Construction types form the backbone of modern building regulations, directly impacting design decisions, safety standards, and project costs across the architectural landscape. The International Building Code (IBC) classifies buildings into five distinct construction types based on their fire-resistance ratings and building materials: Type I through Type V, progressing from most to least fire-resistant. These classifications determine everything from maximum allowable heights and areas to the specific materials permitted in structural components.
For construction professionals and architects, understanding these classifications is crucial for regulatory compliance and project planning. Each type presents unique advantages and limitations, influencing material selection, cost considerations, and building performance characteristics. Whether designing a high-rise commercial building requiring Type I construction or planning a residential project under Type V specifications, these classifications serve as the fundamental framework for ensuring structural integrity and occupant safety.
This comprehensive guide examines each construction type’s technical requirements, practical applications, and critical considerations for modern building projects.
Type I: Fire-Resistant Construction
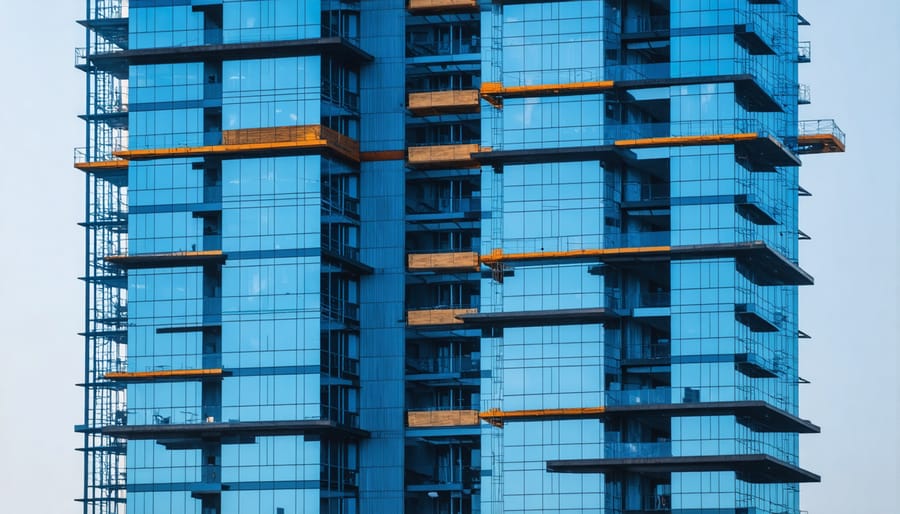
Materials and Requirements
Each construction type is defined by specific material requirements and structural limitations established by the International Building Code (IBC). Type I construction mandates the use of noncombustible materials, primarily steel and concrete, with strict fire-resistance ratings for structural elements. Type II also requires noncombustible materials but with lower fire-resistance requirements than Type I.
Type III construction permits exterior walls to be constructed with noncombustible materials while allowing combustible materials for interior elements. The exterior walls must maintain a two-hour fire-resistance rating, with reduced requirements for interior components.
Type IV, or heavy timber construction, requires exterior walls to be noncombustible materials while utilizing dimensional lumber meeting minimum size requirements for structural members. Columns must be at least 8×8 inches, beams must be 6×10 inches or larger, and floors must be constructed of 4-inch nominal wood decking.
Type V allows the use of combustible materials throughout the structure, with two subcategories: V-A requiring one-hour fire-resistance-rated construction and V-B having no fire-resistance requirements. All types must comply with height and area limitations based on occupancy classification and presence of fire suppression systems.
Applications and Limitations
Type I construction is predominantly required for high-rise buildings, hospitals, and other structures where occupant safety is paramount. These buildings must adhere to stringent building safety regulations due to their size, occupancy levels, and critical functions. Common applications include healthcare facilities, large assembly buildings, high-occupancy structures exceeding 75 feet in height, and facilities storing hazardous materials.
The primary advantage of Type I construction lies in its superior fire resistance and structural integrity. However, these benefits come with significant cost implications due to the extensive use of non-combustible materials and specialized construction techniques. The installation of comprehensive fire suppression systems and multiple means of egress also adds to the overall project expense.
While Type I construction offers the highest level of building safety, its limitations include longer construction timelines, higher material costs, and complex design requirements. The extensive use of steel and concrete necessitates careful planning for thermal expansion and contraction, and the building’s weight requires robust foundation systems. These factors make Type I construction less practical for smaller projects where such stringent safety measures may not be necessary.
Type II: Non-Combustible Construction
Material Specifications
Each construction type requires specific materials that meet stringent code requirements and performance standards. Type I construction predominantly uses noncombustible materials, including steel, concrete, and masonry, with a minimum 3-hour fire rating for structural elements. Type II similarly employs noncombustible materials but with reduced fire-resistance requirements, typically 1-2 hours.
Type III construction features exterior walls made of noncombustible materials while allowing combustible materials for interior elements. The exterior walls must maintain a 2-hour fire rating, while interior structural members require a 1-hour rating. Type IV, or heavy timber construction, utilizes dimensional lumber meeting minimum size requirements: 8×8 inches for columns, 6×10 inches for beams, and 4-inch thick flooring.
Type V construction permits the use of any code-approved materials, including wood frame construction. While being the least restrictive, materials must still meet specific requirements for structural integrity and fire resistance. All material specifications must comply with ASTM standards and local building codes, with proper documentation of fire-resistance ratings and structural performance characteristics.
Common Applications
Each construction type serves distinct building purposes based on occupancy requirements, budget constraints, and safety considerations. Type I construction, commonly used for high-rise buildings, hospitals, and large commercial complexes, provides maximum fire resistance for structures exceeding 75 feet in height. Type II construction typically appears in schools, retail centers, and mid-sized office buildings where non-combustible materials are essential but maximum fire ratings aren’t required.
Type III construction finds extensive application in mixed-use developments, apartments, and small commercial buildings, particularly in urban settings where exterior fire walls are crucial. Type IV (Heavy Timber) construction, while historically used in warehouses and factories, has gained renewed popularity in modern architectural designs for exposed wood aesthetic in offices and residential buildings.
Type V construction, the most economical option, dominates residential construction, particularly in single-family homes, small apartment buildings, and light commercial structures under three stories. This type also serves well for temporary structures and smaller retail establishments where building costs need careful management while maintaining safety standards.
Type III: Ordinary Construction
Exterior Wall Requirements
Exterior wall requirements vary significantly across the five construction types, with fire resistance ratings being a crucial determining factor. Type I and Type II buildings demand the highest level of protection, requiring non-combustible materials and fire-resistance ratings ranging from 2 to 3 hours. Type III construction permits exterior walls constructed of non-combustible materials or fire-retardant-treated wood, with required fire-resistance ratings typically between 1 and 2 hours.
In Type IV (heavy timber) construction, exterior walls must be non-combustible or mass timber elements meeting specific dimensional requirements, while maintaining a minimum fire-resistance rating of 2 hours. Type V construction offers the most flexibility, allowing combustible materials for exterior walls, though fire-resistance ratings of 1 hour are still mandatory in many cases.
Building codes mandate specific opening protectives, such as fire-rated windows and doors, corresponding to the wall’s fire-resistance rating. Additionally, exterior walls must meet structural requirements for wind loads, seismic forces, and weather protection, while incorporating appropriate thermal insulation and vapor barriers to ensure building envelope performance.
Interior Structure Guidelines
Interior structural components must comply with specific requirements based on the construction type classification. For Type I and Type II construction, interior walls and partitions must be constructed of noncombustible materials, typically utilizing steel studs, concrete block, or gypsum assemblies with appropriate fire-resistance ratings. Structural elements in these types require protection through approved fire-resistant materials.
Type III construction allows for interior elements to be constructed of any material permitted by code, provided they meet the required fire-resistance ratings. Common interior materials include wood studs, steel framing, and engineered lumber products. However, load-bearing interior walls must maintain specified fire-resistance ratings based on occupancy and building height.
Type IV construction features heavy timber elements for interior structural components, with minimum nominal dimensions specified for columns, beams, and structural panels. Type V construction offers the most flexibility for interior components, permitting any materials allowed by code, though fire-resistance ratings still apply based on occupancy type and location within the structure.
All construction types must incorporate proper fire stops, draft stops, and cavity barriers as required by local building codes, regardless of the materials used.
Type IV: Heavy Timber Construction
Dimensional Requirements
Dimensional requirements for each construction type are strictly regulated by building codes to ensure structural integrity and fire safety. For Type I and II construction, structural elements must meet minimum protection requirements, typically ranging from 2 to 3 hours of fire resistance. Type III construction requires exterior walls to be noncombustible or fire-retardant-treated wood with a minimum thickness of 2 inches nominal.
In Type IV (Heavy Timber) construction, columns must be at least 8 inches nominal in cross-section, while beams and girders need to be at least 6 inches nominal in width and 10 inches nominal in depth. Floor decking requirements specify a minimum thickness of 3 inches nominal for splined or tongue-and-groove planks.
Type V construction, while having the least restrictive requirements, still mandates minimum dimensions for load-bearing walls. Interior walls must be at least 2×4 nominal lumber, while exterior walls typically require 2×6 construction in most climate zones to accommodate insulation requirements. These dimensional specifications work in conjunction with other building code requirements to ensure safe, compliant structures.
Modern Innovations
Recent modern construction innovations have revolutionized traditional building classifications, particularly in the realm of mass timber construction. Cross-laminated timber (CLT) and other engineered wood products are challenging conventional perspectives on Type III and Type IV construction categories. These advancements have led to the development of tall wood buildings that can now reach heights previously reserved for steel and concrete structures.
The International Building Code has adapted to accommodate these developments, introducing new provisions for mass timber buildings up to 18 stories tall. This evolution reflects growing confidence in timber’s structural capabilities and fire resistance properties when properly engineered. Notable examples include the 25-story Ascent tower in Milwaukee, which showcases how mass timber can meet rigorous safety standards while offering sustainability benefits.
These innovations are reshaping industry standards, with hybrid systems combining traditional materials with advanced timber technologies becoming increasingly common. This integration of modern materials and methods continues to push the boundaries of what’s possible within established construction type classifications.
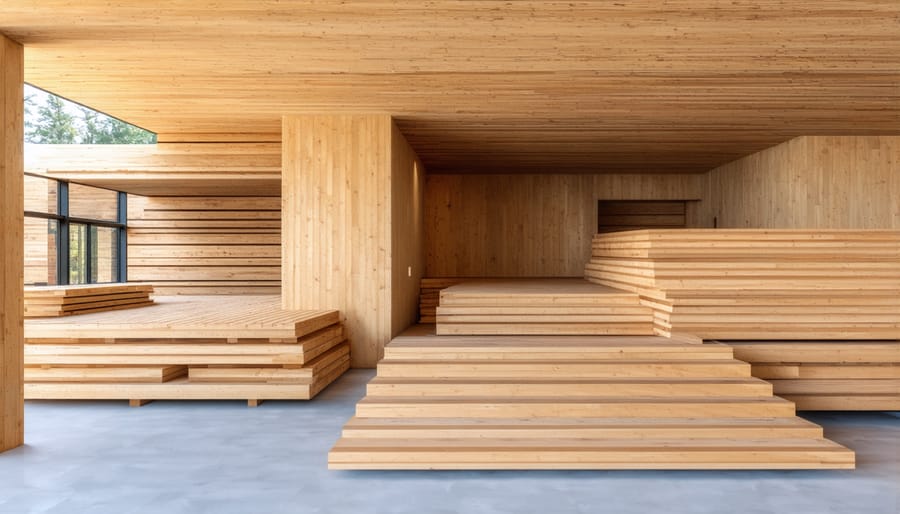
Type V: Wood-Frame Construction
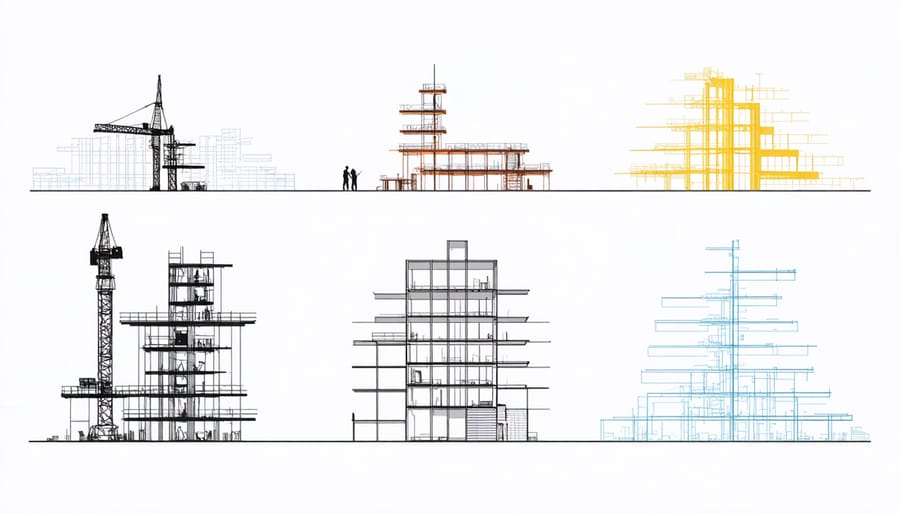
Structural Requirements
Building codes specify distinct requirements for each construction type, with particular emphasis on structural integrity and fire resistance. For Type V construction, which encompasses most wood-frame structures, walls and floors must meet minimum load-bearing capacities while maintaining specified fire-resistance ratings. Exterior walls typically require a one-hour fire-resistance rating, though this may vary based on fire separation distance and occupancy classification.
Load-bearing walls must be designed to support dead loads, live loads, and lateral forces according to local building codes. Floor assemblies need to accommodate minimum live loads of 40 pounds per square foot in residential areas and 100 pounds per square foot in public spaces. Roof structures must withstand both gravity and uplift forces, with specific requirements for snow loads in applicable regions.
For multi-story Type V buildings, fire stops are mandatory at floor levels and roof spaces. The maximum allowable height is typically four stories for Type VA (protected) and two stories for Type VB (unprotected), though specific height and area limitations vary by jurisdiction and occupancy type. All structural members must meet minimum dimensional requirements and spacing specifications to ensure overall building stability and safety.
Fire Safety Measures
Fire safety measures vary significantly across construction types, with more stringent requirements for combustible materials and higher-risk structures. Type I and Type II buildings require comprehensive fire-resistant assemblies, including structural frame protection, fire-rated walls, and non-combustible materials throughout. Type III construction demands fire-rated exterior walls and structural elements, while allowing combustible materials for interior components.
For Type IV (heavy timber) structures, exposed wood members must meet minimum dimensional requirements to achieve inherent fire resistance. Type V construction, while having the least restrictive requirements, still necessitates basic fire protection features such as fire-rated assemblies between units and proper emergency egress.
All construction types must incorporate active fire protection systems based on occupancy, height, and area. These typically include fire sprinkler systems, smoke detection devices, and fire alarm systems. Building size and occupancy limitations become more restrictive as construction types progress from Type I to Type V, reflecting the varying levels of fire resistance inherent in each type’s materials and assemblies.
Additional requirements may include fire-resistant coatings, compartmentalization strategies, and protected vertical openings, depending on specific code requirements and local jurisdiction mandates.
Understanding the five construction types is fundamental to ensuring building safety, code compliance, and project success in the modern construction industry. These classifications serve as essential guidelines that influence everything from material selection to fire safety requirements, ultimately determining how structures are designed, built, and maintained. As the construction industry continues to evolve alongside technological advancements and the future of construction regulations, professionals must maintain a thorough understanding of these classifications to make informed decisions.
The implications of construction type selection extend far beyond initial design considerations, affecting insurance costs, maintenance requirements, and long-term building performance. By properly applying this knowledge, construction professionals can ensure optimal safety standards while maximizing building efficiency and cost-effectiveness. This understanding becomes particularly crucial when addressing urban development challenges, sustainability requirements, and changing occupancy needs.
For industry stakeholders, maintaining expertise in construction types remains an ongoing commitment to professional excellence and public safety. As building technologies and materials continue to advance, this foundational knowledge will remain central to successful project execution and regulatory compliance.