Optimize procurement processes by leveraging supplier relationships, consolidating orders, and negotiating bulk discounts to reduce costs and ensure timely material availability. Implement a robust inventory management system that utilizes real-time tracking, demand forecasting, and just-in-time delivery to minimize carrying costs and prevent stockouts. Streamline logistics operations through strategic warehouse placement, efficient transportation routing, and the use of advanced technologies like RFID and GPS to enhance visibility and reduce lead times. Develop a comprehensive risk mitigation plan that identifies potential supply chain disruptions, establishes contingency measures, and fosters collaboration with key stakeholders to ensure business continuity and minimize the impact of unforeseen events.
Develop a Centralized Procurement Process
Leverage Technology for Procurement
Leveraging technology in construction procurement can significantly streamline processes, improve visibility, and enable data-driven decision making. Procurement software automates many manual tasks, such as request for proposal (RFP) creation, bid analysis, and contract management. This automation not only saves time but also reduces the risk of human error. Cloud-based procurement platforms provide real-time visibility into the entire procurement lifecycle, from requisition to payment. This transparency allows stakeholders to track the status of orders, identify bottlenecks, and make informed decisions to optimize the process. Advanced analytics capabilities within procurement software enable organizations to harness the power of data. By analyzing historical spending patterns, market trends, and supplier performance metrics, companies can identify opportunities for cost savings, negotiate better contracts, and mitigate supply chain risks. Predictive analytics can even help forecast future demand and optimize inventory levels. Integration with other enterprise systems, such as ERP and project management software, ensures a seamless flow of information and eliminates data silos. This holistic view of procurement activities enables better collaboration among teams and more strategic decision making. As the construction industry continues to evolve, embracing digital procurement solutions will be critical for staying competitive, driving efficiency, and achieving long-term success.
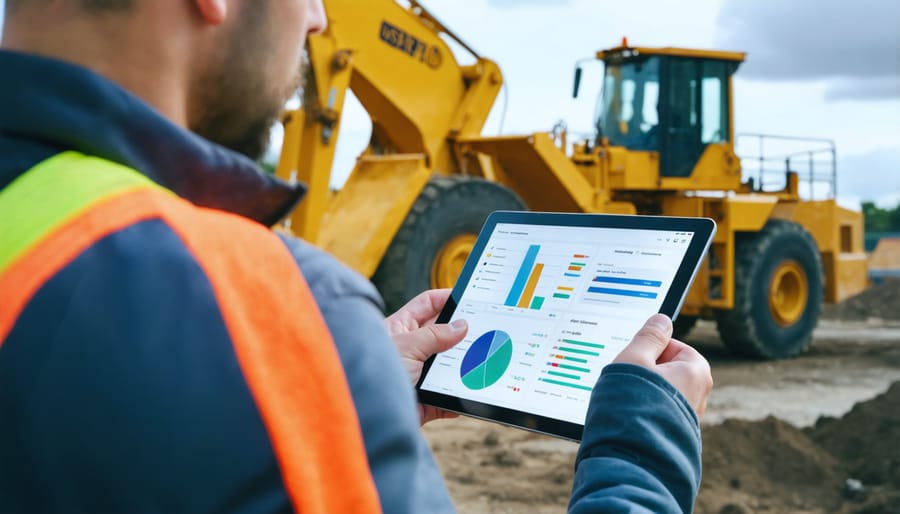
Build Strategic Supplier Relationships
Building strong, strategic relationships with key suppliers is essential for effective logistics and supply chain management in the construction industry. By cultivating long-term partnerships, companies can secure favorable terms, ensure timely deliveries, and maintain a competitive edge. To achieve this, focus on open communication, transparency, and mutual trust. Regularly engage with suppliers to discuss performance expectations, potential improvements, and shared goals. Collaborate on forecasting and planning to align supply with demand, minimizing disruptions and optimizing inventory levels. Consider implementing supplier scorecards to track and evaluate performance against agreed-upon metrics, providing a basis for continuous improvement. Invest in technology solutions that facilitate seamless data sharing and real-time visibility across the supply chain, enabling proactive decision-making and risk mitigation. By treating suppliers as valuable partners and working together to streamline processes, construction companies can build resilient, agile supply chains that drive long-term success in an increasingly competitive market.
Optimize Inventory Management
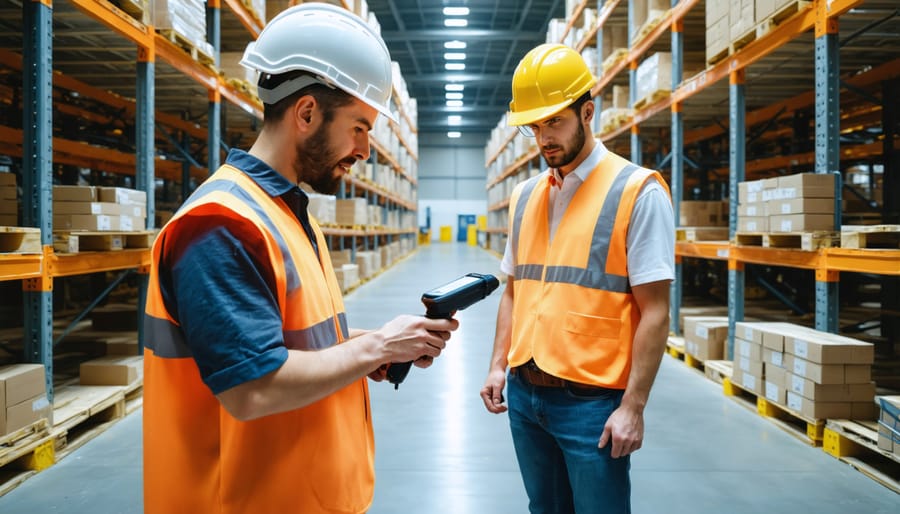
Implement a Robust Tracking System
Implementing a robust tracking system is crucial for effective logistics materials and supply chain management in the construction industry. Real-time inventory tracking enables informed decision-making by providing accurate, up-to-date information on the location and quantity of materials at any given time. This visibility allows construction professionals to optimize stock levels, prevent shortages, and reduce waste. To achieve this level of tracking, consider investing in barcode or Radio Frequency Identification (RFID) systems. These technologies streamline data capture, minimize manual errors, and provide instant updates as materials move through the supply chain. By integrating these systems with your inventory management software, you can gain a comprehensive view of your materials, from procurement to installation on the job site. This real-time data empowers you to make proactive adjustments, ensuring that the right materials are available when and where they are needed. Moreover, a robust tracking system enhances collaboration between stakeholders, as everyone has access to the same reliable information. By implementing these advanced tracking solutions, construction companies can significantly improve their logistics efficiency, reduce costs, and ultimately deliver projects on time and within budget.
Analyze Inventory Data Regularly
In today’s fast-paced construction industry, effective inventory management is crucial for maintaining project timelines and controlling costs. By regularly analyzing inventory data, construction firms can gain valuable insights into their supply chain performance and make data-driven adjustments to optimize stock levels.
Key performance indicators (KPIs) such as inventory turnover, stock accuracy, and days of supply should be closely monitored to identify trends and potential issues. By leveraging advanced analytics tools and real-time data, companies can quickly detect anomalies, forecast demand, and adjust inventory levels accordingly.
Regular data analysis also helps construction firms identify slow-moving or obsolete stock, allowing them to take proactive measures to reduce waste and free up working capital. By continuously monitoring inventory KPIs and making informed decisions based on data-driven insights, construction companies can streamline their supply chain, reduce carrying costs, and improve overall operational efficiency.
Streamline Logistics Operations
Streamlining logistics operations is crucial for optimizing efficiency and reducing costs in construction materials management. One effective strategy is cross-docking, which involves transferring materials directly from inbound to outbound vehicles, bypassing storage. This technique minimizes handling and storage times, leading to faster deliveries and reduced inventory costs.
Transportation route optimization is another key aspect of efficient logistics. By utilizing advanced software and data analytics, construction companies can determine the most cost-effective and time-efficient routes for material deliveries. This not only saves on fuel costs but also ensures that materials arrive at the job site on time, preventing delays.
Efficient job site layout is equally important for streamlining logistics operations. By strategically placing storage areas, unloading zones, and equipment, construction managers can minimize the time and effort required to move materials around the site. This reduces the risk of damage to materials and enhances overall productivity.
Implementing just-in-time (JIT) delivery systems can further optimize logistics by ensuring that materials arrive at the job site precisely when they are needed. This approach reduces the need for on-site storage, minimizes the risk of damage or theft, and helps maintain a clutter-free work environment.
To effectively streamline logistics operations, it is essential to have a robust supply chain risk management plan in place. By identifying potential supply chain risks and developing contingency plans, construction companies can mitigate the impact of disruptions and ensure a smooth flow of materials.
Collaboration and communication among all stakeholders, including suppliers, transporters, and on-site personnel, are vital for the success of streamlined logistics operations. By fostering open lines of communication and using digital tools to share real-time information, construction companies can ensure that everyone is working towards the same goal of efficiency and cost-effectiveness.
Prioritize Supply Chain Risk Management
In today’s complex and interconnected global supply chains, effective risk management is more critical than ever for construction projects. Identifying, assessing, and mitigating potential risks can help prevent costly disruptions, delays, and material shortages. Common supply chain risks include supplier failures, transportation issues, geopolitical events, natural disasters, and quality control problems.
To manage these risks, construction firms should take a proactive approach. This begins with conducting a thorough risk assessment to identify vulnerabilities in the supply chain. Strategies such as diversifying suppliers, establishing backup plans, and building inventory buffers can help mitigate the impact of potential disruptions. For example, sourcing materials from multiple suppliers in different geographic regions can reduce the risk of a single point of failure.
Effective communication and collaboration with suppliers are also essential for risk management. By fostering strong relationships and sharing information, construction firms can better anticipate and respond to potential issues. This may involve implementing supply chain visibility tools to track materials in real-time and detect early warning signs of problems.
Another key strategy is to prioritize risk management in contracts and agreements with suppliers. This can include provisions for performance metrics, quality standards, and contingency plans. By setting clear expectations and holding suppliers accountable, construction firms can reduce the likelihood of disruptions and ensure a more reliable flow of materials.
Ultimately, effective supply chain risk management requires a continuous, proactive approach. By staying vigilant, adapting to changing conditions, and working closely with suppliers, construction firms can build more resilient and reliable supply chains to support their projects.
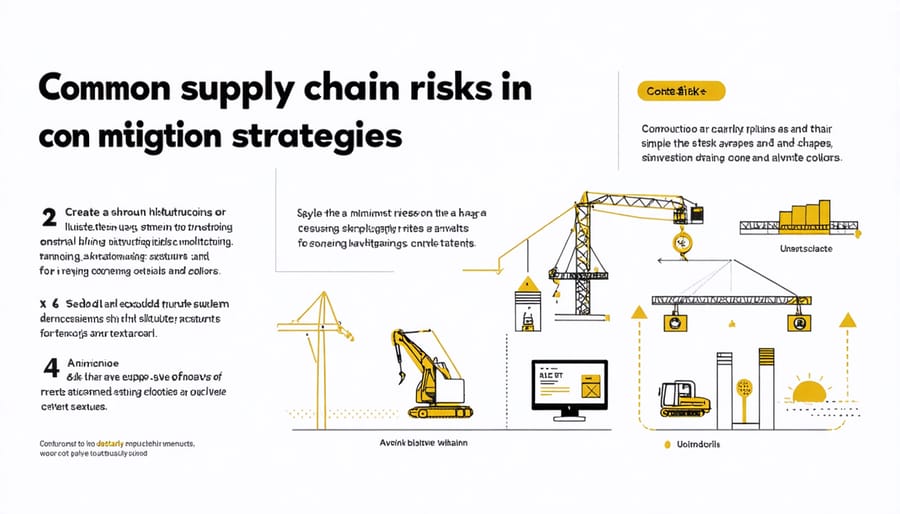
Conclusion
In conclusion, optimizing logistics and supply chain management is critical for construction firms to remain competitive, reduce costs, and deliver projects on time. By implementing strategic procurement practices, leveraging technology for inventory management, streamlining logistics operations, and proactively mitigating risks, construction companies can significantly improve their bottom line. The benefits of these strategies are clear: reduced material waste, improved cash flow, increased productivity, and enhanced customer satisfaction. Construction professionals who prioritize logistics efficiency will be well-positioned to navigate the challenges of the industry and seize new opportunities for growth. The time to act is now – by taking steps to optimize your logistics and supply chain processes, you can set your firm apart from the competition and lay the foundation for long-term success. Whether you’re a seasoned industry veteran or just starting out, embracing these proven strategies is essential for thriving in today’s fast-paced, ever-evolving construction landscape. So don’t wait – start implementing these techniques today and unlock the full potential of your construction business.