Virtual construction design stands at the forefront of digital transformation in construction, revolutionizing how projects move from concept to completion. By integrating Building Information Modeling (BIM), artificial intelligence, and real-time collaboration platforms, this technology enables construction teams to identify and resolve potential conflicts before breaking ground, reducing rework costs by up to 40% and accelerating project delivery timelines by 20-30%.
Through sophisticated 3D modeling and simulation capabilities, virtual construction design empowers stakeholders to make data-driven decisions during the pre-construction phase, effectively minimizing risk and optimizing resource allocation. Project managers can now visualize complex architectural elements, conduct clash detection analyses, and coordinate multiple trade activities within a virtual environment that mirrors real-world conditions with unprecedented accuracy.
As construction firms increasingly embrace digital solutions to maintain competitive advantage, virtual design and construction (VDC) methodology has evolved from a luxury to a necessity, offering tangible benefits in cost control, schedule optimization, and quality assurance. This technological advancement represents not just a tool, but a fundamental shift in how modern construction projects are conceived, planned, and executed.
The Evolution of Construction Design in the Digital Age
From 2D Drawings to Virtual Reality
The evolution from traditional paper-based construction drawings to virtual reality represents a transformative leap in construction design methodology. What began as simple CAD drawings in the 1980s has progressed through 3D BIM modeling to today’s immersive virtual environments. This transition has revolutionized how construction professionals visualize, plan, and execute projects.
Traditional 2D drawings, while fundamental to construction documentation, often required extensive interpretation and left room for errors in spatial understanding. The shift to three-dimensional visualization tools has dramatically improved comprehension of complex architectural details and building systems integration. Virtual reality takes this a step further by allowing stakeholders to experience spaces before they’re built, enabling real-time design modifications and reducing costly mistakes.
Project teams can now walk through virtual buildings, inspect installations, and identify potential conflicts before breaking ground. This immersive approach has proven particularly valuable for client presentations, team collaboration, and safety training, offering an unprecedented level of interaction with design concepts that was impossible with traditional documentation methods.
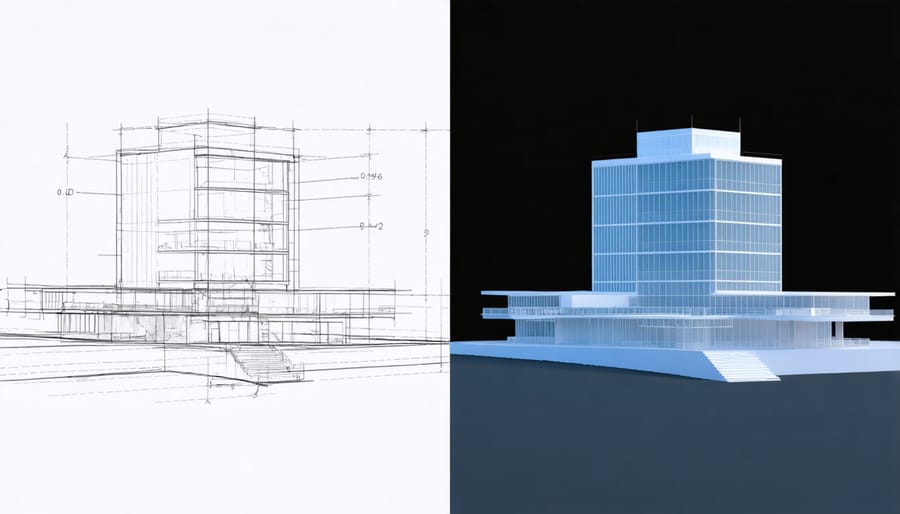
Key Technologies Driving Virtual Design
Building Information Modeling (BIM) stands at the forefront of virtual construction design, enabling teams to create detailed 3D models that integrate crucial project data, from material specifications to cost estimates. This technology serves as the foundation for collaborative design processes, allowing real-time modifications and clash detection before construction begins.
Virtual Reality (VR) and Augmented Reality (AR) have transformed how stakeholders interact with design models. VR enables immersive walkthroughs of unbuilt structures, helping clients and teams visualize spaces and identify potential issues early. AR overlays digital information onto physical spaces, facilitating precise installation and maintenance procedures.
Cloud-based collaboration platforms have become essential, enabling remote teams to work simultaneously on complex projects while maintaining data integrity. Advanced simulation software allows designers to analyze building performance, energy efficiency, and structural integrity within virtual environments.
Parametric design tools have revolutionized the optimization process, automatically generating design variations based on specified parameters and constraints. This capability, combined with artificial intelligence and machine learning algorithms, helps identify optimal solutions for complex design challenges while reducing time and resources required for iteration.
These technologies work in concert to create a comprehensive virtual design ecosystem that enhances accuracy, efficiency, and collaboration throughout the construction lifecycle.
Real-World Applications and Benefits
Clash Detection and Risk Mitigation
Clash detection stands as one of the most powerful advantages of virtual construction design, enabling teams to identify and resolve potential conflicts before they become costly site problems. By creating detailed 3D models that integrate all building systems – structural, mechanical, electrical, and plumbing – teams can detect spatial conflicts and interference issues that might otherwise go unnoticed until construction.
Studies show that early clash detection through virtual design can reduce construction rework by up to 40% and cut overall project costs by 10%. For instance, when multiple systems occupy the same space, such as ductwork intersecting with structural beams, these conflicts are immediately visible in the virtual environment. This allows designers and engineers to make necessary adjustments during the planning phase, rather than dealing with expensive on-site modifications.
Risk mitigation extends beyond clash detection to include constructability analysis, safety planning, and sequence optimization. Virtual design enables teams to simulate construction processes, identifying potential hazards and logistical challenges before breaking ground. Project managers can visualize complex installations, verify clearances, and ensure adequate space for equipment operation and maintenance.
Moreover, virtual design supports collaborative problem-solving by providing a shared platform where all stakeholders can review and resolve issues together. This integrated approach to conflict resolution significantly reduces the likelihood of change orders, delays, and budget overruns while improving project delivery reliability.
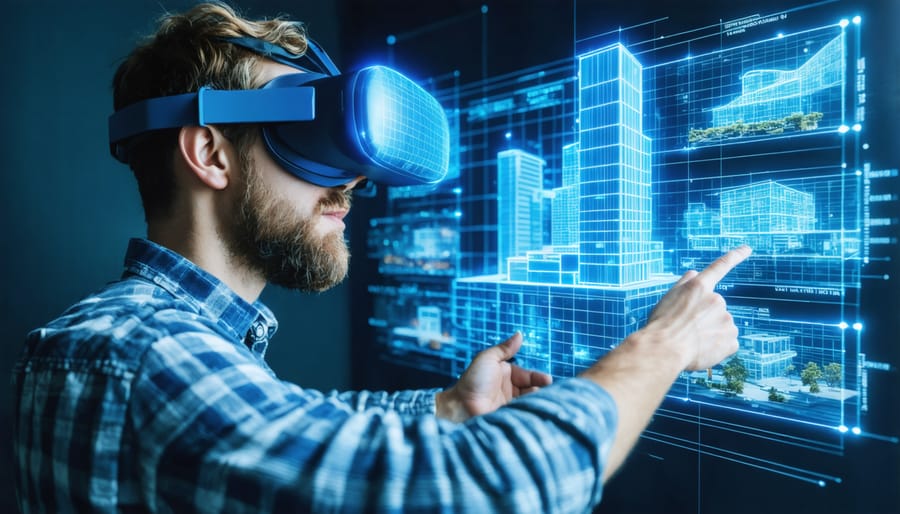
Cost and Time Optimization
Virtual construction design delivers substantial cost savings and time efficiencies throughout the project lifecycle. By identifying and resolving potential conflicts before breaking ground, organizations can reduce expensive on-site modifications and rework by up to 40%. The implementation of digital twins technology further enhances this optimization by enabling real-time monitoring and predictive maintenance.
Recent industry studies indicate that virtual design implementation typically results in a 20-30% reduction in overall project duration and a 15-25% decrease in total project costs. These savings stem from improved coordination among stakeholders, streamlined workflows, and reduced material waste. The ability to perform accurate quantity takeoffs and cost estimates during the early design phases helps teams maintain better budget control and make informed decisions.
Virtual construction design also optimizes resource allocation by enabling precise scheduling and sequencing of construction activities. Project managers can simulate different scenarios to determine the most efficient construction approach, resulting in optimal crew sizing and equipment utilization. This proactive planning reduces idle time and associated costs while ensuring smooth project progression.
Furthermore, the technology’s clash detection capabilities prevent costly interference issues between building systems, potentially saving millions in remediation costs on large-scale projects. The return on investment is particularly evident in complex projects where traditional 2D coordination would be time-consuming and prone to errors.
Collaborative Design and Stakeholder Communication
Virtual construction design revolutionizes stakeholder collaboration by creating a unified digital environment where all project participants can interact with the building model in real-time. This collaborative approach enables architects, engineers, contractors, and clients to work together seamlessly, regardless of their physical location, significantly reducing communication barriers and potential misunderstandings.
The platform facilitates regular design review sessions where stakeholders can virtually walk through the proposed structure, making informed decisions and suggesting modifications before construction begins. This proactive approach to design coordination has proven to reduce costly changes during construction by up to 40% according to recent industry studies.
Client engagement is particularly enhanced through immersive visualization capabilities. Rather than relying on traditional 2D drawings or physical models, clients can experience their future space through virtual reality walkthroughs, leading to better understanding and more confident decision-making. Project teams can easily demonstrate design alternatives, material options, and spatial relationships, ensuring alignment with client expectations throughout the development process.
Furthermore, the technology enables real-time clash detection and resolution, allowing different disciplines to coordinate their work effectively. MEP engineers can collaborate with structural designers to resolve conflicts before they become on-site issues, while architects can ensure their design intent is preserved throughout the coordination process. This integrated approach to design review and stakeholder communication has become instrumental in delivering projects on time and within budget while maintaining high quality standards.
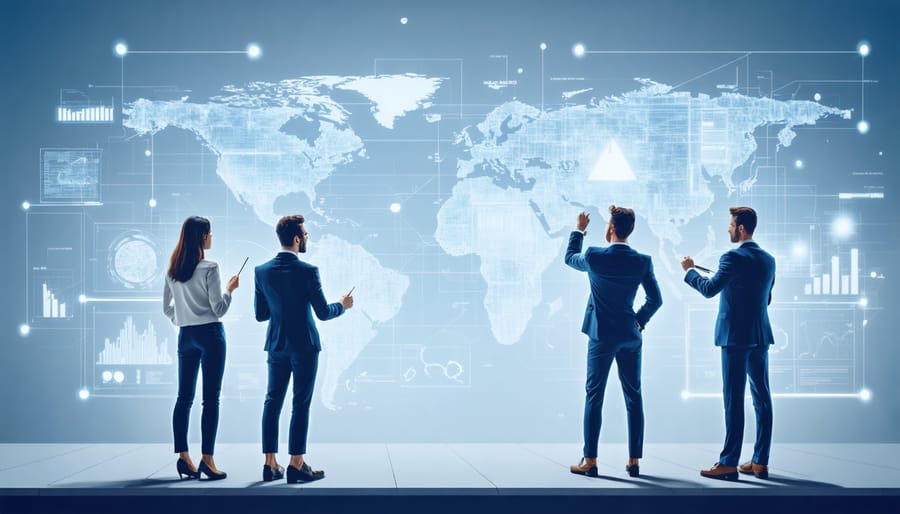
Implementation Strategies and Best Practices
Technology Integration Framework
Implementing virtual design systems in construction requires a systematic approach across multiple organizational levels. The process typically begins with a thorough assessment of existing workflows and technological infrastructure. Organizations must first establish clear objectives and identify key stakeholders who will champion the integration process.
The next crucial step involves selecting appropriate software solutions that align with project requirements and organizational capabilities. This includes Building Information Modeling (BIM) platforms, visualization tools, and collaboration software. Integration should be phased, starting with pilot projects to test functionality and identify potential challenges.
Training programs must be developed and implemented to ensure team members are proficient in using the new technologies. This includes both technical training on specific software platforms and process training to understand new workflows and collaboration methods.
Data management protocols need to be established, including standardization of file formats, naming conventions, and version control systems. Organizations should also implement quality control measures to maintain consistency across virtual design deliverables.
The framework must address cybersecurity concerns and establish backup procedures to protect sensitive project data. Regular system audits and updates ensure optimal performance and compatibility with evolving industry standards.
Finally, organizations should establish metrics to measure the effectiveness of their virtual design implementation, including key performance indicators like reduced rework, improved coordination, and accelerated project timelines. This data drives continuous improvement and helps justify further technology investments.
Team Training and Adaptation
Successful implementation of virtual construction design requires a comprehensive approach to team training and organizational adaptation. Construction firms must invest in structured learning programs that address both technical skills and mindset shifts required for digital transformation.
Training typically begins with foundational courses in Building Information Modeling (BIM) software and virtual design tools, progressing to advanced applications specific to different roles. Project managers need training in digital collaboration and virtual coordination, while designers and engineers require deeper technical expertise in modeling and analysis tools.
Change management plays a crucial role in adoption success. Organizations should identify champions within each department who can mentor colleagues and demonstrate the practical benefits of virtual design tools. Regular workshops and hands-on sessions help team members gain confidence while working with new technologies.
Cross-functional training is essential, as virtual construction design requires seamless collaboration between various disciplines. Teams must understand not only their specific tools but also how their work impacts other stakeholders in the digital workflow.
Performance monitoring and continuous feedback mechanisms help identify gaps in knowledge and skills, allowing organizations to adjust training programs accordingly. Many successful firms implement mentorship programs and create internal knowledge bases to support ongoing learning.
The investment in training typically yields returns through improved project outcomes, reduced errors, and increased team efficiency. Organizations should view team development as a continuous process rather than a one-time initiative.
Future Trends and Innovations
The landscape of virtual construction design is rapidly evolving, with several emerging construction technologies poised to revolutionize the industry. Artificial Intelligence and Machine Learning are becoming increasingly sophisticated, enabling more accurate predictive modeling and automated design optimization. These technologies will enhance decision-making processes by analyzing vast amounts of historical project data to inform future design choices.
Extended Reality (XR) technologies, including advanced Virtual Reality (VR) and Augmented Reality (AR), are expected to become standard tools in construction design workflows. Next-generation VR headsets will offer improved resolution and haptic feedback, allowing designers and stakeholders to physically interact with virtual models in unprecedented ways. Mixed Reality (MR) applications will enable real-time overlay of digital information onto physical construction sites, bridging the gap between virtual design and actual construction.
Digital twins are evolving beyond simple 3D representations to become dynamic, real-time models that continuously update based on sensor data and IoT integration. These advanced digital twins will enable predictive maintenance, optimize building performance, and facilitate better lifecycle management of constructed assets.
Cloud-based collaboration platforms are becoming more sophisticated, incorporating blockchain technology for improved security and transparency in design documentation. These platforms will enable seamless integration of various design tools and better version control across multiple stakeholders.
Generative design powered by AI is expected to revolutionize the conceptual design phase, automatically producing multiple design options based on specified parameters and constraints. This technology will significantly reduce design time while optimizing for factors such as cost, sustainability, and constructability.
The integration of robotics and automation in construction will influence virtual design practices, requiring new considerations in the design phase to accommodate automated construction methods. This will lead to the development of specialized design tools that consider robotic construction capabilities from the outset.
Virtual construction design represents a transformative shift in how we approach building projects, offering unprecedented opportunities for efficiency, accuracy, and collaboration. As demonstrated throughout this article, the integration of virtual design and construction (VDC) technologies has become not just an option, but a necessity for staying competitive in today’s construction landscape.
The benefits are clear and measurable: reduced errors and rework, improved project visualization, enhanced stakeholder communication, and significant cost savings across the project lifecycle. From small residential developments to complex commercial structures, VDC tools have proven their value across diverse project types and scales.
For construction professionals considering the adoption of virtual design technologies, the initial investment in software, training, and process changes should be viewed as a strategic decision that will yield substantial returns. The success stories and case studies presented here demonstrate that organizations embracing these digital tools consistently outperform those relying on traditional methods.
Looking ahead, the continued evolution of virtual construction design technologies, including artificial intelligence, machine learning, and enhanced reality capabilities, will further revolutionize the construction industry. To remain competitive and deliver superior results, construction professionals must embrace these innovations and integrate them into their workflows.
The time to act is now. By implementing virtual construction design solutions today, organizations position themselves at the forefront of industry innovation, ready to meet the challenges and opportunities of tomorrow’s construction landscape.