Decarbonization stands as the construction industry’s most pressing challenge, with buildings accounting for nearly 40% of global carbon emissions. Leading construction firms are revolutionizing their approaches through three critical pathways: materials innovation, process optimization, and operational efficiency. By implementing science-based targets and embracing circular economy principles, the sector can achieve up to 50% emissions reduction by 2030.
The transformation toward carbon-neutral construction demands immediate action across the entire building lifecycle. From specifying low-carbon concrete alternatives to implementing energy-efficient design strategies, every decision impacts the project’s carbon footprint. Forward-thinking organizations are already demonstrating that sustainable construction practices not only reduce environmental impact but also drive competitive advantage through reduced operational costs and enhanced stakeholder value.
This comprehensive guide examines proven decarbonization strategies that deliver measurable results, supported by real-world case studies and expert insights. Whether managing large-scale developments or retrofitting existing structures, these approaches provide a practical framework for achieving significant carbon reductions while maintaining project efficiency and profitability. Our analysis focuses on immediately implementable solutions that align with current industry standards and emerging regulations, ensuring long-term sustainability in an increasingly carbon-conscious market.
The Carbon Footprint Challenge in Modern Construction
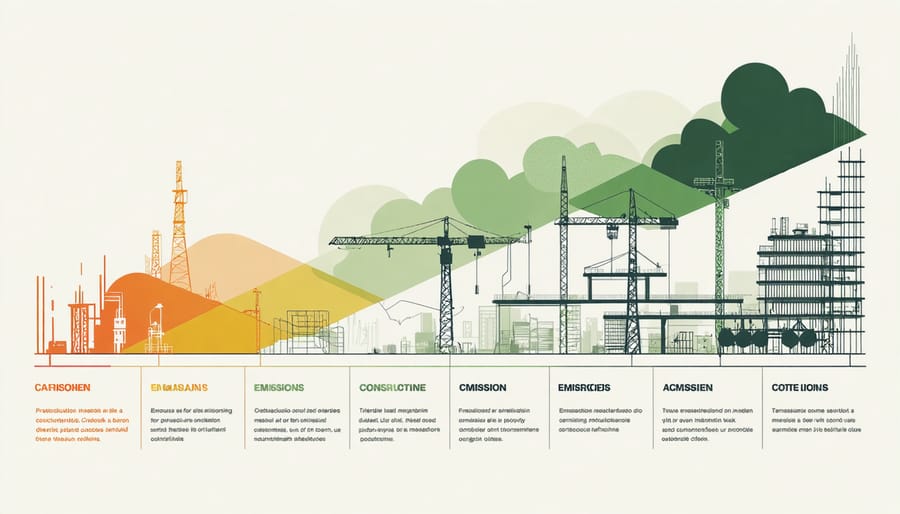
Embodied Carbon: The Hidden Cost
Embodied carbon represents the total greenhouse gas emissions generated throughout a building material’s lifecycle – from extraction and manufacturing to transportation and installation. Unlike operational carbon, which can be reduced over time through efficiency improvements, embodied carbon is locked in once construction is complete. Recent industry studies indicate that embodied carbon can account for up to 50% of a building’s total carbon footprint over its lifespan.
Construction materials such as concrete, steel, and aluminum are particularly carbon-intensive. For instance, cement production alone contributes approximately 8% of global CO2 emissions. Understanding and implementing effective embodied carbon reduction strategies has become crucial for meeting climate goals.
The challenge lies in balancing material performance requirements with environmental impact. Project teams must consider factors such as material sourcing distance, manufacturing processes, and end-of-life recyclability. Early-stage decisions, particularly during design and specification phases, have the most significant impact on embodied carbon levels. This underscores the importance of conducting thorough lifecycle assessments and utilizing Environmental Product Declarations (EPDs) when selecting construction materials.
Operational Carbon: Long-term Impact
Operational carbon emissions represent a significant portion of a building’s total carbon footprint, accounting for approximately 70-80% of lifecycle emissions in conventional buildings. These emissions primarily stem from energy consumption during the building’s operational phase, including heating, cooling, lighting, and other building systems.
To effectively manage operational carbon, building owners and operators must implement comprehensive monitoring systems and adopt energy-efficient technologies. Smart building management systems, coupled with real-time energy consumption tracking, enable precise control over operational emissions. Regular maintenance and system optimization can further reduce energy waste and improve overall building performance.
The selection of renewable energy sources plays a crucial role in minimizing operational carbon. On-site solar installations, wind energy systems, and the procurement of renewable energy through power purchase agreements can significantly reduce or eliminate operational carbon emissions. Additionally, implementing passive design strategies, such as natural ventilation and daylighting, can substantially decrease the energy demand for building operations.
Success in reducing operational carbon requires a long-term commitment to continuous improvement and regular performance evaluations. Building operators should establish clear carbon reduction targets and track progress through standardized measurement protocols.
Material Innovation and Selection
Low-Carbon Concrete Solutions
Recent innovations in concrete technology have revolutionized how the construction industry approaches carbon reduction. Low-carbon concrete alternatives can reduce embodied carbon by up to 70% compared to traditional Portland cement-based formulations.
Supplementary cementitious materials (SCMs) like fly ash, slag, and silica fume are increasingly being incorporated into concrete mixes. These industrial by-products not only reduce the carbon footprint but also enhance durability and strength characteristics. Geopolymer concrete, which uses zero Portland cement, has shown promising results in both structural performance and environmental impact.
Carbon-cure technology represents another breakthrough, injecting captured CO2 into concrete during mixing. This process not only sequesters carbon but also improves the concrete’s compressive strength. Leading construction firms report achieving 20-30% carbon reduction through this method while maintaining structural integrity.
Recent case studies demonstrate successful implementation of these solutions in major projects. The Stockholm bypass tunnel utilized slag-based concrete, reducing carbon emissions by 50,000 tonnes. Similarly, the Singapore Green Building Council documented a 40% reduction in carbon footprint through optimized mix designs incorporating local recycled materials.
For maximum impact, professionals should consider factors such as local material availability, project requirements, and lifecycle performance when selecting low-carbon formulations. Regular testing and quality control remain essential to ensure these innovative solutions meet structural and durability requirements.
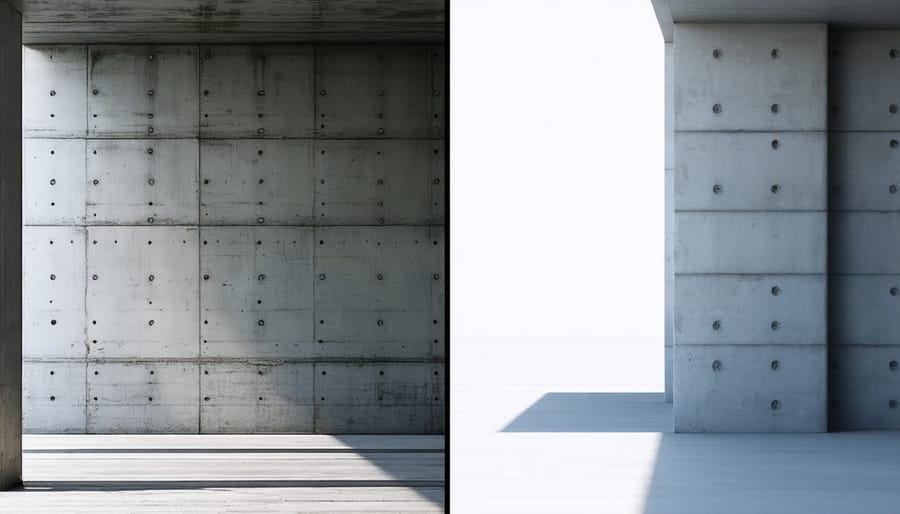
Sustainable Steel and Timber Options
The construction industry is witnessing a significant shift toward sustainable steel and timber alternatives as key components of decarbonization strategies. Green steel, produced using hydrogen-based reduction processes and electric arc furnaces, offers up to 90% lower carbon emissions compared to traditional blast furnace methods. Leading manufacturers are now incorporating recycled content and renewable energy in steel production, creating products with substantially reduced environmental impact.
Mass timber has emerged as a revolutionary alternative to traditional steel and concrete construction. Cross-laminated timber (CLT) and glue-laminated timber (glulam) provide structural capabilities comparable to conventional materials while serving as natural carbon sinks. Recent advancements in engineered wood products have enabled the construction of increasingly tall buildings, with some projects reaching heights previously achievable only with steel.
The combination of sustainable steel and mass timber in hybrid construction systems presents particularly promising opportunities. These hybrid solutions leverage the strengths of both materials, optimizing structural performance while minimizing carbon footprint. For example, the use of steel connectors with mass timber elements creates robust structural systems that maintain sustainability benefits.
Industry leaders are also exploring innovative surface treatments and preservation techniques to enhance the durability and fire resistance of these materials. This development addresses previous concerns about long-term performance and safety, making sustainable alternatives increasingly viable for large-scale commercial projects.
Design and Construction Process Optimization
Digital Twin Technology
Digital twin technology has emerged as a powerful tool in construction decarbonization efforts, enabling real-time monitoring and optimization of carbon emissions throughout project lifecycles. By creating virtual replicas of physical buildings and construction processes, organizations can simulate and analyze various scenarios to identify optimal carbon reduction strategies.
These digital twins integrate data from IoT sensors, building management systems, and construction workflows to provide accurate insights into energy consumption patterns and carbon footprint metrics. Construction teams can leverage this technology to test different material combinations, construction methods, and operational scenarios before implementation, significantly reducing the risk of carbon-intensive decisions.
Recent case studies demonstrate that digital twins can achieve 15-30% carbon reductions through improved resource allocation and process optimization. For example, a commercial development in Singapore utilized digital twin simulation to optimize its HVAC systems, resulting in a 22% decrease in operational carbon emissions.
The technology also enables continuous monitoring of embodied carbon throughout the construction phase, allowing project managers to make real-time adjustments to maintain decarbonization targets. By integrating supply chain data and material tracking, digital twins help identify opportunities for reducing transportation emissions and optimizing material usage, creating a more sustainable construction ecosystem.
As the technology matures, digital twins are becoming increasingly crucial for achieving ambitious carbon reduction goals while maintaining project efficiency and cost-effectiveness.
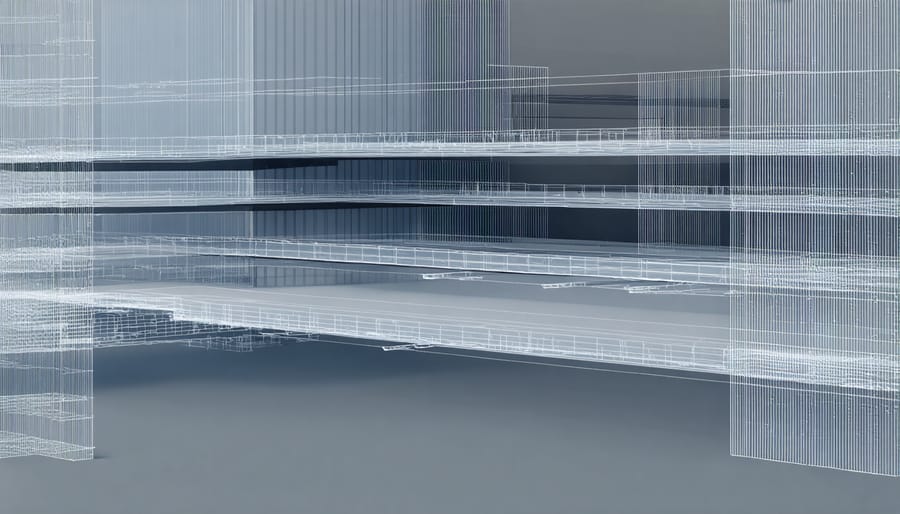
Modular Construction Benefits
Modular construction and prefabrication techniques represent a significant opportunity for carbon reduction in the construction industry. By shifting substantial portions of the building process to controlled factory environments, these methods can reduce carbon emissions by 30-50% compared to traditional on-site construction.
The primary carbon benefits stem from several key factors. First, factory-based production enables precise material usage and waste reduction, with studies showing up to 90% less waste compared to traditional construction methods. Second, controlled environments allow for optimized energy consumption during manufacturing processes, while reducing transportation emissions through consolidated material deliveries.
Quality control in factory settings also ensures better building performance and reduces the need for rework, which traditionally accounts for significant carbon emissions through additional material use and transportation. Modern modular facilities utilize advanced automation and lean manufacturing principles, further enhancing efficiency and reducing energy consumption.
Case studies from leading construction firms demonstrate that modular projects typically require 30% fewer vehicle movements to and from construction sites. This reduction in logistics-related emissions, combined with shorter construction schedules, creates a substantial positive impact on the project’s overall carbon footprint.
The standardization inherent in modular construction also facilitates better lifecycle planning and eventual deconstruction, supporting circular economy principles and reducing end-of-life carbon impacts. As the industry moves toward net-zero goals, modular construction continues to evolve as a crucial strategy in sustainable building practices.
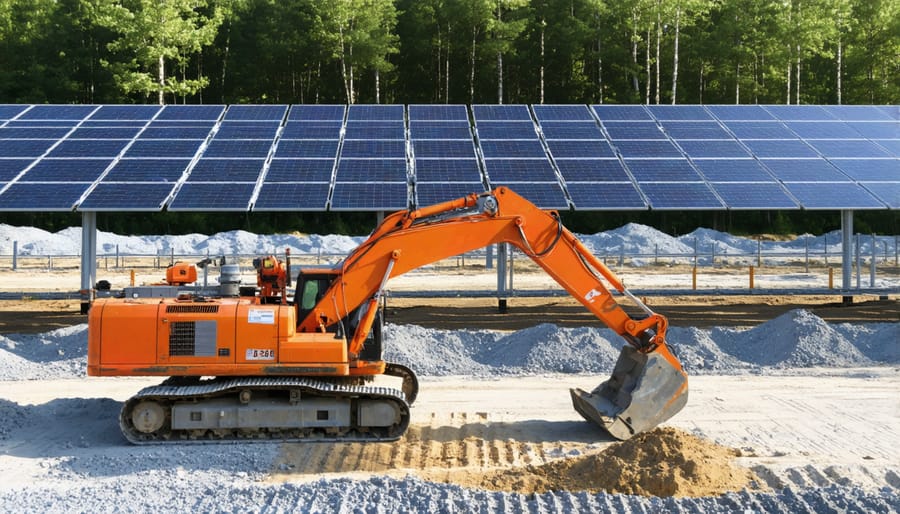
On-Site Energy Management
Renewable Energy Integration
Integrating renewable energy sources during construction requires a strategic approach that combines immediate implementation with long-term sustainability goals. Solar-powered construction equipment and temporary power systems can significantly reduce fossil fuel consumption during the building phase. Project managers should prioritize establishing on-site renewable energy infrastructure early in the construction timeline, enabling these systems to power subsequent construction activities.
Key implementation strategies include installing solar panels on temporary structures and site offices, utilizing portable wind turbines for remote locations, and deploying hybrid power storage systems to maintain consistent energy supply. Construction teams can also leverage microgrids to optimize energy distribution across different work zones, ensuring efficient resource allocation while minimizing waste.
Early planning for permanent renewable energy systems, such as building-integrated photovoltaics (BIPV) and geothermal installations, allows these features to contribute to construction power needs before serving the completed structure. This approach not only reduces carbon emissions during construction but also demonstrates immediate ROI through reduced energy costs.
Modern monitoring systems and smart energy management platforms help construction teams track renewable energy usage, identify optimization opportunities, and adjust consumption patterns for maximum efficiency. This data-driven approach ensures sustainable practices while maintaining project timelines and operational requirements.
Equipment Electrification
The transition to electric construction equipment represents a significant opportunity for reducing carbon emissions on construction sites. Modern electric excavators, loaders, and other heavy machinery offer comparable performance to their diesel counterparts while eliminating direct emissions. Leading manufacturers now provide electric alternatives for most common construction equipment, from compact machines to larger vehicles.
Recent case studies demonstrate that electric equipment can reduce operational costs by up to 25% through lower fuel and maintenance expenses. Construction firms report additional benefits, including reduced noise pollution, improved air quality for workers, and enhanced compliance with urban environmental regulations. Battery technology improvements have extended operating times, with many machines now capable of completing full work shifts on a single charge.
Implementation typically requires careful planning of charging infrastructure and power supply requirements. Construction companies are finding success with a phased approach, starting with smaller equipment and gradually expanding their electric fleet as technology and infrastructure develop. While initial investment costs remain higher than traditional equipment, government incentives and long-term operational savings often result in favorable total cost of ownership calculations.
Supply Chain Decarbonization
Supply chain decarbonization represents a critical frontier in construction sustainability efforts. By implementing sustainable supply chain practices, construction companies can significantly reduce their Scope 3 emissions while improving overall project efficiency.
Key strategies include supplier engagement and certification programs, which ensure materials are sourced from manufacturers committed to carbon reduction. Leading construction firms are implementing supplier scorecards that track emissions data and rewarding vendors who demonstrate substantial progress in reducing their carbon footprint.
Transportation optimization plays a crucial role in supply chain decarbonization. Companies are adopting local sourcing strategies where feasible, consolidating deliveries, and transitioning to electric or hybrid delivery vehicles. Advanced logistics planning systems help minimize unnecessary material movement and reduce associated emissions.
Material passport systems and digital tracking technologies enable better monitoring of carbon emissions throughout the supply chain. These tools provide real-time visibility into the environmental impact of materials from extraction to installation, allowing project managers to make informed decisions about sourcing and transportation.
Collaboration across the supply chain is essential for successful decarbonization. Industry leaders are forming partnerships with suppliers, establishing shared sustainability goals, and investing in joint research and development initiatives. These partnerships often focus on developing low-carbon alternatives for traditional construction materials and improving manufacturing processes.
Innovative procurement strategies, such as bulk purchasing agreements and carbon-weighted tender evaluations, are becoming increasingly common. These approaches incentivize suppliers to reduce their emissions while potentially delivering cost savings through economies of scale.
To ensure long-term success, organizations must implement robust monitoring and reporting systems. Regular audits, standardized carbon accounting methods, and transparent reporting help track progress and identify areas for improvement in supply chain sustainability efforts.
Measuring and Monitoring Success
Effective decarbonization strategies require robust measurement and monitoring systems to track progress and validate results. The implementation of comprehensive carbon tracking systems, alongside traditional construction performance metrics, enables organizations to accurately assess their carbon reduction initiatives.
Key measurement components include establishing baseline emissions data, implementing real-time monitoring systems, and utilizing advanced analytics platforms. Organizations should focus on tracking both direct emissions from construction activities and indirect emissions from material manufacturing and transportation.
Modern carbon monitoring typically involves:
– Digital carbon calculators integrated with BIM systems
– IoT sensors for real-time energy consumption monitoring
– Automated data collection from equipment and processes
– Regular third-party verification of emission measurements
– Cloud-based reporting platforms for stakeholder transparency
Success indicators should encompass both quantitative and qualitative metrics:
– Total carbon emissions per project phase
– Carbon intensity per square meter of construction
– Percentage reduction in embodied carbon
– Material efficiency ratios
– Energy consumption patterns
– Supply chain emissions tracking
Regular auditing and reporting cycles, typically quarterly or monthly, help maintain accountability and identify areas for improvement. Organizations should also consider implementing a carbon budget alongside traditional cost budgeting to ensure comprehensive project oversight and alignment with decarbonization goals.
Industry leaders recommend establishing clear targets and milestones, with regular stakeholder updates to maintain transparency and drive continuous improvement in carbon reduction efforts.
The construction industry stands at a crucial turning point in its journey toward decarbonization. Through the implementation of innovative materials, advanced technologies, and refined processes, significant progress has been made in reducing carbon emissions across construction projects. The adoption of mass timber, low-carbon concrete alternatives, and recycled materials has demonstrated that sustainable construction can be both practical and economically viable.
Looking ahead, the industry’s success in achieving carbon reduction goals will depend on continued innovation and widespread adoption of proven strategies. Digital technologies, including Building Information Modeling (BIM) and AI-powered optimization tools, will play an increasingly important role in minimizing waste and improving energy efficiency. The shift toward circular economy principles and embodied carbon reduction will likely accelerate as regulatory pressures increase and client demands evolve.
For construction professionals, staying informed about emerging technologies and best practices while maintaining a commitment to sustainable construction methods will be essential. As the industry continues to evolve, collaboration between stakeholders, investment in research and development, and the sharing of successful case studies will be crucial in driving the transition toward a zero-carbon construction future.