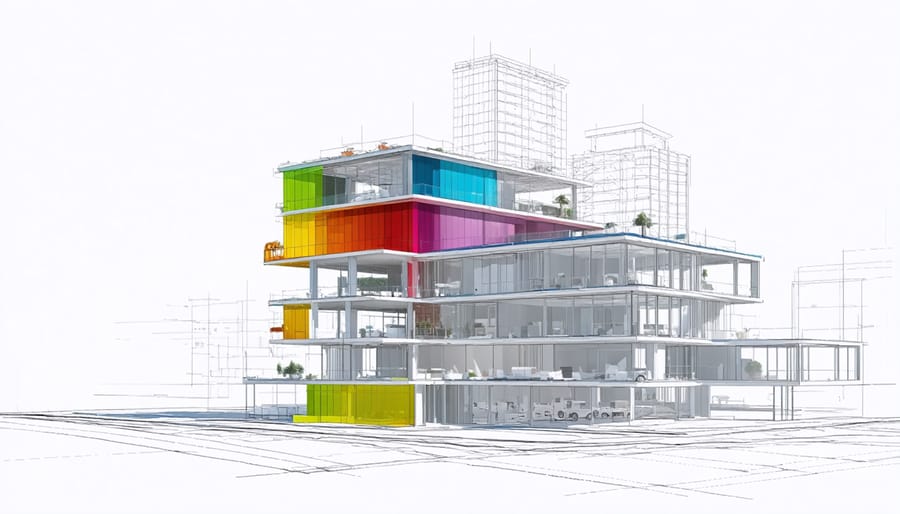
Clash Detection and Problem Prevention
Building Information Modeling (BIM) has revolutionized how construction teams identify and resolve potential conflicts before they become costly on-site problems. Through advanced 3D modeling and intelligent clash detection algorithms, BIM systems automatically identify spatial conflicts between different building components, such as mechanical systems intersecting with structural elements or plumbing lines conflicting with electrical conduits.
Studies indicate that early clash detection through BIM can reduce construction rework by up to 40% and generate cost savings of 2-5% of the total project value. The process works by creating a federated model that combines individual trade models into a single coordinated view, allowing teams to run sophisticated interference checks and identify conflicts that might be missed in traditional 2D reviews.
Real-time collaboration features enable multiple stakeholders to address detected clashes simultaneously, streamlining the resolution process. When conflicts are identified, the system generates detailed reports highlighting specific problem areas, allowing project teams to implement solutions during the design phase rather than discovering issues during construction.
Beyond spatial coordination, BIM’s clash detection capabilities extend to temporal conflicts through 4D scheduling integration. This helps teams identify potential timeline conflicts and logistical issues before they impact project schedules. The system also maintains a comprehensive audit trail of all identified conflicts and their resolutions, providing valuable documentation for quality assurance and future reference.
Automation and Robotics on Construction Sites
Autonomous Equipment
Autonomous equipment represents a significant advancement in construction technology, transforming traditional job sites into highly efficient, safer workspaces. Self-operating machinery, equipped with sophisticated sensors and AI-driven control systems, can now perform complex tasks with minimal human intervention while maintaining optimal construction site security.
Leading construction firms are deploying autonomous excavators that precisely execute earthmoving operations using LiDAR and GPS technology. These machines achieve accuracy levels within 1-2 centimeters while reducing operational time by up to 30% compared to manual operation. Similarly, self-driving dump trucks and material handlers optimize logistics by following predetermined routes and automatically adjusting their paths based on real-time site conditions.
Recent innovations include robotic bricklaying systems capable of laying 3,000 bricks per day – nearly triple the output of skilled human workers. Autonomous concrete finishing robots ensure consistent surface quality while reducing labor requirements and physical strain on workers. These systems integrate seamlessly with Building Information Modeling (BIM) data, enabling precise execution of design specifications.
The ROI for autonomous equipment typically materializes within 18-24 months through increased productivity, reduced labor costs, and improved safety metrics. Industry leaders report up to 45% reduction in workplace incidents after implementing autonomous systems.
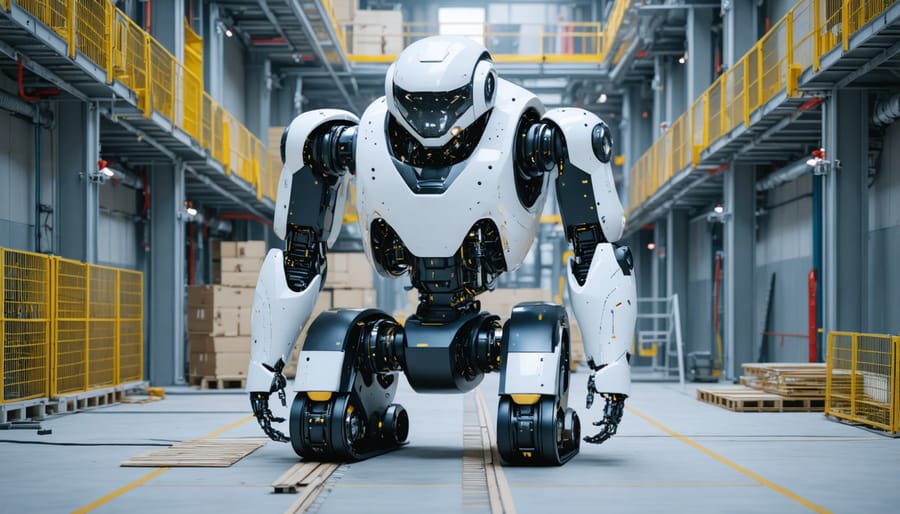
Prefabrication Technology
Prefabrication technology has revolutionized construction processes through automated manufacturing systems that produce building components in controlled factory environments. These advanced facilities utilize robotic assembly lines, computer-controlled cutting machines, and automated quality control systems to create precise, standardized building elements with minimal waste and maximum efficiency.
Modern prefabrication integrates seamlessly with Building Information Modeling (BIM) platforms, enabling direct translation of digital designs into manufacturing instructions. This digital-to-physical workflow ensures exceptional accuracy and reduces errors traditionally associated with manual interpretation of construction drawings.
The benefits of automated prefabrication are substantial: production time can be reduced by up to 50% compared to traditional methods, while quality consistency improves significantly. Weather-independent manufacturing conditions ensure year-round production capability, and the controlled environment allows for better material optimization and waste reduction.
Recent innovations include smart prefabrication systems that incorporate IoT sensors during production, enabling real-time monitoring of component quality and manufacturing processes. These sensors continue to provide valuable data throughout the building’s lifecycle, contributing to predictive maintenance and facility management.
The economic impact is equally impressive, with studies showing that automated prefabrication can reduce overall project costs by 20-30% while significantly improving workplace safety and reducing on-site labor requirements.
IoT and Sensor Integration
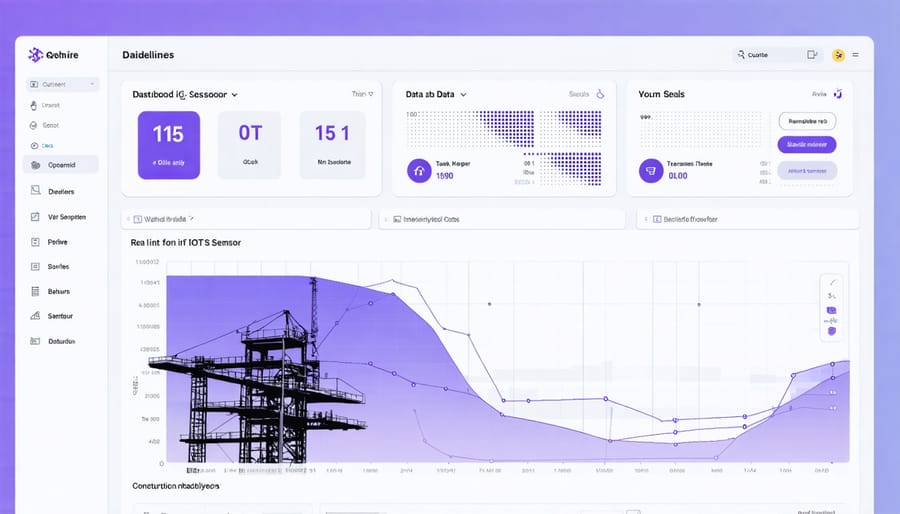
Real-Time Site Monitoring
Real-time site monitoring has revolutionized construction management through the deployment of sophisticated sensor networks that provide continuous oversight of both safety conditions and project progress. These integrated systems utilize a combination of IoT sensors, cameras, and environmental monitors to create a comprehensive digital overview of construction operations.
Advanced sensor networks track critical safety parameters including air quality, noise levels, and structural stability in real-time. Motion sensors and wearable devices monitor worker movements and can instantly alert supervisors to potential safety hazards or accidents. This proactive approach to safety management has demonstrated up to 50% reduction in workplace incidents on sites where these systems are properly implemented.
For progress tracking, automated monitoring systems use a combination of fixed cameras, drone footage, and LiDAR scanners to compare actual construction progress against BIM models and project schedules. These systems can identify discrepancies between planned and actual progress, enabling project managers to make data-driven decisions and implement corrective measures promptly.
The collected data is typically accessible through cloud-based platforms, allowing stakeholders to monitor site conditions remotely and receive automated alerts when parameters exceed predetermined thresholds. This level of oversight ensures better compliance with safety regulations while maintaining optimal project efficiency.
Equipment Performance Tracking
IoT-enabled equipment performance tracking has revolutionized how construction firms monitor and maintain their machinery fleet. Through strategically placed sensors and real-time data collection, construction companies can now track vital metrics such as fuel consumption, engine hours, location, and operational efficiency of their equipment.
These smart systems continuously monitor equipment health indicators, detecting potential issues before they lead to costly breakdowns. For example, vibration analysis sensors can identify bearing wear patterns, while temperature monitoring helps prevent engine overheating. This predictive maintenance approach has shown to reduce equipment downtime by up to 40% and extend machinery lifespan by 20-25%.
Real-time performance data enables project managers to optimize equipment utilization across multiple sites. Advanced analytics platforms process this information to generate actionable insights, such as identifying underutilized machinery or suggesting optimal maintenance schedules. Companies implementing these systems report significant improvements in fleet management efficiency, with some achieving 15-20% reduction in operational costs.
The integration of GPS tracking and geofencing capabilities further enhances equipment security and ensures proper usage within designated work zones, while automated reporting systems simplify compliance documentation and maintenance records.
Data Analytics and AI Applications
Predictive Analytics
Predictive analytics represents a groundbreaking advancement in construction project management, leveraging artificial intelligence and machine learning to forecast potential challenges and optimize project outcomes. By analyzing historical project data, weather patterns, resource allocation, and market conditions, these sophisticated systems can generate accurate predictions for project timelines, costs, and potential risks.
Construction firms implementing predictive analytics report up to 25% reduction in project delays and a 20% improvement in budget accuracy. The technology excels in identifying patterns that might escape human observation, such as correlations between weather conditions and productivity rates, or relationships between material delivery schedules and project milestones.
Risk assessment capabilities have been particularly transformative, enabling project managers to anticipate and mitigate potential issues before they impact the project. Advanced algorithms can evaluate thousands of variables simultaneously, from supply chain disruptions to labor availability, providing real-time risk scores and mitigation recommendations.
Leading construction firms are now integrating predictive analytics with Building Information Modeling (BIM) systems to create comprehensive project simulations. These integrated solutions offer unprecedented visibility into project lifecycles, enabling teams to optimize schedules, reduce waste, and make data-driven decisions throughout the construction process.
Resource Optimization
Artificial Intelligence is revolutionizing resource optimization in construction projects through sophisticated algorithms that enhance decision-making and operational efficiency. AI-powered platforms now analyze vast datasets to optimize workforce allocation, equipment utilization, and material management in real-time. These systems consider multiple variables, including weather conditions, worker availability, equipment maintenance schedules, and delivery timelines to create highly efficient project schedules.
Advanced machine learning algorithms can predict resource requirements with remarkable accuracy, helping project managers prevent bottlenecks and reduce waste. This technological approach aligns perfectly with sustainable construction practices by minimizing excess material orders and optimizing transportation logistics.
Case studies have shown that AI-driven resource optimization can reduce project costs by 15-20% while improving completion times by up to 25%. For instance, leading construction firms are using predictive analytics to optimize equipment deployment across multiple sites, resulting in significantly higher utilization rates and lower idle times.
The integration of IoT sensors with AI platforms enables real-time tracking of materials and equipment, providing project managers with actionable insights for immediate decision-making. This data-driven approach ensures optimal resource allocation while maintaining project quality and timeline commitments.
Future Implementation Strategies
Successful implementation of digital construction technologies requires a strategic, phased approach that considers both organizational readiness and resource allocation. Construction companies should begin by conducting a thorough digital maturity assessment to identify gaps and opportunities within their current operations. This evaluation serves as the foundation for developing a comprehensive digital transformation roadmap.
The next crucial step involves selecting pilot projects for initial technology deployment. These projects should be carefully chosen to demonstrate quick wins while minimizing disruption to ongoing operations. Companies should prioritize digital construction initiatives that align with their specific business objectives and operational challenges.
Training and workforce development play a vital role in technology adoption. Organizations must invest in comprehensive training programs that address both technical skills and change management. This includes establishing dedicated digital champions within teams to facilitate knowledge transfer and support adoption across all levels of the organization.
Data integration and standardization should be prioritized early in the implementation process. Companies need to establish clear protocols for data collection, storage, and sharing across different platforms and stakeholders. This infrastructure forms the backbone for future digital innovations and ensures seamless communication between various technology solutions.
Finally, organizations should develop clear metrics for measuring success and ROI. These metrics should track both quantitative outcomes (cost savings, productivity improvements) and qualitative benefits (improved collaboration, enhanced safety). Regular assessment of these metrics enables organizations to adjust their implementation strategies and ensure continued alignment with business objectives.
Digital construction technology has fundamentally transformed the building industry, revolutionizing how we plan, execute, and manage construction projects. From BIM and digital twins to AI-powered analytics and robotics, these innovations have delivered unprecedented improvements in efficiency, accuracy, and project outcomes. The integration of these technologies has led to significant cost reductions, enhanced safety standards, and superior quality control across construction operations.
Looking ahead, the construction industry is poised for even greater technological advancement. Emerging trends suggest that autonomous construction equipment, advanced prefabrication techniques, and real-time project management platforms will become industry standards. The convergence of IoT sensors, 5G connectivity, and cloud computing promises to create fully connected construction sites that optimize resource utilization and enable predictive maintenance.
As sustainability requirements become more stringent and skilled labor shortages persist, digital technologies will play an increasingly crucial role in meeting these challenges. Construction firms that embrace digital transformation today will be better positioned to compete in tomorrow’s market. The future of construction is undeniably digital, and continued investment in these technologies will be essential for long-term success in the industry.