The economic circular flow diagram stands as the cornerstone of modern economic understanding, illustrating the intricate relationship between production, consumption, and resource management. This fundamental model, particularly relevant to the circular economy in construction, demonstrates how money, resources, and value circulate through an economic system. By mapping the continuous exchange between households, businesses, governments, and financial institutions, the diagram reveals critical insights into sustainable resource utilization and economic efficiency.
For construction professionals and industry stakeholders, understanding this model provides essential framework for optimizing material flows, reducing waste, and implementing sustainable practices. The circular flow concept challenges traditional linear economic thinking, offering a sophisticated approach to resource management that aligns with modern sustainability requirements and regulatory demands. This comprehensive visualization tool helps decision-makers identify opportunities for process improvement, cost reduction, and environmental stewardship within their operations.
Traditional vs. Circular Economic Flow in Construction
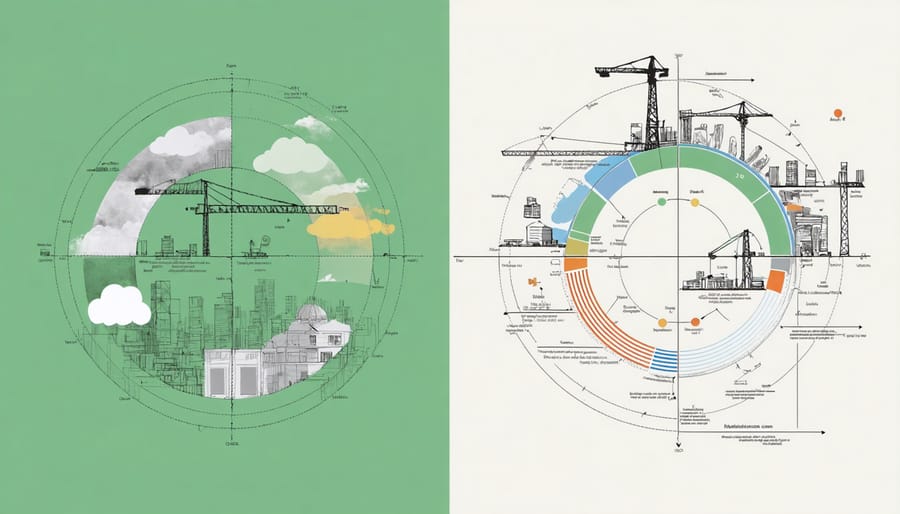
Linear Economy Limitations
The traditional linear economy model in construction follows a straightforward “take-make-dispose” approach that has become increasingly unsustainable in today’s resource-constrained world. This model relies heavily on extracting raw materials, using them once in construction projects, and ultimately disposing of them as waste, creating significant environmental and economic challenges.
Construction projects operating under this linear model typically consume vast quantities of virgin materials while generating substantial waste. According to industry studies, construction activities account for approximately 40% of raw material use globally and generate up to 35% of the world’s waste. This approach not only depletes finite resources but also leads to increased landfill usage and higher disposal costs for construction companies.
The linear model’s limitations become particularly evident in material price volatility and supply chain disruptions. As natural resources become scarcer, construction firms face escalating material costs and uncertain supply availability. Furthermore, this traditional approach fails to capture the potential value retained in building materials at the end of their initial use, missing opportunities for resource recovery and cost savings through reuse and recycling.
These limitations highlight the urgent need for a transition to more sustainable, circular approaches in construction practices.
Circular Flow Advantages
Implementing circular economic principles in construction projects offers significant advantages that extend beyond environmental benefits. Projects adopting these principles typically see a 15-20% reduction in material costs through effective resource optimization and zero waste construction practices. The circular flow model enables better tracking and management of resources throughout the project lifecycle, leading to improved operational efficiency and reduced waste disposal costs.
Financial benefits include enhanced project value through material recovery and reuse, lower procurement expenses, and decreased disposal fees. Construction firms implementing circular principles report an average of 25% improvement in resource utilization and significant reductions in virgin material requirements.
The model also strengthens supply chain resilience by creating closed-loop material cycles, reducing dependency on volatile raw material markets. This approach facilitates better compliance with environmental regulations while positioning companies as industry leaders in sustainable construction practices. Additionally, projects following circular principles often achieve higher sustainability ratings and certifications, leading to increased market value and competitive advantage in the industry.
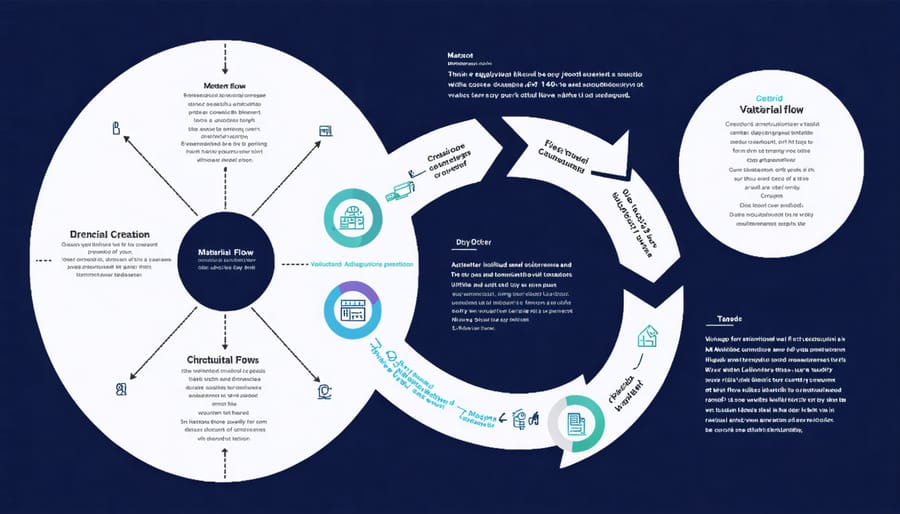
Key Components of Construction’s Circular Flow
Material Flow Cycles
In the construction ecosystem, material flow cycles follow distinct patterns that interconnect various stages of the building lifecycle. Raw materials enter the system through extraction and processing, moving through manufacturing facilities where they’re transformed into construction products. These materials then flow to construction sites, where they’re incorporated into buildings and infrastructure.
During the operational phase, materials continue their journey through maintenance and renovation activities. When buildings reach the end of their lifecycle, materials enter the demolition and waste management stream. In a circular economy model, these materials don’t exit the system but instead feed back through recycling and reuse channels.
Key material flows include concrete aggregates, which can be crushed and repurposed in new construction; steel, which maintains its properties through multiple recycling cycles; and timber, which can be reclaimed for new applications or processed into secondary products. Modern construction practices increasingly emphasize designing for disassembly, enabling easier material recovery and reuse.
Material tracking systems and digital technologies play crucial roles in monitoring these flows, helping construction professionals identify opportunities for material optimization and waste reduction. Building Information Modeling (BIM) systems enable precise material quantity calculations and facilitate better planning for future recovery and reuse, ensuring materials maintain their highest utility throughout their lifecycle.
Financial Flows
In the construction sector’s circular economy, financial flows operate as a vital counterpart to material and service exchanges. Money circulates between key stakeholders, creating a dynamic economic ecosystem that supports sustainable construction practices. Project developers and contractors pay suppliers for sustainable materials and circular solutions, while receiving payments from clients and investors who value environmentally conscious building approaches.
Financial institutions play a crucial role by providing capital through green loans and sustainable construction financing. These monetary instruments enable contractors to invest in circular technologies and processes, while generating returns through improved resource efficiency and reduced waste management costs.
Revenue streams in circular construction often include both traditional sources and innovative mechanisms. These can range from direct payments for construction services to additional income from material recovery, waste reduction, and energy efficiency improvements. The financial benefits extend beyond immediate project completion, as circular buildings typically command premium prices and lower operational costs.
Government incentives and environmental regulations also influence financial flows, creating monetary advantages for circular practices through tax benefits, grants, and penalties for non-compliance. This regulatory framework helps offset initial investments in circular solutions and encourages long-term adoption of sustainable construction methods.
The continuous circulation of financial resources ensures the economic viability of circular construction projects while promoting sustainable development within the industry.
Value Creation Points
In the circular economic flow diagram, value creation occurs at multiple interconnected points, with each participant contributing to the overall economic ecosystem. The primary value generators are businesses and households, which create distinct but complementary forms of economic value.
Businesses generate value through the transformation of raw materials into finished products and services. In the construction sector, this includes converting basic materials like steel, concrete, and timber into completed structures, infrastructure, and building components. The value-add process encompasses design innovation, manufacturing efficiency, and quality improvements that enhance the final product’s utility and market worth.
Households create value through two main channels: labor provision and consumption. By supplying skilled workforce to construction projects, households contribute expertise and productivity that drives the industry forward. Additionally, their consumption choices and spending patterns create market demand that stimulates economic activity and influences production decisions.
Government entities add value through regulatory frameworks, infrastructure development, and public services that facilitate smooth market operations. Financial institutions create value by facilitating capital flow, managing risk, and enabling investment in construction projects.
The interconnected nature of these value points creates a multiplier effect, where initial value creation at one point triggers additional value generation throughout the system. For instance, a construction company’s investment in sustainable building practices can create environmental value, economic benefits for suppliers, and long-term cost savings for end-users, demonstrating the cumulative impact of strategic value creation in the circular flow.
Implementing Circular Flow in Construction Projects
Design Phase Integration
Integrating circular economy principles during the design phase is crucial for maximizing resource efficiency and minimizing waste throughout a project’s lifecycle. Studies show that up to 80% of a project’s environmental impact is determined during the early design stages, making this phase particularly critical for circular implementation.
To effectively incorporate circular principles, design teams should begin with a comprehensive material flow analysis. This involves mapping out all potential resources entering and exiting the project, including raw materials, energy inputs, and potential waste streams. Design professionals should prioritize specifying materials with high recycled content, proven durability, and end-of-life recyclability.
Modular design strategies play a vital role in facilitating future adaptability and component reuse. By designing for disassembly, buildings can be more easily modified, maintained, and eventually deconstructed with minimal waste. This approach requires careful consideration of connection details and material selection.
Digital tools like Building Information Modeling (BIM) can help optimize material use and predict maintenance requirements throughout the building’s lifecycle. These technologies enable teams to simulate different design scenarios and their corresponding resource implications before construction begins.
Collaboration between architects, engineers, and suppliers during the design phase is essential for identifying circular opportunities. Regular design reviews should include discussions about material alternatives, waste reduction strategies, and potential closed-loop systems that can be implemented within the project scope.
Supply Chain Optimization
In the construction industry, optimizing supply chains for circular economy principles requires a fundamental shift from linear to cyclical material flows. Effective sustainable supply chain management begins with strategic supplier partnerships that prioritize recyclable materials and waste reduction protocols.
Key optimization strategies include implementing reverse logistics systems that facilitate the recovery and reprocessing of construction materials, establishing material passports to track resource flows, and developing local supplier networks to minimize transportation impacts. Digital technologies, such as blockchain and IoT sensors, enable real-time tracking of materials throughout their lifecycle, ensuring transparency and traceability in the circular supply network.
Construction companies are increasingly adopting modular design principles and prefabrication techniques that optimize material usage and reduce waste at the source. This approach, combined with just-in-time delivery systems, helps minimize storage requirements and prevents material deterioration.
To create truly circular supply networks, organizations must establish clear performance metrics focusing on material recovery rates, waste reduction targets, and supplier sustainability credentials. Regular audits and continuous improvement processes ensure the supply chain maintains its circular integrity while meeting project requirements and sustainability goals.
Success in supply chain optimization requires collaboration across the entire value chain, from material suppliers to waste management partners, supported by robust data management systems and standardized reporting protocols.
End-of-Life Planning
End-of-life planning in construction plays a critical role in maintaining material flow within the economic cycle. Successful implementation requires careful consideration during the design phase, incorporating strategies for future disassembly, recycling, and material recovery. Industry leaders are increasingly adopting design for deconstruction (DfD) principles, ensuring building components can be efficiently separated and repurposed at the end of their initial use cycle.
Material passports have emerged as essential tools for tracking building components throughout their lifecycle. These digital records document material specifications, locations, and potential reuse options, facilitating efficient recovery and redistribution when structures reach their end of life. Leading construction firms are implementing automated tracking systems and Building Information Modeling (BIM) to maintain accurate material inventories.
Successful end-of-life planning also requires establishing robust reverse logistics networks. These systems enable the efficient collection, sorting, and redistribution of materials from demolition sites to recycling facilities or new construction projects. Several pioneering projects have demonstrated recovery rates exceeding 90% through careful planning and coordination with specialized recycling partners.
To maximize material retention in the economic cycle, construction professionals should:
– Document material specifications and assembly methods
– Design for easy disassembly
– Establish partnerships with recycling facilities
– Implement digital tracking systems
– Create detailed deconstruction plans
– Consider future adaptability in current designs
These strategies ensure materials maintain their highest possible value throughout multiple lifecycle iterations.
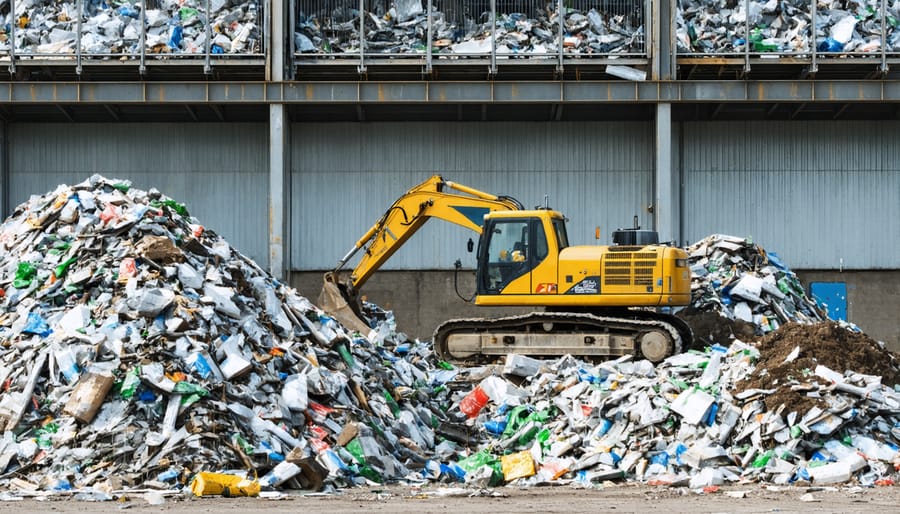
The circular economic flow diagram represents a transformative framework that’s reshaping the construction industry’s approach to resource management and sustainability. As demonstrated through numerous successful circular economy implementations, the benefits extend far beyond environmental preservation to include substantial cost savings and enhanced operational efficiency.
Looking ahead, the construction sector stands at a pivotal moment. The increasing adoption of circular principles is driving innovation in material design, waste management protocols, and supply chain optimization. Companies that embrace these principles are positioning themselves as industry leaders while simultaneously addressing growing regulatory pressures and client demands for sustainable building practices.
Key takeaways from our analysis include the essential role of digital technologies in facilitating circular flows, the importance of collaborative partnerships across the supply chain, and the critical need for standardized measurement frameworks. The data clearly shows that organizations implementing circular economy principles are achieving 15-25% reductions in material costs and up to 40% decrease in waste management expenses.
For construction professionals, the path forward involves integrating circular thinking into every project phase, from design to demolition. This requires a shift from traditional linear models to systems thinking, where waste becomes a resource and buildings are designed for future adaptability and material recovery.
The future outlook is promising, with emerging technologies like blockchain for material tracking, AI for optimization, and advanced recycling processes making circular practices increasingly viable. However, success depends on industry-wide commitment, continued innovation, and supportive policy frameworks. As we move forward, those who adapt to circular principles will likely find themselves better equipped to meet future challenges while contributing to a more sustainable built environment.
Remember, transitioning to a circular economy is not just an environmental imperative but a business opportunity that can drive competitive advantage and long-term growth in the construction sector.