The rapid advancement of the 3D printing revolution in construction has fundamentally transformed material science in the building sector. Contemporary construction-grade materials now encompass specialized concrete composites, polymer-modified cementitious mixtures, and advanced geopolymer formulations specifically engineered for additive manufacturing processes. These materials must meet precise requirements for extrudability, layer adhesion, and structural integrity while maintaining workability throughout the printing process.
The evolution of these materials represents a critical intersection between traditional construction methods and cutting-edge digital fabrication technologies. Enhanced with nano-materials, fiber reinforcements, and smart additives, modern 3D printing materials deliver superior mechanical properties, reduced curing times, and improved dimensional stability compared to conventional construction materials. Industry professionals must understand these materials’ unique characteristics, from rheological properties to final-state performance metrics, to effectively implement 3D printing technology in their construction projects.
This comprehensive analysis examines the most significant materials currently employed in construction-scale 3D printing, their specific applications, and the technical considerations that influence material selection and performance optimization. Through detailed examination of material compositions, performance data, and real-world case studies, we provide essential insights for construction professionals seeking to integrate additive manufacturing into their building processes.
Concrete-Based Materials: The Foundation of 3D Construction
Modified Concrete Composites
Modified concrete composites for 3D printing construction represent a significant advancement in building technology, requiring specific formulations that differ substantially from traditional concrete mixtures. These specialized materials are engineered to meet the unique demands of concrete printing applications, particularly in terms of extrudability, buildability, and setting time.
The primary components typically include ordinary Portland cement, supplementary cementitious materials (SCMs), carefully selected aggregates, and advanced chemical admixtures. The mixture design focuses on achieving optimal rheological properties, with particular attention to flowability and thixotropy. These properties ensure the material can be pumped efficiently through the printing system while maintaining shape stability after extrusion.
Key modifications often include the incorporation of silica fume and fly ash to enhance cohesion and reduce segregation. The aggregate size is typically limited to 4-8mm to prevent nozzle blockage and ensure smooth extrusion. High-range water reducers and viscosity modifying agents are essential additives that help maintain workability without compromising strength development.
Recent developments have introduced fiber reinforcement, typically using polypropylene or steel fibers, to improve tensile strength and reduce shrinkage cracking. Some advanced formulations incorporate phase-change materials (PCMs) or self-healing agents to enhance long-term durability and performance.
The water-to-cement ratio is carefully controlled, typically ranging between 0.35-0.45, to achieve the right balance between printability and structural integrity. Setting accelerators are often included to ensure rapid strength development, enabling the material to support subsequent layers without deformation.
These modified composites must demonstrate consistent performance across various environmental conditions, maintaining their properties throughout the printing process. Quality control measures are particularly crucial, as slight variations in mixture proportions can significantly impact printing success and final structural performance.
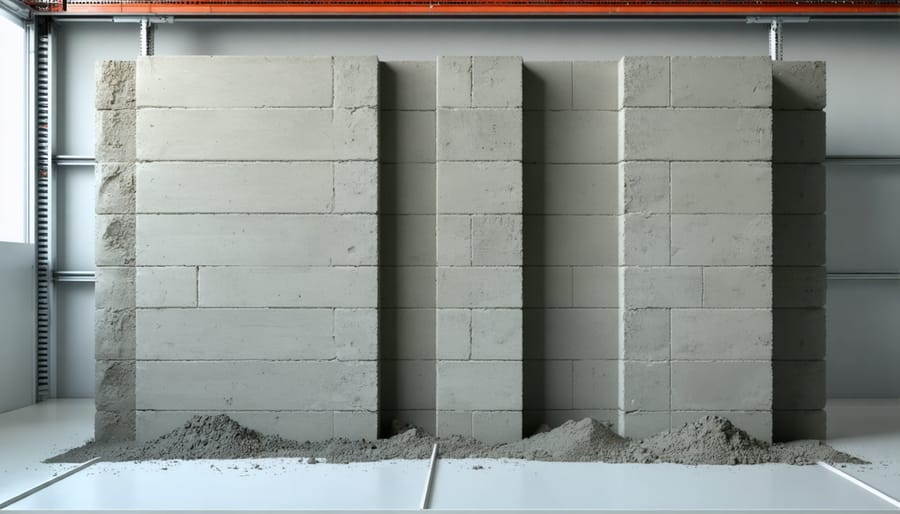
Performance Enhancing Additives
Performance enhancing additives play a crucial role in optimizing the properties of 3D printed construction materials. These additives can be broadly categorized into chemical admixtures and reinforcement materials, each serving specific functions in improving the final product’s performance and durability.
Chemical admixtures are essential components that modify the behavior of concrete mixtures during printing and curing phases. Superplasticizers enhance flowability while maintaining proper viscosity, ensuring smooth material extrusion through the printer nozzle. Set-time modifiers, including accelerators and retarders, help control the crucial window between layers, preventing cold joints while maintaining structural integrity.
Silica fume and fly ash are commonly used as supplementary cementitious materials, improving both fresh and hardened properties of the printed structure. These materials enhance particle packing density and reduce porosity, resulting in higher compressive strength and better durability.
For structural reinforcement, various fiber types are incorporated into the printing mixture. Steel fibers provide excellent tensile strength and crack resistance, while synthetic fibers like polypropylene and glass fibers offer improved ductility and impact resistance. Recent innovations include the use of carbon fibers and basalt fibers, which provide superior strength-to-weight ratios.
Nano-materials such as carbon nanotubes and graphene oxide are emerging as revolutionary additives in 3D printed construction. These materials significantly enhance mechanical properties and can introduce smart features like self-sensing capabilities for structural health monitoring.
Water-reducing agents and viscosity modifying admixtures (VMA) are essential for maintaining proper rheological properties. They ensure consistent material flow while preventing segregation and bleeding, critical factors for successful layer-by-layer construction.
The selection of performance enhancing additives must consider factors such as material compatibility, environmental conditions, and project requirements. Proper dosage and mixing sequences are crucial for achieving optimal results, as overdosing can lead to adverse effects on print quality and structural performance.
Polymer-Based Construction Materials
Thermoplastic Materials
Thermoplastic materials play a crucial role in 3D printed construction, offering unique advantages in terms of workability, cost-effectiveness, and potential for reducing environmental impact through recyclability. The most commonly used thermoplastics include Acrylonitrile Butadiene Styrene (ABS), Polylactic Acid (PLA), and High-Impact Polystyrene (HIPS), each bringing distinct properties to construction applications.
ABS stands out for its excellent structural integrity and impact resistance, making it ideal for load-bearing components and architectural elements. Its high glass transition temperature ensures stability across varying weather conditions, while its chemical resistance protects against environmental degradation.
PLA, derived from renewable resources like corn starch, offers superior printability and dimensional accuracy. While traditionally considered less durable than ABS, recent advancements in PLA composites have significantly enhanced its mechanical properties, making it suitable for non-structural building components and decorative elements.
HIPS provides exceptional dimensional stability and weather resistance, particularly valuable for exterior applications. Its lightweight nature and ease of processing make it cost-effective for large-scale printing projects, while its smooth surface finish reduces post-processing requirements.
Emerging developments in fiber-reinforced thermoplastics are expanding applications in structural elements. Glass fiber and carbon fiber composites demonstrate enhanced strength-to-weight ratios and improved thermal performance, enabling their use in more demanding construction scenarios.
When selecting thermoplastic materials for construction projects, professionals must consider factors such as UV stability, fire resistance, and thermal expansion coefficients. Proper material certification and compliance with building codes remain essential for successful implementation in construction projects.
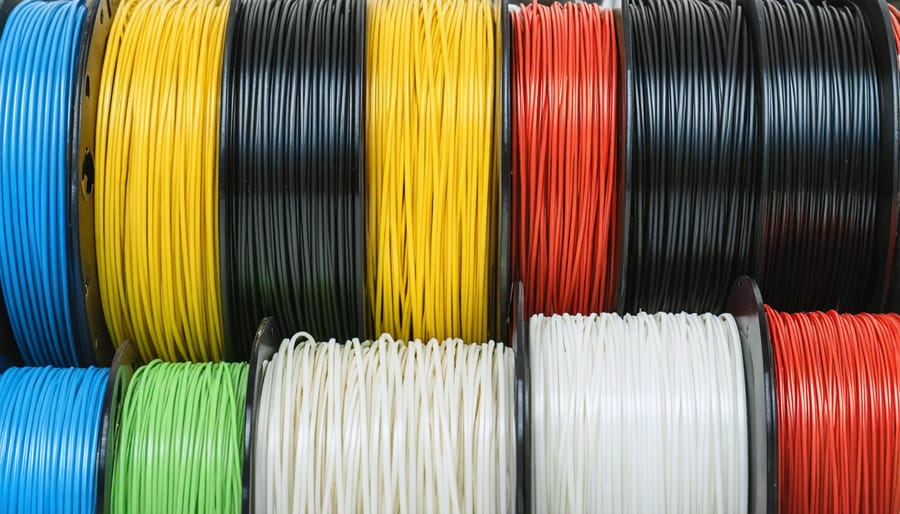
Composite Polymers
Composite polymers represent a significant advancement in 3D printing construction materials, combining the versatility of polymeric materials with enhanced structural properties. These sophisticated blends typically incorporate reinforcing agents such as glass fibers, carbon fibers, or mineral particles within a polymer matrix, creating materials that exhibit superior mechanical strength and durability compared to traditional polymers.
The most widely used composite formulations include fiber-reinforced polymers (FRPs) and particle-reinforced composites. Glass fiber-reinforced polymers (GFRPs) offer excellent tensile strength and impact resistance while maintaining relatively low weight, making them ideal for load-bearing components in 3D printed structures. Carbon fiber composites, though more expensive, provide exceptional strength-to-weight ratios and thermal stability, crucial for high-performance architectural elements.
Recent developments have introduced nano-reinforced polymers, where materials like carbon nanotubes or graphene are incorporated at the molecular level. These additions significantly enhance the material’s mechanical properties while maintaining printability. For instance, nano-silica reinforced polymers have shown up to 40% improvement in compressive strength compared to conventional polymer formulations.
Construction professionals should consider several key factors when selecting composite polymers for 3D printing applications. These include the material’s viscosity during printing, cure time, thermal expansion coefficients, and long-term stability under environmental exposure. The optimal blend ratio between the polymer matrix and reinforcing agents must be carefully balanced to maintain printability while achieving desired structural properties.
Performance data from recent construction projects demonstrates that composite polymers can achieve compressive strengths ranging from 40 to 90 MPa, making them suitable for both structural and non-structural applications in modern construction.
Sustainable and Bio-Based Materials
Recycled Materials
The integration of recycled materials in 3D construction printing represents a significant advancement in sustainable construction practices. Recent innovations have enabled the incorporation of various waste materials into printable concrete mixtures, reducing environmental impact while maintaining structural integrity.
Construction and demolition waste (CDW), when properly processed and screened, can replace up to 50% of virgin aggregates in 3D printing concrete mixtures. Research indicates that recycled concrete aggregates (RCA), when combined with appropriate admixtures, achieve comparable mechanical properties to traditional materials. Glass waste, ground into fine particles, serves as an effective supplementary cementitious material, enhancing workability and reducing cement content.
Industrial by-products such as fly ash and slag have demonstrated excellent performance in 3D printing applications. These materials not only improve the environmental footprint but also enhance specific properties of the printing mixture. Fly ash increases flowability and reduces heat of hydration, while slag contributes to long-term strength development.
Plastic waste, particularly PET and HDPE, can be processed into fiber reinforcement for printed concrete, improving tensile strength and crack resistance. Several pilot projects have successfully utilized these recycled materials, demonstrating their viability in full-scale construction applications while reducing landfill waste and raw material consumption.
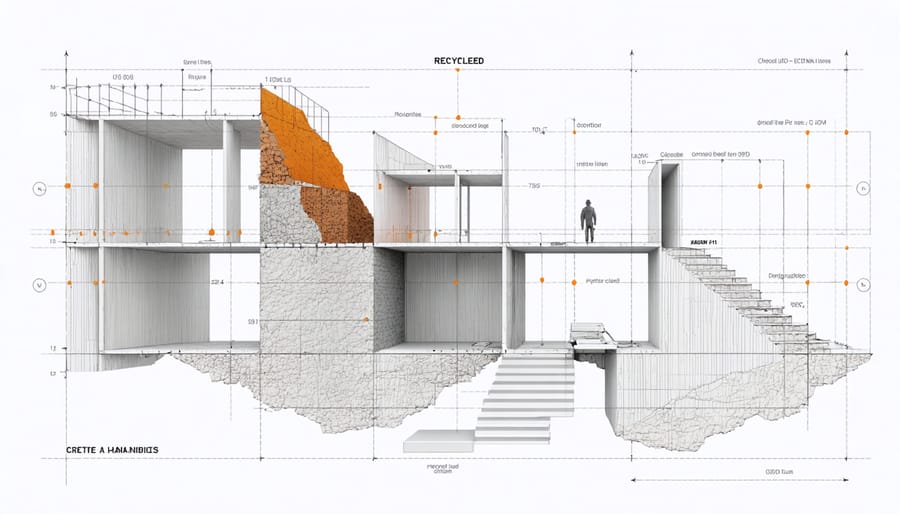
Natural Composites
Natural composites are emerging as sustainable alternatives in 3D printing construction, combining biological materials with traditional binding agents to create eco-friendly building solutions. Wood-based composites, incorporating sawdust and cellulose fibers, demonstrate impressive compressive strength while reducing the carbon footprint of construction projects.
Bamboo fiber reinforced composites have gained particular attention due to their high tensile strength and rapid renewability. When mixed with appropriate matrices, these materials exhibit excellent dimensional stability and resistance to environmental factors. Studies have shown that bamboo-based printing materials can achieve compressive strengths comparable to conventional concrete while offering superior flexibility.
Hemp-based composites represent another promising category, combining agricultural waste products with mineral binders to create lightweight yet durable construction materials. These materials offer excellent thermal insulation properties and natural moisture regulation capabilities, making them particularly suitable for residential construction.
Recent developments include mycelium-based composites, which utilize fungal growth as a natural binding agent. While still in experimental stages, these materials show promise for non-load-bearing applications and insulation purposes. Their self-growing nature and minimal energy requirements during production make them particularly attractive from a sustainability perspective.
Performance testing indicates that natural composites generally offer improved thermal properties and reduced environmental impact compared to traditional materials, though considerations must be made regarding moisture resistance and long-term durability in exposed conditions.
Material Selection Criteria
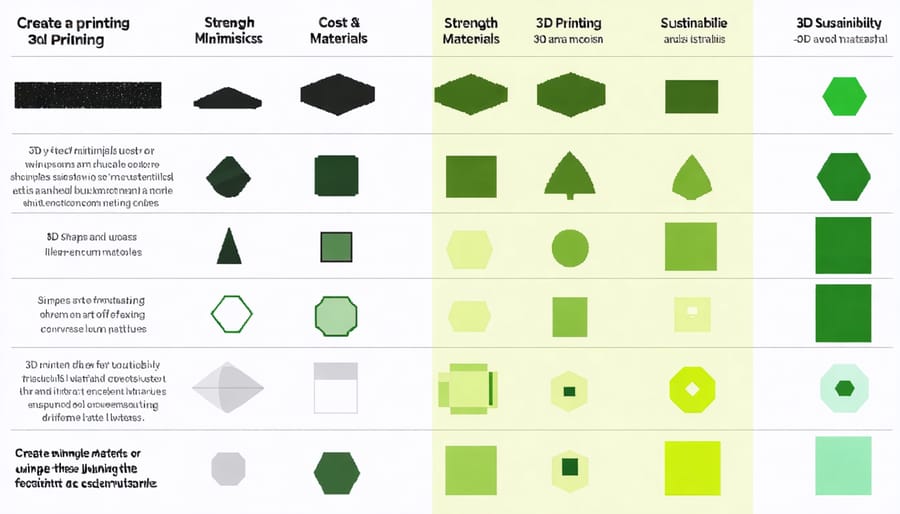
Performance Requirements
Materials used in 3D printing construction must meet rigorous performance requirements and comply with established building codes to ensure structural integrity and safety. The primary technical specifications focus on compressive strength, typically requiring a minimum of 4,000 PSI (27.6 MPa) for structural applications. The material’s flowability must maintain a Slump Flow value between 600-700mm to ensure proper extrusion while preventing segregation.
Durability requirements dictate that materials demonstrate freeze-thaw resistance of at least 300 cycles in cold climates and maintain structural integrity under varying environmental conditions. The setting time should be carefully controlled, with initial setting occurring between 20-60 minutes to allow proper layer adhesion while maintaining constructability.
Building codes increasingly address 3D printed construction materials, requiring compliance with standards such as ACI 318 for concrete structures. Materials must demonstrate fire resistance ratings according to ASTM E119, typically requiring a minimum 2-hour rating for load-bearing walls. Additionally, the mixture design must achieve a bond strength between layers of at least 1.5 MPa to ensure structural continuity.
Quality control specifications mandate regular testing of fresh material properties, including rheology measurements and temperature monitoring. The hardened material must undergo standardized testing for mechanical properties, with coefficient of variation not exceeding 15% for compressive strength results.
Environmental performance requirements include minimum recycled content specifications, typically 20% or higher, and VOC emission limits below 50 g/L. The material composition must also demonstrate resistance to chemical attack, with a pH tolerance range of 3-11, ensuring long-term durability in various exposure conditions.
Cost and Availability Considerations
The cost-effectiveness of materials in 3D construction printing varies significantly based on market availability, regional factors, and project scale. Traditional concrete-based mixtures typically range from $100-200 per cubic meter, while specialized printable concrete formulations can cost 30-50% more due to enhanced performance requirements and additives. These premium materials often justify their higher costs through reduced labor expenses and faster construction timelines.
Material availability presents another crucial consideration, as specialized 3D printing materials may not be readily accessible in all markets. Large-scale projects require reliable supply chains and local material sources to ensure consistent production. Some manufacturers have developed partnerships with regional suppliers to establish dedicated material production facilities, helping stabilize both costs and availability.
Storage and handling requirements also impact overall material costs. Many printable materials have specific temperature and humidity requirements, necessitating climate-controlled storage facilities. Additionally, some materials have limited shelf life, requiring careful inventory management to minimize waste.
Emerging alternatives like geopolymer-based materials and recycled content mixtures show promise in reducing material costs while maintaining performance standards. These sustainable options typically cost 10-15% less than traditional formulations, though availability may be limited in some regions.
Project planners should consider the total cost of ownership when selecting materials, including factors such as maintenance requirements, durability, and potential material waste during printing. While initial material costs might be higher for specialized formulations, the overall project economics often favor these materials due to reduced labor costs, faster construction times, and improved building performance.
The future of 3D printing construction materials stands at a pivotal moment, with rapid advancements reshaping traditional building practices. As one of the most transformative emerging construction technologies, materials science continues to evolve, promising enhanced performance and sustainability.
Industry experts anticipate significant developments in composite materials that combine strength with flexibility, potentially revolutionizing structural capabilities. Research laboratories worldwide are exploring bio-based alternatives and smart materials that can adapt to environmental conditions, suggesting a future where buildings become more responsive and sustainable.
The implications for the construction industry are far-reaching. Material costs are expected to decrease as production scales up and processes become more efficient. This cost reduction, coupled with improved material properties, will likely accelerate adoption across various construction sectors. Additionally, new materials being developed specifically for 3D printing applications will enable more complex architectural designs while maintaining structural integrity.
Environmental considerations will continue to drive innovation in material development. The focus on reducing carbon footprints and implementing circular economy principles is leading to breakthrough developments in recyclable and biodegradable construction materials. These advances will help address sustainability challenges while meeting increasingly stringent building regulations.
For construction professionals, staying informed about these material developments will be crucial. The integration of new materials will require updated skills and knowledge, creating opportunities for specialization in advanced construction techniques. As the technology matures, we can expect to see standardization of materials and processes, making 3D printing an increasingly viable option for mainstream construction projects.