Quality standards in the construction industry serve as the cornerstone of project success, safety compliance, and long-term infrastructure sustainability. Recent data from the International Organization for Standardization (ISO) reveals that construction projects adhering to established quality standards are 73% more likely to meet completion deadlines and stay within budget constraints. These standards, encompassing everything from material specifications to workplace safety protocols, have evolved significantly with the integration of digital quality management systems and real-time monitoring technologies.
The construction sector’s increasing complexity, coupled with heightened regulatory scrutiny, demands a robust understanding of quality standards that extend beyond traditional compliance checkboxes. Modern quality frameworks now incorporate sustainable building practices, advanced material testing protocols, and comprehensive documentation systems that ensure accountability at every project phase. For industry professionals, mastering these standards isn’t just about meeting minimum requirements—it’s about establishing a competitive edge in a market where quality assurance directly impacts project outcomes, client satisfaction, and organizational reputation.
This comprehensive examination of construction industry quality standards will explore current regulatory frameworks, implementation strategies, and technological solutions that are reshaping how the industry approaches quality management in the 21st century.
Core Quality Standards Framework
ISO 9001 in Construction
ISO 9001 certification in construction provides a systematic approach to quality management, ensuring consistent delivery of projects that meet client requirements and regulatory standards. When implemented effectively, this framework transforms project delivery by establishing standardized processes for planning, execution, and quality control.
In construction projects, ISO 9001 implementation focuses on key areas including document control, resource management, project planning, and continuous improvement. Construction firms must maintain detailed records of quality procedures, inspection results, and corrective actions. This documentation serves as evidence of compliance and facilitates process improvement.
The standard requires construction companies to establish clear communication channels between stakeholders, implement robust risk management strategies, and maintain strict control over suppliers and subcontractors. Regular internal audits help identify potential issues before they impact project delivery.
Notable benefits of ISO 9001 in construction include reduced rework costs, improved client satisfaction, enhanced project efficiency, and better risk management. Companies report significant reductions in defects and warranty claims after certification.
Implementation challenges often include resistance to change, documentation requirements, and initial resource allocation. However, successful adoption leads to standardized workflows, better resource utilization, and improved project outcomes. Modern digital tools have simplified the documentation process, making ISO 9001 compliance more achievable for construction firms of all sizes.
Building Codes and Standards
Building codes and standards form the backbone of construction quality control, establishing minimum requirements for safety, performance, and durability. The International Building Code (IBC) and its regional adaptations serve as primary references for building codes and safety standards across numerous jurisdictions. These comprehensive frameworks address structural integrity, fire protection, accessibility, and environmental sustainability.
Notable international standards include the Eurocodes in European Union countries and the National Building Code of Canada (NBCC), each tailored to regional conditions while maintaining globally recognized quality benchmarks. The standards are regularly updated to incorporate technological advances and lessons learned from field experience.
Construction professionals must navigate multiple layers of regulatory requirements, from local building departments to national oversight agencies. Key aspects include structural design parameters, material specifications, energy efficiency requirements, and occupancy classifications. These standards are increasingly focusing on sustainable construction practices and resilience against natural disasters.
Compliance with these codes requires detailed documentation, regular inspections, and third-party verification at critical construction phases. Modern Building Information Modeling (BIM) systems have become valuable tools for ensuring and demonstrating code compliance throughout the project lifecycle.
Quality Management Systems (QMS)
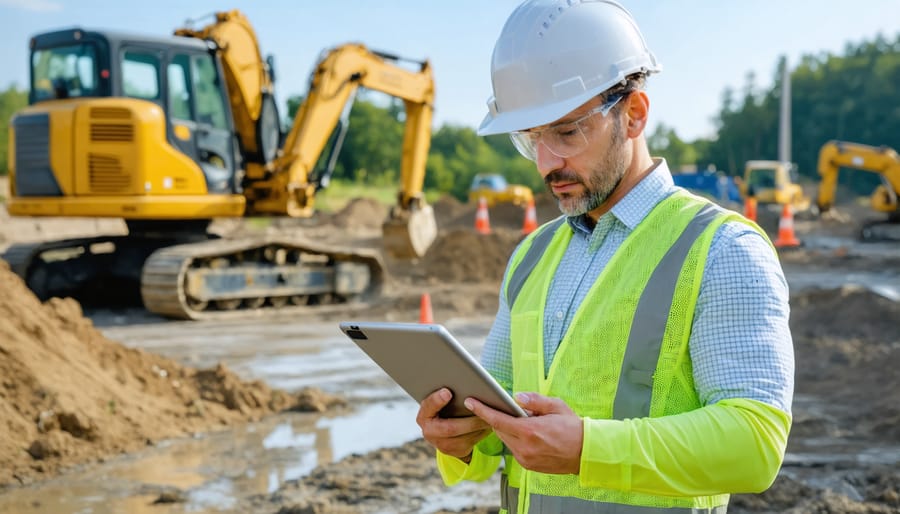
Documentation and Record Keeping
Documentation and record keeping serve as the backbone of quality assurance in construction projects. Effective documentation systems capture critical project information, demonstrate compliance with regulations, and provide an audit trail for quality control processes. Construction firms must maintain detailed records of material specifications, inspection reports, test results, and quality control procedures throughout the project lifecycle.
Essential documentation includes quality control plans, material certifications, daily inspection logs, non-conformance reports, and corrective action records. These documents should be organized systematically using a standardized filing system, whether digital or physical, ensuring easy retrieval and reference when needed. Modern construction management software solutions facilitate real-time documentation and streamline record-keeping processes.
Project teams must maintain as-built drawings, which document any deviations from original plans, along with supporting documentation explaining these changes. Quality-related communications, including meeting minutes, correspondence, and approval documents, should be preserved to establish a clear chain of decisions and accountability.
Documentation requirements often extend beyond project completion, with many jurisdictions requiring retention periods of up to ten years. Implementing a robust document control system helps organizations maintain compliance, defend against claims, and demonstrate due diligence in quality management. Regular audits of documentation systems ensure completeness, accuracy, and accessibility of records, supporting continuous improvement in quality management practices.
Quality Control Procedures
Quality control in construction requires a systematic approach with clearly defined checkpoints throughout the project lifecycle. The process begins with pre-construction material testing and verification, ensuring all components meet critical safety standards and specifications.
Initial inspections focus on material certifications, dimensional accuracy, and structural integrity. Project managers must implement daily quality control checks, including material storage conditions, equipment calibration, and workmanship assessment. Documentation through detailed checklists and digital inspection forms ensures accountability and traceability.
Key checkpoints include:
– Foundation and structural element inspection
– Building envelope verification
– MEP systems testing
– Finish work quality assessment
– Final commissioning and testing
Quality control teams should conduct regular site audits, maintaining detailed logs of non-conformances and corrective actions. Third-party inspections at crucial project milestones provide independent verification of quality standards compliance.
Modern quality control procedures increasingly incorporate digital tools for real-time monitoring and reporting. Building Information Modeling (BIM) enables virtual quality checks before physical construction begins, while mobile inspection apps streamline documentation and communication between project stakeholders.
The final quality control phase involves comprehensive testing of all building systems, thorough documentation review, and verification that all specifications have been met before project handover.
Material and Workmanship Standards
Material Testing Requirements
Material testing in construction projects requires rigorous adherence to standardized procedures to ensure structural integrity and compliance with industry regulations. Key materials such as concrete, steel, aggregates, and soil must undergo comprehensive testing at certified laboratories following ASTM International and ISO standards.
Concrete testing involves multiple parameters, including compressive strength, slump testing, and air content analysis. Samples must be collected at specific intervals during construction, with test cylinders prepared and cured under controlled conditions. Steel testing encompasses tensile strength, yield point verification, and chemical composition analysis to ensure conformity with design specifications.
Quality assurance protocols mandate regular soil testing for foundation work, including particle size distribution, moisture content, and load-bearing capacity. These tests must align with sustainable building standards while maintaining structural requirements.
Documentation plays a crucial role in material testing compliance. All test results must be properly recorded, certified by qualified professionals, and maintained in project records. Failed tests require immediate corrective action and retesting protocols. Modern construction projects increasingly utilize digital testing management systems to streamline documentation and ensure real-time compliance tracking.
Testing frequency and sampling methods must follow project specifications and regulatory requirements. Independent third-party testing agencies often conduct verification testing to ensure unbiased results and maintain quality control standards throughout the construction process.
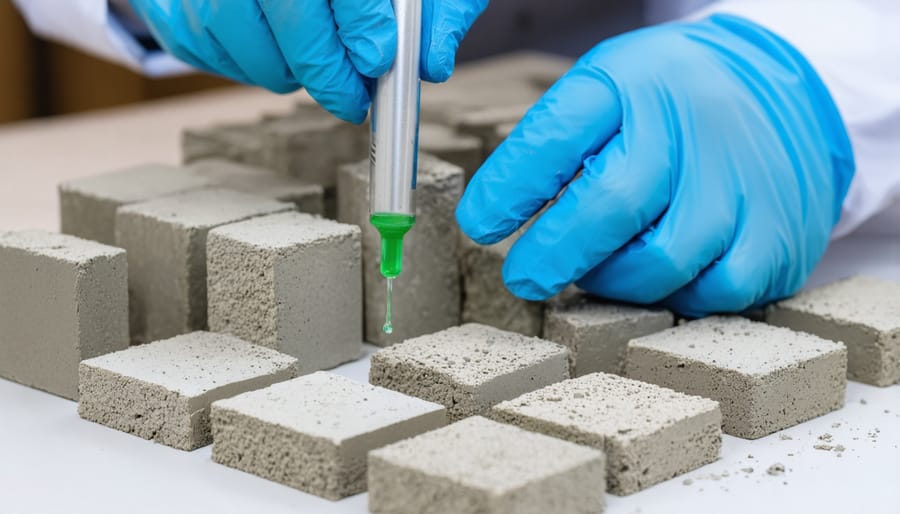
Workmanship Inspection Criteria
Workmanship inspection criteria form the backbone of quality control in construction projects, establishing clear benchmarks for acceptable work quality. Key inspection points include dimensional accuracy, with tolerances typically ranging from ±3mm for structural elements to ±1mm for finish work. Surface finish requirements demand smooth, uniform appearances without visible defects, with concrete surfaces rated according to the ACI standards from Class A to D.
Material installation must meet manufacturer specifications and industry standards, particularly for critical elements like waterproofing membranes and fire-rated assemblies. Joint alignments should maintain consistent spacing and width, with maximum acceptable deviations of 2mm for visible joints. Plumbness and levelness tolerances are typically set at 1:500 for vertical elements and 1:1000 for horizontal surfaces.
Quality inspectors evaluate work against these criteria using calibrated measurement tools and documented checklists. Critical inspection points include foundation elements, structural frameworks, MEP installations, and finishing works. Each trade must meet specific acceptance criteria, such as proper nail spacing in drywall installation (150mm on center at panel edges) or minimum concrete cover for reinforcement (typically 40mm for exposed conditions).
Non-conforming work must be documented, evaluated, and either remediated or accepted through formal deviation procedures. Regular inspection intervals should be established based on project complexity and risk assessment, with results recorded in standardized inspection reports.
Technology and Quality Assurance
Digital Quality Management Tools
Modern quality management in construction has been revolutionized by digital tools that streamline inspection processes, documentation, and compliance tracking. These construction technology innovations have transformed traditional quality control methods into efficient, data-driven systems.
Cloud-based quality management platforms now enable real-time collaboration between site teams and office personnel, allowing immediate issue reporting and resolution tracking. Mobile applications equipped with digital checklists and photo documentation capabilities ensure consistent inspection procedures while eliminating paper-based workflows.
Building Information Modeling (BIM) integration with quality management software provides precise reference points for inspections and helps identify potential issues before they occur. Advanced analytics tools process collected data to generate insights on common defects, compliance patterns, and areas requiring improvement.
Digital tools also facilitate automated reporting and documentation storage, ensuring regulatory compliance and creating comprehensive audit trails. These systems typically include features for managing certifications, calibration records, and material testing results, providing a single source of truth for all quality-related information.
BIM Integration
Building Information Modeling (BIM) has revolutionized quality assurance in construction by providing a comprehensive digital framework for project planning, execution, and monitoring. This integrated approach enables real-time collaboration among stakeholders while maintaining stringent quality standards throughout the project lifecycle.
BIM’s 3D modeling capabilities allow for early detection of design conflicts and potential construction issues, significantly reducing costly rework and quality-related problems during execution. The platform’s ability to store and manage detailed component specifications ensures that materials and installations meet prescribed quality requirements.
Quality managers leverage BIM’s data-rich environment to conduct virtual inspections, track construction progress, and verify compliance with industry standards. The technology’s clash detection features help identify spatial conflicts before they manifest on-site, while its documentation capabilities maintain a clear audit trail for quality control processes.
Advanced BIM implementations incorporate 4D and 5D elements, linking construction schedules and cost data to quality parameters. This integration enables proactive quality management by highlighting potential issues in the construction sequence and allowing for timely interventions to maintain quality standards.
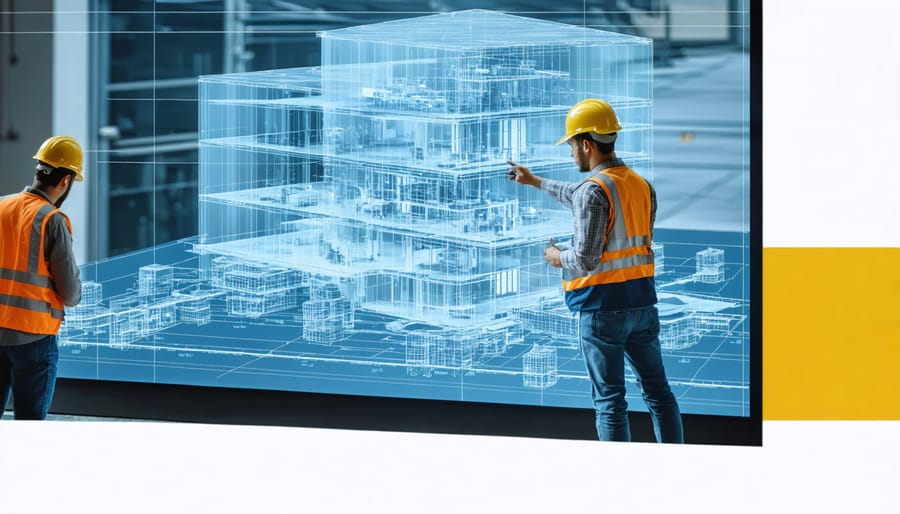
In today’s rapidly evolving construction landscape, maintaining rigorous quality standards is not just a regulatory requirement but a fundamental driver of project success and organizational reputation. The implementation of comprehensive quality management systems, combined with regular audits and continuous improvement processes, ensures that construction projects meet or exceed industry benchmarks while delivering value to stakeholders.
The adoption of digital tools and modern quality control technologies has revolutionized how the industry approaches quality assurance, enabling real-time monitoring, data-driven decision-making, and enhanced collaboration among project teams. However, technology alone cannot guarantee quality; it must be supported by well-trained personnel, robust processes, and a culture that prioritizes excellence at every level of operations.
As construction projects become increasingly complex, the importance of adhering to established quality standards cannot be overstated. Organizations that invest in quality management systems, employee training, and technological solutions position themselves for long-term success while contributing to the industry’s overall advancement. By maintaining unwavering commitment to quality standards, construction companies not only protect their interests but also ensure the safety, durability, and sustainability of built environments for generations to come.