Discover the world of prefabricated homes, where innovative construction methods merge with sleek design to create efficient, affordable living spaces. From modular and panelized systems to shipping container and tiny homes, prefab construction offers a range of benefits, including faster build times, reduced waste, and improved quality control. As the housing industry evolves, prefabricated homes are emerging as a compelling solution for homeowners, developers, and architects seeking to balance cost, sustainability, and style. In this article, we’ll explore the main types of prefabricated homes, their unique features, and the advantages they offer, providing valuable insights for anyone considering this forward-thinking approach to residential construction.
Modular Homes
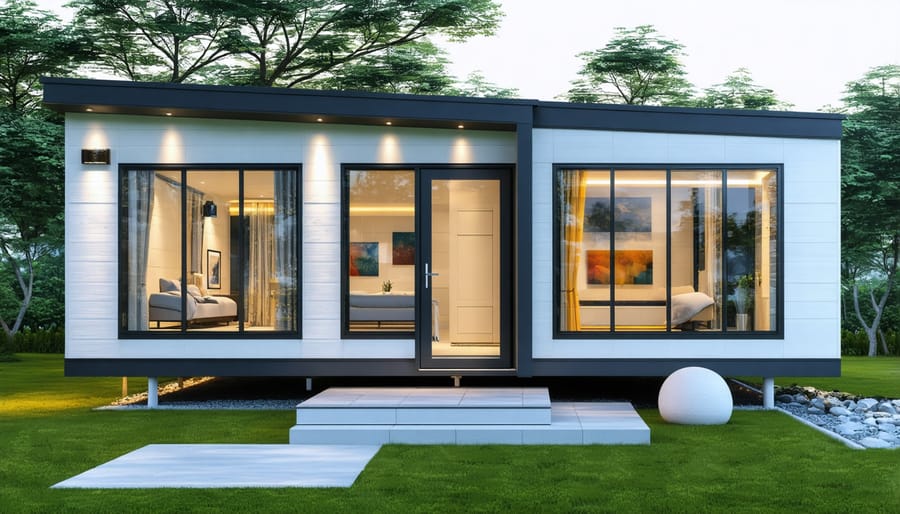
How Modular Homes are Built
The construction process for modular homes combines precision factory assembly with efficient on-site installation. In the factory, skilled workers construct individual modules using advanced machinery and quality control measures. Each module, built to meet or exceed local building codes, includes complete electrical, plumbing, and HVAC systems. The controlled factory environment minimizes waste, ensures consistent quality, and allows for simultaneous construction of multiple modules. Once complete, the modules are transported to the building site, where a crane carefully places them onto a pre-prepared foundation. Professional crews then seamlessly connect the modular homes together, complete the utility connections, and perform any necessary finishing work. This streamlined process significantly reduces on-site construction time compared to traditional building methods, minimizing disruption to the surrounding area and allowing for faster project completion. The factory-built nature of modular homes also enables better quality control, improved energy efficiency, and reduced exposure to weather-related delays or damage during construction.
Benefits of Modular Construction
Modular construction offers numerous benefits for construction professionals and project stakeholders. One of the most significant advantages is the potential for substantial time and cost savings. By manufacturing building components in a controlled factory environment, modular construction minimizes on-site labor and reduces the impact of weather delays, resulting in shorter project timelines and lower overall costs. Additionally, the factory setting allows for enhanced quality control, as each module undergoes rigorous inspections and testing to ensure compliance with building codes and quality standards.
Moreover, modular construction provides greater flexibility and customization options compared to traditional construction methods. Designers and engineers can create custom floor plans and layouts to meet specific project requirements, while still leveraging the efficiency of prefabricated components. This adaptability enables modular construction to cater to a wide range of applications, from residential homes to commercial buildings and beyond.
Case studies demonstrate the tangible benefits of modular construction. For example, a recent project in the United Kingdom utilized modular techniques to construct a 25-story student housing complex in just 12 months, reducing the construction timeline by 50% compared to traditional methods. This not only resulted in significant cost savings but also allowed the facility to open in time for the academic year, generating revenue for the owners.
Panelized Homes
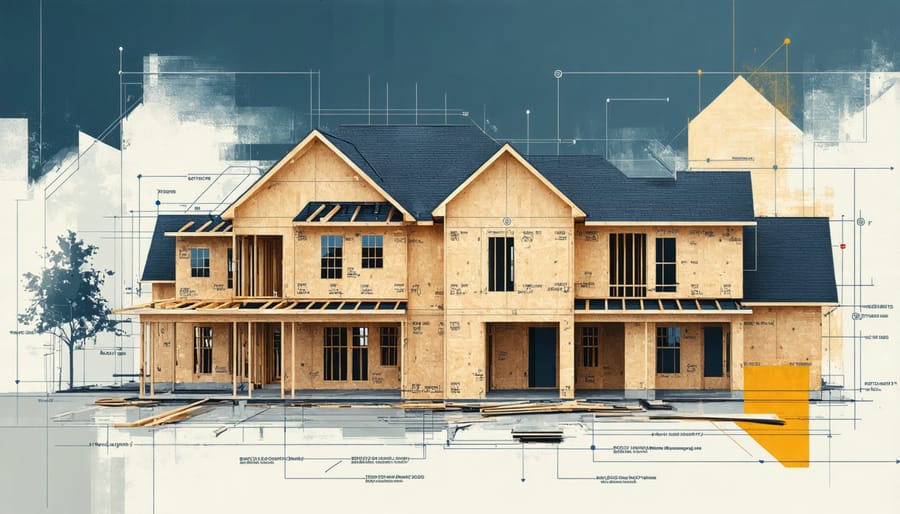
Types of Panelized Systems
Panelized systems are a popular type of prefabricated construction, offering flexibility and efficiency. Structural Insulated Panels (SIPs) combine insulation and structural framing, providing superior energy efficiency and quick assembly. Open-frame panels, consisting of studs, sheathing, and sometimes utilities, allow for customization and on-site finishing. Closed-frame panels include pre-installed insulation, wiring, and plumbing, minimizing on-site work. Concrete panels offer durability and thermal mass, ideal for foundations and walls. Timber frame panels showcase exposed wood beams and trusses, adding rustic charm. Steel frame panels provide strength and fire resistance for commercial projects. Choosing the right panel system depends on factors such as climate, building codes, aesthetic preferences, and budget. Panelized construction streamlines the building process, reducing waste and labor costs while maintaining design flexibility. With careful planning and coordination, panelized systems deliver high-quality, efficient, and customizable prefabricated homes tailored to specific project requirements.
Panelized vs. Stick-Built Homes
Panelized homes are constructed using factory-built wall panels, while stick-built homes are built entirely on-site using traditional methods. Panelized construction offers several advantages over stick-built, including faster build times, reduced labor costs, and improved quality control. Factory-controlled environments minimize material waste and ensure consistent panel quality. On-site assembly is streamlined, reducing construction time by up to 60%. Panelized homes also offer superior energy efficiency due to tighter seals and higher-grade insulation, resulting in long-term energy efficiency benefits. However, stick-built homes allow for greater customization and design flexibility. Ultimately, the choice between panelized and stick-built depends on project priorities, such as budget, timeline, and desired performance. Panelized construction is ideal for projects prioritizing speed, cost-effectiveness, and energy efficiency, while stick-built may be preferred for highly customized designs or smaller-scale projects.
Shipping Container Homes
Designing with Containers
Architects are pushing the boundaries of container home design, transforming these sturdy steel boxes into stunning, livable spaces. One notable example is the Joshua Tree Residence by Whitaker Studio, which features a starburst-like arrangement of containers, creating a unique, eco-friendly desert retreat. Another innovative project is the Quadrum Ski & Yoga Resort in the Caucasus Mountains, where stacked containers provide guests with luxurious, minimalist accommodations that blend seamlessly with the rugged landscape.
Architects are also experimenting with container stacking and arrangement to optimize space and functionality. The Caterpillar House by Sebastián Irarrázaval Arquitectos showcases a modular design with strategically placed containers that create a spacious, light-filled interior. Cutting-edge projects like these demonstrate the versatility of containers as a building material, inspiring architects to think outside the box and craft remarkable, sustainable living spaces that redefine the concept of home.
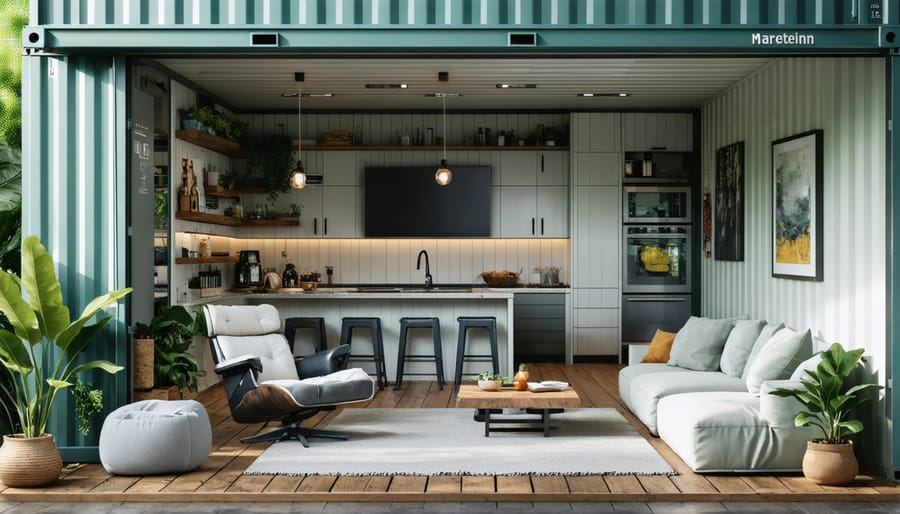
Challenges and Considerations
When considering prefabricated homes, it’s essential to be aware of potential challenges and regulations. Zoning laws and building codes may vary by location, impacting the feasibility of certain prefab designs. Obtaining necessary permits and approvals can be complex, requiring careful navigation of local requirements. Transportation logistics and site access are also critical factors, as prefab components must be safely delivered and assembled on-site. Additionally, while prefab construction offers many benefits, it may have limitations in terms of customization and design flexibility compared to traditional builds. Working closely with experienced prefab manufacturers and local authorities is crucial to address these challenges effectively. By carefully considering regulations, logistics, and design constraints early in the planning process, construction professionals can successfully integrate prefabricated homes into their projects while minimizing potential obstacles.
Kit Homes
Kit Home Providers
Several notable companies offer comprehensive kit home packages, providing customers with a streamlined and efficient approach to building their dream homes. Linwood Homes, a well-established kit home provider, offers a wide range of customizable designs and high-quality materials, ensuring that each home meets the unique needs and preferences of its owners. Another prominent player in the industry, Shelter-Kit, prides itself on its user-friendly, pre-cut, and pre-drilled kit homes that can be assembled by the homeowner or a local contractor, making the process more accessible and cost-effective. Additionally, Bensonwood Homes combines the benefits of kit homes with the expertise of experienced craftsmen, offering a balance between prefabrication and on-site customization. These kit home providers, along with many others in the industry, offer a compelling alternative to traditional home construction, empowering individuals to take a more active role in the building process while benefiting from the efficiency and quality of prefabricated components.
Assembly and Customization
Prefabricated homes, such as kit homes, typically arrive on-site in pre-cut, pre-measured sections that are ready for assembly. The construction process involves following a set of detailed instructions to piece together the various components, which may include wall panels, roof trusses, and floor systems. Skilled labor is often required to ensure proper assembly and adherence to local building codes. One of the significant advantages of prefabricated homes is the ability to customize the design to suit individual preferences and site requirements. Many manufacturers offer a range of floor plans, materials, and finishes, allowing for personalization within the framework of the prefabricated system. This flexibility enables construction professionals to create unique, tailored housing solutions while still benefiting from the efficiency and cost-effectiveness of prefabrication.
Tiny Prefab Homes
The tiny home movement has gained significant traction in recent years, with many individuals seeking to downsize and simplify their living spaces. Prefabrication has played a crucial role in making this trend more accessible and affordable. Tiny prefab homes, typically ranging from 100 to 400 square feet, offer a compact and efficient housing solutions that can be customized to meet various needs and preferences.
These diminutive dwellings are built off-site in a controlled factory environment, ensuring high quality and precision. The modular construction process allows for faster completion times and reduced waste compared to traditional on-site builds. Tiny prefab homes often incorporate multi-functional spaces, clever storage solutions, and energy-efficient features to maximize comfort and sustainability within a limited footprint.
One of the primary advantages of tiny prefab homes is their affordability. By reducing square footage and streamlining the construction process, these homes can be significantly more cost-effective than larger, traditionally built houses. Additionally, their small size and prefabricated nature make them ideal for remote locations, as they can be easily transported and assembled on-site with minimal disturbance to the surrounding environment. Remote construction could significantly benefit from the adaptability of tiny prefab homes.
As the demand for sustainable and minimalist living continues to grow, tiny prefab homes are poised to play an increasingly important role in the housing market. Their combination of efficiency, affordability, and customization options make them an attractive choice for those looking to embrace a simpler, more intentional lifestyle.
Conclusion
Prefabricated homes offer a compelling solution for the construction industry, providing numerous benefits such as faster build times, reduced costs, improved quality control, and enhanced sustainability. The various types of prefab homes, including modular, panelized, and shipping container homes, cater to a wide range of project requirements and design preferences. As the demand for efficient and eco-friendly construction methods continues to grow, prefab homes are poised to play an increasingly significant role in shaping the future of the industry.
The adoption of prefabricated construction techniques not only streamlines the building process but also opens up new possibilities for innovative designs and customization. With the potential to revolutionize the way we approach residential and commercial construction, prefab homes represent a promising avenue for industry professionals to explore and leverage in their projects. By embracing the benefits and versatility of prefabricated construction, the industry can work towards creating more sustainable, affordable, and high-quality housing solutions that meet the evolving needs of modern society.