Automation is revolutionizing the construction industry at an unprecedented pace, transforming traditional building processes into data-driven, efficient operations that deliver projects faster, safer, and more cost-effectively. From robotic bricklayers to AI-powered project management systems, construction firms are witnessing productivity gains of up to 50% while reducing workplace accidents by 30%. The integration of automated solutions addresses the industry’s most pressing challenges: labor shortages, rising costs, and increasing project complexity.
Industry leaders leveraging automation report significant improvements across key performance indicators: schedule adherence improved by 35%, material waste reduced by 25%, and project costs decreased by up to 20%. These metrics underscore automation’s potential to reshape construction fundamentals, from site preparation to final inspection. As construction demands grow more complex and deadlines more stringent, automation emerges as not just an operational advantage but a competitive necessity.
This comprehensive analysis examines cutting-edge automation technologies reshaping construction, providing decision-makers with essential insights for strategic implementation. We’ll explore proven solutions, ROI considerations, and practical implementation strategies based on successful case studies from industry pioneers.
Key Technologies Driving Construction Automation
Building Information Modeling (BIM) Integration
Building Information Modeling (BIM) automation represents a transformative advancement in construction project management, seamlessly integrating design, planning, and execution phases into a unified digital workflow. By automating clash detection, quantity takeoffs, and construction sequencing, BIM significantly reduces human error while accelerating project timelines.
Modern BIM platforms now incorporate artificial intelligence to optimize building designs, predict potential construction challenges, and automatically generate detailed construction documentation. This automation enables real-time collaboration among stakeholders, with automated updates reflecting changes across all project dimensions simultaneously.
The integration of BIM with other construction technologies, such as reality capture and digital twin solutions, creates a powerful ecosystem for project monitoring and control. Automated progress tracking, deviation analysis, and performance monitoring provide unprecedented visibility into construction operations, enabling proactive decision-making and risk mitigation.
For construction managers, this translates to improved resource allocation, more accurate cost estimations, and enhanced project coordination. The system’s ability to automatically generate detailed reports and visualizations ensures all stakeholders maintain clear visibility throughout the project lifecycle.
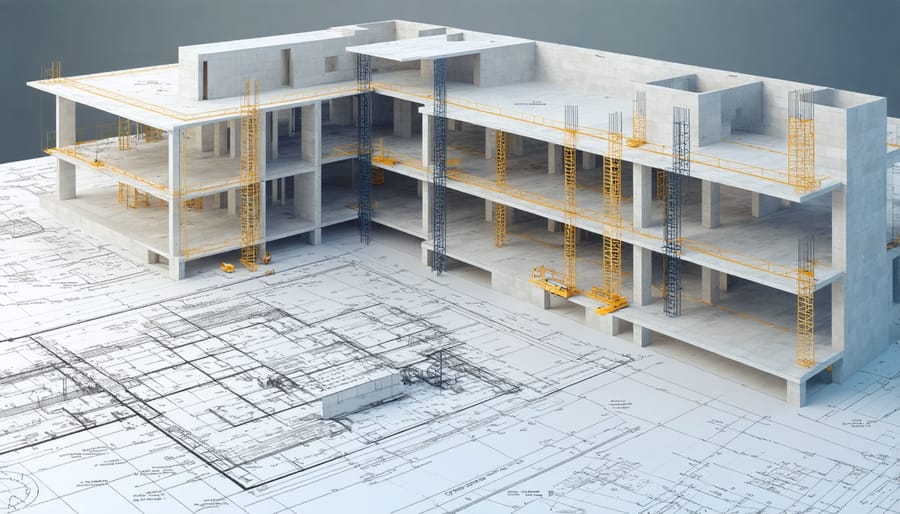
AI and Machine Learning Applications
The implementation of AI in construction management has revolutionized project execution through various practical applications. Predictive analytics algorithms are now being employed to forecast project timelines and potential delays, enabling proactive risk management. Machine learning systems analyze historical project data to optimize resource allocation and improve scheduling accuracy by up to 25%.
Computer vision technology, integrated with AI, monitors job sites in real-time, ensuring worker safety and compliance with regulations. These systems can detect safety violations and equipment misuse, reducing workplace incidents by approximately 30%. Additionally, BIM (Building Information Modeling) platforms enhanced with AI capabilities facilitate automated clash detection and design optimization, saving countless hours in the planning phase.
AI-powered robots and drones are increasingly utilized for site surveys, progress monitoring, and quality control inspections. These autonomous systems can collect and process data with unprecedented accuracy, providing project managers with actionable insights. Natural Language Processing (NLP) algorithms are streamlining documentation processes by automatically generating reports and analyzing contract documents for potential risks or discrepancies.
Robotics and Autonomous Equipment
Robotic systems are revolutionizing construction operations through automated task execution and enhanced precision. Autonomous robots now handle various functions, from bricklaying and concrete finishing to demolition and materials transport. Leading contractors are deploying robotic arms for precise welding and assembly operations, while mobile robots equipped with advanced sensors navigate construction sites to perform inspections and material handling tasks.
Recent innovations include exoskeletons that enhance worker capabilities, reducing physical strain during heavy lifting operations, and collaborative robots (cobots) that work alongside human teams for increased efficiency. Drone systems provide aerial surveying, progress monitoring, and safety inspections, while autonomous construction vehicles perform earthmoving and grading tasks with minimal human intervention.
These robotic solutions not only improve productivity and safety but also address labor shortages by automating repetitive tasks. Construction firms implementing robotics report up to 300% increases in productivity for specific operations, while maintaining higher quality standards and reducing workplace injuries.
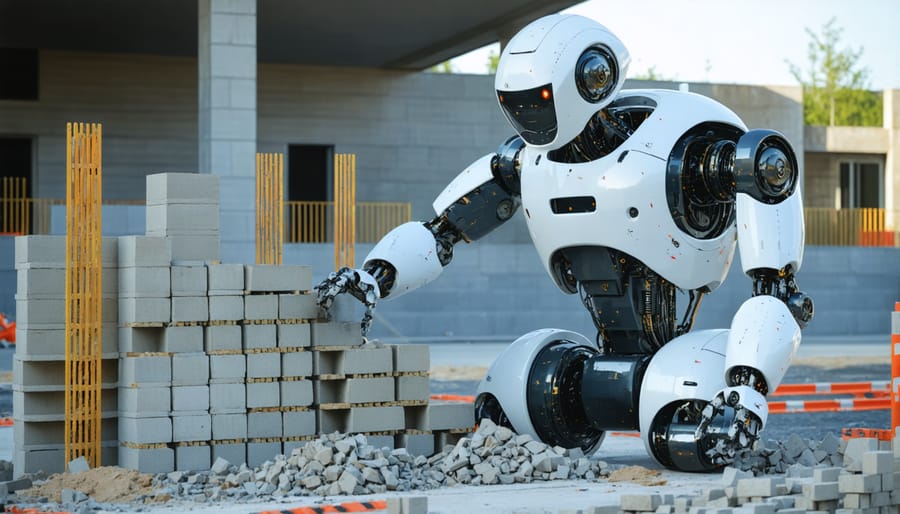
Real-World Implementation Case Studies
Large-Scale Commercial Project Success Story
The Hudson Yards development in New York City stands as a prime example of successful automation implementation in large-scale commercial construction. This $25 billion project utilized an integrated suite of automated systems that revolutionized traditional construction methodologies, resulting in a 30% reduction in overall project timeline and a 25% decrease in labor costs.
Central to the project’s success was the deployment of automated material handling systems, including self-navigating cranes and robotic inventory management solutions. These systems coordinated seamlessly with Building Information Modeling (BIM) software, enabling real-time tracking of construction progress and material deployment across the 28-acre site.
The project team implemented autonomous surveying drones that conducted daily site inspections, generating precise 3D models that were automatically compared against design specifications. This technology identified potential issues before they became costly problems, reducing rework by an estimated 45% compared to traditional methods.
Perhaps most impressive was the installation of prefabricated building components using automated assembly systems. These robots, guided by advanced positioning software, achieved placement accuracy within 2mm tolerance while operating at heights exceeding 1,000 feet. The precision and speed of these systems proved particularly valuable during the construction of the site’s signature structure, 30 Hudson Yards.
The project’s automation strategy extended to quality control, where AI-powered inspection systems monitored concrete curing conditions and structural integrity in real-time. This technological integration not only enhanced safety standards but also contributed to achieving LEED Platinum certification through optimized resource utilization and reduced waste.
The Hudson Yards project demonstrates how strategic implementation of construction automation can deliver substantial benefits in efficiency, safety, and sustainability while maintaining exceptional quality standards.
Infrastructure Project Automation Benefits
A recent case study of the London Crossrail project demonstrates the transformative impact of automation in infrastructure construction. The implementation of automated monitoring systems and robotic construction equipment resulted in a 30% reduction in project timeline and a 25% decrease in labor costs.
The project utilized autonomous surveying drones for progress monitoring and digital twin technology for real-time project visualization. These automated solutions enabled project managers to identify potential issues before they became costly problems, reducing rework by approximately 40%.
Smart sensors deployed throughout the construction site continuously monitored structural integrity, environmental conditions, and equipment performance. This automated data collection and analysis system prevented an estimated 15 major delays by alerting teams to potential structural concerns before they escalated.
The integration of automated material handling systems proved particularly effective, with robotic delivery vehicles and automated storage solutions optimizing logistics operations. This resulted in a 35% improvement in material handling efficiency and a significant reduction in on-site accidents.
Cost analysis revealed that while the initial investment in automation technology was substantial, the project achieved ROI within 18 months. The combination of reduced labor costs, improved efficiency, and decreased error rates contributed to overall cost savings of 20%.
Environmental benefits were also significant, with automated waste management systems reducing construction waste by 45% and smart energy management systems lowering power consumption by 30%. These improvements aligned with sustainability goals while delivering operational cost benefits.
The project’s success has established a blueprint for future infrastructure developments, demonstrating how strategic automation implementation can deliver measurable improvements in efficiency, safety, and cost-effectiveness.
ROI and Performance Metrics
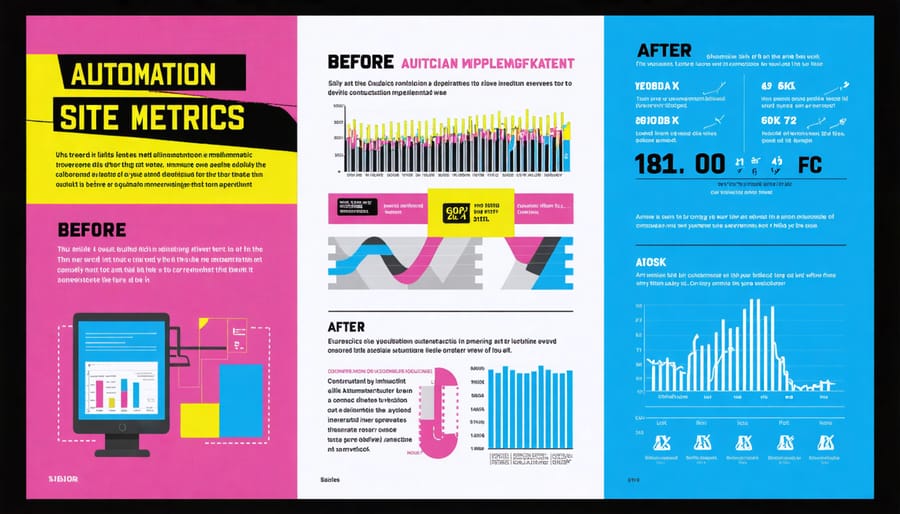
Cost-Benefit Analysis
The implementation of automation technologies in construction requires significant upfront investment, but the long-term financial benefits often justify these costs. Industry data shows that construction companies investing in automation typically achieve ROI within 12-24 months, depending on project scale and technology type.
Initial investments vary significantly: basic robotic systems start at $50,000, while comprehensive automated solutions can exceed $500,000. However, labor cost savings average 20-35% annually, with some projects reporting up to 45% reduction in direct labor expenses. Automated equipment also operates 3-4 times faster than traditional methods, significantly reducing project timelines.
Maintenance costs typically represent 8-12% of the initial investment annually, but this is offset by reduced workplace accidents, with automated sites reporting 73% fewer safety incidents. Insurance premiums often decrease by 15-25% after implementing automated systems.
Productivity gains average 30-40% across various construction tasks, while material waste reduction ranges from 15-25%. Energy efficiency improvements of 20-30% are common with modern automated systems. Quality control automation reduces rework by up to 25%, generating substantial cost savings.
Companies should consider both tangible and intangible benefits: improved project accuracy, enhanced competitive advantage, and better workforce utilization. While smaller construction firms might find the initial investment challenging, leasing options and phased implementation strategies can make automation more accessible, providing scalable solutions for various budget levels.
Productivity and Safety Improvements
Recent industry data reveals that construction automation delivers significant measurable improvements in both productivity and workplace safety. Projects implementing automated systems have reported productivity gains of 30-50% in specific tasks, with some robotic solutions achieving up to 300% faster completion rates compared to traditional methods.
Safety statistics are equally compelling, showing a 40-60% reduction in workplace incidents where construction site monitoring innovations and automated systems are deployed. Automated equipment eliminates human exposure to hazardous environments, particularly in activities like working at heights, handling heavy materials, and operating in confined spaces.
A recent study by the Construction Industry Institute found that projects utilizing automation technologies experienced a 25% decrease in project duration and a 20% reduction in overall costs. Precision-guided equipment reduces material waste by up to 30%, while automated quality control systems catch potential issues before they become costly problems.
Worker fatigue-related incidents have decreased by 45% where automated assistance systems are employed, particularly in repetitive tasks like bricklaying and concrete finishing. Additionally, real-time monitoring and predictive maintenance systems have reduced equipment downtime by 35%, ensuring more consistent project progression and improved resource utilization.
Implementation Strategies and Best Practices
Technology Selection Framework
Selecting the right automation technology for construction projects requires a systematic approach based on several key factors. First, assess your specific project needs and operational challenges to identify areas where automation can provide the most significant impact. Consider factors such as project scale, complexity, available resources, and existing workflows.
Evaluate potential solutions using a three-tier framework: technical feasibility, economic viability, and implementation practicality. Technical feasibility involves analyzing whether the technology aligns with your current infrastructure and can integrate with existing automated project management tools. Economic viability requires calculating both direct costs and long-term ROI, including maintenance and training expenses.
Implementation practicality focuses on your team’s capacity to adopt and maintain the technology. Consider factors such as:
– Required training and skill development
– Integration with existing processes
– Vendor support and maintenance requirements
– Scalability potential
– Regulatory compliance
Prioritize solutions that offer demonstrable benefits in multiple areas, such as safety improvements, productivity gains, and quality enhancement. Consider starting with pilot programs to test effectiveness before full-scale deployment. Regular assessment of technology performance against predetermined metrics ensures optimal selection and utilization of automation solutions.
Change Management and Training
Successful implementation of automation technologies in construction requires a well-planned change management strategy and comprehensive training program. Organizations must address both technical and cultural aspects of the transition to ensure widespread adoption and maximize return on investment.
A phased implementation approach typically yields the best results. Begin by identifying automation champions within the organization who can advocate for new technologies and support their colleagues during the transition. These individuals should receive advanced training and serve as primary points of contact for troubleshooting and support.
Construction companies should develop structured training programs that cater to different skill levels and roles. This includes hands-on workshops for equipment operators, technical training for maintenance staff, and management-level sessions focusing on workflow optimization and project integration. Regular refresher courses and updates on new features help maintain competency and enthusiasm for automated systems.
Clear communication about the benefits and impact of automation is crucial. Address common concerns about job security by emphasizing how automation enhances worker safety and creates opportunities for upskilling. Document success stories and share performance metrics to demonstrate positive outcomes and maintain momentum.
Change resistance can be mitigated through active stakeholder engagement and continuous feedback loops. Regular surveys and team meetings help identify implementation challenges early, allowing for timely adjustments to training programs and support systems. This adaptive approach ensures smooth integration of automation technologies while maintaining workforce morale and productivity.
Construction automation represents a transformative force that continues to reshape the industry landscape. As technologies mature and become more accessible, construction firms that embrace automation stand to gain significant competitive advantages through improved efficiency, safety, and cost-effectiveness. The integration of robotics, AI, and autonomous systems is no longer a future prospect but a present reality that demands attention and strategic planning.
Looking ahead, we can expect further innovations in prefabrication, 3D printing, and autonomous equipment, alongside more sophisticated data analytics and project management solutions. While challenges remain in terms of initial investment costs and workforce adaptation, the trajectory is clear: automation will become increasingly essential for maintaining competitiveness in the construction sector.
Success in this evolving landscape will depend on careful technology selection, comprehensive training programs, and a balanced approach to implementation that considers both immediate needs and long-term objectives. Construction firms that act now to develop their automation capabilities will be best positioned to thrive in tomorrow’s construction industry.